Technology and Applications of galvanized versus stainless steel
Galvanized steel and stainless steel are distinct materials with unique properties suitable for various applications.
Galvanized Steel:
Galvanized steel is steel coated with a layer of zinc through a process called galvanization. This coating protects the underlying steel from corrosion, making it ideal for outdoor and industrial applications where exposure to moisture and other elements is common. Common uses include roofing, fencing, automotive parts, and HVAC systems. It is relatively inexpensive compared to stainless steel, which makes it a cost-effective choice for large-scale projects where corrosion resistance is crucial but absolute longevity is not a primary concern.
Stainless Steel:
Stainless steel, on the other hand, contains chromium, which forms a passive oxide layer on its surface when exposed to oxygen. This layer prevents corrosion and rust, even in harsh environments. Stainless steel is highly durable, aesthetically pleasing, and resistant to staining, making it suitable for applications requiring hygiene, such as kitchen appliances, medical equipment, architectural facades, and marine environments. It is more expensive than galvanized steel but offers superior longevity and a more polished appearance.
Comparison:
In summary, the choice between galvanized and stainless steel depends on the specific requirements of the application. Galvanized steel is cost-effective and provides good corrosion protection for less demanding environments. In contrast, stainless steel offers unparalleled durability, hygiene, and aesthetic appeal, albeit at a higher cost. Understanding these differences helps in selecting the right material for each application, balancing performance requirements with budget considerations.

Quality Testing Methods for galvanized versus stainless steel and how to control quality
Quality testing methods for galvanized and stainless steel typically focus on different properties due to their distinct compositions and intended uses:
Galvanized Steel:
1. Visual Inspection: Check for uniform coating and absence of defects like bare spots or rough areas.
2. Coating Thickness Measurement: Using techniques like magnetic induction or eddy current to ensure adequate zinc coating thickness.
3. Adhesion Test: Assess the bond strength between the zinc coating and the steel substrate.
4. Salt Spray Test: Evaluate corrosion resistance by exposing samples to a salt mist environment.
5. Coating Weight Test: Weighing samples before and after stripping the zinc to determine the coating weight.
Stainless Steel:
1. Visual Inspection: Look for surface defects such as scratches, pits, or contamination.
2. Chemical Composition Analysis: Verify the elemental composition to ensure it meets specified grades (e.g., ASTM standards).
3. Mechanical Properties Testing: Assess strength, hardness, and ductility through tests like tensile and hardness testing.
4. Corrosion Resistance Testing: Perform tests like salt spray, crevice corrosion, or electrochemical methods to evaluate resistance to corrosion.
5. Surface Finish Evaluation: Measure roughness and finish consistency using tools like profilometers.
Quality Control Measures:
– Standard Operating Procedures (SOPs): Clearly define testing procedures and criteria for acceptance.
– Regular Inspection: Implement routine checks during manufacturing to catch deviations early.
– Calibration of Equipment: Ensure that measurement tools are calibrated regularly for accurate results.
– Supplier Audits: Verify the quality management systems of suppliers to ensure consistent material quality.
– Training Programs: Educate personnel on quality standards and testing methods to enhance competency.
By employing these methods and control measures, manufacturers can ensure that both galvanized and stainless steel products meet required quality standards for their intended applications.

Tips for Procurement and Considerations when Purchasing from galvanized versus stainless steel
Procurement Tips:
1. Evaluate Requirements: Understand the specific needs of your project, including environmental conditions, load-bearing requirements, and aesthetic preferences.
2. Supplier Vetting: Choose reputable suppliers with proven track records. Verify certifications, quality standards, and customer reviews.
3. Cost Analysis: Compare the total cost of ownership, not just the initial purchase price. Consider maintenance, longevity, and potential downtime costs.
4. Material Specifications: Ensure materials meet industry standards and project specifications. Request material certifications and test reports.
5. Lead Time: Consider supplier lead times and ensure they align with your project timeline to avoid delays.
Galvanized Steel Considerations:
1. Corrosion Resistance: Galvanized steel is coated with zinc, offering moderate corrosion resistance suitable for less aggressive environments.
2. Cost: Generally less expensive than stainless steel, making it a cost-effective choice for projects with budget constraints.
3. Durability: While durable, galvanized steel can suffer from zinc layer wear over time, particularly in harsh environments.
4. Maintenance: Requires periodic inspections and maintenance, especially in coastal or industrial areas where corrosion can be more aggressive.
5. Applications: Ideal for outdoor structures, roofing, and automotive parts where moderate corrosion resistance is sufficient.
Stainless Steel Considerations:
1. Corrosion Resistance: Superior to galvanized steel, particularly in harsh environments, due to the presence of chromium which forms a passive protective layer.
2. Cost: More expensive upfront but can be cost-effective long-term due to lower maintenance and longer lifespan.
3. Durability: Highly durable and resistant to rust, staining, and corrosion, making it suitable for both indoor and outdoor use.
4. Maintenance: Low maintenance with infrequent need for inspections and repairs.
5. Applications: Suitable for high-corrosion environments such as marine, chemical, and food processing industries, as well as for high-end architectural features.
In summary, the choice between galvanized and stainless steel depends on budget, environmental conditions, and long-term maintenance considerations. Proper evaluation of these factors will ensure the selection of the most suitable material for your project.

FAQs on Sourcing and Manufacturing from galvanized versus stainless steel in China
FAQs on Sourcing and Manufacturing from Galvanized vs. Stainless Steel in China
#### 1. What are the main differences between galvanized steel and stainless steel?
– Galvanized Steel: Coated with a layer of zinc to prevent corrosion. It is typically cheaper but less durable in harsh environments.
– Stainless Steel: Contains chromium, providing inherent corrosion resistance. It is more durable and suitable for a wider range of applications but is more expensive.
#### 2. Why source steel from China?
– Cost-Effectiveness: Lower manufacturing costs due to economies of scale and lower labor costs.
– Diverse Supply Chain: China offers a vast network of suppliers with various capabilities and specializations.
– Customization: Chinese manufacturers can often provide customized solutions to meet specific requirements.
#### 3. What are the quality considerations for galvanized steel from China?
– Zinc Coating Thickness: Ensure the coating is thick enough to provide adequate corrosion resistance.
– Material Grade: Verify the steel grade to ensure it meets required specifications.
– Certification: Check for ISO or other relevant certifications to ensure quality standards are met.
#### 4. What are the quality considerations for stainless steel from China?
– Chromium Content: Ensure the stainless steel has the appropriate chromium content (usually at least 10.5%) for corrosion resistance.
– Material Grade: Verify the grade (e.g., 304, 316) to match the intended application.
– Certification: Look for certifications like ISO 9001 to ensure quality control.
#### 5. How to verify the credibility of Chinese suppliers?
– Factory Audits: Conduct on-site inspections or hire third-party auditors.
– References and Reviews: Check supplier references and online reviews.
– Sample Testing: Request samples and conduct rigorous testing before placing bulk orders.
#### 6. What are the logistical considerations?
– Shipping Costs: Factor in the cost of shipping, including tariffs and duties.
– Lead Times: Account for manufacturing and shipping lead times to avoid delays.
– Customs and Regulations: Ensure compliance with import regulations and standards of your country.
#### 7. Which steel type is better for specific applications?
– Galvanized Steel: Best for projects with lower budgets and environments with moderate exposure to moisture and corrosion.
– Stainless Steel: Ideal for applications requiring high durability, aesthetic appeal, and exposure to harsh environments (e.g., marine, chemical).
By understanding these factors, businesses can make informed decisions when sourcing galvanized or stainless steel from China.
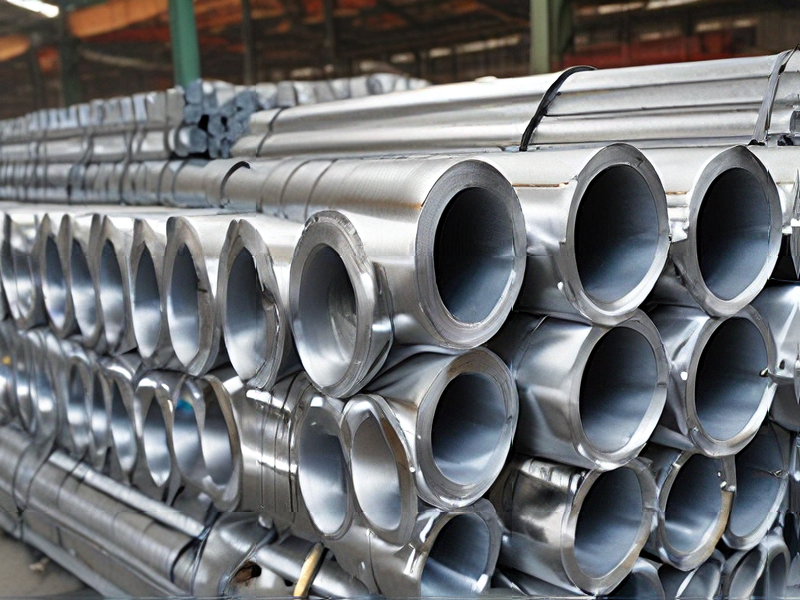