Technology and Applications of what is the strongest.metal
The strongest metal in terms of tensile strength is tungsten. It has the highest tensile strength of any naturally occurring metal, making it exceptionally resistant to breaking under tension. Tungsten’s strength allows it to withstand extremely high temperatures, up to 3,422 degrees Celsius (6,192 degrees Fahrenheit), without melting. These properties make tungsten crucial in various industrial and technological applications.
Applications of Tungsten:
1. Industrial Tools: Tungsten is widely used in manufacturing tools and equipment that require durability and heat resistance, such as cutting tools, drill bits, and armor-piercing ammunition.
2. Electronics: Due to its high melting point and electrical conductivity, tungsten is used in electrical contacts and heating elements. It’s also used in the production of semiconductors and integrated circuits.
3. Aerospace and Defense: Tungsten alloys are employed in aerospace applications, including rocket engine nozzles and aircraft components, due to their strength and ability to withstand high temperatures.
4. Medical Devices: Tungsten is used in medical imaging equipment, such as X-ray tubes and CT scanners, due to its ability to produce high-energy radiation efficiently.
5. Sporting Goods: Tungsten alloys are used in darts, golf clubs, and fishing weights due to their high density, allowing for smaller and more precise designs.
6. Jewelry: Tungsten’s hardness and scratch resistance make it popular in jewelry, especially for men’s wedding bands.
Overall, tungsten’s strength and resilience make it indispensable across a wide range of industries, from manufacturing and aerospace to electronics and medicine. Its unique properties contribute significantly to advancements in technology and everyday applications.
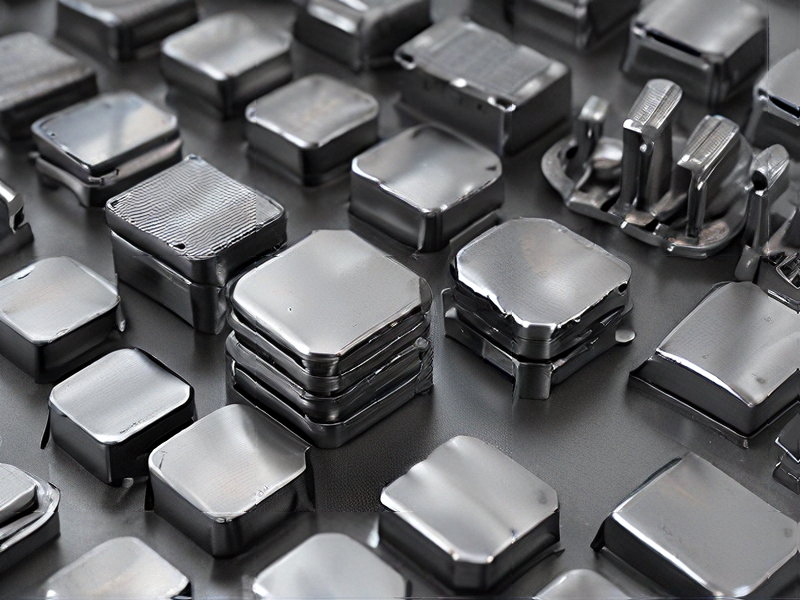
Quality Testing Methods for what is the strongest.metal and how to control quality
Determining the strongest metal involves various testing methods like tensile strength tests, hardness tests (e.g., Rockwell hardness), and impact tests to assess toughness. For quality control, key approaches include:
1. Material Testing: Conducting tensile tests to measure maximum stress a material can withstand.
2. Hardness Testing: Employing methods like Brinell or Vickers tests to assess resistance to deformation.
3. Impact Testing: Evaluating toughness through Charpy or Izod tests, measuring energy absorbed during fracture.
To control quality:
– Statistical Process Control (SPC): Monitoring and controlling processes using statistical methods to ensure consistency.
– Quality Assurance Systems: Implementing ISO standards (e.g., ISO 9001) for systematic quality management.
– Non-Destructive Testing (NDT): Utilizing methods like ultrasound or X-ray to detect defects without damaging the material.
– Supplier Quality Management: Assessing suppliers through audits and quality agreements.
These methods ensure robust quality management from raw material assessment through to final product testing, ensuring adherence to stringent quality standards.
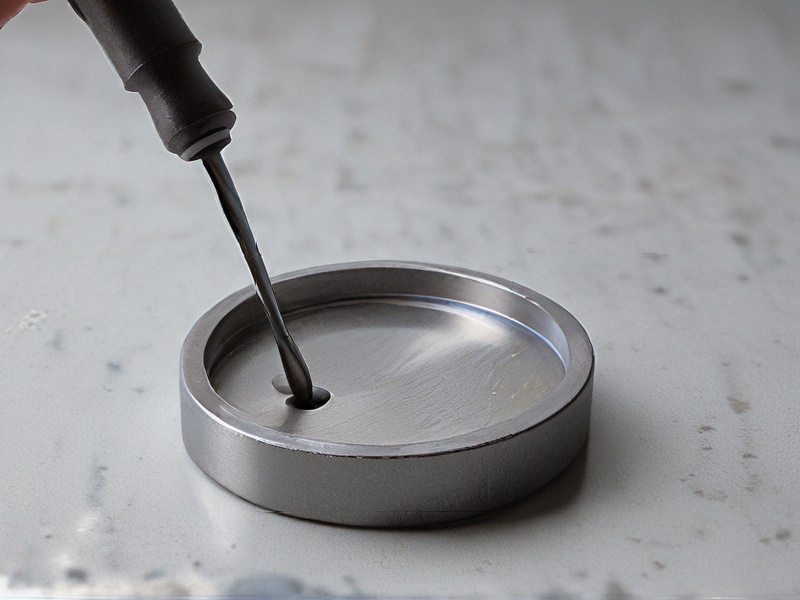
Tips for Procurement and Considerations when Purchasing from what is the strongest.metal
When procuring metals, especially for applications requiring strength, several considerations are crucial:
1. Strength Requirements: Define the specific strength characteristics needed for your application (e.g., tensile strength, yield strength, hardness). This will guide your choice among different metals.
2. Material Selection: For maximum strength, consider metals known for their high tensile strength and toughness. Titanium and its alloys (e.g., Ti-6Al-4V) are renowned for their high strength-to-weight ratio. Stainless steels like 17-4 PH offer excellent strength and corrosion resistance.
3. Cost Considerations: Evaluate the cost of the material and its processing against your budget. High-strength metals can be expensive, so balance performance requirements with financial constraints.
4. Environmental Factors: Consider the operating environment (temperature, humidity, exposure to corrosive elements). Some metals may require additional treatments or coatings to withstand harsh conditions.
5. Manufacturability: Assess how easily the metal can be formed, machined, welded, and assembled into the final product. Some high-strength metals may pose challenges in processing.
6. Certifications and Standards: Ensure the metal meets required industry standards and certifications for your application (e.g., ASTM, ISO standards).
7. Supplier Reliability: Choose reputable suppliers known for quality materials and reliable delivery times. Supplier relationships are crucial for ongoing procurement needs.
8. Testing and Quality Assurance: Implement testing procedures to verify material properties and ensure consistency in strength and performance.
By focusing on these considerations, you can make informed decisions when procuring metals for applications that demand high strength, ensuring optimal performance and durability of your products.

FAQs on Sourcing and Manufacturing from what is the strongest.metal in China
When sourcing and manufacturing metals in China, understanding the strongest metal for your needs and navigating the process effectively is crucial. Here are some FAQs to guide you:
1. What is the strongest metal for manufacturing?
Titanium alloys, particularly Ti-6Al-4V, are renowned for their strength-to-weight ratio and corrosion resistance, making them ideal for aerospace and medical industries.
2. How do I find a reliable supplier in China?
Utilize online directories like Alibaba or Global Sources to find suppliers, ensuring they have a proven track record, certifications (like ISO 9001), and positive client feedback.
3. What are the key considerations when choosing a manufacturer?
Look for manufacturers with expertise in your specific metal requirements, sufficient production capacity, quality control measures, and a willingness to accommodate customization.
4. What are common challenges when sourcing from China?
Quality control issues, language barriers, intellectual property protection, and logistical complexities are common challenges. Conduct due diligence and consider visiting potential suppliers.
5. How can I ensure product quality?
Implement thorough supplier audits, specify quality standards in your contract, conduct inspections during production, and consider hiring a third-party inspection service.
6. What are the lead times and logistics involved?
Understand production lead times, shipping options (sea freight, air freight), customs procedures, and import/export regulations to plan effectively and mitigate delays.
7. What are the payment terms typically used?
Negotiate payment terms that balance risk between parties, such as initial deposit, progress payments, and final payment upon inspection and approval.
Navigating sourcing and manufacturing in China requires careful planning, clear communication, and proactive management of risks and logistics.
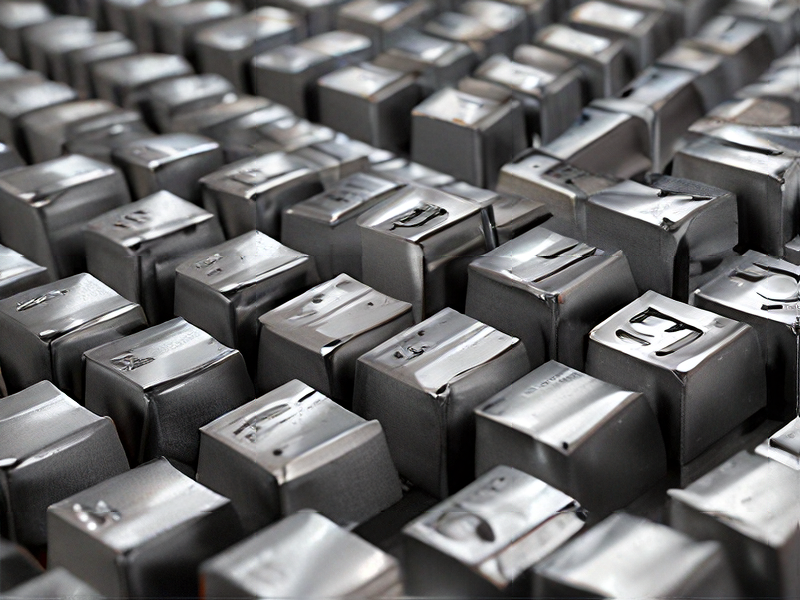