Technology and Applications of metal grinding
Technology and Applications of Metal Grinding
Technology:
Metal grinding is a crucial machining process that involves the use of abrasive wheels to remove material from a workpiece, achieving a high surface finish and precise dimensions. There are various types of metal grinding technologies:
1. Surface Grinding: Uses a rotating abrasive wheel to smooth flat surfaces.
2. Cylindrical Grinding: Works on the external surfaces of cylindrical objects.
3. Centerless Grinding: Involves no holding of the workpiece, relying on a blade and two wheels.
4. Internal Grinding: Focuses on the interior surfaces of cylindrical workpieces.
5. Electrochemical Grinding (ECG): Combines electrochemical machining with conventional grinding, minimizing heat and improving precision.
Applications:
Metal grinding is pivotal in various industries due to its ability to produce high-precision parts. Key applications include:
1. Automotive Industry: Grinding is essential for manufacturing engine components, gears, and transmission parts, ensuring they meet strict tolerance requirements.
2. Aerospace Industry: Used for producing high-precision turbine blades, landing gear components, and structural parts, where safety and performance are critical.
3. Tool and Die Making: Ensures the production of accurate molds and dies used in stamping and injection molding processes.
4. Medical Devices: Grinding is used to create surgical instruments, implants, and other medical devices, requiring precise dimensions and smooth finishes.
5. Heavy Machinery: Components such as bearings, shafts, and hydraulic parts are ground to meet high durability and performance standards.
6. Electronics: In the manufacturing of semiconductors and other electronic components, grinding ensures the required precision and surface quality.
In summary, metal grinding technology plays a vital role in achieving precision, smooth finishes, and strict tolerances in various industries, making it indispensable in modern manufacturing.
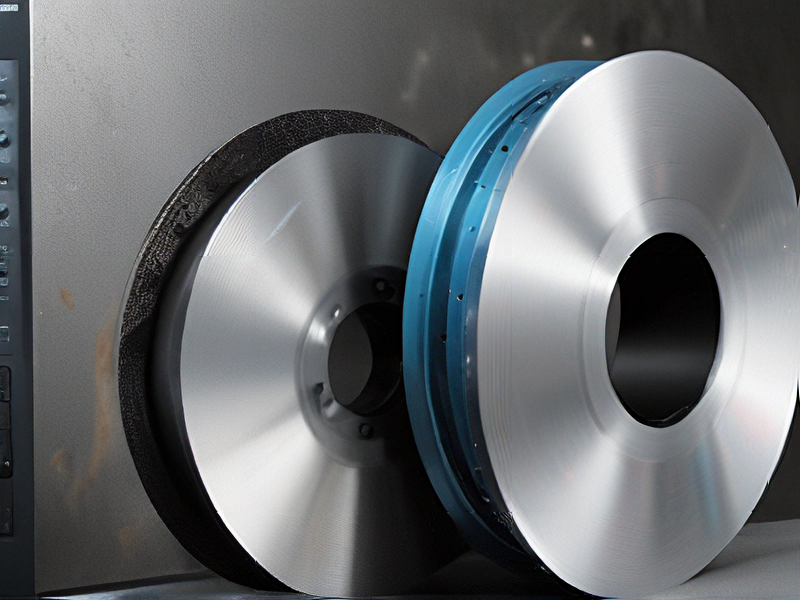
Quality Testing Methods for metal grinding and how to control quality
Quality testing methods for metal grinding typically focus on ensuring dimensional accuracy, surface finish, and structural integrity of the metal components. Here are key methods to control quality:
1. Dimensional Inspection: Utilize precision measuring tools such as calipers, micrometers, or coordinate measuring machines (CMM) to verify dimensions against engineering drawings.
2. Surface Roughness Measurement: Employ surface profilometers to assess the roughness average (Ra) or other surface texture parameters, ensuring it meets specified requirements.
3. Visual Inspection: Conduct visual checks for defects like cracks, scratches, or improper grinding patterns that could affect functionality or aesthetics.
4. Hardness Testing: Perform hardness tests using tools such as Rockwell or Vickers testers to ensure the metal’s hardness matches specified requirements, indicating proper heat treatment and material quality.
5. Metallographic Examination: Use metallographic techniques like microscopy or etching to inspect microstructures for anomalies such as grain size, inclusion content, or phase distribution.
To control quality effectively:
– Establish Standards: Define clear quality standards and specifications for dimensions, surface finish, hardness, etc., based on customer requirements and industry standards.
– Regular Inspections: Implement regular inspection intervals during grinding operations to detect deviations early and take corrective actions promptly.
– Training and Skill Development: Ensure operators are trained in inspection methods and understand the importance of quality control in every stage of grinding.
– Feedback Loop: Establish a feedback loop where inspection results inform process adjustments or improvements to maintain consistent quality.
By integrating these methods into the grinding process and maintaining rigorous quality control measures, manufacturers can ensure that their metal grinding operations produce components that meet or exceed customer expectations and industry standards.
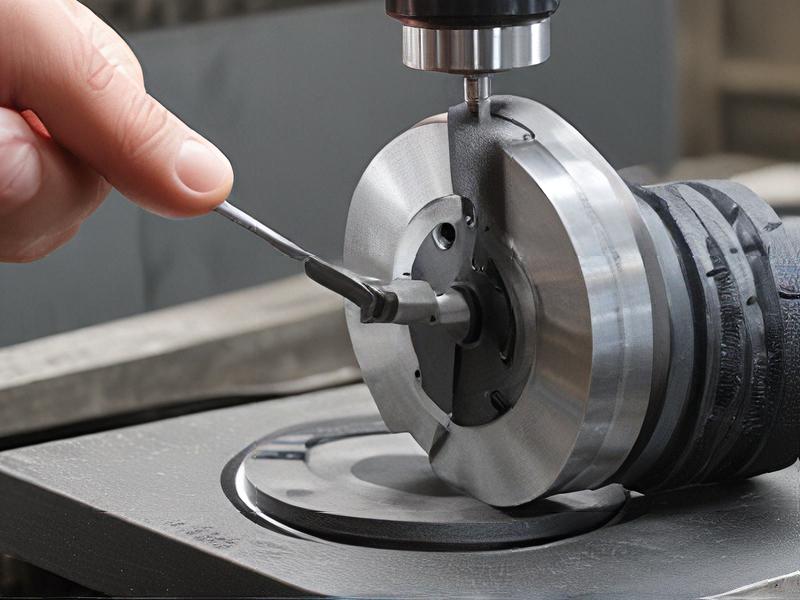
Tips for Procurement and Considerations when Purchasing from metal grinding
When procuring metal grinding equipment, several key considerations can ensure you make an informed decision:
1. Performance Requirements: Define your operational needs such as throughput capacity, precision, and type of metals to be processed. Ensure the equipment meets or exceeds these specifications.
2. Quality and Durability: Opt for reputable brands known for quality craftsmanship and durability. Check customer reviews and warranties to gauge reliability.
3. Safety Features: Prioritize machines with robust safety features like emergency stops, protective shields, and compliance with industry standards (e.g., OSHA in the US).
4. Ease of Maintenance: Choose equipment with accessible parts, clear maintenance guidelines, and availability of spare parts. This minimizes downtime and reduces operational costs.
5. Cost and ROI: Compare initial purchase costs with long-term operational savings and productivity gains. Factor in maintenance, energy consumption, and potential for increased throughput.
6. Supplier Reputation: Select suppliers with a proven track record in the industry. Consider their support capabilities, including training, technical assistance, and responsiveness to queries.
7. Environmental Impact: Assess the equipment’s energy efficiency and adherence to environmental regulations. Opt for models that minimize waste generation and energy consumption.
8. Compatibility and Integration: Ensure the equipment integrates smoothly with existing workflows and other machinery. Compatibility with software systems for data logging and analysis can enhance operational efficiency.
9. Future Expansion: Anticipate future growth needs and consider scalability options offered by the equipment. Flexibility in configuration and capacity can support business expansion.
10. User Feedback: Gather feedback from operators who will use the equipment daily. Their insights on usability, reliability, and performance can provide valuable perspective.
By focusing on these considerations, you can effectively procure metal grinding equipment that aligns with your operational requirements, enhances productivity, and ensures long-term value for your investment.
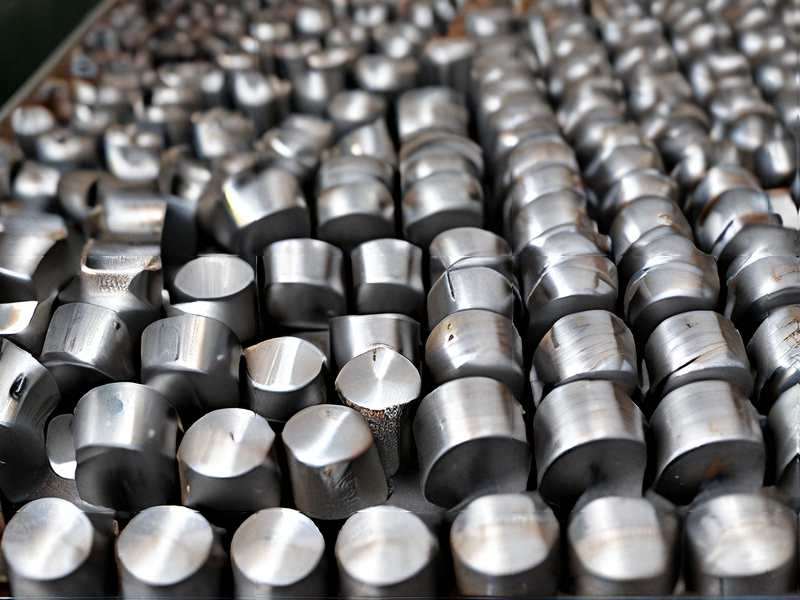
FAQs on Sourcing and Manufacturing from metal grinding in China
When sourcing metal grinding services from China, it’s essential to consider several frequently asked questions (FAQs) to ensure quality and reliability:
1. What types of metal grinding services are available in China?
China offers a wide range of metal grinding services, including precision grinding, surface grinding, cylindrical grinding, and internal grinding, among others.
2. How can I ensure the quality of metal grinding in China?
Quality assurance can be ensured by selecting suppliers with certifications like ISO 9001, conducting factory audits, and requesting samples and test reports.
3. What are the typical lead times for metal grinding orders from China?
Lead times vary based on the complexity of the job and supplier capacity but typically range from a few days to several weeks.
4. What are the factors influencing the cost of metal grinding services in China?
Factors include the complexity of the part, tolerances required, batch size, and the type of grinding process used.
5. How do I handle intellectual property concerns when sourcing from China?
Use non-disclosure agreements (NDAs), clearly define ownership in contracts, and consider working with suppliers who respect intellectual property rights.
6. What are common challenges when sourcing metal grinding services from China?
Challenges may include language barriers, cultural differences, logistics, and ensuring consistent quality over time.
7. Can I visit the facilities of potential suppliers in China?
Yes, many suppliers welcome visits. It’s beneficial to tour facilities, meet the team, and inspect equipment and processes firsthand.
8. How do I manage communication effectively with Chinese suppliers?
Establish clear communication channels, use translators if necessary, and maintain regular contact to address any issues promptly.
9. What are the payment terms typically used when sourcing from China?
Payment terms often include a deposit upfront with the balance due upon completion or shipment, but terms can vary and should be negotiated.
10. What steps should I take to ensure environmental and ethical standards are met?
Choose suppliers who adhere to local environmental regulations and ethical standards, and consider certifications such as ISO 14001 for environmental management.
Navigating the sourcing and manufacturing landscape in China requires diligence, clear communication, and thorough due diligence to ensure a successful partnership for metal grinding services.
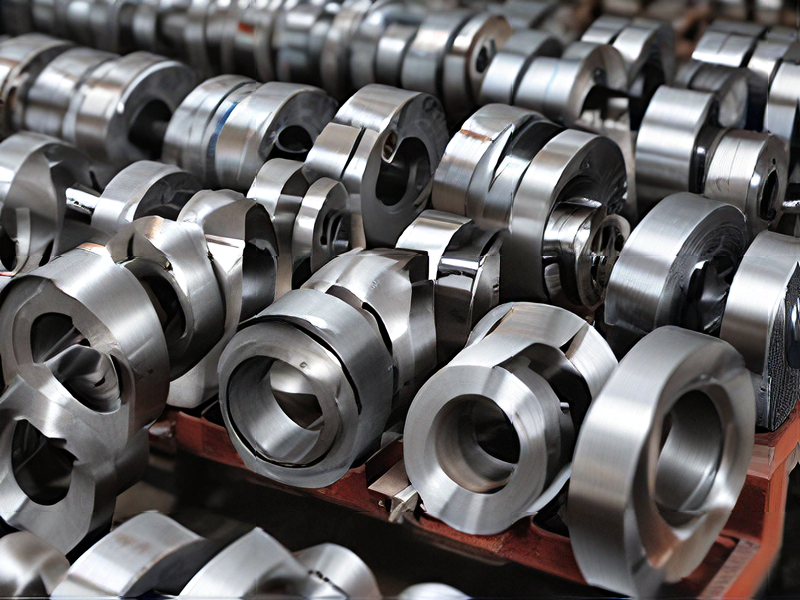