Technology and Applications of cnc machining shops
CNC machining shops utilize computer numerical control (CNC) systems to automate manufacturing processes with precision. These shops are integral to industries ranging from aerospace to automotive due to their ability to produce complex parts efficiently.
Technology: CNC machines interpret CAD (Computer-Aided Design) files to guide cutting tools along multiple axes with high accuracy. Modern advancements include multi-axis machining, allowing intricate geometries to be created in a single setup. High-speed machining (HSM) techniques enhance productivity by reducing cycle times, while adaptive control systems adjust cutting parameters in real-time for optimal results. Additionally, robotics and automation integrate tasks such as loading, unloading, and quality inspection, further streamlining operations.
Applications: CNC machining is pivotal in prototyping and production. It fabricates components for engines, turbines, and medical devices with exacting tolerances and repeatability. Industries benefit from the versatility to work with various materials like metals, plastics, and composites. CNC shops cater to bespoke and low-volume projects as well as mass production, ensuring scalability and cost-effectiveness.
Future Trends: Industry 4.0 trends see CNC shops adopting IoT (Internet of Things) for remote monitoring and predictive maintenance. Additive manufacturing integration enables hybrid processes for complex assemblies. Advances in software improve simulation and optimization, reducing lead times and material waste.
In summary, CNC machining shops leverage advanced technologies to meet diverse manufacturing needs efficiently and precisely, playing a crucial role in modern industrial production.
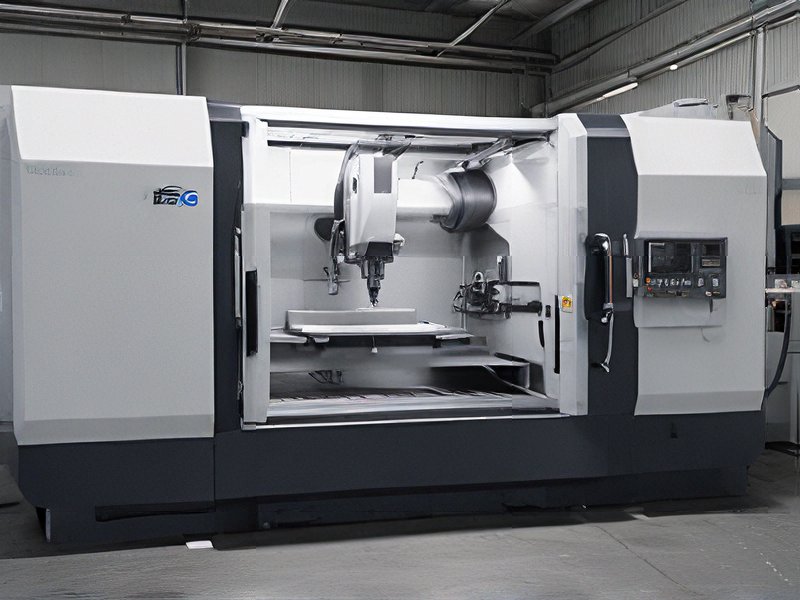
Quality Testing Methods for cnc machining shops and how to control quality
Quality testing in CNC machining shops involves several key methods to ensure precision and consistency:
1. Dimensional Inspection: Using coordinate measuring machines (CMMs) and gauges to verify part dimensions against CAD specifications.
2. Surface Finish Evaluation: Employing surface roughness testers to assess the quality of machined surfaces.
3. Visual Inspection: Inspecting parts for defects such as scratches, burrs, or tool marks.
4. Material Hardness Testing: Ensuring parts meet specified hardness requirements using hardness testers.
5. First Article Inspection (FAI): Thoroughly inspecting the first produced part to validate manufacturing processes and setup.
To control quality effectively:
1. Establish Quality Standards: Define clear tolerances and acceptance criteria for all parts.
2. Routine Calibration: Regularly calibrate machines and inspection tools to maintain accuracy.
3. Process Monitoring: Implement process controls and real-time monitoring to detect deviations promptly.
4. Training and Skill Development: Train operators on inspection techniques and quality standards.
5. Documentation and Traceability: Maintain detailed records of inspections and testing results for traceability and continuous improvement.
By integrating these methods and controls, CNC machining shops can consistently produce high-quality parts that meet customer specifications and industry standards.
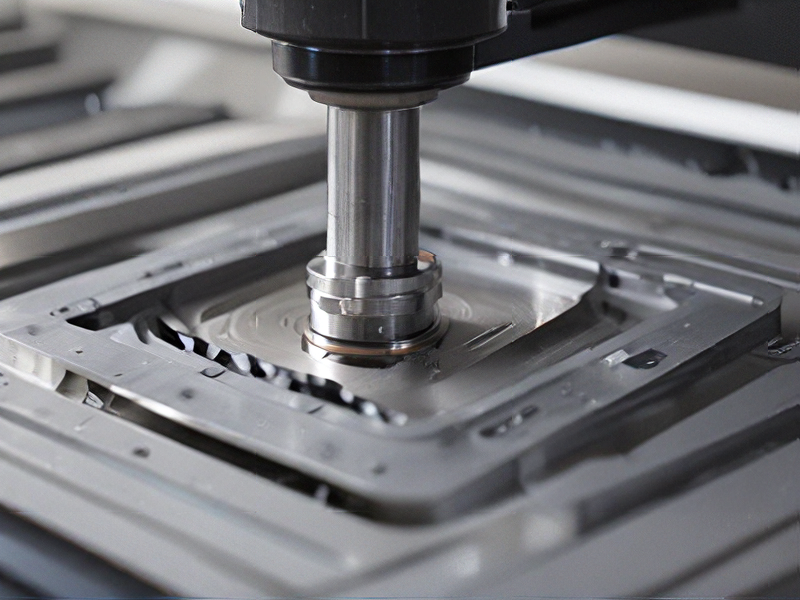
Tips for Procurement and Considerations when Purchasing from cnc machining shops
When procuring from CNC machining shops, consider the following tips and considerations:
1. Capability Assessment: Evaluate the shop’s CNC capabilities, including the types of machines they use (e.g., multi-axis, Swiss-style), materials they work with (metals, plastics), and their proficiency in complex geometries or tight tolerances.
2. Quality Standards: Ensure the shop adheres to quality standards such as ISO certifications or industry-specific standards (e.g., AS9100 for aerospace). Request samples or inspect previous work to gauge their quality.
3. Experience and Expertise: Prefer shops with experience in your industry or similar projects. Look for reviews, testimonials, or case studies showcasing their expertise and successful projects.
4. Capacity and Lead Times: Verify if the shop has the capacity to handle your order volume within your required timeframe. Discuss lead times, production schedules, and their ability to meet deadlines.
5. Cost and Pricing Structure: Compare pricing structures, including setup fees, material costs, and any additional charges. Beware of unusually low prices that could indicate compromised quality or hidden costs.
6. Communication and Collaboration: Establish clear communication channels and assess their responsiveness. A good CNC shop should be open to discussing project details, providing updates, and addressing concerns promptly.
7. Prototyping and Testing: If applicable, inquire about their prototyping capabilities and testing procedures. Ensure they can accommodate iterative design changes and conduct necessary tests before full production.
8. Logistics and Shipping: Consider logistics aspects such as shipping options, packaging, and delivery timelines. Clarify responsibilities regarding shipping costs and handling of finished parts.
9. Supplier Stability: Evaluate the shop’s financial stability and reliability as a long-term supplier. Check their track record with other clients and their ability to manage fluctuations in demand.
10. Contractual Agreements: Formalize agreements with clear terms regarding specifications, quality expectations, timelines, and intellectual property rights.
By carefully assessing these factors, you can ensure a smooth procurement process and establish a reliable partnership with a CNC machining shop that meets your specific needs and requirements.
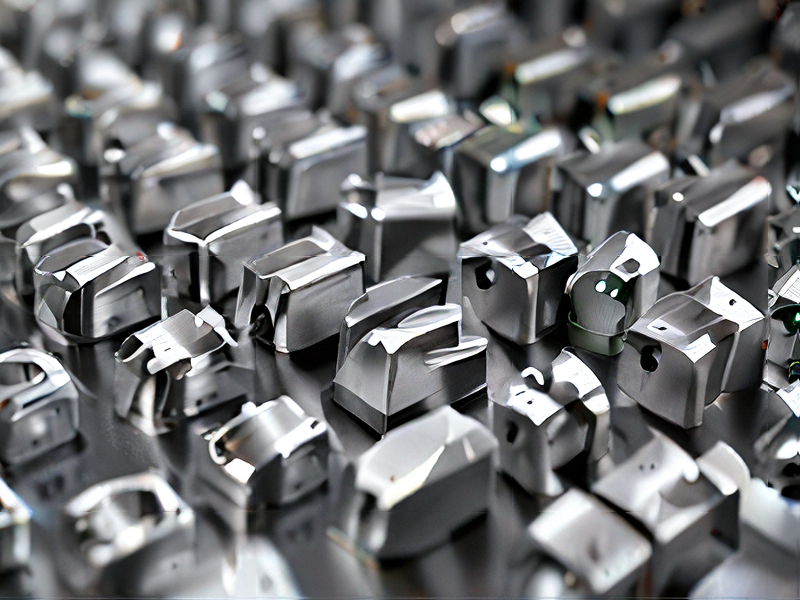
FAQs on Sourcing and Manufacturing from cnc machining shops in China
When sourcing and manufacturing from CNC machining shops in China, it’s important to consider several FAQs:
1. Quality Assurance: How do CNC shops ensure quality standards? Many reputable shops use ISO certifications and implement rigorous quality control processes.
2. Communication: How effective is communication with Chinese CNC shops? Clear communication channels are crucial; ensure specifications and expectations are clearly understood.
3. Lead Times: What are typical lead times for CNC machining in China? Lead times vary but can be influenced by factors like complexity, quantity, and shop capacity.
4. Costs: How do costs compare to other regions? China often offers competitive pricing due to lower labor and overhead costs, but prices can vary widely based on project specifics.
5. Intellectual Property Protection: What measures are in place to protect intellectual property? Ensure CNC shops have confidentiality agreements and respect IP rights.
6. Logistics: How are shipping and logistics handled? Consider transportation costs, lead times, and import/export regulations.
7. Capacity and Scalability: Can CNC shops handle large orders or sudden increases in demand? Assess their capacity and scalability to meet your business needs.
8. Payment Terms: What are typical payment terms? Negotiate clear payment terms to avoid misunderstandings.
9. References and Reviews: Can the CNC shop provide references or customer reviews? Checking testimonials and reviews can offer insights into their reputation.
10. Cultural Considerations: Are there cultural differences that may affect business interactions? Understanding cultural norms can aid in building effective partnerships.
Navigating these FAQs can help you make informed decisions when sourcing and manufacturing from CNC machining shops in China, ensuring a smooth and productive business relationship.
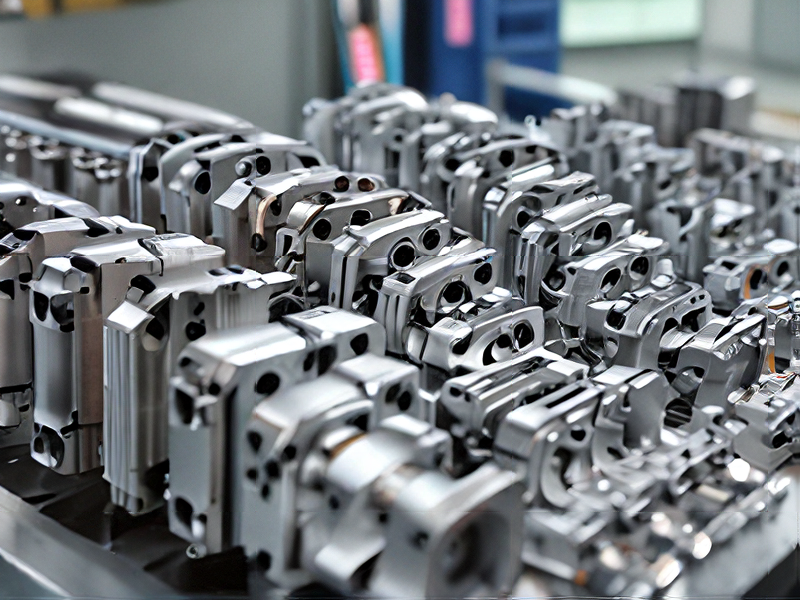