Technology and Applications of engraving machine metal
Engraving machines for metal offer precise control and versatility in creating detailed designs on various metal surfaces. Utilizing CNC (Computer Numerical Control) technology, these machines translate digital designs into physical engravings with high accuracy. Key applications include:
1. Industrial Marking: Engraving machines are crucial for marking serial numbers, logos, and specifications on metal components used in manufacturing and assembly processes. This ensures traceability and quality control.
2. Personalization: They enable customization of metal items such as jewelry, trophies, and gifts with names, dates, or unique patterns. This adds value and personal significance to the items.
3. Prototyping and Toolmaking: Engraving machines aid in prototyping parts and toolmaking by engraving identifiers, part numbers, and functional details directly onto metal tools and prototypes.
4. Artistic and Decorative Applications: Artists and craftsmen use engraving machines to create intricate designs on metal art pieces, sculptures, and architectural elements, showcasing creativity and craftsmanship.
5. Security and Identification: Engraved markings on metal plates or tags serve security purposes in asset tracking, labeling machinery parts, and ensuring proper identification in industrial settings.
Technological advancements have enhanced engraving machines with faster engraving speeds, finer detailing capabilities, and compatibility with a wide range of metals including steel, aluminum, brass, and titanium. These machines typically use diamond or carbide-tipped tools to achieve precise depth and clarity in engraving, catering to diverse industrial, commercial, and artistic needs.
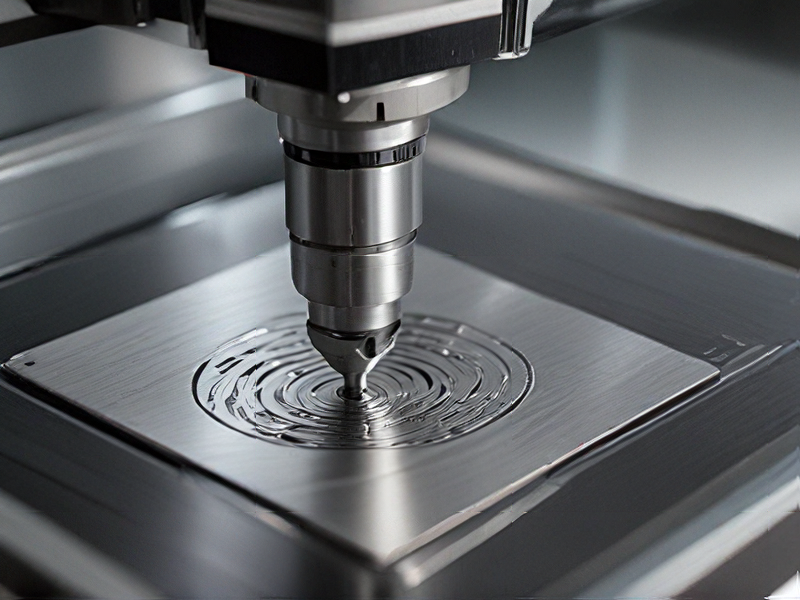
Quality Testing Methods for engraving machine metal and how to control quality
Quality testing methods for engraving machine metal typically involve a combination of visual inspection and precision measurement techniques. Visual inspection checks for surface defects such as scratches, uneven engraving depth, or incomplete patterns. This can be done using magnification tools like microscopes or magnifying lenses.
Precision measurement is crucial for ensuring accuracy in engraving depth and dimensions. Techniques such as coordinate measuring machines (CMMs) or digital height gauges are used to verify engraving depth, width of lines, and overall dimensional accuracy against design specifications.
To control quality effectively, regular calibration of the engraving machine and measuring instruments is essential. Calibration ensures that the machine engraves to the correct depth and accuracy consistently. Implementing standard operating procedures (SOPs) for machine setup, maintenance, and operation helps maintain consistency in quality.
Additionally, using quality control charts to monitor key parameters over time can highlight trends or deviations from desired standards, enabling proactive adjustments or maintenance. Training operators in proper machine operation and quality inspection techniques also plays a vital role in ensuring consistent quality output.
By integrating these methods and controls into the production process, manufacturers can uphold high standards of quality in metal engraving while minimizing defects and ensuring customer satisfaction.
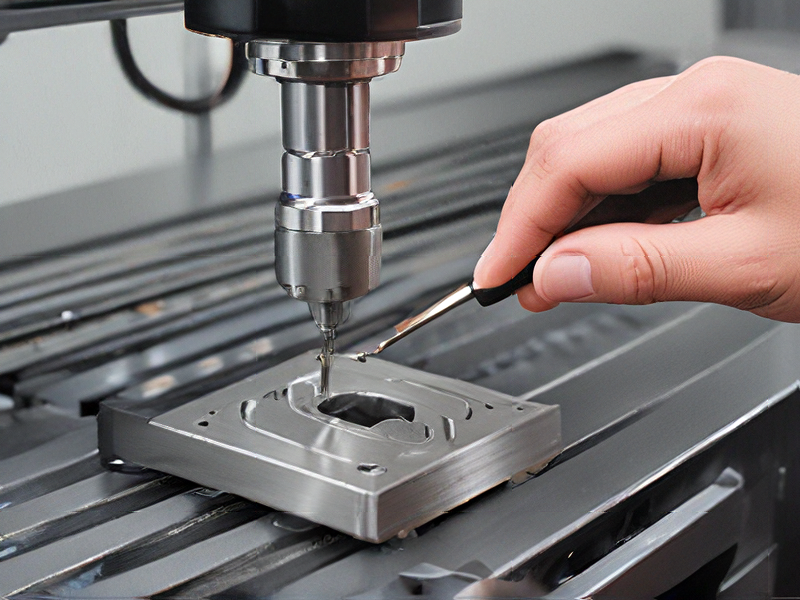
Tips for Procurement and Considerations when Purchasing from engraving machine metal
When purchasing an engraving machine for metal, consider the following tips and factors:
1. Machine Capability: Ensure the engraving machine is capable of handling metal. Look for features like high-powered spindles, rigid frames, and compatibility with metal engraving bits.
2. Material Compatibility: Verify that the machine supports the types of metal you intend to engrave (e.g., aluminum, stainless steel). Some machines may require specific settings or tools for different metals.
3. Engraving Depth and Precision: Metal engraving often requires precise depth control and fine detail. Choose a machine with adjustable settings for depth and high-resolution engraving capabilities.
4. Ease of Use: Consider user-friendly features such as intuitive software interfaces, automated tool changers (if applicable), and compatibility with CAD/CAM software for designing and generating engraving paths.
5. Durability and Maintenance: Opt for machines constructed from robust materials like cast iron or steel for durability. Check ease of maintenance and availability of spare parts.
6. Size and Workspace: Evaluate the machine’s footprint to ensure it fits your workspace. Consider the size of metal sheets or items you plan to engrave.
7. Speed and Efficiency: Assess engraving speed and overall production efficiency. Machines with faster spindle speeds and efficient cooling systems can enhance productivity.
8. Budget and ROI: Determine your budget and compare it with the machine’s features and capabilities. Consider long-term ROI based on production needs and potential growth.
9. Reviews and Support: Research user reviews and customer support options from the manufacturer or supplier. Good support ensures timely assistance for troubleshooting and maintenance.
10. Safety Features: Ensure the machine complies with safety standards and includes features like emergency stop buttons and protective enclosures for safe operation.
By considering these factors, you can select an engraving machine that meets your needs for engraving on metal efficiently and effectively.
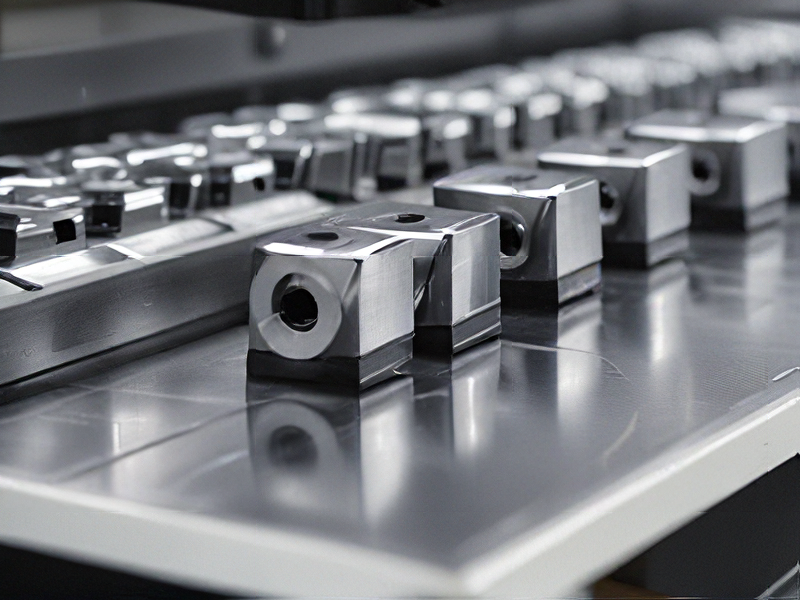
FAQs on Sourcing and Manufacturing from engraving machine metal in China
Certainly! Here are some FAQs regarding sourcing and manufacturing engraving machines from metal in China:
1. What are the advantages of sourcing engraving machines from China?
Sourcing from China often offers cost advantages due to lower manufacturing costs and a wide range of suppliers. China also has advanced capabilities in precision manufacturing.
2. How do I find a reliable manufacturer in China?
Research is crucial. Use platforms like Alibaba, attend trade shows, and seek recommendations. Verify certifications and visit factories if possible. Communication and a clear contract are key.
3. What are the common challenges in manufacturing in China?
Quality control can be an issue. Language barriers may affect communication. Intellectual property protection is another concern, requiring robust agreements and vigilance.
4. Can I customize engraving machines from Chinese manufacturers?
Yes, many Chinese manufacturers offer customization options. Ensure detailed specifications and prototypes are provided to avoid misunderstandings.
5. What should I consider when negotiating with Chinese suppliers?
Besides price, clarify payment terms, production timelines, and quality standards. Build a relationship to foster better cooperation and address potential issues proactively.
6. How can I ensure product quality?
Implement quality control inspections at different production stages. Provide clear guidelines and conduct testing before shipment. Regular audits and feedback loops help maintain standards.
7. What are typical shipping and logistics considerations?
Factor in shipping costs, import duties, and lead times. Choose reliable logistics partners and consider warehousing options to manage inventory effectively.
8. How can I protect my intellectual property when manufacturing in China?
Utilize non-disclosure agreements (NDAs), register patents or trademarks, and control access to sensitive information. Work closely with legal counsel familiar with international IP laws.
By addressing these FAQs, you can navigate sourcing and manufacturing engraving machines from metal in China more effectively, balancing opportunities with challenges to achieve successful outcomes.
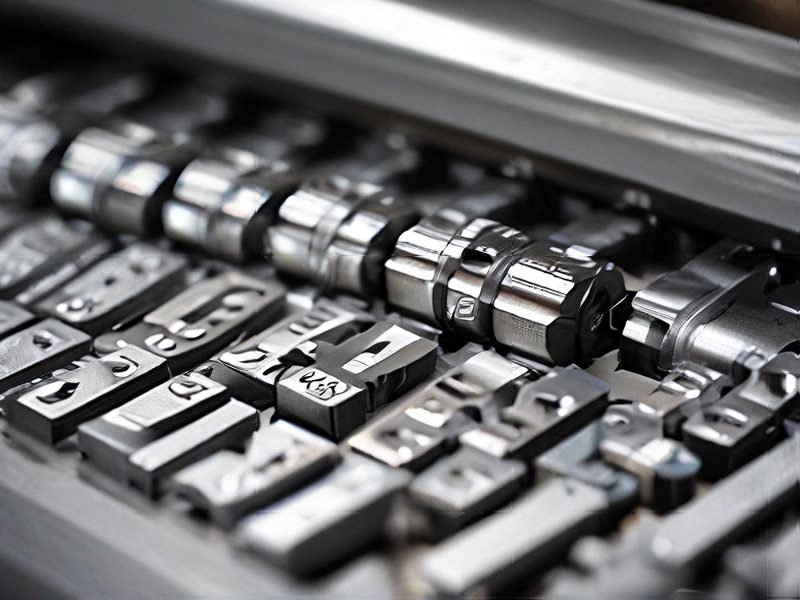