Technology and Applications of steel meshing
Steel meshing, often referred to as steel mesh or welded wire mesh, finds extensive applications across various industries due to its structural integrity, flexibility, and durability. This material consists of interconnected steel wires welded together to form a grid pattern, creating a versatile product suitable for diverse applications.
In construction, steel mesh is commonly used in reinforced concrete structures to enhance tensile strength and prevent cracking. It acts as reinforcement in walls, floors, and foundations, providing structural stability and supporting heavy loads. The mesh can also be utilized in concrete slabs to control cracking caused by temperature changes and shrinkage.
In the manufacturing sector, steel mesh serves as a vital component in fencing and security applications. It provides a robust barrier for perimeter security, protecting properties, and facilities from unauthorized access. Additionally, it is employed in industrial shelving units and storage systems due to its strength and ability to withstand heavy loads.
In landscaping and agriculture, steel mesh acts as a barrier against pests while allowing ventilation and sunlight in greenhouse structures. It also serves as trellises for plants to climb and support structures for retaining walls in landscaping projects.
Furthermore, steel mesh is utilized in transportation infrastructure for reinforcing pavements, bridges, and tunnels, ensuring longevity and safety under heavy traffic conditions.
The versatility of steel meshing extends to its use in art installations, furniture manufacturing, and DIY projects due to its malleability and aesthetic appeal. Overall, steel meshing’s adaptability and strength make it indispensable in various industries, contributing to safer, more durable, and aesthetically pleasing structures and products.

Quality Testing Methods for steel meshing and how to control quality
Quality testing methods for steel mesh typically involve both destructive and non-destructive techniques to ensure robustness and reliability:
1. Dimensional Checks: Verify wire diameter, mesh size, and overall dimensions using calipers, micrometers, or laser measurement systems.
2. Tensile Strength Testing: Conduct tensile tests on samples to determine the maximum load the mesh can withstand before breaking, ensuring it meets strength requirements.
3. Bend and Rebend Tests: Evaluate the flexibility and ductility by bending samples at specified angles and examining for cracks or fractures.
4. Visual Inspection: Examine for surface defects, such as rust, corrosion, or uneven welding, which can affect durability.
5. Non-Destructive Testing (NDT):
– Ultrasonic Testing: Detect internal defects like voids or inclusions using high-frequency sound waves.
– Magnetic Particle Testing: Identify surface and near-surface defects using magnetic fields and iron particles.
– Radiographic Testing: Utilize X-rays or gamma rays to inspect for internal flaws and weld integrity.
6. Chemical Composition Analysis: Verify alloy composition through spectroscopic methods to ensure it meets specified standards.
To control quality:
– Standard Operating Procedures (SOPs): Implement clear procedures for manufacturing and testing.
– Regular Calibration: Calibrate testing equipment to maintain accuracy.
– Quality Control Checks: Conduct frequent inspections throughout production.
– Supplier Quality Assurance: Ensure raw materials meet quality standards before use.
– Employee Training: Train staff on quality procedures and equipment operation.
By combining these methods and controls, manufacturers can ensure steel mesh products meet stringent quality requirements, enhancing reliability and performance in various applications.

Tips for Procurement and Considerations when Purchasing from steel meshing
When procuring steel mesh, consider several key factors to ensure you get the right product:
1. Specifications and Standards: Verify that the steel mesh meets required specifications (e.g., size, gauge, material grade) and standards (ASTM, ISO) suitable for your application. This ensures quality and performance consistency.
2. Quality and Durability: Assess the quality of the steel mesh, including its tensile strength, corrosion resistance, and structural integrity. Higher grades are crucial for long-term durability, especially in challenging environments.
3. Supplier Reputation: Choose reputable suppliers with a track record of delivering quality products on time. Check reviews, certifications, and their ability to provide technical support and after-sales service.
4. Cost and Value: Balance cost with value by considering lifecycle costs rather than just upfront expenses. Cheaper options may require more frequent replacement or maintenance, costing more in the long run.
5. Customization and Flexibility: Evaluate if the supplier offers customization options such as different sizes, coatings, or configurations to meet specific project requirements.
6. Logistics and Lead Times: Confirm the supplier’s capability to meet your delivery schedule and logistical requirements. Timely delivery is crucial to avoid project delays.
7. Environmental and Regulatory Compliance: Ensure the steel mesh complies with environmental regulations and safety standards applicable in your region.
8. Warranty and Support: Understand the warranty terms and conditions offered by the supplier. Reliable support for installation, troubleshooting, and maintenance can add significant value.
By considering these factors, you can make informed decisions when purchasing steel mesh, ensuring it meets your project’s technical requirements and budget constraints effectively.

FAQs on Sourcing and Manufacturing from steel meshing in China
Certainly! Here are some FAQs on sourcing and manufacturing steel meshing in China:
1. Why should I consider sourcing steel meshing from China?
China offers competitive pricing due to lower manufacturing costs and access to abundant raw materials. Moreover, Chinese manufacturers often have extensive experience and advanced technology in producing steel mesh products.
2. How can I ensure quality when sourcing from China?
It’s crucial to conduct thorough supplier evaluations, including factory visits, requesting samples, and checking certifications like ISO standards. Establish clear quality requirements in your contracts and consider hiring a third-party inspection service.
3. What are common challenges in manufacturing steel meshing in China?
Challenges may include communication barriers, cultural differences, and varying interpretations of quality standards. Shipping logistics and lead times can also impact sourcing from China.
4. Are there environmental considerations when sourcing from China?
Yes, ensure suppliers comply with local environmental regulations and industry standards. Request information on their environmental practices and certifications to mitigate any environmental impact.
5. What are typical payment terms and negotiation strategies?
Payment terms often include initial deposits and balance payments upon completion or shipment. Negotiation strategies can involve requesting competitive pricing, flexible payment terms, and long-term partnerships.
6. How can I protect my intellectual property (IP) when manufacturing in China?
Use legal safeguards such as non-disclosure agreements (NDAs), trademarks, and patents. Work with reputable manufacturers and consider consulting with legal professionals specializing in international IP law.
By addressing these FAQs, you can navigate sourcing and manufacturing steel meshing in China more effectively, ensuring quality, compliance, and competitive pricing.
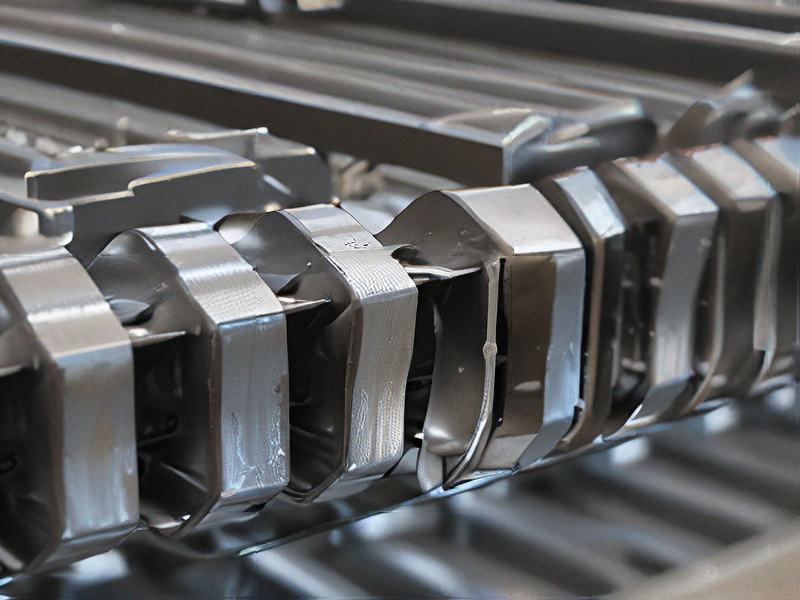