Technology and Applications of grinder for metal
Grinders are versatile power tools widely used in metalworking for shaping, smoothing, and finishing metal surfaces.
These tools operate by utilizing abrasive wheels, discs, or belts to grind away material.
Applications:
* Metal Cutting: Grinders excel at cutting through metal, enabling tasks like removing excess material, shaping contours, and creating slots.
* Sharpening: They effectively sharpen tools like chisels, knives, and drill bits.
* Deburring: Grinders efficiently remove sharp edges and burrs from metal parts after machining or fabrication.
* Surface Finishing: By using finer abrasive materials, grinders can smooth and polish metal surfaces, achieving a desired finish.
Types of Grinders:
* Angle Grinders: Portable and versatile, used for a wide range of cutting, grinding, and polishing applications.
* Bench Grinders: Fixed-position grinders with adjustable speed and wheel diameter, ideal for precise grinding tasks.
* Belt Grinders: Utilize abrasive belts for aggressive material removal and shaping, often used in industrial settings.
Grinders are essential tools in metalworking, offering precision, versatility, and efficiency in various metal processing operations.

Quality Testing Methods for grinder for metal and how to control quality
Quality testing methods for metal grinders focus on ensuring performance, durability, and safety. Here are key methods and quality control practices:
1. Material Inspection:
– Chemical Analysis: Ensure the metal composition meets specifications using spectrometry or chemical tests.
– Hardness Testing: Verify the hardness of the grinder components using Rockwell or Vickers hardness tests to ensure durability.
2. Dimensional Accuracy:
– Gauge Measurement: Use micrometers, calipers, and gauges to check dimensions against design specifications.
– Coordinate Measuring Machine (CMM): Provides precise measurements of complex geometries.
3. Performance Testing:
– Runout Inspection: Measure the wobble or deviation from true rotation to ensure smooth operation.
– Surface Finish: Check the surface roughness of ground parts using profilometers to ensure quality finish.
– Load Testing: Simulate operating conditions to verify the grinder can handle specified loads without failure.
4. Safety and Durability Tests:
– Fatigue Testing: Assess the grinder’s ability to withstand repeated use without cracking or breaking.
– Vibration Analysis: Ensure the grinder operates within acceptable vibration levels to prevent operator fatigue and machine wear.
5. Operational Checks:
– Noise Level Testing: Measure the noise produced during operation to ensure it meets safety standards.
– Thermal Imaging: Detect hotspots and ensure even heat distribution during operation to prevent overheating.
Quality Control Measures:
1. Standard Operating Procedures (SOPs): Implement and adhere to detailed SOPs for manufacturing and testing.
2. Statistical Process Control (SPC): Use control charts to monitor and maintain process quality.
3. Inspection and Testing Plans: Develop comprehensive inspection and testing schedules throughout the production cycle.
4. Corrective Actions: Establish procedures for addressing non-conformities and implementing corrective measures.
5. Documentation and Traceability: Maintain detailed records of materials, processes, and test results for traceability.
By integrating these methods and practices, manufacturers can ensure high-quality metal grinders that meet performance and safety standards.
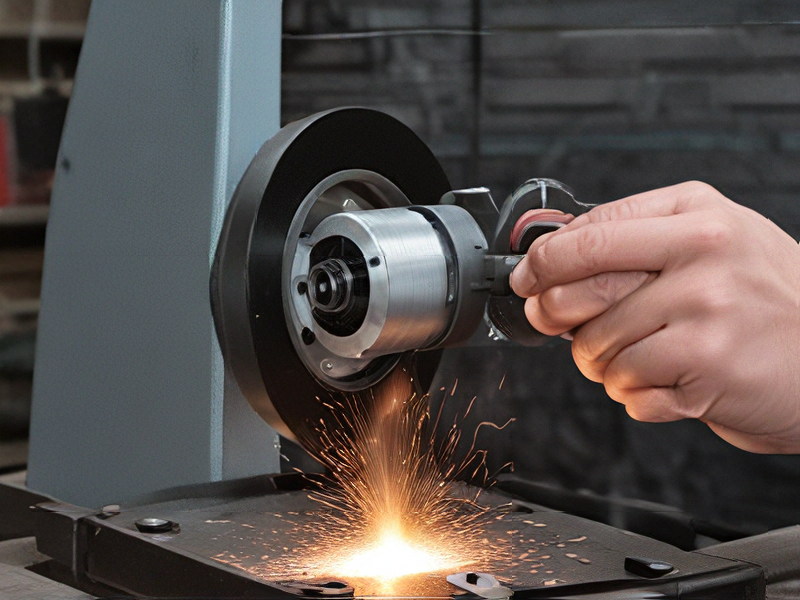
Tips for Procurement and Considerations when Purchasing from grinder for metal
When purchasing a grinder for metal, consider the following tips and considerations:
1. Type of Grinder: Choose between angle grinders, bench grinders, or die grinders based on your specific needs. Angle grinders are versatile for cutting and grinding, bench grinders are ideal for sharpening tools, and die grinders are suited for intricate tasks.
2. Power and Size: Opt for a grinder with sufficient power (measured in watts or horsepower) for your intended tasks. Larger discs typically require more power. Consider the size of the grinder based on portability and workspace constraints.
3. Disc Size and Speed: Select the appropriate disc size (e.g., 4.5 inches, 7 inches) based on the thickness of the metal and the tasks you’ll perform. Ensure the grinder’s speed (measured in revolutions per minute, RPM) matches the disc’s specifications for safe and effective operation.
4. Safety Features: Look for grinders with essential safety features such as adjustable guards, safety locks, and vibration reduction mechanisms. Ensure the grinder has proper ventilation to prevent overheating.
5. Durability and Build Quality: Choose grinders made from durable materials like stainless steel or high-quality plastics. Check reviews or ratings for insights into long-term reliability.
6. Additional Features: Consider features like variable speed settings for versatility, ergonomic designs for comfort during extended use, and compatibility with accessories such as different types of discs and wheels.
7. Brand Reputation and Warranty: Opt for reputable brands known for producing reliable power tools. Check for warranties that cover defects or malfunctions.
8. Cost and Value: Balance your budget with the grinder’s features and durability. Avoid compromising on quality for a lower price, as a durable grinder will provide better long-term value.
By carefully considering these factors, you can select a grinder that meets your metalworking needs effectively and safely.
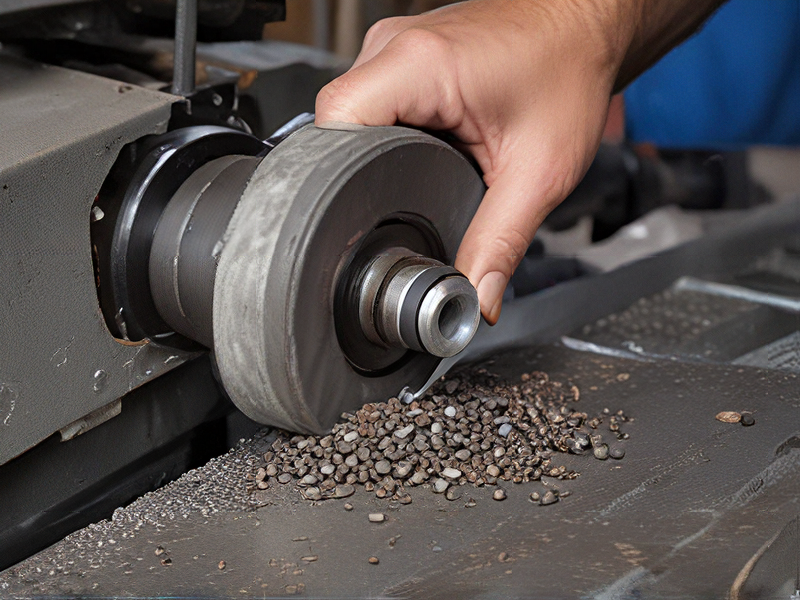
FAQs on Sourcing and Manufacturing from grinder for metal in China
Certainly! When sourcing a metal grinder from China, it’s essential to address several FAQs to ensure a smooth manufacturing process:
1. How do I find reliable manufacturers?
– Utilize platforms like Alibaba or attend trade fairs in China (e.g., Canton Fair) to connect with verified suppliers. Request samples and check certifications to verify reliability.
2. What are the typical manufacturing costs?
– Costs vary based on materials, complexity, and quantities. Obtain detailed quotes, including tooling costs, unit prices, and shipping expenses to estimate total expenditure accurately.
3. How can I ensure product quality?
– Implement a rigorous quality assurance process. Conduct factory audits, define product specifications clearly, and consider hiring a third-party inspection service to monitor production.
4. What are the lead times for manufacturing and shipping?
– Lead times depend on production schedules and shipping methods. Discuss timelines upfront, including production milestones and transit times to anticipate delivery dates.
5. What are the payment terms?
– Negotiate favorable payment terms, such as initial deposits and balance payments upon inspection or delivery. Use secure payment methods to mitigate risks.
6. How can I handle customs and import regulations?
– Work with a freight forwarder experienced in importing from China. Ensure compliance with customs requirements and tariffs to avoid delays or additional costs.
7. What should I do if there are issues with the product?
– Establish clear communication channels with the manufacturer. Have a contingency plan for resolving quality issues, such as returns, replacements, or refunds.
By addressing these FAQs diligently, you can navigate the complexities of sourcing and manufacturing a metal grinder from China effectively.
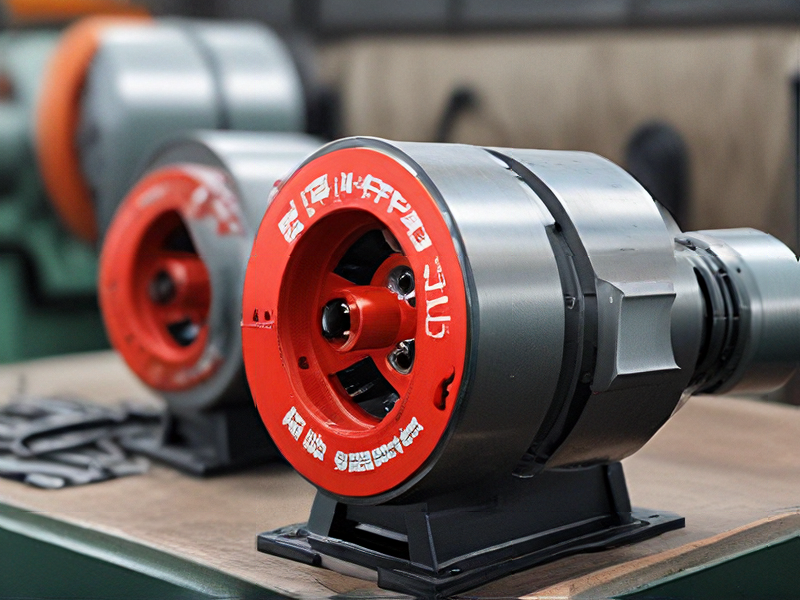