Technology and Applications of machine shop cnc
Computer Numerical Control (CNC) technology revolutionizes manufacturing processes in machine shops by automating tasks traditionally performed manually. CNC machines are equipped with pre-programmed computer software that controls their operation with precision and consistency. This technology finds applications across various industries, including aerospace, automotive, electronics, and medical devices.
In a machine shop setting, CNC machines such as lathes, mills, and routers perform tasks like cutting, drilling, shaping, and finishing materials like metals, plastics, and composites. The key benefits of CNC include enhanced productivity, repeatability of processes, and the ability to produce complex shapes and parts with tight tolerances. This capability reduces human error and material waste, leading to cost savings and improved efficiency.
The software-driven nature of CNC allows for flexibility in production. Operators can easily reprogram machines to manufacture different parts without extensive retooling, making it ideal for small batch or customized production runs. Advanced CNC systems incorporate features like multi-axis machining, automatic tool changers, and real-time monitoring for further optimization of operations.
Moreover, CNC technology integrates with CAD/CAM software, enabling seamless transition from design to manufacturing. This integration facilitates rapid prototyping and iterative design improvements, accelerating time-to-market for new products.
In conclusion, CNC technology has transformed machine shops by streamlining manufacturing processes, increasing precision, and enabling cost-effective production of complex parts across diverse industries. Its continued evolution promises even greater efficiency and capabilities in the future of manufacturing.
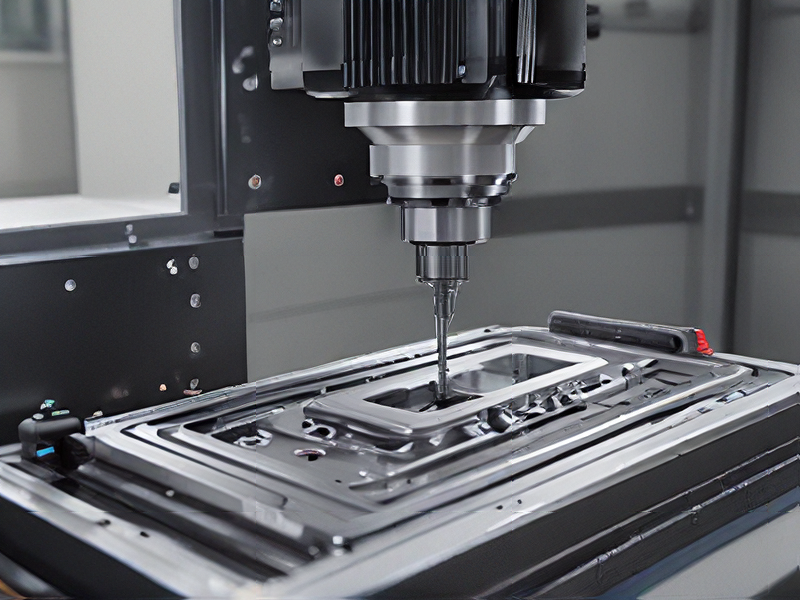
Quality Testing Methods for machine shop cnc and how to control quality
Quality control in a CNC machine shop involves several methods to ensure precision and reliability of manufactured parts. Key techniques include:
1. First Article Inspection (FAI): Conducting detailed checks on the first piece produced to verify it meets all specifications.
2. In-process Inspection: Monitoring critical dimensions and features during machining to catch deviations early.
3. Final Inspection: Comprehensive checks on finished parts against design specifications using measurement tools like CMMs (Coordinate Measuring Machines) and gauges.
4. Statistical Process Control (SPC): Analyzing data from machining processes to detect variations and maintain consistency.
5. Tool Calibration: Regularly calibrating cutting tools and measuring instruments to ensure accuracy.
6. Documentation and Traceability: Maintaining detailed records of inspections and production parameters for traceability and process improvement.
7. Training and Qualification: Ensuring operators are trained to use equipment properly and understand quality standards.
Effective quality control requires adherence to documented procedures, continuous training, and proactive problem-solving to maintain high standards and meet customer requirements consistently.

Tips for Procurement and Considerations when Purchasing from machine shop cnc
When procuring services from a CNC machine shop, consider the following tips and considerations to ensure a successful partnership and quality outcomes:
1. Capabilities and Expertise: Assess the machine shop’s capabilities, including the types of CNC machines they use, their experience with similar projects, and their expertise in handling specific materials or processes relevant to your needs.
2. Quality Assurance: Inquire about the shop’s quality control measures and certifications (e.g., ISO standards). Ensure they have rigorous inspection processes in place to maintain high standards throughout production.
3. Capacity and Lead Times: Understand the shop’s capacity to handle your project within your required timeframe. Discuss lead times, production schedules, and their ability to accommodate any fluctuations in demand.
4. Cost and Pricing Structure: Obtain detailed quotes that outline all costs involved, including setup fees, material costs, machining time, and any additional services. Clarify payment terms and conditions upfront.
5. Communication and Collaboration: Establish clear lines of communication from the outset. Ensure the shop can provide regular updates on the progress of your project and is responsive to any queries or concerns you may have.
6. Prototyping and Testing: If applicable, discuss options for prototyping and testing to validate designs before full-scale production. Determine if the shop offers prototyping services and their process for iterating designs.
7. Logistics and Shipping: Clarify logistics arrangements, including shipping methods, packaging requirements, and any associated costs. Ensure the shop can deliver finished components to your location efficiently and securely.
8. References and Reviews: Request references or read reviews from other clients to gauge the shop’s reputation for reliability, quality, and customer service.
9. Contractual Agreements: Review and finalize contractual agreements that clearly define project scope, deliverables, timelines, quality standards, and dispute resolution procedures.
10. Continuous Improvement: Inquire about the shop’s commitment to continuous improvement and innovation in CNC machining technologies. A forward-thinking approach can lead to better solutions and efficiencies over time.
By carefully considering these tips and factors when selecting a CNC machine shop, you can mitigate risks, ensure alignment with your project requirements, and foster a productive and beneficial partnership.

FAQs on Sourcing and Manufacturing from machine shop cnc in China
Certainly! Here are some FAQs regarding sourcing and manufacturing from CNC machine shops in China:
1. What types of CNC machining services do Chinese machine shops offer?
Chinese machine shops typically offer a wide range of CNC machining services, including milling, turning, drilling, and precision machining of various materials such as metals, plastics, and composites.
2. How can I find a reliable CNC machine shop in China?
Look for shops with certifications (ISO 9001, for instance), positive customer reviews, and a demonstrated track record of delivering quality products. Engaging through reputable sourcing platforms or industry referrals can also help.
3. What are the typical lead times for CNC machining in China?
Lead times can vary based on factors like part complexity, material availability, and shop capacity. On average, expect lead times ranging from a few days to several weeks, depending on the specifics of your order.
4. How can I ensure quality control when manufacturing in China?
Specify quality requirements clearly in your initial discussions and enforce quality checks throughout production. Consider third-party inspections or audits to verify compliance with standards and specifications.
5. What are the common challenges when sourcing from Chinese machine shops?
Challenges may include language barriers, cultural differences, intellectual property concerns, and logistical issues such as shipping and customs clearance. Effective communication and clear agreements can mitigate these challenges.
6. What are the advantages of sourcing CNC machining from China?
China offers competitive pricing due to lower labor and production costs, access to advanced machining technologies, and a large pool of skilled labor and suppliers.
Navigating these FAQs can help streamline your sourcing and manufacturing processes when working with CNC machine shops in China, ensuring smoother operations and satisfactory outcomes.
