Technology and Applications of wood laser cutter machine
A wood laser cutter machine utilizes laser technology for precise cutting and engraving on various types of wood and wood-based materials. It works by directing a high-powered laser beam onto the surface of the wood, which melts, burns, or vaporizes the material in a controlled manner.
Key Applications:
1. Precision Cutting: Laser cutters excel in creating intricate designs and precise cuts in wood, which are difficult to achieve with traditional tools. This is particularly useful in industries like furniture manufacturing, where intricate patterns and designs are in demand.
2. Engraving and Marking: Laser cutters can engrave detailed designs, logos, or text onto wooden surfaces. This capability finds applications in personalized gifts, signage, and branding on wooden products.
3. Prototyping and Rapid Manufacturing: For designers and engineers, laser cutters facilitate rapid prototyping of wood-based products. This allows for quick iterations and adjustments before moving to full-scale production.
4. Art and Craft: Artists and hobbyists use wood laser cutters for creating detailed artwork, sculptures, and decorations. The precision and versatility of laser cutting expand creative possibilities in woodworking.
5. Architectural Models: Architects and designers use laser cutters to create detailed models of buildings and structures, showcasing intricate details of wood components.
Technology Advancements:
Modern wood laser cutter machines feature:
– High Precision: Capable of cutting materials with micron-level accuracy.
– Versatility: Can handle various types of wood, veneers, plywood, and MDF.
– Automation: Integrated with computer numerical control (CNC) systems for automated operation and batch processing.
– Safety Features: Including fume extraction systems and safety interlocks to ensure safe operation.
Future Directions:
Advancements in laser technology continue to enhance cutting speeds, improve energy efficiency, and broaden the range of materials that can be processed. Integration with artificial intelligence (AI) and machine learning could further automate settings optimization and enhance cutting quality.
In conclusion, wood laser cutter machines represent a pivotal technology in modern woodworking and manufacturing, enabling intricate designs, precise cuts, and efficient production across various industries and applications.
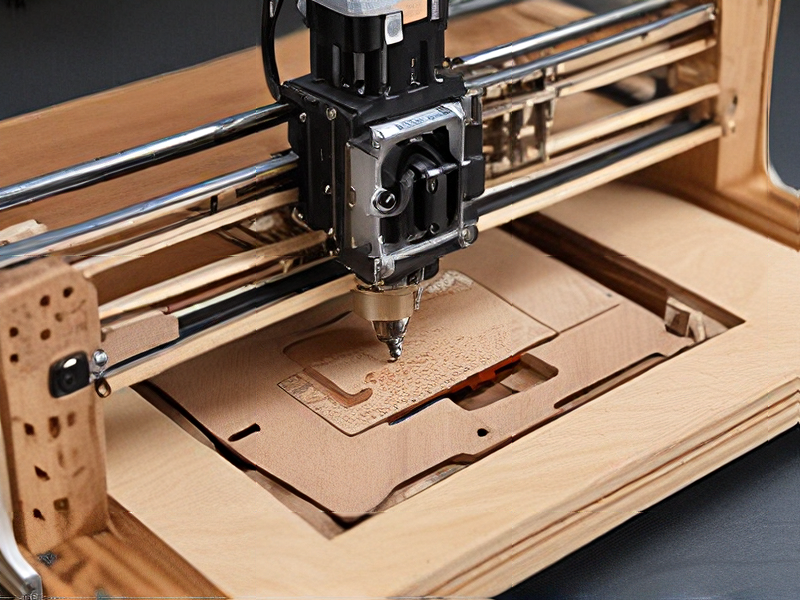
Quality Testing Methods for wood laser cutter machine and how to control quality
Quality testing methods for a wood laser cutter machine typically involve several key approaches to ensure reliable performance and output consistency.
1. Dimensional Accuracy Check: Measure the dimensions of laser-cut wood pieces against design specifications using calipers or measuring tools to ensure they meet tolerances.
2. Edge Quality Inspection: Evaluate the smoothness and consistency of cut edges visually and through touch to ensure they meet the desired finish standards without burning or rough edges.
3. Material Integrity Assessment: Inspect for signs of burning, charring, or discoloration on the wood surface, which can affect the aesthetic and structural integrity of the cut pieces.
4. Precision of Cuts: Test the precision of cuts by comparing actual cuts against digital design files or templates to verify alignment and accuracy.
5. Durability Testing: Conduct tests to assess the durability and strength of laser-cut wood pieces under typical usage conditions to ensure they meet expected performance standards.
To control quality effectively, implement the following strategies:
1. Regular Maintenance: Schedule routine maintenance and calibration of the laser cutter machine to keep it operating within optimal parameters.
2. Operator Training: Train operators thoroughly on machine operation, maintenance procedures, and quality standards to minimize errors and ensure consistent output.
3. Quality Control Checks: Implement checkpoints at different stages of production to detect and rectify any deviations from quality standards promptly.
4. Feedback Loop: Establish a feedback loop where operators report issues or anomalies encountered during production for continuous improvement.
5. Documentation and Record Keeping: Maintain detailed records of quality tests, inspections, and any corrective actions taken to track performance and identify recurring issues.
By integrating these testing methods and quality control measures, manufacturers can maintain high standards of quality in laser-cut wood products, ensuring customer satisfaction and operational efficiency.
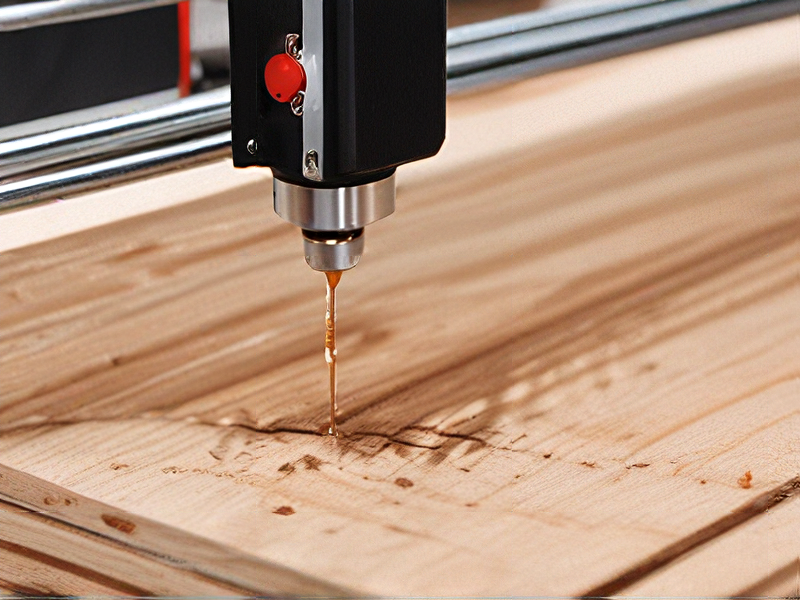
Tips for Procurement and Considerations when Purchasing from wood laser cutter machine
When purchasing a wood laser cutter machine, consider the following key tips and considerations:
1. Machine Specifications: Assess the laser power (measured in watts), bed size, and types of materials it can effectively cut. Ensure it meets your specific woodworking requirements, such as cutting thickness and speed.
2. Quality and Reliability: Research the manufacturer’s reputation for build quality, reliability, and after-sales support. Read reviews from other users to gauge their experiences with the machine.
3. Ease of Use and Software Compatibility: User-friendly interfaces and compatibility with design software (like AutoCAD or Adobe Illustrator) can streamline operations. Ensure the machine’s software meets your design and production needs.
4. Safety Features: Laser cutters pose safety risks. Look for machines with safety features like emergency stop buttons, enclosure interlocks, and fume extraction systems to protect operators and comply with safety standards.
5. Maintenance and Service: Consider maintenance requirements and the availability of technical support or service technicians. Reliable customer support ensures minimal downtime and efficient issue resolution.
6. Cost and Budget: Evaluate the initial cost of the machine, including any additional accessories or software licenses required. Factor in long-term operating costs such as electricity, maintenance, and replacement parts.
7. Training and Support: Ensure the supplier offers training for machine operation and maintenance. Adequate training reduces the learning curve and improves productivity.
8. Future Expansion and Upgrades: Assess whether the machine allows for future upgrades or modifications to accommodate changing business needs or technological advancements.
9. Environmental Impact: Consider the environmental impact of laser cutting, including energy consumption and waste disposal. Choose machines with energy-efficient features and responsible waste management practices.
10. References and Recommendations: Seek recommendations from industry peers or trade associations to gain insights into which brands or models are well-regarded within the woodworking community.
By carefully evaluating these factors, you can select a wood laser cutter machine that aligns with your operational needs, budget constraints, and long-term business goals.
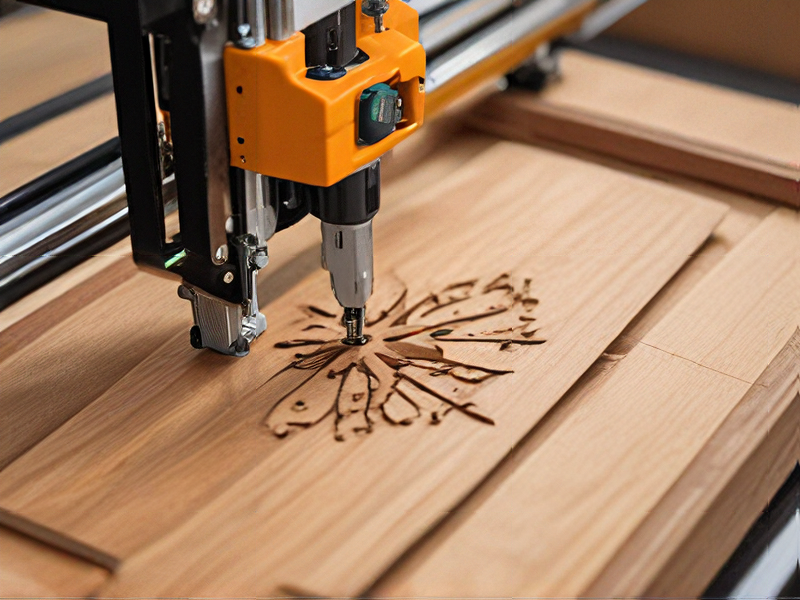
FAQs on Sourcing and Manufacturing from wood laser cutter machine in China
## FAQs on Sourcing and Manufacturing with Wood Laser Cutters in China
1. Where can I find reliable wood laser cutter manufacturers in China?
Online platforms like Alibaba and Global Sources list numerous manufacturers. Attending trade shows like Canton Fair provides face-to-face interaction.
2. What factors should I consider when choosing a manufacturer?
Evaluate their experience, production capacity, quality control processes, certifications (ISO, CE), and customer reviews.
3. What are the typical lead times for wood laser cutter production?
Lead times vary based on order size and complexity. Expect 2-4 weeks for standard models and longer for customized solutions.
4. How can I ensure quality control?
Request samples, conduct on-site inspections, and establish clear quality standards in your contract.
5. What are the shipping costs from China?
Shipping costs depend on the size, weight, and destination. Sea freight is generally more economical for bulk orders, while air freight is faster but pricier.
6. What are the payment options?
Common methods include T/T (bank transfer), L/C (letter of credit), and PayPal.
7. Is it possible to visit the factory before placing an order?
Yes, many manufacturers welcome factory visits to build trust and assess their capabilities.
8. What kind of after-sales support can I expect?
Reputable manufacturers offer technical support, warranties, and spare parts availability.
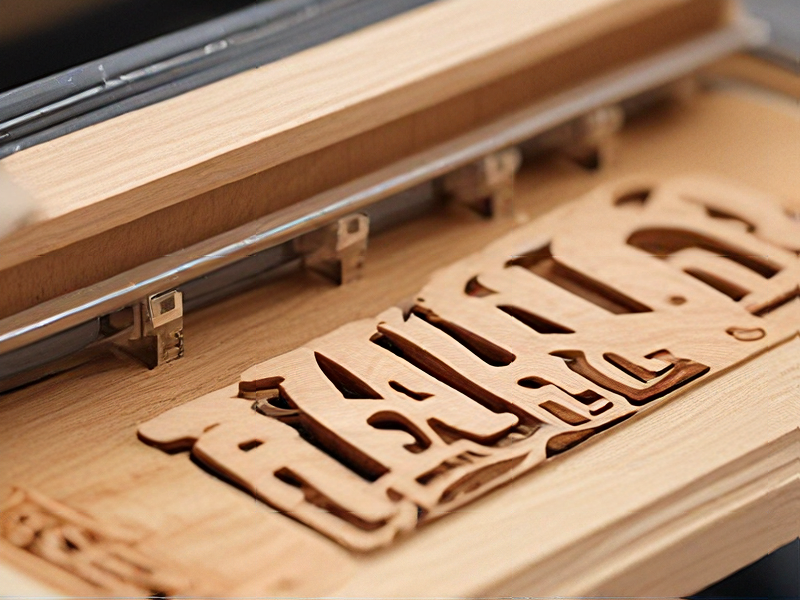