Technology and Applications of custom drive shaft
Technology and Applications of Custom Drive Shafts
Custom drive shafts are critical components in automotive, industrial, and aerospace sectors, transmitting torque and rotation to drive various machinery and vehicles. These shafts are tailored to specific requirements, ensuring optimal performance, durability, and reliability.
Technology:
1. Materials: Custom drive shafts can be made from a variety of materials, including steel, aluminum, carbon fiber, and composite materials. Carbon fiber and composites offer high strength-to-weight ratios, reducing vehicle weight and improving fuel efficiency.
2. Manufacturing Techniques: Advanced manufacturing techniques such as CNC machining, 3D printing, and precision welding are employed to create drive shafts with precise dimensions and tolerances. Balancing is crucial to prevent vibrations and ensure smooth operation.
3. Design Software: CAD (Computer-Aided Design) and FEA (Finite Element Analysis) software are used to design and simulate drive shaft performance under various conditions, optimizing the design for strength, durability, and efficiency.
Applications:
1. Automotive: Custom drive shafts are essential in high-performance and racing vehicles, where they must withstand high torque and rotational speeds. They are also used in off-road and custom-built vehicles, ensuring compatibility with unique configurations.
2. Industrial Machinery: In industrial settings, custom drive shafts transmit power in machinery such as conveyors, pumps, and compressors. They are designed to handle specific load requirements and environmental conditions, enhancing machine efficiency and longevity.
3. Aerospace: Aerospace applications demand lightweight and high-strength drive shafts to reduce weight while maintaining performance. Custom drive shafts in aircraft help manage complex power transmission systems, ensuring reliability and safety.
4. Marine: Marine vessels utilize custom drive shafts to connect engines to propellers. These shafts must resist corrosion and withstand the harsh marine environment, ensuring long-term durability and performance.
In summary, custom drive shafts leverage advanced materials, manufacturing techniques, and design tools to meet specific performance needs across diverse applications, from high-speed automotive use to industrial machinery and aerospace systems.

Quality Testing Methods for custom drive shaft and how to control quality
Quality testing methods for custom drive shafts typically involve several key processes to ensure reliability and performance:
1. Dimensional Inspection: Utilizing precise measurements to verify shaft length, diameter, and key dimensions against design specifications. Tools such as calipers, micrometers, and coordinate measuring machines (CMM) are commonly used.
2. Material Analysis: Ensuring the correct material composition (e.g., alloy steel) through spectroscopic analysis to confirm strength and durability properties.
3. Surface Quality Inspection: Checking for surface imperfections like scratches, dents, or cracks using visual inspection and dye penetrant testing.
4. Dynamic Testing: Subjecting the shaft to operational conditions (torque, speed) to simulate real-world usage and assess performance under load. This often involves balancing tests to minimize vibration.
5. Non-Destructive Testing (NDT): Techniques such as ultrasonic testing and magnetic particle inspection to detect internal defects without damaging the shaft.
6. Assembly and Fit Testing: Verifying compatibility and proper fit with associated components like yokes or flanges to ensure seamless integration.
To control quality effectively:
– Establish Clear Specifications: Define precise quality standards and performance criteria for each shaft.
– Supplier Qualification: Partner with reputable suppliers who adhere to industry standards and provide traceable materials.
– In-Process Inspections: Conduct inspections at key stages of manufacturing to catch issues early and prevent defects from progressing.
– Document Control: Maintain thorough documentation of inspection results, production processes, and any corrective actions taken.
– Continuous Improvement: Implement feedback mechanisms and regular reviews to identify opportunities for enhancing processes and product quality.
By integrating these methods and controls, manufacturers can ensure that custom drive shafts meet stringent quality requirements, enhancing reliability and customer satisfaction.
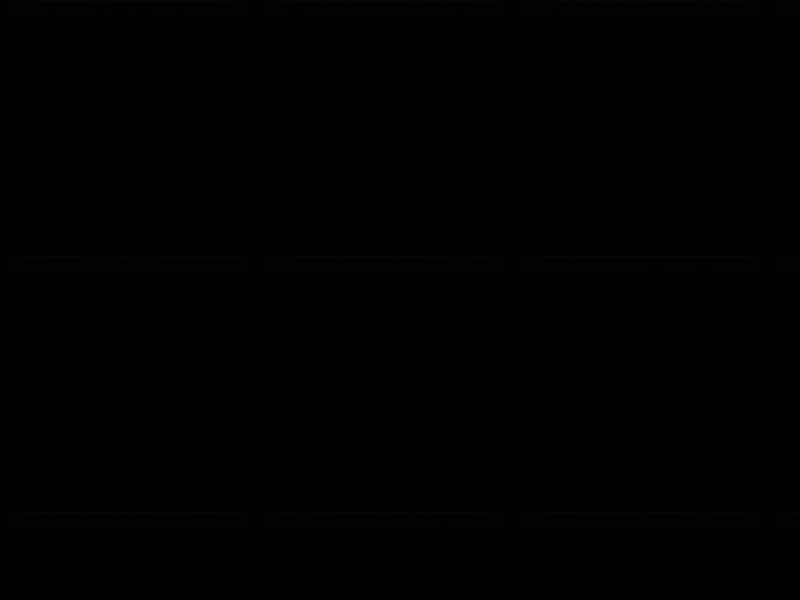
Tips for Procurement and Considerations when Purchasing from custom drive shaft
Tips for Procurement
1. Needs Assessment: Clearly define the specific requirements for the drive shaft, including dimensions, material specifications, and performance criteria. Understand the application’s demands, such as torque, speed, and load.
2. Supplier Evaluation: Research potential suppliers thoroughly. Look for companies with a proven track record, industry certifications, and positive customer feedback. Ensure they have experience in manufacturing custom drive shafts.
3. Quality Assurance: Verify the supplier’s quality control processes. Request details on their testing procedures and certifications (e.g., ISO 9001). High-quality materials and precise manufacturing processes are crucial.
4. Technical Expertise: Engage with suppliers who have strong technical support teams. They should be able to offer design recommendations and assist in troubleshooting.
5. Lead Time and Flexibility: Assess the supplier’s lead time and their ability to accommodate changes in design or order quantity. Flexibility can be crucial if project timelines or requirements shift.
Considerations when Purchasing
1. Design Specifications: Ensure that all design specifications are clearly communicated and agreed upon with the supplier. Any changes in design should be documented and approved.
2. Material Selection: Choose the right materials for your application. Different materials offer varying degrees of strength, durability, and resistance to environmental factors.
3. Cost vs. Quality: Balance cost considerations with quality. Cheaper options might compromise performance and longevity, leading to higher long-term costs.
4. Customization Needs: Determine the extent of customization required. Custom drive shafts can be tailored for specific applications, but this often involves additional costs and lead time.
5. Warranty and Support: Review the supplier’s warranty terms and post-purchase support policies. A robust warranty and accessible support can mitigate risks and ensure ongoing performance.
6. Compliance and Standards: Ensure the drive shafts comply with relevant industry standards and regulations. This is essential for safety and performance assurance.
By following these tips and considerations, you can effectively manage the procurement process and ensure you receive high-quality, custom drive shafts that meet your specific needs.

FAQs on Sourcing and Manufacturing from custom drive shaft in China
Certainly! When sourcing and manufacturing custom drive shafts in China, here are some frequently asked questions:
1. What are the advantages of manufacturing in China?
China offers cost advantages due to lower labor and production costs, access to a wide range of materials and manufacturing capabilities, and established supply chain networks.
2. How can I ensure product quality?
It’s crucial to conduct thorough due diligence on potential suppliers, including factory audits, quality certifications (e.g., ISO 9001), and requesting samples for testing before full production.
3. What is the typical production lead time?
Lead times can vary based on complexity and volume but generally range from a few weeks to a couple of months. Clear communication and agreements on timelines are essential.
4. How do I manage intellectual property (IP) concerns?
Ensure that contracts with suppliers include robust IP protection clauses. Additionally, consider registering patents or trademarks in China and internationally if necessary.
5. What are common challenges when manufacturing in China?
Challenges may include language barriers, cultural differences, logistics complexities, and occasionally, issues with product quality or intellectual property infringement.
6. What are the logistics and shipping options?
Suppliers typically offer shipping options including air freight, sea freight, or a combination (multi-modal transport). Choose based on cost, urgency, and volume considerations.
7. What are the payment terms?
Payment terms are negotiable but often involve initial deposits (e.g., 30%) with the balance paid upon completion or shipment. Use secure payment methods and consider using a letter of credit for larger orders.
Navigating these aspects requires thorough planning, clear communication, and leveraging local expertise or support if needed.
