Technology and Applications of auto parts suppliers
Auto parts suppliers play a crucial role in the automotive industry, providing components that are essential for vehicle manufacturing, maintenance, and repair. These suppliers leverage advanced technology and innovative applications to meet the demanding requirements of modern vehicles.
Technology: Auto parts suppliers utilize cutting-edge technology in various aspects of their operations. Advanced manufacturing techniques such as CNC machining, 3D printing, and robotic assembly are employed to produce high-precision components with tight tolerances. Computer-aided design (CAD) and simulation software help in prototyping and optimizing part designs for performance, durability, and safety. Additionally, suppliers integrate IoT (Internet of Things) devices into their production lines to monitor equipment performance, predict maintenance needs, and ensure consistent quality.
Applications: The applications of auto parts suppliers extend across a wide range of components and systems within vehicles. They supply critical parts like engines, transmissions, braking systems, and electrical components. For electric and hybrid vehicles, suppliers are at the forefront of developing batteries, electric motors, and sophisticated electronic control units (ECUs). Moreover, they provide aftermarket parts, ensuring vehicle owners have access to replacement components that meet original equipment manufacturer (OEM) standards.
In conclusion, auto parts suppliers combine technological innovation with specialized manufacturing capabilities to support the automotive industry’s evolution towards more efficient, safer, and technologically advanced vehicles. Their contributions are pivotal in driving forward the development and maintenance of vehicles worldwide.

Quality Testing Methods for auto parts suppliers and how to control quality
Auto parts suppliers employ several quality testing methods to ensure the reliability and performance of their products. These methods typically include:
1. Dimensional Inspection: Using precision tools like calipers and gauges to verify critical dimensions against specifications.
2. Material Testing: Conducting tests such as hardness tests, tensile tests, and spectroscopic analysis to ensure materials meet required standards.
3. Functional Testing: Simulating real-world conditions to assess how parts perform under stress, temperature variations, and operational loads.
4. Durability Testing: Subjecting parts to accelerated life tests or endurance tests to determine longevity and reliability over time.
5. Visual Inspection: Checking for surface defects, imperfections, and adherence to cosmetic standards.
To control quality effectively, suppliers implement several strategies:
1. Supplier Quality Assurance: Establishing stringent criteria for incoming materials and components from suppliers.
2. Process Control: Monitoring manufacturing processes closely to detect deviations early and prevent non-conforming products.
3. Quality Management Systems (QMS): Implementing ISO standards or other quality frameworks to ensure systematic quality control.
4. Statistical Process Control (SPC): Using statistical tools to monitor and control production processes, ensuring consistency and reliability.
5. Root Cause Analysis: Investigating and addressing the root causes of quality issues to prevent recurrence.
By combining these testing methods with robust quality control measures, auto parts suppliers can consistently deliver products that meet or exceed customer expectations for performance, reliability, and safety.

Tips for Procurement and Considerations when Purchasing from auto parts suppliers
When procuring auto parts from suppliers, consider these key tips:
1. Supplier Reliability: Choose suppliers with a proven track record of reliability and quality. Check reviews, testimonials, and industry reputation.
2. Quality Standards: Ensure parts meet or exceed industry standards (e.g., OEM specifications). Quality affects performance and customer satisfaction.
3. Price vs. Value: Balance cost-effectiveness with quality. Cheaper isn’t always better if it compromises reliability or performance.
4. Inventory and Availability: Suppliers should maintain adequate stock levels to avoid delays in delivery. Just-in-time inventory systems can be beneficial.
5. Warranty and Support: Verify warranty terms and after-sales support. Clear policies on returns, replacements, and technical assistance are crucial.
6. Compatibility and Fitment: Ensure parts are compatible with the vehicles you service. Incorrect fitments lead to customer dissatisfaction and additional costs.
7. Shipping and Logistics: Consider shipping costs, lead times, and logistics efficiency. Timely delivery impacts your ability to serve customers promptly.
8. Environmental and Ethical Practices: Prefer suppliers with eco-friendly practices and ethical labor standards. This aligns with corporate social responsibility goals.
9. Communication and Relationship: Build a good relationship with suppliers. Effective communication fosters understanding and resolves issues promptly.
10. Continuous Improvement: Regularly evaluate suppliers’ performance and seek feedback from your team and customers. Continuous improvement ensures long-term satisfaction.
By focusing on these considerations, you can streamline procurement processes, enhance customer satisfaction, and optimize operational efficiency in your auto parts business.

FAQs on Sourcing and Manufacturing from auto parts suppliers in China
Certainly! When sourcing auto parts from suppliers in China, here are some common FAQs and considerations:
1. Quality Assurance: How can I ensure the quality of auto parts from Chinese suppliers?
– Answer: It’s crucial to conduct thorough due diligence. Request samples, ask for certifications (like ISO, TS, or others relevant to your industry), and consider third-party inspections.
2. MOQ (Minimum Order Quantity): What are typical MOQs for auto parts?
– Answer: MOQs vary widely based on the part and supplier. Negotiate based on your needs and production capabilities.
3. Lead Times: What are standard lead times for manufacturing auto parts in China?
– Answer: Lead times can range from weeks to months. Clarify expectations upfront and establish clear timelines.
4. Costs and Pricing: How can I ensure competitive pricing?
– Answer: Obtain quotes from multiple suppliers, consider factors like materials and production volume, and negotiate based on market benchmarks.
5. Intellectual Property Protection: How can I protect my designs and IP?
– Answer: Use legal contracts (like NDA and manufacturing agreements), consider patents where applicable, and choose suppliers with a reputation for respecting IP rights.
6. Logistics and Shipping: What are the logistics considerations when importing auto parts?
– Answer: Factor in shipping costs, customs procedures, and any import tariffs or regulations. Work closely with freight forwarders for smooth delivery.
7. Communication: How can I overcome language barriers and ensure effective communication?
– Answer: Use clear, concise communication. Consider hiring translators or using bilingual project managers if necessary.
8. Payment Terms: What are typical payment terms with Chinese suppliers?
– Answer: Payment terms can vary (e.g., T/T, L/C). Negotiate terms that balance risk and cash flow.
By addressing these FAQs, you can navigate sourcing and manufacturing auto parts from suppliers in China more effectively, ensuring quality, cost-efficiency, and timely delivery.
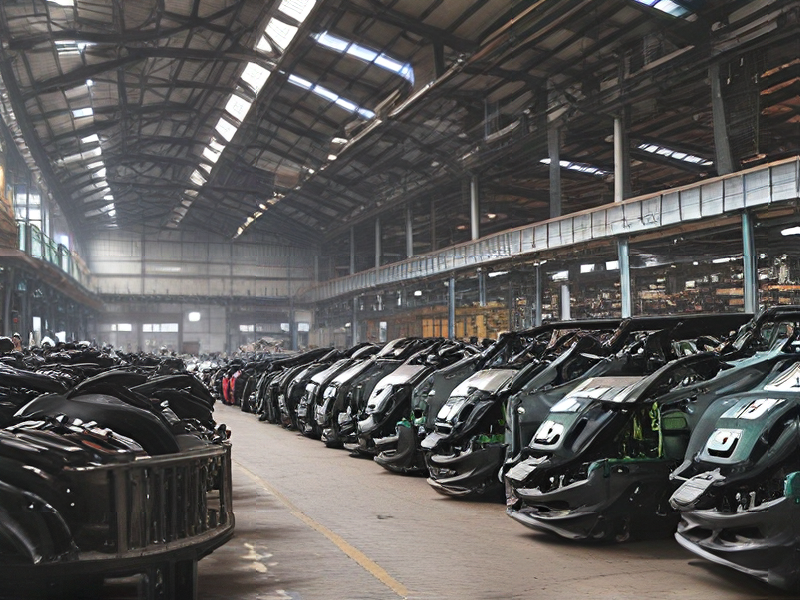