Technology and Applications of stainless steel vs galvanized
Technology and Applications of Stainless Steel vs. Galvanized Steel
#### Stainless Steel
Technology: Stainless steel is an alloy of iron with a minimum of 10.5% chromium, which forms a passive layer of chromium oxide, preventing corrosion. Other elements like nickel and molybdenum are added to enhance properties such as strength, ductility, and resistance to corrosion and high temperatures.
Applications:
1. Architecture and Construction: Used for structural components, facades, and roofing due to its aesthetic appeal and durability.
2. Medical Equipment: Favored for surgical instruments and implants because of its biocompatibility and ease of sterilization.
3. Food and Beverage: Employed in kitchen equipment, storage tanks, and food processing plants for its non-reactivity and hygiene.
4. Automotive and Aerospace: Utilized in exhaust systems, aircraft frames, and components due to its strength-to-weight ratio and resistance to extreme conditions.
#### Galvanized Steel
Technology: Galvanized steel involves coating steel with a layer of zinc, either through hot-dip galvanizing or electro-galvanizing. The zinc layer serves as a sacrificial anode, protecting the underlying steel from corrosion.
Applications:
1. Construction: Commonly used in structural beams, roofing, and fencing for its cost-effectiveness and rust resistance.
2. Automotive: Applied in body panels and underbody parts to prevent rust and prolong vehicle life.
3. HVAC Systems: Utilized in ductwork and outdoor units due to its corrosion resistance.
4. Agricultural Equipment: Employed in machinery and storage facilities to withstand harsh environmental conditions.
Comparison
– Corrosion Resistance: Stainless steel offers superior long-term resistance compared to galvanized steel, which may degrade over time as the zinc layer wears off.
– Cost: Galvanized steel is generally more cost-effective than stainless steel, making it a preferred choice for budget-sensitive projects.
– Strength and Durability: Stainless steel is stronger and more durable, especially in high-stress and high-temperature environments.
In summary, stainless steel is preferred for applications requiring high durability, aesthetic appeal, and corrosion resistance, while galvanized steel is favored for its cost-effectiveness and adequate protection in less demanding environments.

Quality Testing Methods for stainless steel vs galvanized and how to control quality
Quality Testing Methods for Stainless Steel vs. Galvanized Steel
Stainless Steel:
1. Chemical Analysis: Use spectrometers to verify alloy composition.
2. Mechanical Testing: Perform tensile and hardness tests to assess strength and ductility.
3. Corrosion Resistance Tests: Salt spray tests or immersion tests in acidic solutions to gauge resistance.
4. Non-Destructive Testing (NDT): Employ ultrasonic, radiographic, and dye penetrant tests to detect internal and surface flaws.
5. Visual Inspection: Check for surface defects, such as pitting or scaling.
Galvanized Steel:
1. Coating Thickness Measurement: Use magnetic gauges or X-ray fluorescence (XRF) to measure the zinc layer thickness.
2. Adhesion Tests: Conduct bend tests or impact tests to ensure the zinc coating adheres well.
3. Corrosion Resistance Tests: Perform salt spray tests to evaluate the durability of the zinc coating.
4. Mechanical Testing: Similar to stainless steel, including tensile and hardness tests.
5. Visual Inspection: Inspect for uniformity of the coating, and any signs of peeling or blistering.
Quality Control Methods:
1. Material Certification: Require supplier certifications and perform incoming material inspections to verify compliance with standards.
2. Standard Operating Procedures (SOPs): Implement SOPs for all testing methods and ensure technicians are trained.
3. Statistical Process Control (SPC): Use SPC to monitor and control the manufacturing process, identifying variations before defects occur.
4. Regular Audits: Conduct internal and external audits to ensure adherence to quality standards.
5. Documentation: Maintain detailed records of all tests and inspections for traceability.
6. Continuous Improvement: Use feedback from testing and inspections to continuously improve processes.
These methods and controls help ensure that both stainless steel and galvanized steel meet the necessary quality standards for their respective applications.
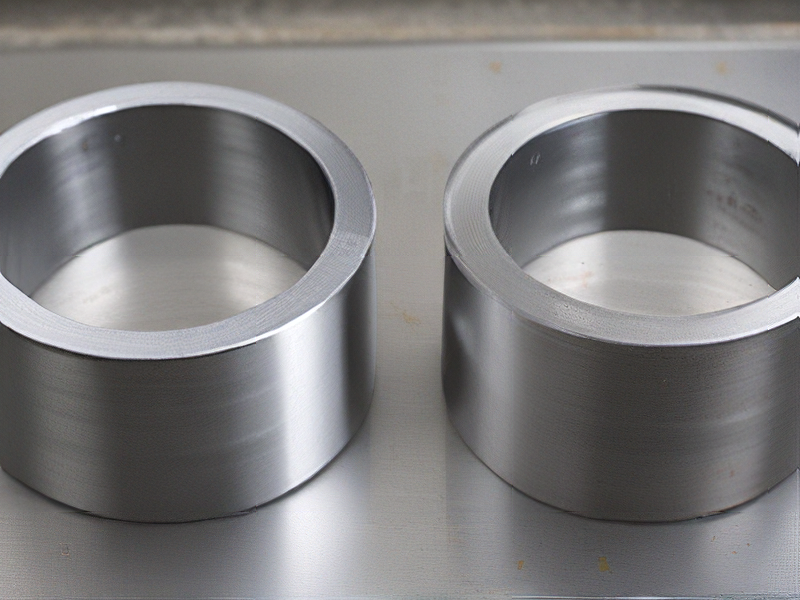
Tips for Procurement and Considerations when Purchasing from stainless steel vs galvanized
When procuring materials, choosing between stainless steel and galvanized steel involves key considerations:
Stainless Steel
Advantages:
1. Corrosion Resistance: Stainless steel is highly resistant to rust and corrosion, making it ideal for environments exposed to moisture, chemicals, and saltwater.
2. Durability: It is stronger and more durable than galvanized steel, with better resistance to wear and tear.
3. Hygiene: Its non-porous surface is easy to clean, making it suitable for food processing, medical, and pharmaceutical applications.
4. Aesthetics: Offers a sleek, modern appearance, often preferred for architectural and design purposes.
Considerations:
1. Cost: Generally more expensive than galvanized steel due to its composition and properties.
2. Weight: Stainless steel can be heavier, potentially increasing transportation and handling costs.
3. Welding: Requires specialized welding techniques and equipment.
Galvanized Steel
Advantages:
1. Cost-Effective: Typically cheaper than stainless steel, making it a good option for budget-conscious projects.
2. Corrosion Resistance: The zinc coating provides a sacrificial layer that protects the underlying steel from rust.
3. Availability: Widely available and used in a variety of applications from construction to automotive parts.
Considerations:
1. Durability: Less durable than stainless steel, with the zinc coating prone to chipping, which can lead to rust if not properly maintained.
2. Aesthetics: The coating can dull over time and may not offer the same visual appeal as stainless steel.
3. Longevity: The protective coating wears off over time, particularly in harsh environments, reducing the lifespan of the material.
Procurement Tips
1. Evaluate Environment: Choose based on exposure to corrosive elements. Stainless steel is better for harsh conditions.
2. Budget Analysis: Consider total cost of ownership, including initial costs, maintenance, and lifespan.
3. Application Needs: Match material properties to application requirements, considering strength, hygiene, and aesthetics.
4. Supplier Reliability: Ensure suppliers have a good track record and can provide consistent quality and timely delivery.
By weighing these factors, you can make an informed decision tailored to your specific procurement needs.
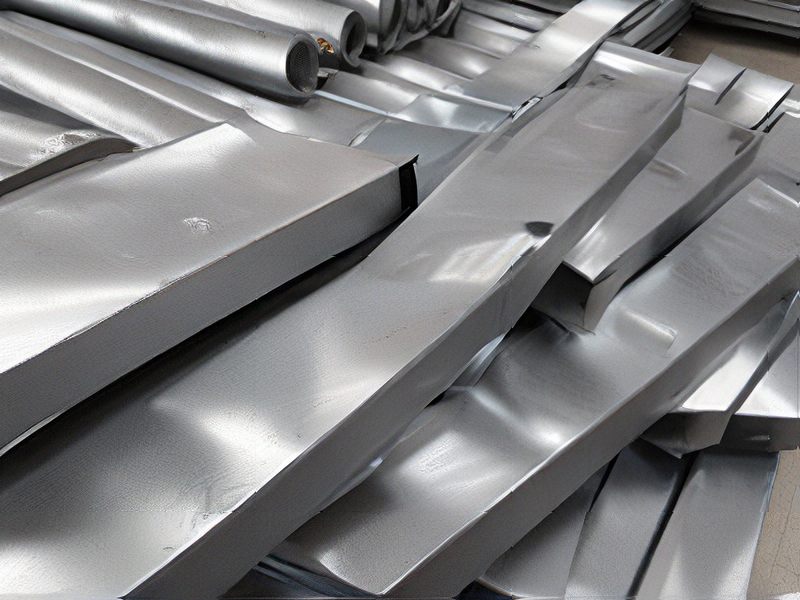
FAQs on Sourcing and Manufacturing from stainless steel vs galvanized in China
When sourcing stainless steel versus galvanized products from China, several FAQs commonly arise:
1. Cost and Durability: Stainless steel is generally more expensive due to its higher corrosion resistance and durability compared to galvanized steel, which is coated with zinc. Stainless steel is ideal for applications requiring long-term durability, especially in corrosive environments, while galvanized steel offers good corrosion resistance at a lower cost.
2. Manufacturing Processes: Stainless steel fabrication involves welding, machining, and sometimes heat treatment to achieve desired properties. Galvanized steel involves a coating process where the steel is immersed in molten zinc, offering protection against rust and corrosion.
3. Quality Standards: Both materials must meet international standards for quality and performance. Stainless steel grades such as 304 and 316 are widely used for their corrosion resistance and mechanical properties, while galvanized steel’s effectiveness depends on the thickness and quality of the zinc coating.
4. Applications: Stainless steel is preferred in industries like construction, marine, and food processing due to its hygiene, strength, and aesthetic appeal. Galvanized steel is suitable for outdoor structures, fencing, and automotive parts where corrosion resistance is needed but cost is a concern.
5. Supplier Selection: When choosing suppliers in China, verify their experience with your specific material requirements and their adherence to quality standards. Ensure they can provide certifications like ISO 9001 for quality management and product-specific certifications (e.g., ASTM for stainless steel, EN for galvanized steel).
6. Environmental Considerations: Stainless steel is recyclable and has a longer lifespan, making it environmentally friendly. Galvanized steel, while recyclable, may have environmental considerations due to zinc coatings.
Navigating between stainless steel and galvanized steel involves balancing cost, durability, and application-specific requirements while ensuring compliance with international standards and environmental considerations.
