Technology and Applications of cast iron versus carbon steel
Cast iron and carbon steel are both widely used in various applications due to their distinct properties and characteristics.
Cast Iron:
Cast iron is a brittle alloy with a high carbon content (typically 2-4%) and silicon. It is known for its excellent heat retention, making it ideal for cookware such as skillets and Dutch ovens. Cast iron’s ability to distribute heat evenly also makes it suitable for applications like engine blocks and pipes in the construction industry. Its low melting point enables easy casting into complex shapes, giving it an advantage in decorative and architectural elements.
Applications:
1. Cookware: Cast iron skillets and pans are valued for their even heating and natural non-stick properties.
2. Industrial: Used for pipes, machine bases, and heavy machinery components due to its durability and thermal properties.
3. Architectural: Decorative elements like fences, gates, and ornate structures benefit from cast iron’s malleability and aesthetic appeal.
Carbon Steel:
Carbon steel is an alloy of iron and carbon (up to 2.1% by weight), with small amounts of other elements like manganese and silicon. It is versatile and used extensively in construction, automotive, and manufacturing industries. Carbon steel’s strength, hardness, and ductility make it suitable for structural applications where strength-to-weight ratio is critical.
Applications:
1. Construction: Beams, structural supports, and reinforcement bars rely on carbon steel for its high tensile strength.
2. Automotive: Gears, axles, and chassis components benefit from carbon steel’s durability and impact resistance.
3. Tools and Machinery: Cutting tools, drill bits, and machine components leverage carbon steel’s hardness and wear resistance.
Comparison:
– Strength and Durability: Carbon steel is stronger and more durable than cast iron, making it preferable for structural and load-bearing applications.
– Heat Resistance: Cast iron retains heat better than carbon steel, making it suitable for high-temperature cooking and industrial uses.
– Machinability: Carbon steel is easier to machine and work with compared to cast iron, which can be brittle and challenging to shape.
In conclusion, while both cast iron and carbon steel find extensive use across various industries, their specific properties dictate their suitability for different applications, ranging from cookware to heavy machinery and construction. Each material’s unique characteristics ensure they remain indispensable in modern manufacturing and everyday life.
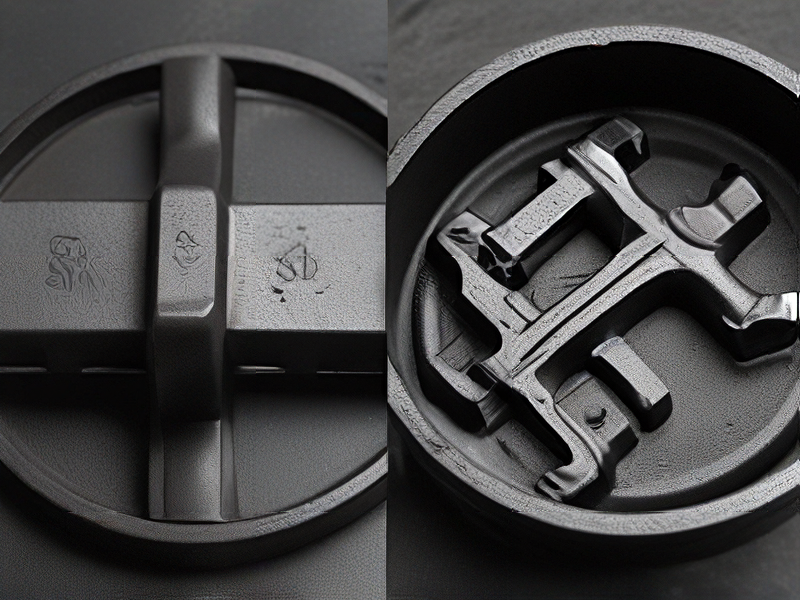
Quality Testing Methods for cast iron versus carbon steel and how to control quality
Quality testing methods for cast iron and carbon steel primarily focus on ensuring material properties and structural integrity. For cast iron, common tests include:
1. Chemical Composition Analysis: Verifies alloy constituents (e.g., carbon, silicon) to ensure they meet specified standards using techniques like spectroscopy.
2. Microstructure Examination: Evaluates grain size and distribution through microscopy to ensure uniformity and absence of defects like graphite nodules.
3. Hardness Testing: Measures material resistance to indentation using Rockwell or Brinell scales to ensure it meets hardness requirements.
4. Tensile Strength Testing: Determines material strength and elasticity under tension to ensure it withstands intended loads without failure.
5. Impact Testing: Assesses material toughness by subjecting samples to controlled impacts, crucial for evaluating resistance to sudden loads.
For carbon steel, similar tests are employed but tailored to its specific properties:
1. Chemical Analysis: Ensures carbon content and alloy elements are within specified ranges to achieve desired strength and durability.
2. Mechanical Properties Testing: Includes tensile, yield, and elongation tests to verify strength, ductility, and ability to deform without fracturing.
3. Macro Examination: Inspects the surface and cross-section for defects such as cracks, laminations, and inclusions that could compromise structural integrity.
4. Corrosion Resistance Testing: Determines susceptibility to corrosion in various environments, critical for applications exposed to moisture or chemicals.
Quality control measures involve:
– Process Control: Monitoring and adjusting manufacturing parameters to maintain consistency and quality throughout production.
– Inspection: Regular checks during and after production to detect deviations and ensure adherence to specifications.
– Certification and Standards Compliance: Ensuring products meet international standards (e.g., ASTM, ISO) through rigorous testing and documentation.
By employing these methods and controls, manufacturers can uphold high standards for both cast iron and carbon steel, ensuring reliability and performance in various applications.

Tips for Procurement and Considerations when Purchasing from cast iron versus carbon steel
When deciding between cast iron and carbon steel for procurement, consider the following:
1. Durability and Strength: Cast iron is brittle but offers excellent heat retention and even cooking. Carbon steel is more flexible and durable, making it suitable for high-heat cooking and heavy-duty use.
2. Weight and Handling: Cast iron is heavier and more cumbersome, which affects transportation and handling costs. Carbon steel is lighter and easier to maneuver.
3. Maintenance: Cast iron requires seasoning to maintain a non-stick surface and prevent rust. Carbon steel also needs seasoning but is less prone to rusting.
4. Versatility: Carbon steel heats up and cools down quickly, making it ideal for tasks requiring precise temperature control. Cast iron retains heat longer and distributes it evenly, making it suitable for slow cooking and baking.
5. Cost: Cast iron tends to be cheaper initially but may require more maintenance over time. Carbon steel is generally more expensive but offers better long-term value due to durability and ease of maintenance.
6. Environmental Impact: Consider the environmental impact of production and disposal. Both materials are recyclable, but the manufacturing processes differ in energy consumption and emissions.
7. Supplier Reliability: Evaluate suppliers based on their reputation, quality control measures, and reliability of supply. Ensure they meet regulatory standards and provide consistent product quality.
8. End-User Preferences: Consult with chefs or end-users to understand their preferences and specific needs. Factors such as cooking techniques, menu offerings, and kitchen equipment compatibility can influence the decision.
By weighing these factors, you can make an informed decision based on your specific procurement needs and operational requirements.

FAQs on Sourcing and Manufacturing from cast iron versus carbon steel in China
When sourcing and manufacturing from China, choosing between cast iron and carbon steel involves several considerations:
1. Material Properties: Cast iron is brittle yet has excellent heat retention, making it ideal for cookware like skillets and pans. Carbon steel, lighter and more flexible, suits items requiring durability and resilience, like knives and tools.
2. Cost Efficiency: Cast iron, typically cheaper due to simpler manufacturing processes, is more economical for bulk production. Conversely, carbon steel’s higher initial cost often balances out through its longevity and performance.
3. Manufacturing Expertise: China has robust capabilities in both materials, with regions specializing in different production techniques. Southern China, for instance, excels in cast iron manufacturing, while eastern regions are adept at carbon steel.
4. Quality Control: Vigilance in monitoring production standards is crucial. Detailed specifications and regular inspections are necessary to maintain consistent quality, ensuring products meet international standards.
5. Environmental Impact: Both materials have environmental considerations. Carbon steel involves higher energy consumption during production but is more easily recyclable. Cast iron, though durable, demands more energy for melting and casting.
6. Logistics and Supply Chain: Understanding shipping costs, lead times, and logistical challenges ensures timely delivery and minimizes disruptions.
In summary, while both cast iron and carbon steel offer distinct advantages, the choice depends on specific product requirements, cost considerations, and quality control measures throughout the sourcing and manufacturing process in China.
