Technology and Applications of machine to laser cut wood
Machine-to-laser cutting technology revolutionizes woodworking by employing high-powered lasers to precisely cut wood based on digital designs. This process starts with CAD software, where designs are created or imported. The software then translates these designs into instructions for the laser cutter, specifying cut paths, depths, and shapes.
In operation, the laser cutter emits a concentrated beam of light that vaporizes or melts the wood along the programmed path. This method offers exceptional precision, enabling intricate designs and sharp edges that traditional tools struggle to replicate. Moreover, it minimizes material wastage as the cuts are extremely precise.
Applications span various industries, including furniture manufacturing, where complex components can be produced efficiently and with minimal manual intervention. Prototyping benefits significantly from laser cutting, allowing rapid iteration and refinement of designs. Artisans also utilize this technology for detailed artwork and decorative pieces, leveraging its ability to etch or engrave wood surfaces precisely.
Advancements in laser cutting technology have led to increased automation and integration with other manufacturing processes, enhancing overall efficiency and output quality. As sustainability gains importance, laser cutting’s minimal material wastage and energy efficiency further underscore its appeal.
In conclusion, machine-to-laser cutting represents a transformative technology in woodworking, offering unparalleled precision, versatility across industries, and sustainable manufacturing practices. Its applications continue to expand as innovations in laser technology and software integration advance.
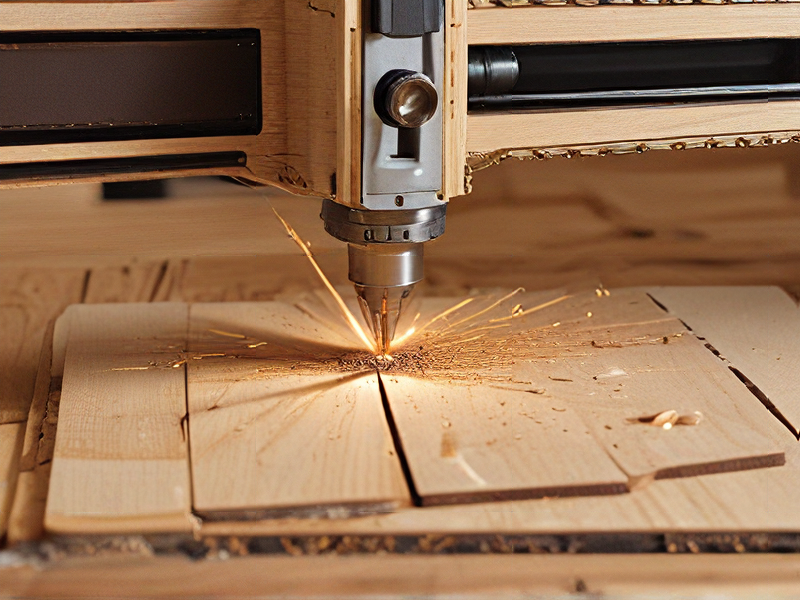
Quality Testing Methods for machine to laser cut wood and how to control quality
Quality testing methods for machine laser cutting wood typically involve several key steps to ensure precision and consistency:
1. Dimensional Accuracy: Use calipers or micrometers to measure cut dimensions against specifications. Variations beyond tolerance indicate potential issues with machine calibration or material handling.
2. Edge Quality: Inspect cut edges for smoothness and consistency. Visual inspection and touch can reveal rough spots, charring, or irregularities that affect finish quality.
3. Material Integrity: Check for signs of burning, scorching, or warping on the wood surface, especially at high-power settings. Ensure the wood remains structurally sound and aesthetically pleasing.
4. Accuracy of Cuts: Use precision measuring tools to verify the alignment and accuracy of cuts relative to design specifications. Misaligned cuts can impact assembly or aesthetic outcomes.
5. Burn-through and Kerf Width: Measure the kerf width (width of material removed by the laser) and check for burn-through on thinner materials. Consistency in these parameters ensures predictable outcomes.
To control quality effectively:
– Regular Maintenance: Schedule routine maintenance for the laser cutter to keep optics clean, ensure alignment, and replace worn parts.
– Calibration Checks: Regularly calibrate the laser cutter according to manufacturer guidelines to maintain cutting precision.
– Material Inspection: Use high-quality wood and inspect each batch for consistency in density and moisture content, as these factors affect cutting performance.
– Operator Training: Train operators thoroughly in machine operation, material handling, and quality inspection protocols to minimize errors.
– Quality Assurance Procedures: Implement documented procedures for testing and inspecting cuts at various stages of production to catch defects early.
By integrating these testing methods and quality control measures into your production process, you can consistently achieve high-quality laser-cut wood products that meet customer expectations.
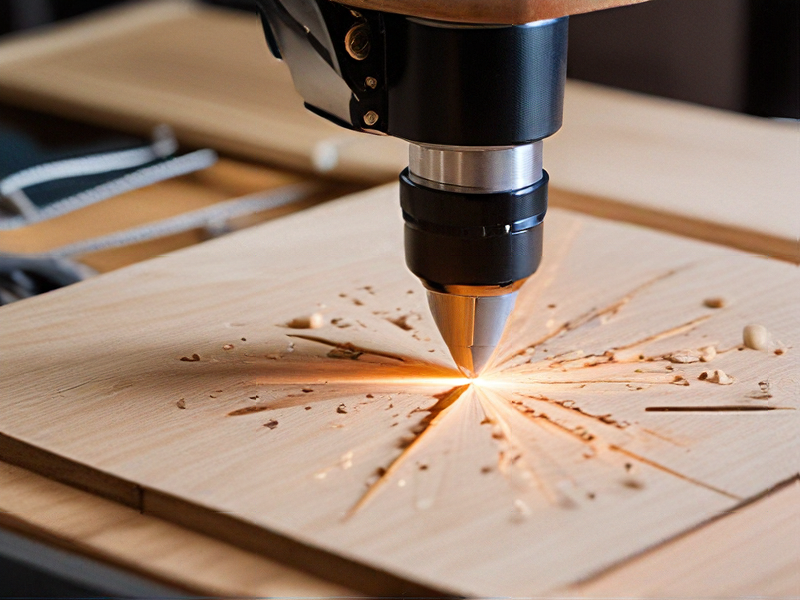
Tips for Procurement and Considerations when Purchasing from machine to laser cut wood
When purchasing a machine for laser cutting wood, several key considerations and tips can ensure you make an informed procurement decision:
1. Laser Type and Power: Choose a laser type (CO2 or fiber) and power level suitable for your intended wood cutting applications. CO2 lasers are versatile for various wood thicknesses and types, while fiber lasers excel in precision cutting.
2. Bed Size and Capacity: Consider the size of the laser bed in relation to the maximum dimensions of wood sheets or pieces you plan to work with. Ensure the machine can accommodate your typical workload sizes.
3. Software and Interface: Evaluate the user-friendliness of the machine’s software and interface. Intuitive software can streamline design-to-cut workflows and minimize learning curves for operators.
4. Cutting Speed and Accuracy: Look for machines that offer optimal cutting speed without compromising accuracy and edge quality. Features like autofocus and advanced motion systems contribute to consistent results.
5. Maintenance and Support: Check for availability of technical support, training, and maintenance services from the supplier or manufacturer. Reliable support ensures minimal downtime and maximum machine longevity.
6. Ventilation and Safety Features: Laser cutting generates fumes and requires proper ventilation. Ensure the machine has adequate ventilation systems and safety features such as emergency stops and enclosure interlocks.
7. Cost Efficiency: Consider not only the initial purchase cost but also operational costs such as electricity, maintenance, and consumables (e.g., laser tubes). Calculate the machine’s long-term cost efficiency.
8. Reviews and References: Research user reviews and seek references from other businesses using similar machines. Insights from current users can provide valuable perspectives on performance and reliability.
9. Future Expansion: Anticipate future needs such as additional functionalities (e.g., rotary attachments for engraving cylindrical objects) or increased production capacity. Choose a machine that can scale with your business growth.
10. Training and Skill Development: Invest in training for operators to maximize machine utilization and safety. Training programs offered by manufacturers or third-party providers can enhance operational efficiency.
By carefully considering these factors and tips, you can select a laser cutting machine that meets your specific wood cutting requirements while ensuring productivity, safety, and cost-effectiveness.
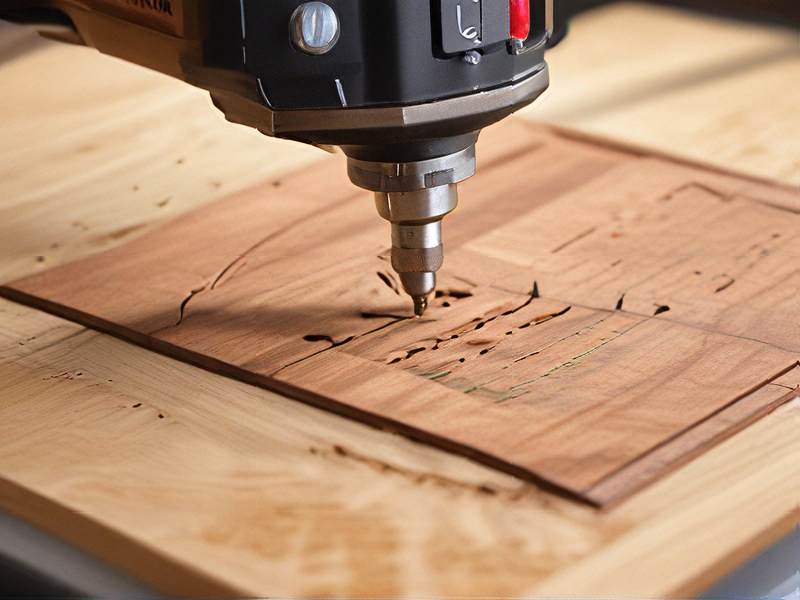
FAQs on Sourcing and Manufacturing from machine to laser cut wood in China
FAQs on Sourcing and Manufacturing Laser Cut Wood in China
#### 1. Why should I consider sourcing laser-cut wood from China?
China is a global leader in manufacturing with advanced technology, skilled labor, and competitive pricing. The country’s vast manufacturing base ensures a variety of suppliers and materials.
#### 2. How do I find reliable suppliers?
Use platforms like Alibaba, Global Sources, and Made-in-China. Verify supplier credentials, check reviews, and request samples. Consider third-party inspection services to ensure quality.
#### 3. What should I look for in a supplier?
Check for experience in laser cutting, quality certifications (ISO, FSC), production capacity, and previous client references. A supplier with strong R&D capabilities can offer better customization options.
#### 4. What types of wood are available for laser cutting?
Common woods include plywood, MDF, bamboo, and various hardwoods like oak and walnut. Ensure the wood is of high quality and free from defects that can affect the laser cutting process.
#### 5. What are the typical lead times?
Lead times vary based on order size, complexity, and supplier capacity. Generally, expect 2-4 weeks for production and an additional 1-2 weeks for shipping.
#### 6. How do I ensure the quality of the laser-cut wood?
Request detailed product specifications and samples. Use third-party inspection services to check the quality during production and before shipment.
#### 7. What are the payment terms?
Common terms include a 30% deposit before production and 70% upon completion. Use secure payment methods like PayPal, letters of credit, or escrow services for added security.
#### 8. What about shipping and logistics?
Suppliers often handle shipping logistics. Choose between air and sea freight based on your budget and timeline. Ensure your supplier provides necessary documentation like the bill of lading and commercial invoice.
#### 9. Are there any import regulations?
Check your country’s import regulations for wood products, including tariffs, taxes, and required certifications. Ensure compliance to avoid customs issues.
#### 10. How can I manage communication and language barriers?
Use clear, concise language and confirm all details in writing. Many Chinese suppliers have English-speaking staff, but using translation tools can also help ensure accurate communication.
By following these guidelines, you can effectively source high-quality laser-cut wood from China, ensuring a smooth manufacturing process and reliable product delivery.
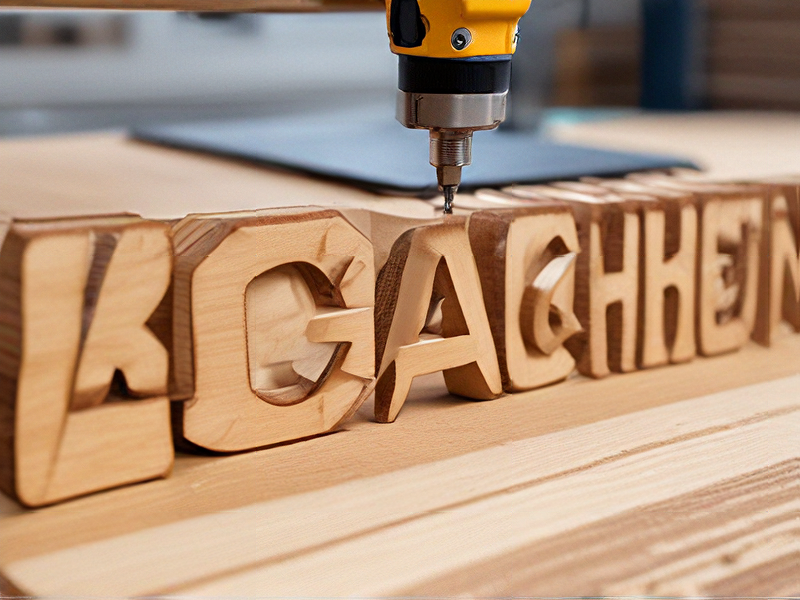