Technology and Applications of engraving metal machine
Engraving metal machines utilize various technologies to achieve precise and intricate designs on metal surfaces. The primary methods include mechanical, laser, and chemical engraving.
1. Mechanical Engraving: This traditional method involves a rotating cutter or graver that physically cuts into the metal surface. It’s highly precise and can create deep, detailed engravings suitable for industrial and artistic applications. Computer Numerical Control (CNC) systems have enhanced this process, allowing for automated and complex designs.
2. Laser Engraving: Utilizing high-powered lasers, this method vaporizes the metal surface to create marks. It offers speed, precision, and versatility, making it ideal for both small-scale and industrial applications. Laser engraving is popular in personalized items, signage, and industrial part marking due to its ability to produce fine details and intricate patterns.
3. Chemical Etching: This process involves using chemicals to selectively etch designs into the metal surface. It’s advantageous for producing high volumes of identical parts with consistent quality. Chemical etching is often used in manufacturing electronic components, nameplates, and fine art prints.
Applications of engraving machines span various industries:
– Jewelry: Engraving machines add personalized messages or intricate patterns to rings, bracelets, and pendants.
– Industrial: Parts and tools are marked for identification, traceability, and branding purposes using engraving techniques.
– Automotive: Engraving machines are used to create serial numbers, logos, and decorative elements on vehicle parts.
– Medical: Surgical instruments and implants are often marked with laser engraving for traceability and identification purposes.
In conclusion, engraving metal machines employ mechanical, laser, and chemical technologies to cater to diverse applications ranging from industrial marking to artistic engraving. Each method offers unique advantages in terms of precision, speed, and versatility, making them indispensable tools in modern manufacturing and customization processes.
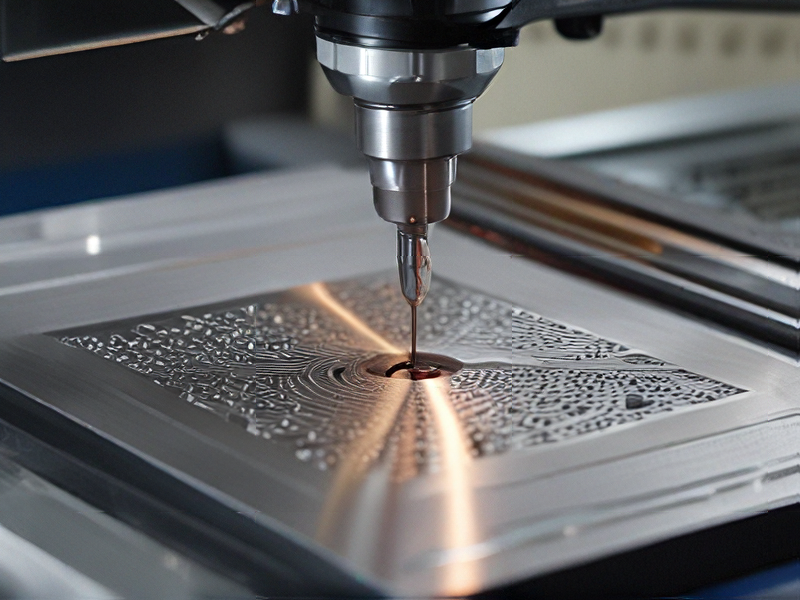
Quality Testing Methods for engraving metal machine and how to control quality
Quality testing methods for engraving metal machines typically involve several key approaches to ensure precision and consistency:
1. Visual Inspection: Technicians visually inspect engraved samples under controlled lighting to detect any irregularities, such as uneven depth or improper alignment.
2. Dimensional Measurement: Using precise measurement tools like calipers or coordinate measuring machines (CMMs), operators verify critical dimensions such as engraving depth and spacing between characters.
3. Surface Profiling: Laser profilometers or surface roughness testers analyze the surface finish of engraved areas to ensure it meets specified requirements for smoothness and texture.
4. Durability Testing: Samples undergo stress tests to evaluate the durability of the engraving against factors like abrasion, corrosion, and exposure to harsh environments.
5. Optical Character Recognition (OCR): Software-based OCR systems verify the accuracy of engraved characters by comparing them against a digital standard, ensuring legibility and correctness.
To control quality effectively:
– Establish Clear Standards: Define precise engraving specifications for depth, character spacing, and alignment.
– Regular Calibration: Calibrate machines and measurement tools regularly to maintain accuracy and consistency.
– Training and Skill Development: Train operators to recognize quality issues and perform testing methods effectively.
– Documentation and Reporting: Maintain detailed records of testing results and inspections to track trends and identify areas for improvement.
By implementing these methods and controls, manufacturers can ensure that their metal engraving processes consistently produce high-quality results that meet customer expectations and industry standards.
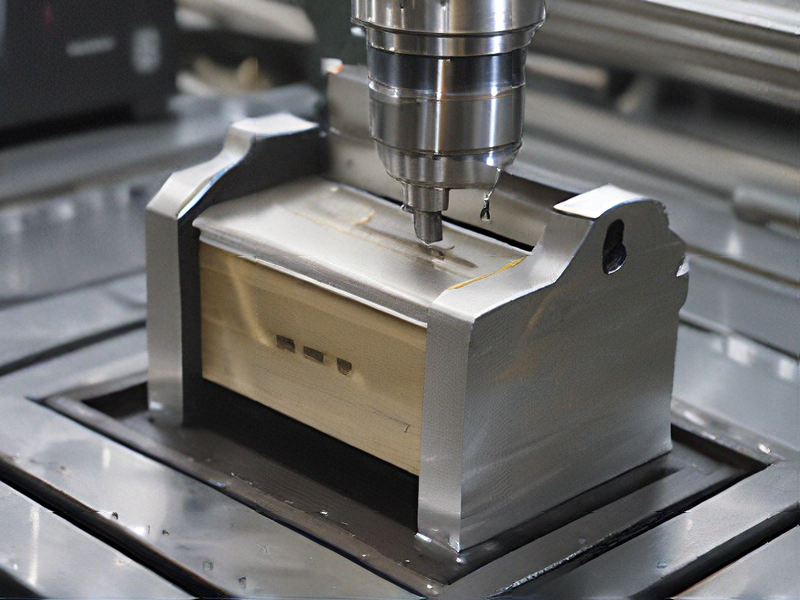
Tips for Procurement and Considerations when Purchasing from engraving metal machine
When purchasing an engraving machine for metal, several key considerations can ensure you make an informed procurement decision:
1. Machine Capability: Assess the machine’s engraving capabilities such as depth, speed, and precision. Consider whether it meets your specific requirements for the types of metals and designs you plan to work with.
2. Ease of Use: Look for user-friendly features such as intuitive software, touchscreen interfaces, and ease of setup. Training requirements for operators should also be considered.
3. Durability and Maintenance: Metal engraving can be demanding, so ensure the machine is robust and durable. Check maintenance requirements and availability of spare parts.
4. Engraving Quality: Evaluate sample outputs to gauge the quality of engraving the machine produces. Pay attention to factors like clarity, detail, and consistency.
5. Compatibility and Integration: Verify compatibility with your existing software systems and design files. Consider integration capabilities if you plan to automate workflows.
6. Support and Training: Assess the supplier’s reputation for customer support, including availability of technical assistance and training programs.
7. Cost and Return on Investment (ROI): Compare upfront costs, ongoing operational expenses (like maintenance and consumables), and expected ROI based on your production needs.
8. Safety Features: Ensure the machine complies with safety regulations and incorporates features like emergency stop buttons and protective enclosures.
9. Reviews and References: Seek reviews from other users and ask for references from the supplier to validate performance claims and customer satisfaction.
10. Future Scalability: Consider future business growth and whether the machine can scale with increased production demands or technological advancements.
By carefully evaluating these factors, you can select an engraving machine that aligns with your operational requirements, budget constraints, and long-term business goals.
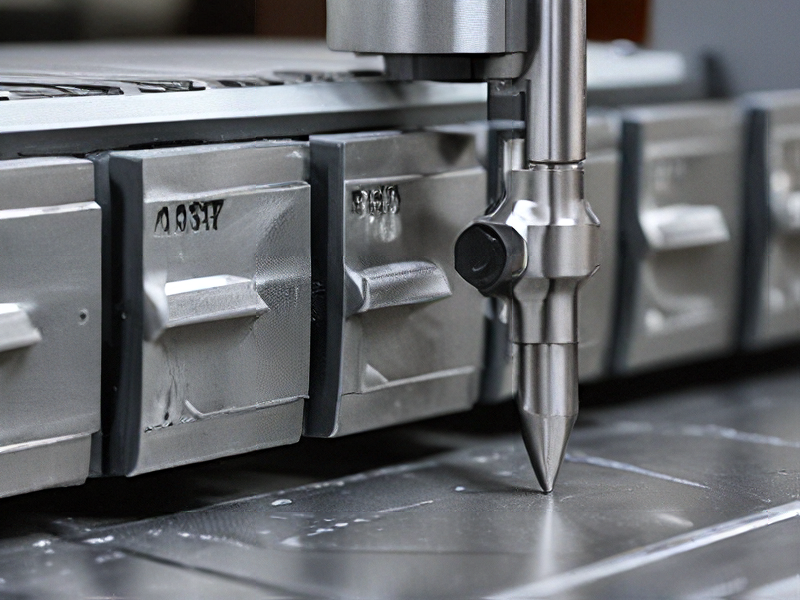
FAQs on Sourcing and Manufacturing from engraving metal machine in China
Certainly! Here are some FAQs regarding sourcing and manufacturing from an engraving metal machine in China:
1. What types of engraving metal machines are available in China?
– China offers a wide range of engraving machines, including laser, CNC, and manual options tailored for various metal types and sizes.
2. How do I find a reliable manufacturer in China?
– Research extensively online, read reviews, seek referrals, and consider visiting trade shows or using sourcing platforms to connect directly with manufacturers.
3. What should I consider when choosing a supplier?
– Evaluate their experience, production capabilities, quality control measures, certifications, and past client feedback to ensure they meet your standards.
4. Can I customize an engraving machine to my specifications?
– Yes, many Chinese manufacturers offer customization options. Specify your requirements for size, engraving depth, material compatibility, and software integration.
5. What are the typical lead times and shipping options?
– Lead times vary but average around 4-8 weeks depending on customization and order volume. Shipping options include sea freight for large orders and air freight for smaller, urgent shipments.
6. How do I ensure product quality and compliance with regulations?
– Conduct factory audits, request samples, and verify certifications like CE or ISO. Communicate clearly regarding quality standards and ensure compliance with import regulations in your country.
7. What support can I expect post-purchase?
– Many manufacturers offer technical support, training, and warranty services. Clarify these details before finalizing your purchase to ensure ongoing support.
Navigating sourcing and manufacturing from China requires thorough research, clear communication, and careful consideration of quality and regulatory requirements to ensure a successful partnership and product outcome.
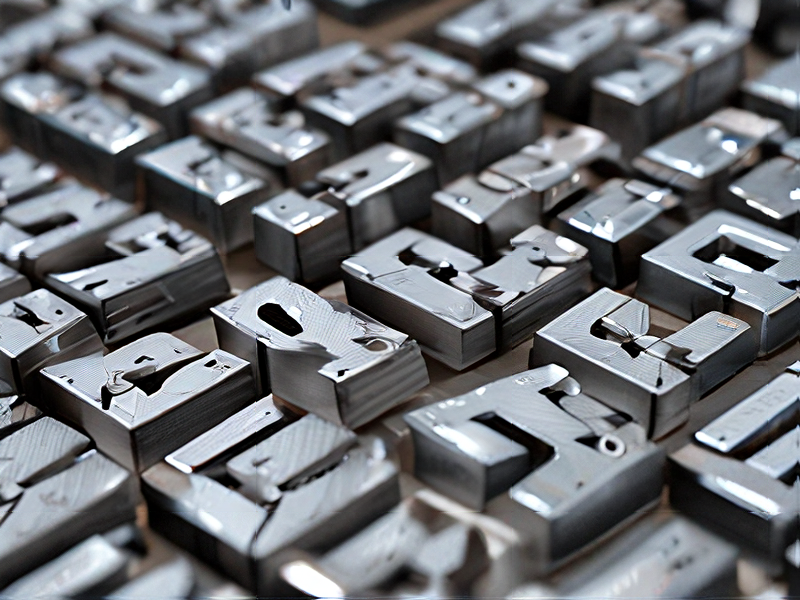