Technology and Applications of machining parts manufacturers
Machining parts manufacturers play a crucial role in modern industry, utilizing advanced technologies to produce precise components for various applications. Computer Numerical Control (CNC) machining is a cornerstone technology, enabling automated precision through computer programs that control machine tools like lathes, mills, and grinders. CNC machining ensures consistent quality and allows for complex geometries that are difficult to achieve manually.
Materials commonly machined include metals (aluminum, steel, titanium) and engineering plastics (nylon, ABS), each requiring specific techniques and tools. Advanced machining processes such as electrical discharge machining (EDM) and laser cutting further extend capabilities, particularly useful for intricate designs or hard-to-machine materials.
Applications span across industries:
1. Automotive: Precision-engineered components for engines, transmissions, and chassis.
2. Aerospace: Critical parts like turbine blades, landing gear components, and structural elements.
3. Medical: Implants, surgical instruments, and diagnostic equipment requiring high precision and biocompatibility.
4. Electronics: Small, intricate parts for consumer electronics and industrial equipment.
5. Energy: Components for turbines, generators, and oil exploration equipment.
Quality control is paramount, with manufacturers employing advanced metrology tools like coordinate measuring machines (CMM) and optical inspection systems to ensure adherence to tight tolerances.
Innovations in machining include additive manufacturing (3D printing), which complements subtractive methods by producing complex geometries with reduced waste. Hybrid machining combines additive and subtractive techniques for improved efficiency and versatility.
Looking ahead, trends include automation with robotics for lights-out manufacturing, where machines operate autonomously 24/7, enhancing productivity and reducing labor costs. Machining parts manufacturers continue to evolve with technology, driving innovation across industries and enabling the production of increasingly sophisticated and precise components.

Quality Testing Methods for machining parts manufacturers and how to control quality
Machining parts manufacturers employ several quality testing methods to ensure high standards:
1. Dimensional Inspection: Using precise measuring tools like calipers, micrometers, and coordinate measuring machines (CMMs) to verify dimensions against specifications.
2. Surface Finish Evaluation: Assessing the texture and smoothness of machined surfaces using profilometers or visual inspection.
3. Material Testing: Verifying material properties through methods like hardness testing, spectroscopy for composition analysis, and mechanical testing (e.g., tensile strength).
4. Non-Destructive Testing (NDT): Techniques such as ultrasonic testing, radiography, and magnetic particle inspection to detect internal defects without damaging the part.
5. Statistical Process Control (SPC): Monitoring machining processes in real-time using control charts to ensure consistency and identify deviations.
6. First Article Inspection (FAI): Thorough inspection of the first produced part to validate manufacturing processes and verify compliance with design requirements.
To control quality effectively, manufacturers should implement robust Quality Management Systems (QMS) that include:
– Documented Procedures: Clearly defined processes for machining, inspection, and quality assurance.
– Training Programs: Ensuring staff are skilled in inspection methods and understand quality standards.
– Supplier Quality Management: Evaluating and auditing suppliers to maintain consistent material and component quality.
– Continuous Improvement: Using feedback loops from inspections and customer feedback to refine processes and prevent defects.
– Traceability: Tracking parts throughout production to quickly address any quality issues that arise.
By integrating these methods and controls, machining parts manufacturers can uphold high quality standards and meet customer expectations reliably.

Tips for Procurement and Considerations when Purchasing from machining parts manufacturers
When procuring machining parts from manufacturers, consider these tips and factors:
1. Supplier Capability Assessment: Evaluate manufacturers based on their experience, certifications (ISO standards, for instance), and track record in producing similar parts. Look for expertise in materials and processes relevant to your needs.
2. Quality Assurance: Ensure the manufacturer has robust quality control measures in place. Request documentation such as inspection reports, quality certificates, and adherence to industry standards.
3. Cost vs. Value: While cost is crucial, prioritize value over the lowest price. Factors such as quality, reliability, and delivery timelines should also influence your decision.
4. Communication and Responsiveness: Choose manufacturers who are responsive to inquiries, provide clear communication, and are willing to collaborate closely throughout the production process.
5. Capacity and Scalability: Verify if the manufacturer has the capacity to handle your order volume and can scale production if needed without compromising quality or timelines.
6. Supply Chain Resilience: Assess the manufacturer’s ability to manage their supply chain effectively, especially regarding raw materials and potential disruptions.
7. Geographical Considerations: Evaluate the location of the manufacturer in relation to your own operations to manage logistics, shipping costs, and potential regulatory considerations.
8. Intellectual Property Protection: Ensure that the manufacturer respects your intellectual property rights and has measures in place to safeguard confidential information.
9. Sustainability and Compliance: Check if the manufacturer adheres to environmental regulations and practices sustainable manufacturing processes if these are priorities for your organization.
10. Long-Term Partnership Potential: Aim for a manufacturer who views the relationship as a partnership rather than a transaction, demonstrating willingness to grow and improve together.
By considering these factors, you can make informed decisions when selecting a machining parts manufacturer, ensuring quality, reliability, and alignment with your procurement goals.
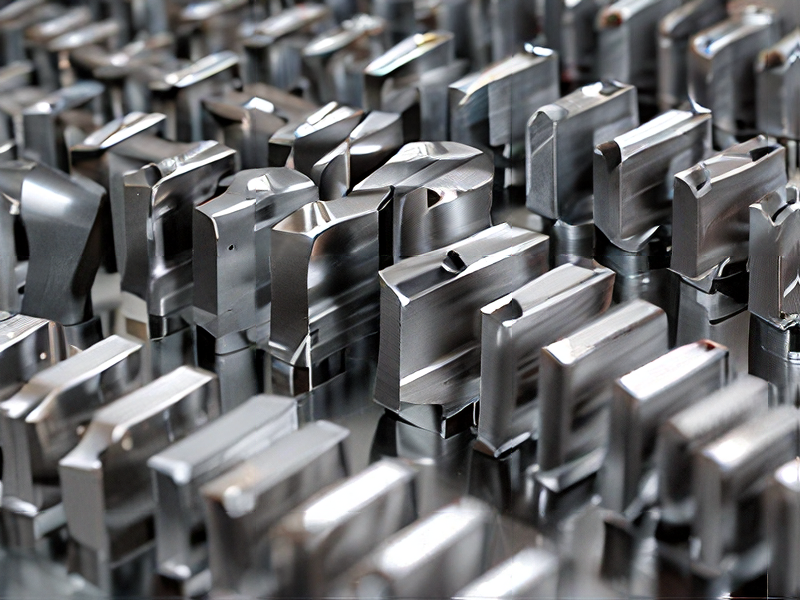
FAQs on Sourcing and Manufacturing from machining parts manufacturers in China
Certainly! Here are some frequently asked questions (FAQs) related to sourcing and manufacturing from machining parts manufacturers in China:
1. What are the typical lead times for machining parts from China?
Lead times can vary based on complexity and quantity but generally range from 4-12 weeks. It’s crucial to clarify this with your manufacturer upfront.
2. How do I ensure quality control when manufacturing parts in China?
Implementing rigorous quality control measures is essential. This includes on-site inspections, specifying quality standards in your contract, and possibly hiring a third-party inspection service.
3. What are common challenges when sourcing from China?
Challenges can include communication barriers, intellectual property concerns, and logistical issues like shipping and customs delays. Working with experienced partners can mitigate these risks.
4. How can I find a reliable machining parts manufacturer in China?
Utilize online platforms, industry directories, and referrals to find manufacturers with proven track records. Conduct thorough background checks and request samples before finalizing any agreements.
5. What are typical payment terms when dealing with Chinese manufacturers?
Payment terms often include initial deposits (30-50%) with the balance due upon completion or shipment. Negotiate terms that balance protection with incentivizing timely production.
6. How do tariffs and trade policies impact sourcing from China?
Stay informed about tariffs, trade agreements, and geopolitical factors that may affect pricing and logistics. This can influence sourcing decisions and budgeting.
7. What should I consider when selecting a machining technique?
Consider factors such as material properties, precision requirements, batch size, and cost-efficiency when choosing between CNC machining, casting, forging, or other methods.
Navigating sourcing and manufacturing in China requires careful planning, clear communication, and proactive quality management to ensure successful outcomes.
