Technology and Applications of machine for engraving on metal
Machine engraving on metal involves the use of advanced technologies such as CNC (Computer Numerical Control) engraving machines. These machines utilize precise computer-controlled movements to etch designs, text, or patterns onto metal surfaces with high accuracy and consistency.
The process typically begins with CAD (Computer-Aided Design) software, where the desired design is created or imported. This design is then converted into machine-readable code that guides the CNC engraving machine’s movements.
Key applications of machine engraving on metal include:
1. Industrial Marking: Engraving serial numbers, part numbers, logos, and other identifying marks on metal components used in manufacturing and assembly processes.
2. Personalization and Customization: Creating bespoke designs on metal items such as jewelry, trophies, gifts, and personalized items.
3. Prototyping: Rapidly prototyping metal components with detailed markings and identifiers for testing and validation.
Technological advancements have led to the integration of laser engraving systems, which offer even finer details and faster processing times compared to traditional mechanical engraving methods. Laser engraving utilizes focused laser beams to vaporize or displace the metal surface, providing versatility in engraving depths and complexity.
Moreover, CNC engraving machines are capable of handling various types of metals including stainless steel, aluminum, brass, and titanium, offering flexibility across different industrial sectors.
In conclusion, machine engraving on metal combines precision, versatility, and efficiency, catering to diverse industrial and personalized applications with advanced technological capabilities like CNC and laser engraving systems.

Quality Testing Methods for machine for engraving on metal and how to control quality
Quality testing methods for machines used for engraving on metal typically involve several key approaches:
1. Dimensional Accuracy Checks: Use precision measuring tools like calipers or coordinate measuring machines (CMM) to verify that engraved dimensions meet specifications.
2. Surface Roughness Measurement: Employ surface roughness testers to ensure the engraved surfaces meet required smoothness standards.
3. Visual Inspection: Conduct visual inspections under adequate lighting to detect any defects such as burrs, uneven engraving depths, or inconsistent lettering.
4. Material Testing: Perform material testing to ensure the metal substrate maintains its structural integrity and meets hardness requirements after engraving.
5. Durability Testing: Subject engraved samples to environmental tests (e.g., corrosion resistance, wear resistance) to verify longevity under real-world conditions.
To control quality effectively:
– Establish Standards: Define clear quality standards and specifications for engraving depth, alignment, and finish.
– Regular Calibration: Regularly calibrate engraving machines and testing equipment to maintain accuracy.
– Training and Certification: Ensure operators are trained in machine operation, quality standards, and inspection techniques.
– Process Monitoring: Implement continuous process monitoring to detect deviations and make adjustments promptly.
– Feedback Loop: Establish a feedback loop where issues found during quality testing are analyzed, and corrective actions are implemented to prevent recurrence.
By integrating these methods and controls into your quality management system, you can ensure consistent, high-quality metal engraving output.

Tips for Procurement and Considerations when Purchasing from machine for engraving on metal
When procuring a machine for engraving on metal, careful consideration and strategic planning are crucial. Here are some key tips:
1. Identify Needs and Specifications
– Material Compatibility: Ensure the machine can handle the types of metal you plan to engrave (e.g., stainless steel, aluminum, brass).
– Engraving Precision: Look for machines with high precision and resolution, especially if fine details are critical.
– Production Volume: Choose a machine that matches your production scale—whether for occasional use or high-volume production.
2. Technology and Features
– Laser vs. Mechanical Engraving: Laser engraving offers high precision and versatility, while mechanical engraving may be more robust for certain tasks.
– Software Compatibility: Ensure the machine’s software is user-friendly and compatible with your design tools.
– Cooling Systems: Laser engravers, in particular, may require efficient cooling systems to prevent overheating.
3. Quality and Reliability
– Brand Reputation: Opt for reputable brands known for quality and durability.
– Customer Reviews and Testimonials: Research user experiences to gauge reliability and performance.
– Warranty and Support: Check for comprehensive warranties and accessible customer support.
4. Budget and Costs
– Initial Cost vs. Long-Term Value: Balance the upfront investment with long-term operational costs, including maintenance and consumables.
– Hidden Costs: Be aware of additional costs such as replacement parts, software licenses, and training.
5. Vendor Selection
– Credibility and Trustworthiness: Select vendors with a proven track record and good customer service.
– After-Sales Support: Ensure the vendor offers robust after-sales support, including training, troubleshooting, and maintenance services.
– Delivery and Installation: Confirm the logistics for delivery and installation, including any associated costs.
6. Compliance and Safety
– Regulatory Compliance: Ensure the machine complies with local safety and environmental regulations.
– Operator Safety: Consider machines with safety features to protect operators, such as enclosed laser systems and emergency stop buttons.
Conclusion
Investing in a metal engraving machine requires careful evaluation of your specific needs, machine features, and vendor reliability. By considering these factors, you can make a well-informed decision that enhances your production capabilities and ensures a return on investment.

FAQs on Sourcing and Manufacturing from machine for engraving on metal in China
Certainly! Here are some FAQs regarding sourcing and manufacturing from a machine for engraving on metal in China:
1. What types of metal engraving machines are available in China?
China offers a variety of metal engraving machines, including laser engravers, CNC routers, and handheld engraving tools. These machines cater to different scales and types of metal engraving needs.
2. How do I find a reliable manufacturer in China for metal engraving machines?
It’s crucial to conduct thorough research, read reviews, and possibly visit trade shows like Canton Fair. Verifying certifications (ISO, CE) and requesting samples can also ensure quality.
3. What are the typical costs involved in importing a metal engraving machine from China?
Costs can vary based on the type and specifications of the machine, shipping methods, import duties, and taxes. It’s advisable to get detailed quotes and factor in all expenses.
4. What are common challenges when sourcing metal engraving machines from China?
Challenges may include language barriers, quality control during manufacturing, intellectual property protection, and navigating import regulations.
5. How can I ensure quality control when manufacturing in China?
Establishing clear specifications, conducting factory audits, and implementing a comprehensive quality control plan are essential. Regular inspections during production and before shipment are recommended.
6. Are there any environmental or ethical considerations I should be aware of?
Ensuring manufacturers comply with environmental regulations and ethical standards (such as fair labor practices) is crucial. Requesting environmental certifications and conducting supplier audits can help mitigate risks.
Navigating these aspects carefully can help you successfully source and manufacture metal engraving machines from China while ensuring quality and compliance with regulations.
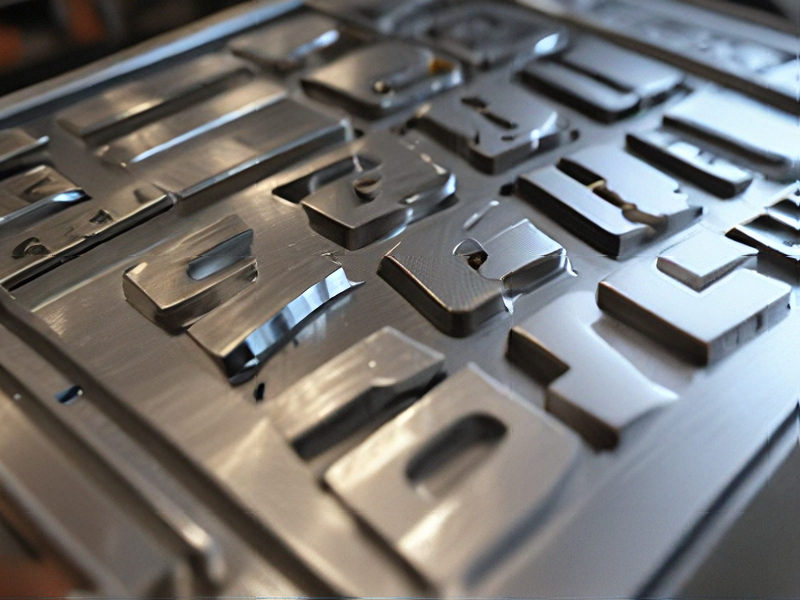