Technology and Applications of cnc machining shop
CNC (Computer Numerical Control) machining shops utilize computer-controlled machines to manufacture parts and components with high precision and efficiency. These shops employ various CNC machines such as mills, lathes, routers, and grinders, each tailored for specific tasks like cutting, drilling, shaping, and finishing raw materials like metals, plastics, and wood.
Applications of CNC machining are diverse and crucial across industries. In aerospace, CNC machines fabricate complex aircraft components with tight tolerances, ensuring safety and performance. Automotive manufacturing relies on CNC for producing engine parts, chassis components, and intricate molds for car bodies. In medical devices, CNC machining ensures the precise fabrication of implants, surgical tools, and prosthetics, crucial for patient care and treatment outcomes.
The technology’s flexibility enables rapid prototyping and iterative design processes, where CAD (Computer-Aided Design) models are directly translated into physical objects. This capability is invaluable in product development across consumer goods, electronics, and even artistic sculptures.
CNC machining shops also benefit from automation and robotics, enhancing production speed and consistency while minimizing human error. Advanced CNC systems integrate real-time monitoring and feedback loops to maintain quality and optimize workflows.
Overall, CNC machining plays a pivotal role in modern manufacturing, offering scalability, accuracy, and versatility across a wide range of applications, making it indispensable in industries seeking high-quality production and innovation.

Quality Testing Methods for cnc machining shop and how to control quality
Quality control in a CNC machining shop involves several key methods to ensure precision and consistency:
1. First Article Inspection (FAI): Conducted on the initial part to verify it meets all requirements before starting production.
2. In-Process Inspection: Regular checks during machining to detect deviations early, ensuring corrections are made promptly.
3. Final Inspection: Comprehensive examination of finished parts against specifications before delivery.
4. Statistical Process Control (SPC): Monitoring key process variables (e.g., dimensions, tolerances) to maintain consistency and identify trends.
5. Quality Management Systems (QMS): Implementing ISO 9001 standards ensures standardized procedures and continuous improvement.
6. Tooling and Equipment Maintenance: Regular calibration and maintenance of CNC machines and tools prevent errors.
7. Employee Training: Ensuring operators are trained in machining techniques and quality standards enhances accuracy.
8. Corrective and Preventive Actions (CAPA): Addressing non-conformities promptly and implementing preventive measures to avoid recurrence.
9. Documentation and Traceability: Maintaining comprehensive records of inspections and parts for traceability and accountability.
By integrating these methods, a CNC machining shop can uphold rigorous quality standards, minimize defects, and consistently deliver high-quality parts to customers.
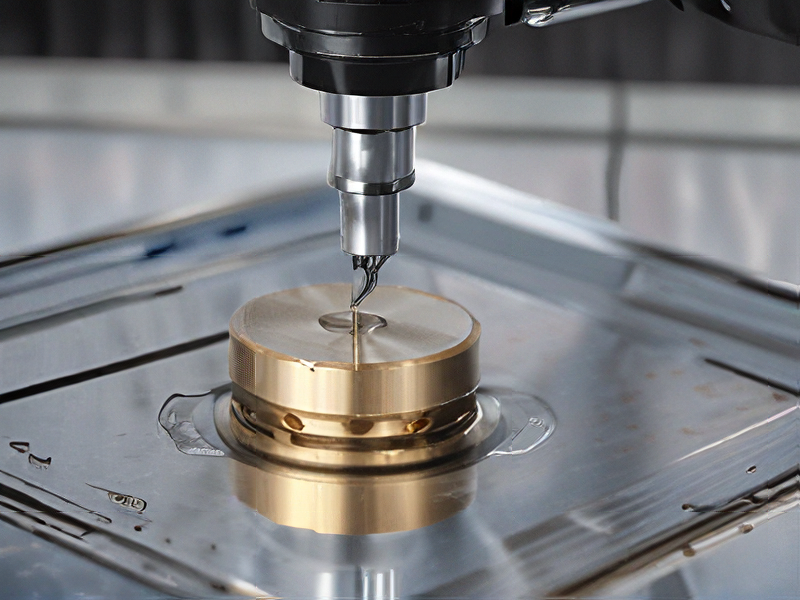
Tips for Procurement and Considerations when Purchasing from cnc machining shop
When selecting a CNC machining shop for procurement, consider the following tips:
1. Capabilities and Expertise: Ensure the shop has experience and capabilities relevant to your specific machining needs. Look for certifications or past projects similar to yours.
2. Quality Assurance: Check for quality control measures such as ISO certifications or adherence to industry standards (e.g., AS9100 for aerospace). Reviews and client testimonials can also provide insights into their quality reputation.
3. Technology and Equipment: Evaluate their CNC machines and technology. Updated equipment often means better precision and efficiency. Ask about their maintenance schedules to ensure reliability.
4. Cost and Pricing Structure: Compare quotes from multiple shops. Be wary of significantly low prices as they may compromise quality. Transparent pricing with no hidden costs is preferable.
5. Lead Times and Flexibility: Understand their production capacity and lead times. A reliable shop should provide clear timelines and be able to accommodate your schedule.
6. Communication and Support: Effective communication is crucial. Ensure they are responsive to inquiries and provide clear updates throughout the manufacturing process.
7. Material Selection and Sourcing: Check if they can source materials or if you need to provide them. Ensure they use high-quality materials suitable for your application.
8. Location and Logistics: Consider proximity to reduce shipping costs and lead times. Alternatively, confirm their ability to handle shipping logistics efficiently.
9. Customer Service and After-Sales Support: Evaluate their approach to customer service. A good shop should offer support after delivery, including addressing any issues that may arise.
10. Ethics and Sustainability: Assess their environmental practices and ethical standards, if important to your company’s values.
By carefully considering these factors, you can select a CNC machining shop that meets your quality, cost, and service expectations effectively.
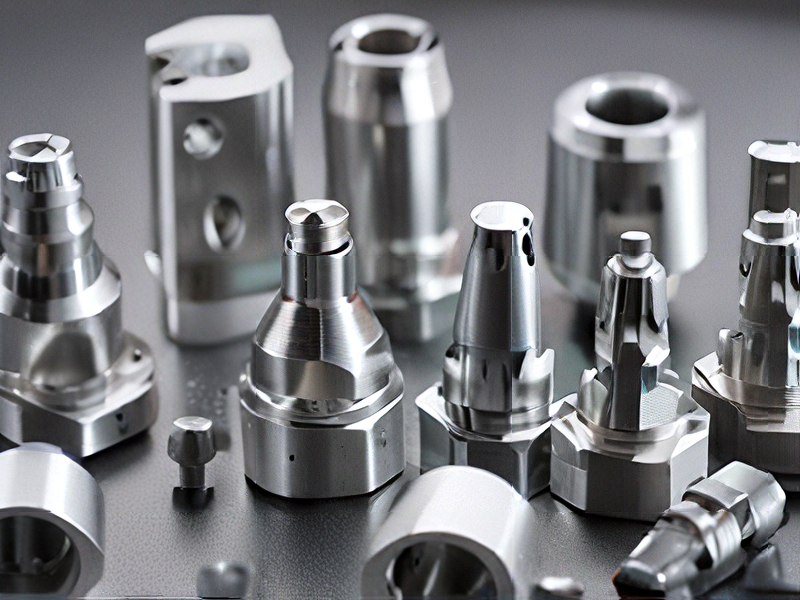
FAQs on Sourcing and Manufacturing from cnc machining shop in China
Certainly! Here are some frequently asked questions (FAQs) regarding sourcing and manufacturing from a CNC machining shop in China:
1. What types of CNC machining services do you offer?
Our shop offers a wide range of CNC machining services including milling, turning, drilling, and surface grinding.
2. What materials can you work with?
We can work with various materials such as metals (aluminum, steel, stainless steel, brass), plastics (ABS, POM, Nylon), and others upon request.
3. What is your production capacity?
Our shop has the capability to handle both small and large production runs, depending on your requirements.
4. What quality control measures do you have in place?
We adhere to strict quality control processes, including inspection at multiple stages of production to ensure precision and consistency.
5. What is your typical lead time for orders?
Lead times can vary based on the complexity and volume of the order, but we strive to meet reasonable deadlines to accommodate our clients.
6. Can you handle custom designs and prototypes?
Yes, we specialize in custom machining projects and can work with you to develop prototypes and bring your designs to life.
7. What are your shipping options?
We offer flexible shipping options including sea freight, air freight, and express courier services to ensure timely delivery worldwide.
8. How do you ensure intellectual property protection?
We take intellectual property rights seriously and are open to signing non-disclosure agreements (NDAs) to protect our clients’ designs and information.
9. Do you provide any additional services such as finishing or assembly?
Yes, we offer additional services including surface finishing (anodizing, plating, painting) and assembly if required.
10. What certifications or standards do you adhere to?
We adhere to ISO 9001 standards and can provide material certificates and inspection reports upon request.
These FAQs cover essential aspects of sourcing and manufacturing from a CNC machining shop in China, ensuring clarity and transparency in the process.
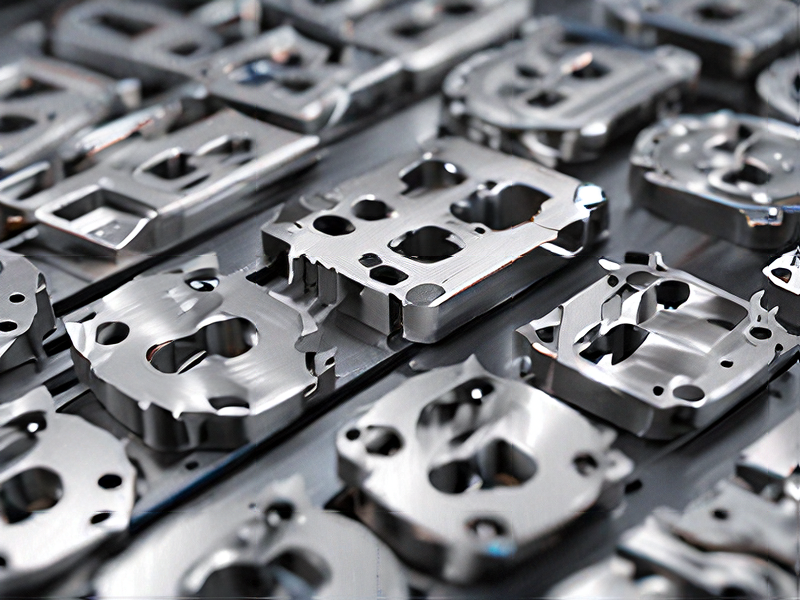