Technology and Applications of wood laser cutting machine
Wood laser cutting machines utilize high-powered lasers to precisely cut and engrave wood materials. These machines are equipped with CO2 lasers that can vaporize wood, producing clean edges and intricate designs without physical contact. The technology allows for highly detailed cuts and engravings on various types of wood, ranging from plywood to hardwood.
Applications of wood laser cutting machines are diverse across several industries. In manufacturing and production, these machines are used for creating furniture components, cabinetry, and decorative wood panels with exceptional accuracy and speed. They are also employed in crafting industries for making custom signage, ornaments, and art pieces, where precise detailing is crucial.
The benefits of using wood laser cutting machines include the ability to work with complex designs and patterns that traditional tools may struggle to execute. The process is non-contact, minimizing material wastage and reducing the need for extensive finishing work. Additionally, lasers can cut through thick materials efficiently, expanding the range of possible applications.
Furthermore, these machines are compatible with computer-aided design (CAD) software, enabling seamless integration into digital workflows for design prototyping and customization. They are also equipped with features for adjusting laser intensity and speed, allowing operators to achieve different levels of engraving depth and cutting precision.
Overall, wood laser cutting machines are indispensable tools in modern manufacturing and crafting, offering versatility, precision, and efficiency in transforming wood materials into a wide array of functional and artistic products.
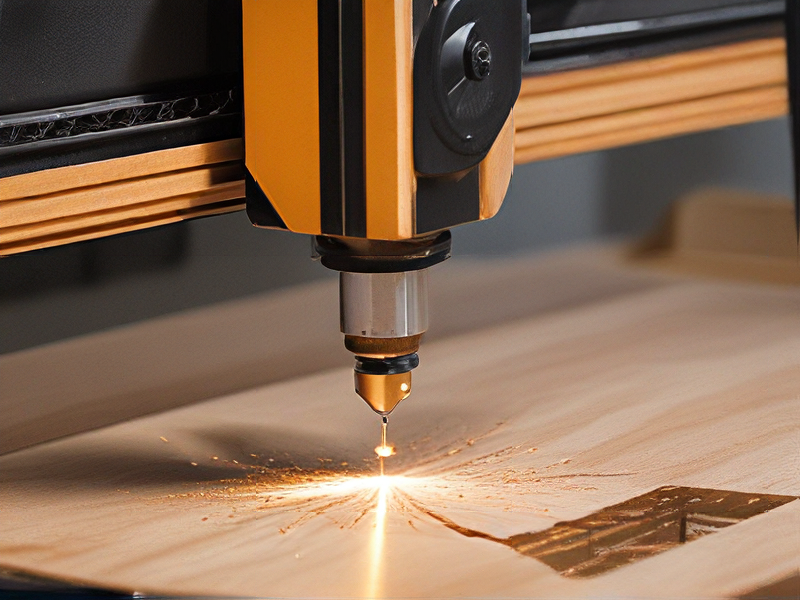
Quality Testing Methods for wood laser cutting machine and how to control quality
Quality testing methods for wood laser cutting machines typically include:
1. Dimensional Accuracy: Measure the precision of cuts using calipers or laser measurement tools. Ensure the actual dimensions match the design specifications.
2. Edge Quality: Inspect cut edges for smoothness, burns, or charring. Use visual inspection or a microscope to check for imperfections.
3. Material Integrity: Verify that the wood does not warp, crack, or splinter excessively during cutting. This ensures the structural integrity of the cut pieces.
4. Cutting Speed and Efficiency: Test the machine’s ability to maintain consistent cutting speeds and efficiency over time. Measure throughput and compare it against benchmarks.
5. Software Control and Calibration: Regularly calibrate the laser power, focus, and alignment using test patterns and software controls. This ensures accurate cutting according to design files.
6. Safety Features: Confirm that all safety features, such as emergency stop buttons and protective shields, are functional and comply with safety standards.
To control quality effectively:
– Establish Standard Operating Procedures (SOPs): Document procedures for machine setup, operation, and maintenance to ensure consistency.
– Implement Regular Maintenance: Schedule routine maintenance to keep the machine in optimal condition and prevent breakdowns.
– Employee Training: Train operators in machine operation, troubleshooting, and quality control measures to minimize errors.
– Quality Assurance Checks: Conduct regular inspections and audits to monitor machine performance and adherence to quality standards.
– Feedback Mechanism: Establish a feedback loop where operators can report issues or anomalies for quick resolution.
By integrating these methods and controls, manufacturers can ensure consistent and high-quality output from their wood laser cutting machines.
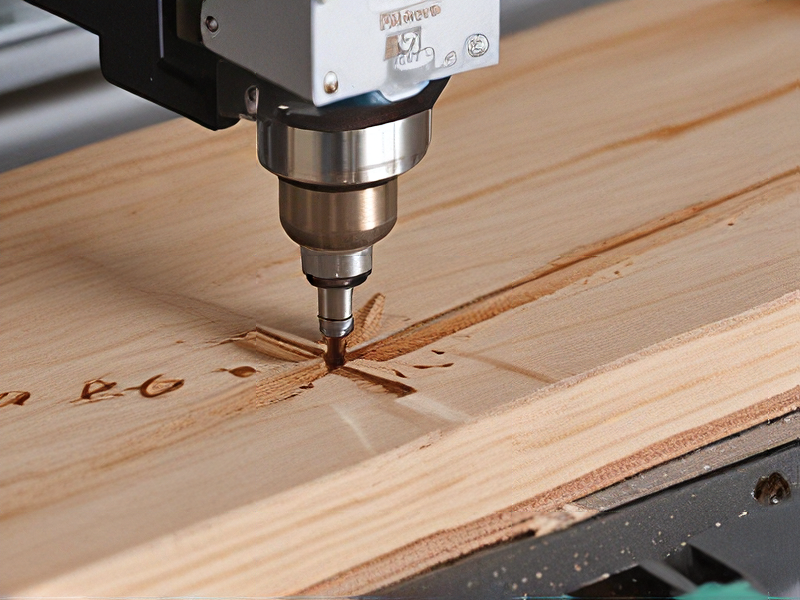
Tips for Procurement and Considerations when Purchasing from wood laser cutting machine
When purchasing a wood laser cutting machine for procurement purposes, several key considerations can ensure you make an informed decision:
1. Machine Specifications: Evaluate the laser power, cutting bed size, and types of wood it can process. Higher laser power allows for thicker and faster cuts, while bed size determines the maximum material dimensions.
2. Precision and Speed: Look for machines with high cutting precision and speed. This ensures intricate designs and efficient production.
3. Ease of Use and Software: User-friendly interfaces and compatible software streamline operations. Ensure the machine integrates well with your existing workflow.
4. Maintenance and Support: Check the supplier’s reputation for after-sales service, maintenance requirements, and availability of spare parts. Reliable support minimizes downtime.
5. Safety Features: Laser cutting involves high temperatures and potentially hazardous materials. Ensure the machine meets safety standards and includes protective features like enclosures and emergency stop buttons.
6. Cost Efficiency: Consider initial costs, operational expenses (like energy consumption), and potential return on investment. Compare quotes from multiple suppliers.
7. Customer Reviews and References: Seek feedback from other users to gauge reliability, performance, and durability.
8. Training and Installation: Evaluate if the supplier offers training for your operators and assistance with installation/setup.
9. Future Scalability: Assess whether the machine can accommodate future business growth and changes in production demands.
10. Environmental Impact: Consider the machine’s energy efficiency and waste management capabilities to align with sustainability goals.
By prioritizing these factors during your procurement process, you can ensure that the wood laser cutting machine you choose meets your operational needs efficiently and effectively.
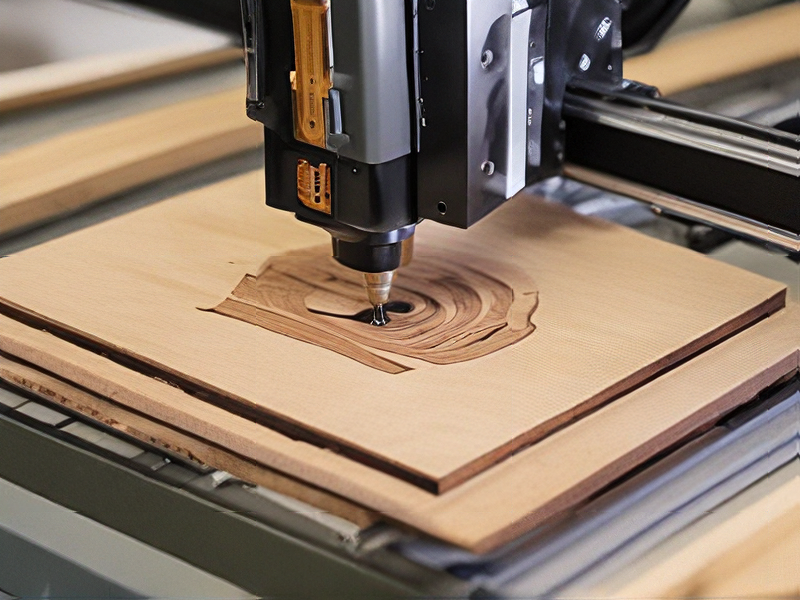
FAQs on Sourcing and Manufacturing from wood laser cutting machine in China
When sourcing and manufacturing from a wood laser cutting machine in China, consider these FAQs:
1. What should I consider when choosing a supplier?
– Look for suppliers with a proven track record in manufacturing laser cutting machines.
– Check reviews and customer feedback to gauge reliability and product quality.
– Ensure they can provide after-sales support and spare parts.
2. What types of wood can be cut with a laser cutting machine?
– Laser cutting machines can typically cut a wide range of woods, including plywood, MDF, hardwoods like oak and maple, and even some composite materials.
3. What are the advantages of using a laser cutting machine for wood?
– Precision cutting with intricate designs.
– Minimal material wastage compared to traditional cutting methods.
– Ability to cut complex shapes and patterns quickly.
4. Are there any limitations or considerations for using laser cutting on wood?
– Thickness of the wood can affect cutting depth and speed.
– Certain types of wood may produce more smoke or require ventilation.
– Initial setup costs and maintenance of the laser equipment should be considered.
5. How can I ensure product quality and compliance with regulations?
– Conduct inspections during and after manufacturing to ensure quality standards are met.
– Verify that the supplier complies with local and international safety regulations for laser equipment.
6. What are typical lead times and shipping considerations?
– Lead times vary but typically range from weeks to months depending on customization and order volume.
– Shipping costs, logistics, and import/export regulations should be carefully planned.
By addressing these FAQs, you can navigate the process of sourcing and manufacturing wood laser cutting machines in China more effectively.
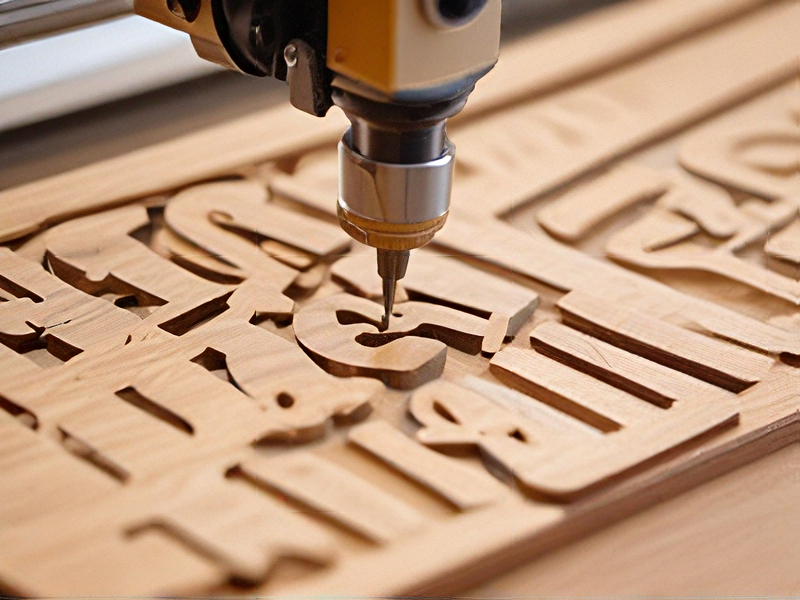