Technology and Applications of laser machines for wood cutting
Laser machines for wood cutting utilize high-powered lasers to precisely cut and engrave wood materials across various thicknesses and densities. These machines are equipped with CO2 or fiber lasers that emit concentrated beams of light, which are directed through mirrors or fiber optics onto the wood surface. Here’s an overview of their technology and applications:
Technology:
1. Laser Source: CO2 lasers (wavelength around 10.6 micrometers) are commonly used for wood cutting due to their ability to efficiently vaporize wood with minimal heat-affected zones. Fiber lasers (wavelength around 1.06 micrometers) are also used, especially for marking and engraving wood.
2. Optics and Guidance: The laser beam is directed precisely using mirrors or fiber optics onto the wood surface, guided by computer numerical control (CNC) systems. This ensures accuracy and repeatability in cutting patterns.
3. Power and Speed: Laser machines vary in power levels (ranging from tens to hundreds of watts) and can adjust cutting speeds based on the wood’s type and thickness. Higher power levels enable faster cutting speeds and deeper cuts.
Applications:
1. Precision Cutting: Laser machines excel in cutting intricate designs, curves, and sharp corners that may be challenging with traditional saws or routers. They are used in manufacturing furniture components, cabinetry, and decorative wooden items.
2. Engraving and Marking: Beyond cutting, lasers are used for engraving logos, serial numbers, or decorative patterns onto wooden surfaces. This is popular in custom woodworking, signage, and artistic applications.
3. Material Versatility: Laser machines can handle various wood types, including hardwoods, softwoods, plywood, and veneers. They can cut through thick materials up to several centimeters, depending on the laser’s power.
4. Automation and Efficiency: Integration with CAD/CAM software allows for automated production processes, minimizing waste and maximizing efficiency in wood processing industries.
In conclusion, laser machines for wood cutting combine advanced laser technology with precise CNC control to offer versatile cutting, engraving, and marking capabilities across a wide range of wood materials. They enhance productivity and enable intricate designs that traditional tools cannot achieve efficiently.
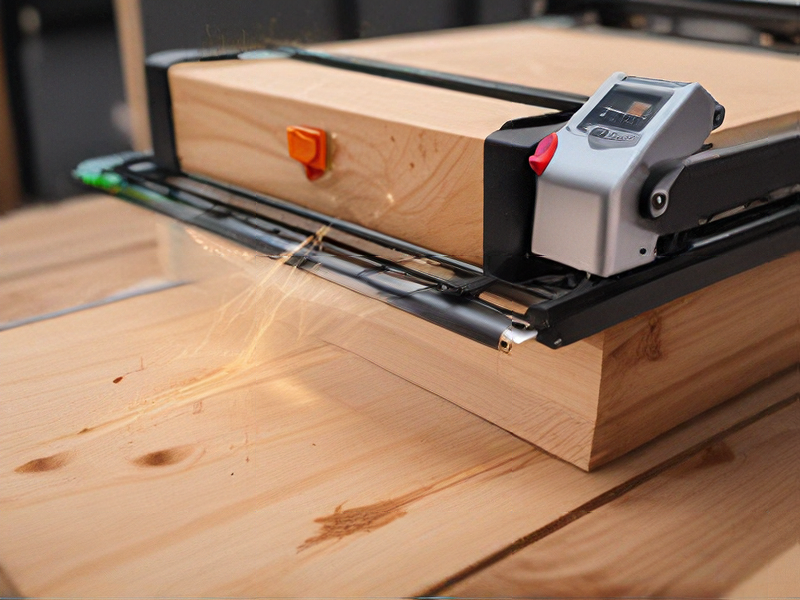
Quality Testing Methods for laser machines for wood cutting and how to control quality
Quality testing methods for laser machines used in wood cutting typically involve several key approaches:
1. Dimensional Accuracy Checks: Verify that the laser-cut pieces match the specified dimensions using precision measurement tools like calipers or coordinate measuring machines (CMM).
2. Edge Quality Assessment: Evaluate the smoothness and precision of cut edges. This can be done visually or with microscopic inspection to ensure there are no burrs or rough edges.
3. Material Integrity Testing: Check for any signs of material damage, such as burning, charring, or excessive heat affecting the wood structure. This ensures the wood remains structurally sound after cutting.
4. Precision of Cuts: Utilize test patterns or geometric shapes to assess the laser’s ability to cut accurately along complex paths and intricate designs.
5. Repeatable Performance: Conduct tests over time to ensure consistency in cutting performance, particularly with varying wood types and thicknesses.
To control quality effectively:
– Calibration and Maintenance: Regularly calibrate the laser machine according to manufacturer guidelines and maintain it properly to ensure consistent performance.
– Operator Training: Train operators thoroughly on machine operation, maintenance, and quality control procedures to minimize errors and maximize output quality.
– Quality Control Plan: Implement a structured quality control plan that includes regular inspections, testing procedures, and documentation of results.
– Feedback Loop: Establish a feedback mechanism where issues or deviations in quality are promptly addressed, possibly through iterative improvement processes.
By implementing these methods and controls, manufacturers can ensure that laser machines for wood cutting consistently produce high-quality outputs that meet customer specifications and expectations.
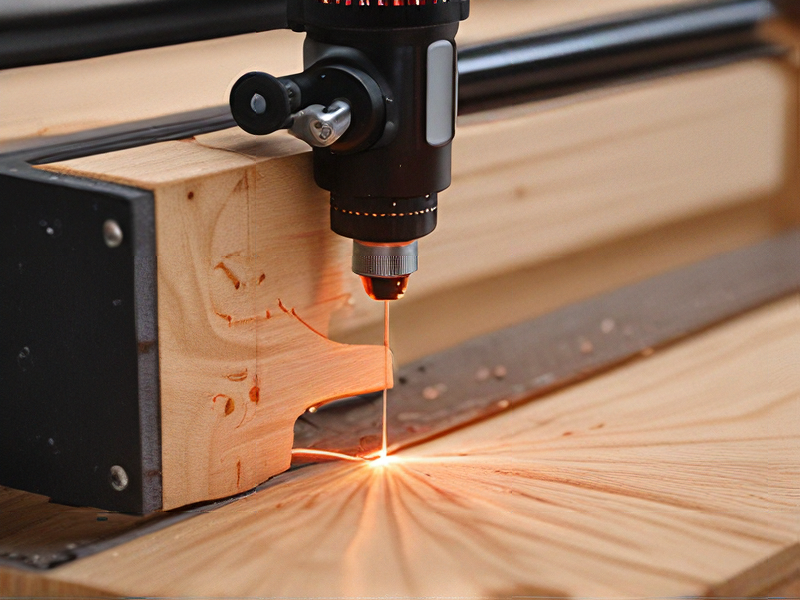
Tips for Procurement and Considerations when Purchasing from laser machines for wood cutting
When purchasing laser machines for wood cutting, consider these essential tips and considerations:
1. Laser Type and Power: Choose between CO2 and fiber lasers based on your specific wood cutting needs. CO2 lasers are versatile for various wood types and thicknesses, while fiber lasers are more efficient for thin materials and offer higher precision.
2. Cutting Area Size: Determine the required bed size or cutting area based on the typical dimensions of your wood pieces. Ensure the machine can accommodate your largest workpieces comfortably.
3. Accuracy and Precision: Check the laser’s focusing capability and beam quality for precise cuts, especially if you need intricate designs or fine details in your woodwork.
4. Speed and Productivity: Evaluate the machine’s cutting speed and how it aligns with your production requirements. Higher wattage lasers generally cut faster but may come at a higher cost.
5. Ease of Use and Software Compatibility: User-friendly interfaces and compatible software are crucial for seamless operation and design flexibility. Consider the learning curve for your operators.
6. Maintenance Requirements: Understand the maintenance schedule and costs associated with the laser machine. Opt for machines with accessible parts and good support from the manufacturer.
7. Safety Features: Laser machines pose inherent risks, so ensure the machine complies with safety standards (like FDA regulations in the US) and includes features like emergency stop buttons, protective enclosures, and exhaust systems.
8. Support and Training: Choose a supplier that offers comprehensive training for your operators and ongoing technical support to troubleshoot issues quickly.
9. Budget and ROI: Balance initial investment with long-term returns. Consider not just the purchase price but also operational costs, maintenance, and potential productivity gains.
10. Reviews and References: Research user reviews and seek references from other woodworkers using similar laser machines to gauge reliability and performance.
By carefully considering these factors, you can choose a laser machine for wood cutting that enhances productivity, meets safety standards, and aligns with your specific woodworking needs.
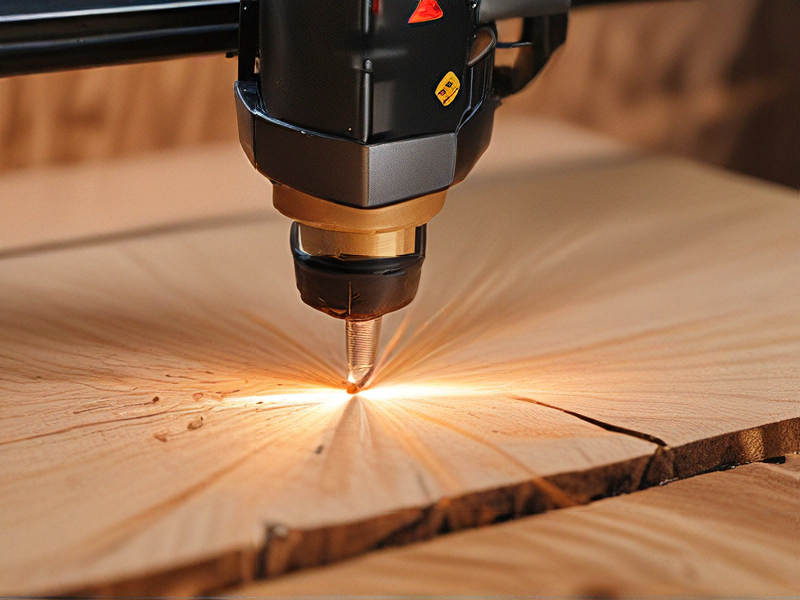
FAQs on Sourcing and Manufacturing from laser machines for wood cutting in China
## FAQs on Sourcing & Manufacturing Wood Cutting Laser Machines in China
Where can I find reputable laser machine manufacturers in China?
Start with online directories like Alibaba, Global Sources, and Made-in-China. Look for manufacturers with good reviews, certifications (e.g., ISO), and clear contact information.
What are the key factors to consider when choosing a manufacturer?
* Machine type & specs: CO2 or fiber laser, cutting area, power, accuracy, and automation level.
* Experience & reputation: Years in business, customer testimonials, and industry recognition.
* Pricing & payment terms: Get competitive quotes and clarify payment methods and timelines.
* After-sales service & support: Warranty coverage, spare parts availability, and technical assistance.
What are the typical lead times for custom-built machines?
Expect lead times ranging from 2 to 6 months depending on complexity and manufacturer capacity.
How can I ensure quality control during manufacturing?
Request detailed production photos and videos, conduct virtual site visits, and consider third-party inspections.
What are the shipping options and costs?
Most manufacturers offer both sea and air freight options. Shipping costs vary based on machine size, destination, and chosen method.
Are there any import regulations I need to be aware of?
Yes, check with your local customs office for specific regulations and required documentation.
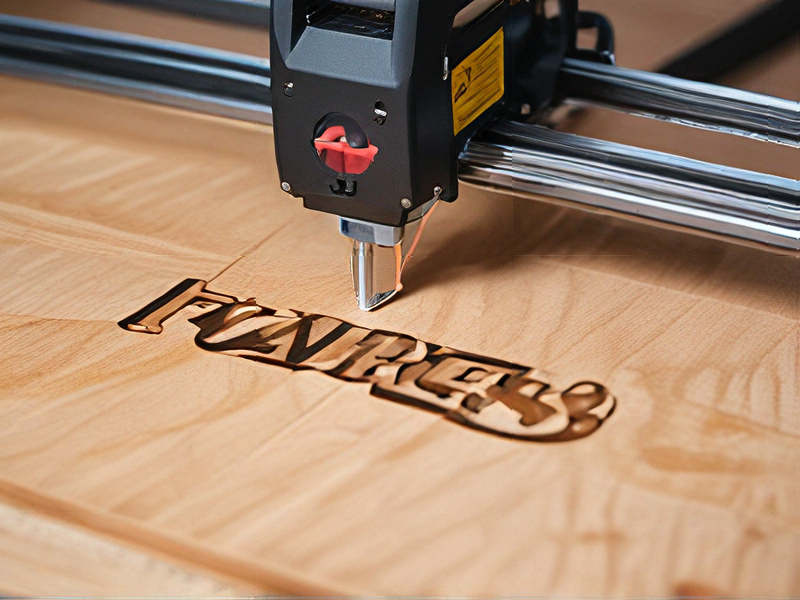