Technology and Applications of numerical control machining
Numerical Control (NC) machining utilizes computerized systems to control machine tools in manufacturing processes. It revolutionized production by automating operations previously controlled manually. Here’s an overview of its technology and applications:
Technology:
NC machining replaces manual control with computerized instructions, known as G-code. G-code specifies coordinates and tool paths, guiding machines through precise movements. Modern systems integrate CAD (Computer-Aided Design) and CAM (Computer-Aided Manufacturing) software to streamline the process from design to execution. CNC (Computer Numerical Control) machines, a subset of NC, enhance capabilities with advanced features like multi-axis control and automated tool changers.
Applications:
1. Precision Manufacturing: NC machining achieves high accuracy and repeatability critical for aerospace, automotive, and medical industries. It fabricates complex parts with tight tolerances, enhancing product quality and consistency.
2. Prototyping and Customization: Ideal for rapid prototyping, NC machining swiftly transforms digital designs into physical prototypes. Customization is cost-effective, catering to diverse customer needs without tooling changes.
3. Mass Production: NC machining enables efficient mass production of standardized components. It optimizes production workflows, reducing lead times and minimizing waste compared to traditional methods.
4. Versatility Across Materials: From metals to plastics and composites, NC machining adapts to various materials. It accommodates intricate designs and diverse material properties, ensuring versatility in manufacturing applications.
5. Automation and Efficiency: Automation reduces labor costs and operator errors while increasing production efficiency. Continuous advancements in NC technology, such as real-time monitoring and predictive maintenance, further enhance operational reliability and productivity.
In conclusion, NC machining’s technological advancements and versatile applications underscore its pivotal role in modern manufacturing. From enhancing precision to enabling rapid prototyping and efficient mass production, it continues to drive innovation across industries worldwide.
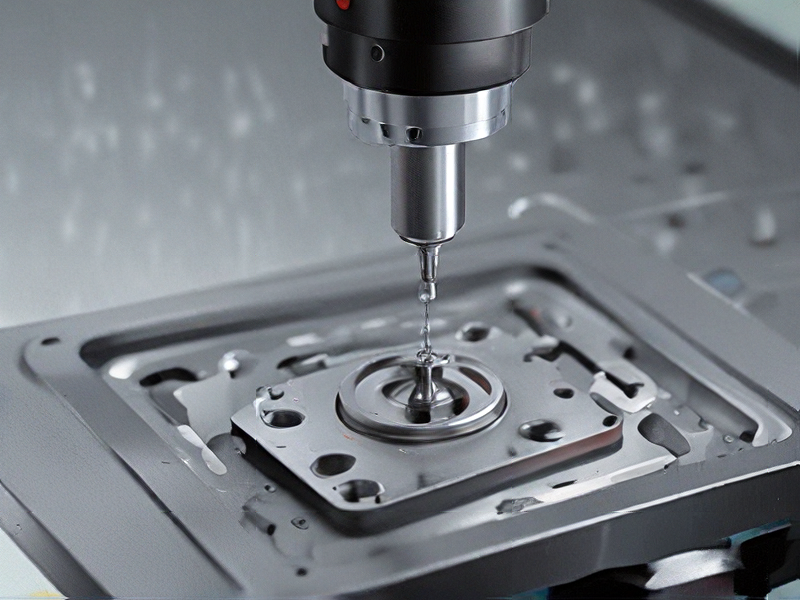
Quality Testing Methods for numerical control machining and how to control quality
Quality testing methods for numerical control (NC) machining involve several key approaches to ensure precision and consistency:
1. Dimensional Accuracy: Utilize precision measuring tools such as micrometers, calipers, and coordinate measuring machines (CMM) to verify part dimensions against CAD specifications.
2. Surface Finish Evaluation: Employ surface roughness testers to assess the smoothness and texture of machined surfaces, crucial for parts requiring low friction or aesthetic appeal.
3. Tool Wear Monitoring: Implement tool condition monitoring systems to detect wear or breakage early, preventing defects and ensuring tool longevity.
4. In-process Monitoring: Use sensors and probes integrated into the NC machines to monitor cutting forces, vibrations, and temperature, providing real-time feedback to adjust machining parameters.
5. Statistical Process Control (SPC): Apply SPC techniques to analyze process variability and ensure machining operations remain within acceptable limits, using control charts and data analysis.
To control quality effectively:
– Regular Calibration: Maintain and calibrate measuring instruments and NC machines to ensure accuracy and reliability.
– Operator Training: Train operators in machine programming, tooling setup, and quality inspection procedures to minimize errors and maximize efficiency.
– Documentation and Traceability: Document machining parameters, inspection results, and part history to trace issues and ensure compliance with quality standards.
– Continuous Improvement: Implement feedback mechanisms and root cause analysis to address quality deviations promptly and improve processes iteratively.
By integrating these methods and controls, manufacturers can enhance product quality, reduce scrap rates, and achieve consistent results in NC machining operations.
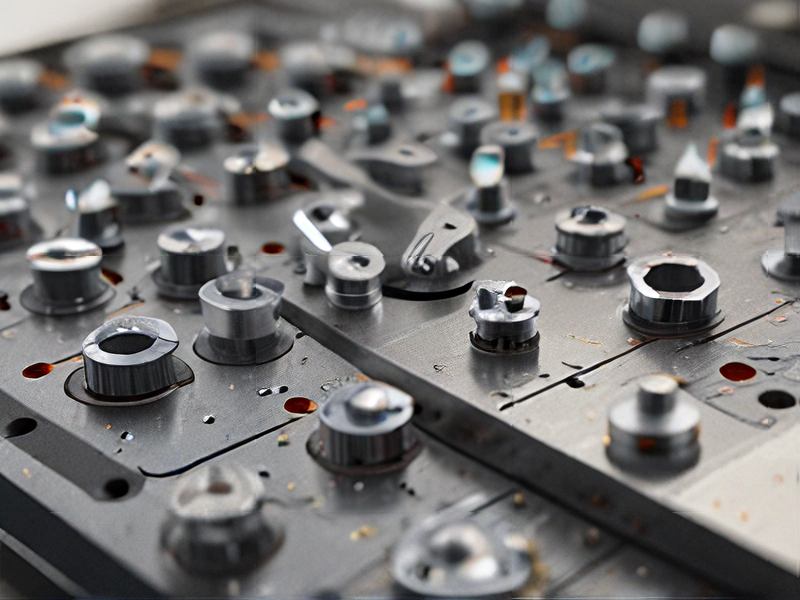
Tips for Procurement and Considerations when Purchasing from numerical control machining
When procuring from numerical control machining (NC machining), several critical considerations can ensure successful outcomes:
1. Technical Specifications: Clearly define your part requirements, including dimensions, tolerances, materials, and surface finish. NC machining capabilities vary, so ensure the supplier can meet your specifications.
2. Quality Assurance: Verify the supplier’s quality management system, certifications (e.g., ISO 9001), and inspection processes. Request sample parts or visit the facility if possible to assess quality firsthand.
3. Capacity and Capability: Evaluate the supplier’s equipment, expertise, and production capacity. Consider their experience with similar projects and their ability to handle your order volume within your timeline.
4. Cost and Pricing: Obtain detailed quotes that itemize costs for materials, machining, finishing, and any additional services. Compare pricing with multiple suppliers to ensure competitiveness without compromising quality.
5. Lead Times: Discuss lead times for both initial orders and ongoing production. Ensure the supplier can meet your delivery schedule, especially if you have strict deadlines.
6. Communication and Support: Establish clear communication channels and responsiveness expectations. A responsive supplier that provides regular updates can mitigate risks and ensure project alignment.
7. Flexibility and Scalability: Assess the supplier’s flexibility to accommodate changes in design or order volume. Determine their scalability in case your production needs increase in the future.
8. Logistics and Shipping: Discuss shipping options, packaging requirements, and logistics arrangements. Clarify responsibilities for handling customs, duties, and any international shipping requirements if applicable.
9. Reputation and References: Research the supplier’s reputation in the industry through reviews, testimonials, and references from past clients. A reliable supplier with positive feedback enhances confidence in your procurement decision.
10. Contractual Agreements: Ensure all terms, conditions, and warranties are clearly defined in a written contract. Address intellectual property rights, confidentiality, payment terms, and dispute resolution mechanisms.
By meticulously evaluating these factors and fostering a collaborative relationship with your chosen NC machining supplier, you can optimize procurement outcomes and achieve your manufacturing goals effectively.
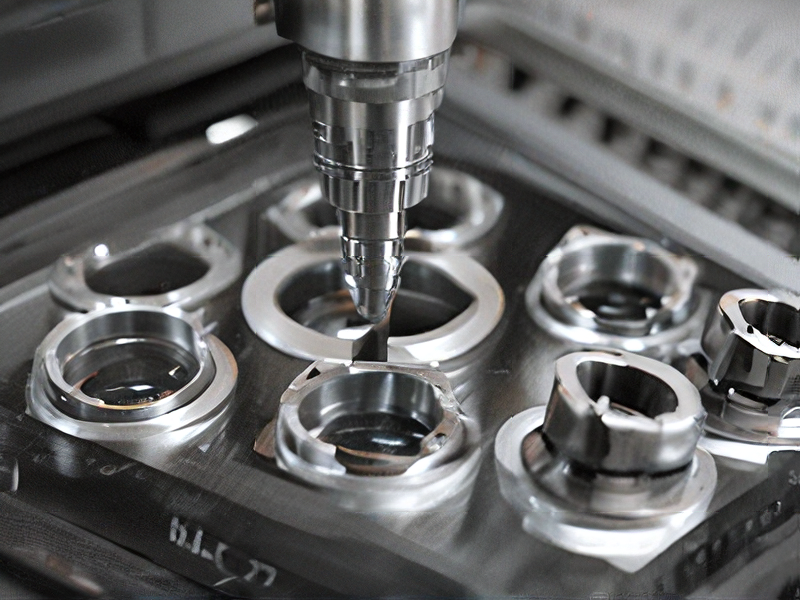
FAQs on Sourcing and Manufacturing from numerical control machining in China
When sourcing numerical control machining services from China, it’s essential to address several frequently asked questions (FAQs):
1. Quality Assurance: How can I ensure quality when outsourcing CNC machining to China? Opt for suppliers with ISO certifications or proven track records. Conducting thorough due diligence and requesting samples can also mitigate risks.
2. Communication: How do I overcome language barriers and ensure effective communication? Choose suppliers with English proficiency or employ translators if necessary. Clear and detailed communication from the outset is crucial.
3. Cost Considerations: What factors influence pricing for CNC machining in China? Costs can vary based on complexity, material specifications, batch size, and supplier capabilities. Obtain detailed quotes and consider negotiating for bulk orders.
4. Lead Times: How long does manufacturing typically take, and how can I expedite production? Lead times depend on project specifics and supplier capacity. Discuss timelines upfront and consider flexibility in scheduling to manage deadlines effectively.
5. Intellectual Property (IP): How can I protect my designs and IP rights when outsourcing to China? Use non-disclosure agreements (NDAs) and ensure suppliers adhere to confidentiality agreements. Consider legal advice for additional protection.
6. Logistics and Shipping: What are the logistics challenges, and how can I manage shipping efficiently? Factor in shipping costs, customs procedures, and potential delays. Engage reliable freight forwarders and track shipments closely.
7. Supplier Selection: How do I choose the right CNC machining supplier in China? Evaluate suppliers based on their experience, capabilities, customer reviews, and ability to meet your specific requirements. Consider visiting facilities if feasible.
By addressing these FAQs, businesses can navigate the complexities of sourcing and manufacturing CNC machining in China effectively, ensuring quality, cost-efficiency, and timely delivery of products.
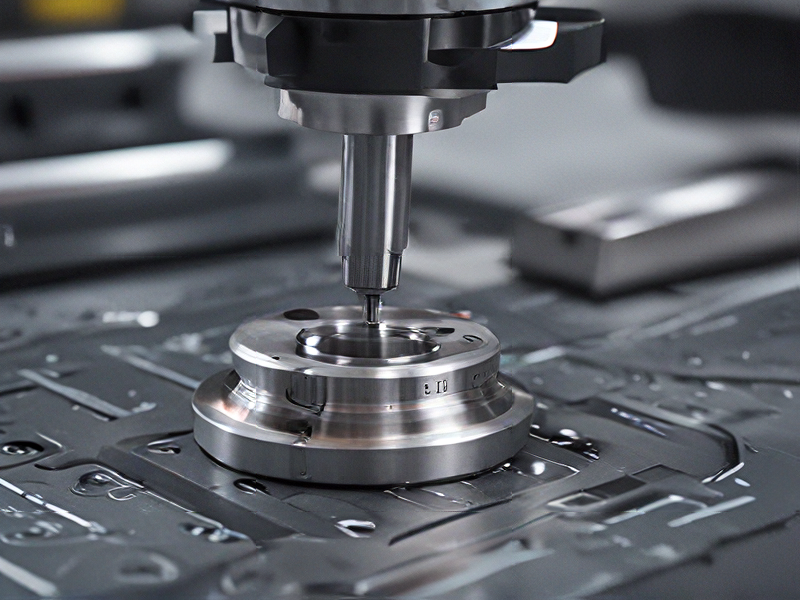