Technology and Applications of machine parts manufacturer
Machine parts manufacturers are pivotal in the industrial landscape, supplying components crucial for various technologies and applications. These manufacturers produce a wide array of parts, ranging from simple fasteners to complex precision components used in aerospace, automotive, medical devices, and beyond.
In aerospace, machine parts manufacturers create high-strength, lightweight components such as turbine blades and structural elements crucial for aircraft performance and safety. These parts often require advanced materials like titanium alloys or composites and must adhere to stringent quality standards to withstand extreme conditions.
In the automotive sector, manufacturers produce components that enhance vehicle efficiency, safety, and comfort. This includes engine parts, transmission components, braking systems, and suspension elements. Advanced manufacturing techniques such as CNC machining and 3D printing enable precise fabrication of these parts to meet demanding automotive specifications.
Medical device manufacturing relies heavily on machine parts suppliers to produce components for diagnostic equipment, surgical instruments, and implants. These parts must meet strict regulatory requirements for biocompatibility, sterilization, and precision to ensure patient safety and efficacy.
Industrial machinery and equipment manufacturers also depend on specialized parts like gears, bearings, and shafts to maintain operational reliability and efficiency. These components often require custom designs and materials to withstand heavy loads, high speeds, and harsh environments.
Overall, machine parts manufacturers play a critical role across diverse industries by providing essential components that enable technological advancement, improve product performance, and ensure safety and reliability in various applications. Their ability to innovate, adapt to new technologies, and maintain high-quality standards is essential for driving progress in modern engineering and manufacturing.
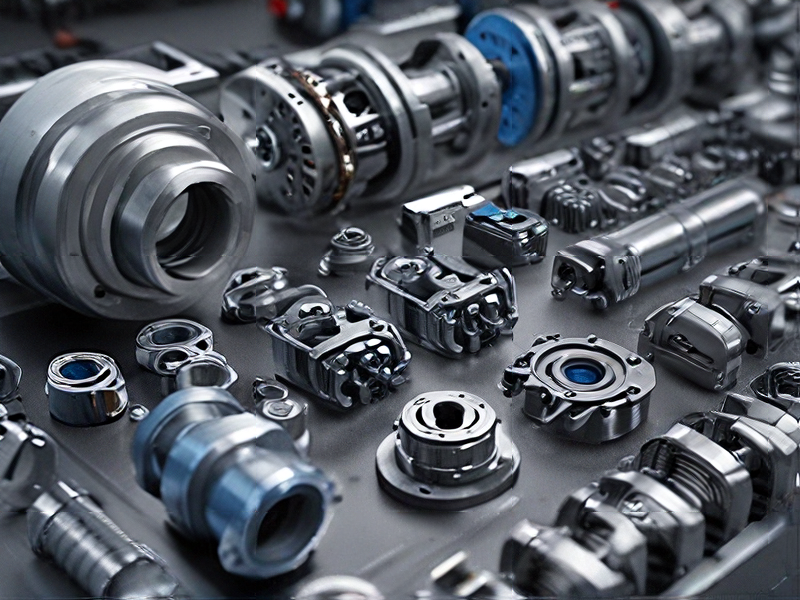
Quality Testing Methods for machine parts manufacturer and how to control quality
For a machine parts manufacturer, ensuring high-quality products is crucial. Here are effective quality testing methods and control measures:
1. Dimensional Inspection: Use precision tools like calipers, micrometers, and CMM (Coordinate Measuring Machine) to verify dimensions against specifications.
2. Material Testing: Employ techniques such as spectroscopy, hardness testing, and metallography to ensure materials meet required standards for strength and composition.
3. Visual Inspection: Train inspectors to detect surface defects, scratches, burrs, or other imperfections that could affect functionality or aesthetics.
4. Functional Testing: Conduct operational tests to verify parts perform as intended under realistic conditions. This might include endurance testing, pressure testing, or load testing.
5. Statistical Process Control (SPC): Monitor manufacturing processes using control charts to detect any deviations or trends that could impact quality.
6. Supplier Quality Assurance: Implement rigorous checks on incoming materials and components from suppliers to maintain consistency and reliability.
7. Documentation and Traceability: Maintain detailed records of inspections, tests, and quality control measures for traceability and continuous improvement.
To control quality effectively, establish clear quality standards and procedures, provide regular training for employees, invest in reliable testing equipment, and foster a culture of quality throughout the organization. Regular audits and feedback loops from customers can also provide valuable insights for ongoing improvement efforts.
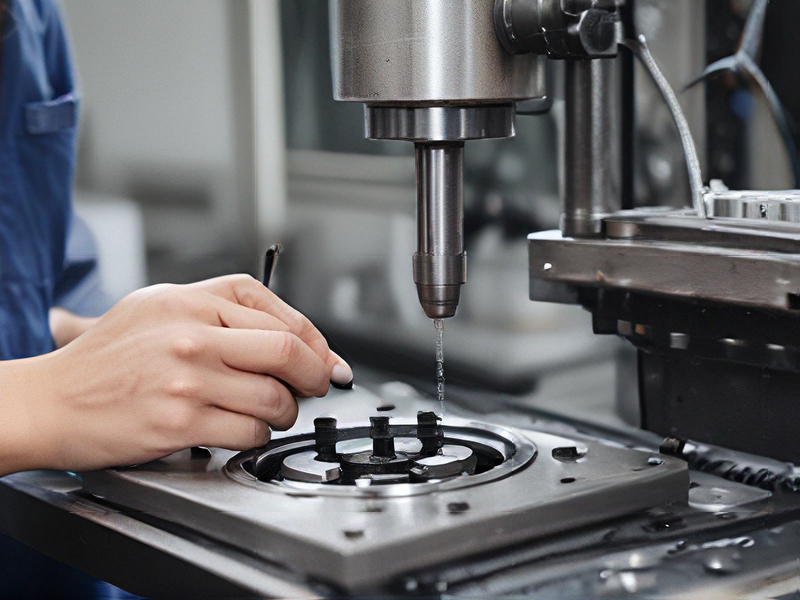
Tips for Procurement and Considerations when Purchasing from machine parts manufacturer
When procuring machine parts from manufacturers, consider these key tips and considerations:
1. Supplier Reliability: Ensure the manufacturer has a proven track record of delivering quality parts on time. Check references and reviews from other clients.
2. Quality Standards: Verify that the manufacturer adheres to industry standards and certifications (e.g., ISO 9001) to guarantee the parts meet your specifications.
3. Customization Capabilities: Assess if the manufacturer can customize parts to fit your specific requirements and if they have the technical expertise to handle complex designs.
4. Cost and Pricing: Compare quotes from multiple suppliers to ensure competitive pricing without compromising on quality. Factor in shipping costs and any potential tariffs.
5. Lead Times: Clarify production lead times to ensure they align with your project timelines. Discuss flexibility in case of urgent orders or changes in quantities.
6. Communication and Support: Choose a manufacturer who communicates clearly and promptly, offering good customer support throughout the procurement process.
7. Quality Control Processes: Inquire about the manufacturer’s quality control measures and inspection processes to minimize defects and ensure consistency.
8. Supplier Location: Consider the proximity of the manufacturer to your facility to potentially reduce shipping costs and transit times.
9. Environmental and Ethical Practices: Check if the manufacturer follows sustainable practices and ethical standards in their operations.
10. Contractual Agreements: Draft clear contracts that outline specifications, delivery terms, payment schedules, and warranties to avoid misunderstandings.
By carefully evaluating these factors, you can select a reliable machine parts manufacturer who meets your quality, timeline, and budget requirements effectively.
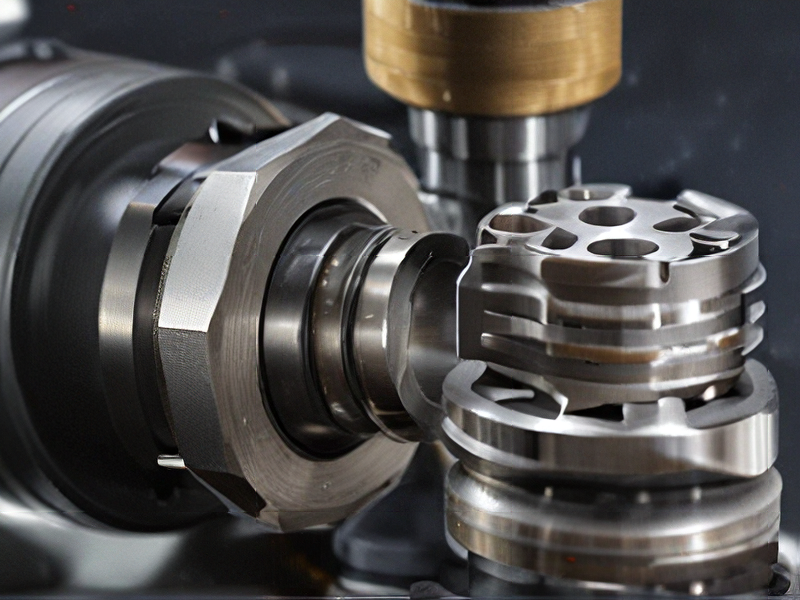
FAQs on Sourcing and Manufacturing from machine parts manufacturer in China
Certainly! Here are some FAQs addressing sourcing and manufacturing from a machine parts manufacturer in China:
1. What are the typical lead times for manufacturing machine parts in China?
Lead times can vary based on complexity and volume but generally range from 4 to 12 weeks.
2. How do you ensure the quality of machine parts produced in your facility?
We employ strict quality control measures, including inspections at each production stage and final quality checks before shipment.
3. What types of materials do you commonly work with?
We work with various metals such as steel, aluminum, and stainless steel, as well as plastics and composite materials.
4. Can you accommodate custom designs and specifications?
Yes, we specialize in custom manufacturing and can produce parts according to detailed drawings and specifications provided by clients.
5. What certifications and standards does your manufacturing facility adhere to?
Our facility adheres to ISO 9001 standards, ensuring consistent quality management throughout the production process.
6. What shipping options do you offer, and how do you handle logistics?
We provide flexible shipping options including sea freight and air freight, and our logistics team manages the entire process to ensure timely delivery.
7. How do you handle intellectual property protection and confidentiality?
We sign non-disclosure agreements (NDAs) with our clients to protect their designs and intellectual property throughout the manufacturing process.
8. What are your payment terms and methods accepted?
Payment terms are typically negotiated based on project scope and duration, with common methods including bank transfers and letters of credit.
9. Do you offer post-sales support or warranties?
Yes, we provide warranties on our products and offer ongoing support to address any issues that may arise post-delivery.
10. How do you handle communication and project updates with international clients?
We maintain regular communication via email, video calls, and project management tools to provide updates and ensure transparency throughout the manufacturing process.
These FAQs cover essential aspects of sourcing and manufacturing machine parts in China, providing insights into processes, quality control, logistics, and client communication.
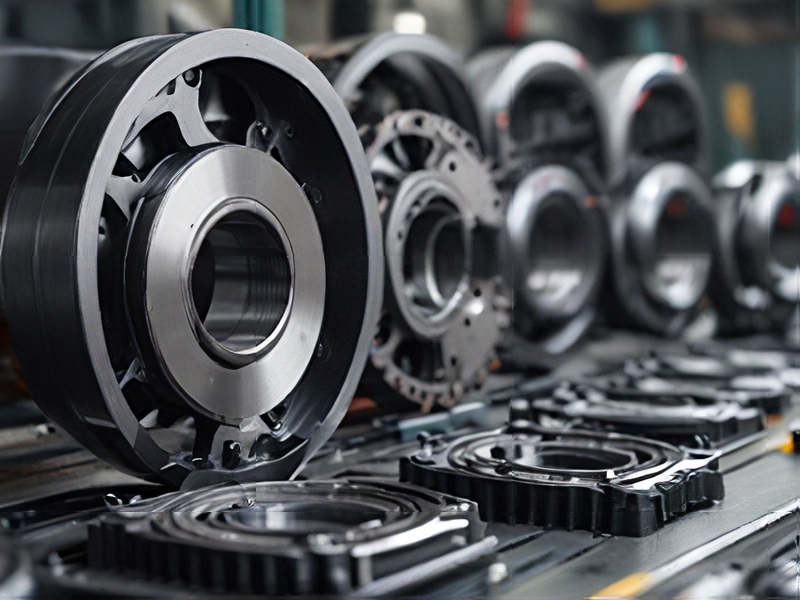