Technology and Applications of laser cutting machine for wood
Laser cutting machines for wood utilize focused laser beams to precisely cut through wood materials. This technology offers several advantages, including high precision, speed, and versatility in cutting intricate patterns and designs.
Technology:
Laser cutting machines for wood employ CO2 lasers typically in the range of 150 to 400 watts. These machines direct the laser beam through a series of mirrors and lenses onto the wood surface. The intense heat generated by the laser vaporizes or burns away the material along the designated cutting path. Computer numerical control (CNC) systems precisely control the movement of the laser, ensuring accurate cuts according to programmed designs.
Applications:
1. Custom Furniture: Laser cutting allows for precise cutting of wood pieces, facilitating the creation of custom furniture designs with intricate details.
2. Craftsmanship and Art: Artists and craftsmen use laser cutting to create detailed wood artwork, sculptures, and decorative items that would be challenging to produce manually.
3. Architectural Models: Architects and designers use laser cutting to create scaled models of buildings and structures, showcasing intricate details and designs.
4. Inlays and Joinery: Laser cutting enables precise fitting of wood pieces for inlays and intricate joinery work, enhancing craftsmanship and design.
5. Prototyping: Manufacturers use laser cutting to produce prototypes of new wood products quickly and accurately before full-scale production.
6. Packaging: Laser-cut wood is used in packaging design for custom inserts and displays, ensuring secure and aesthetically pleasing packaging solutions.
Overall, laser cutting machines for wood are essential tools in various industries, offering precision, speed, and versatility in creating intricate designs and functional wood products.
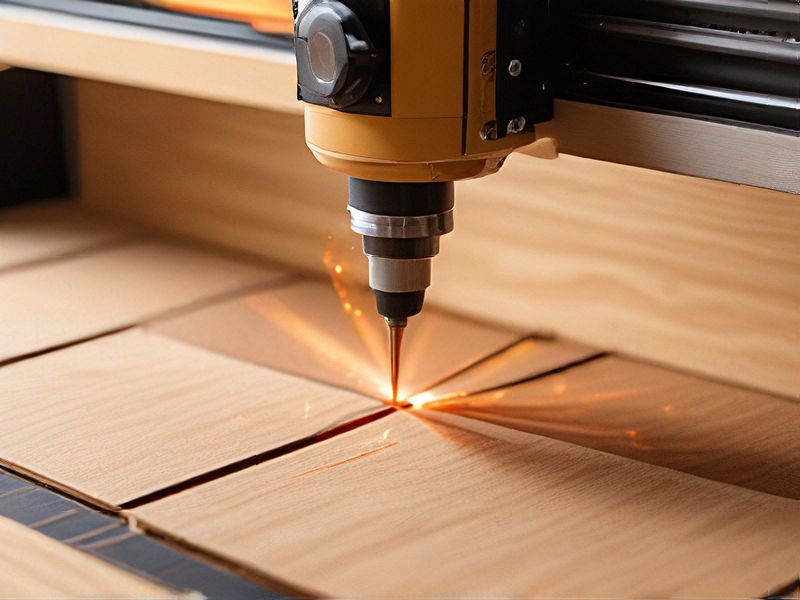
Quality Testing Methods for laser cutting machine for wood and how to control quality
Quality testing methods for laser cutting machines used for wood typically focus on ensuring precision, efficiency, and consistency in cutting operations. Here are key methods to control and maintain quality:
1. Dimensional Accuracy: Measure the dimensions of cut pieces against design specifications using calipers or laser measurement devices.
2. Edge Quality Inspection: Evaluate the smoothness and cleanliness of cut edges to ensure they meet desired standards. Visual inspection and touch can often detect rough edges or charring.
3. Material Inspection: Check for signs of burning or discoloration on the wood surface caused by excessive heat during cutting. This can affect the aesthetic and functional quality of the final product.
4. Testing for Kerf Width: Measure the width of the kerf (material removed during cutting) to ensure it matches the machine settings and design requirements.
5. Repeatable Testing Protocols: Develop standardized testing procedures to ensure consistent quality across batches. This includes setting up a schedule for regular machine maintenance and calibration.
6. Operator Training and Monitoring: Properly train operators to use the laser cutting machine effectively and monitor their performance to ensure adherence to quality standards.
7. Quality Control Checks: Implement checkpoints throughout the production process to catch any deviations early and take corrective actions promptly.
By integrating these methods into your quality control process, you can ensure that your laser cutting machine consistently produces high-quality wood products that meet customer expectations.
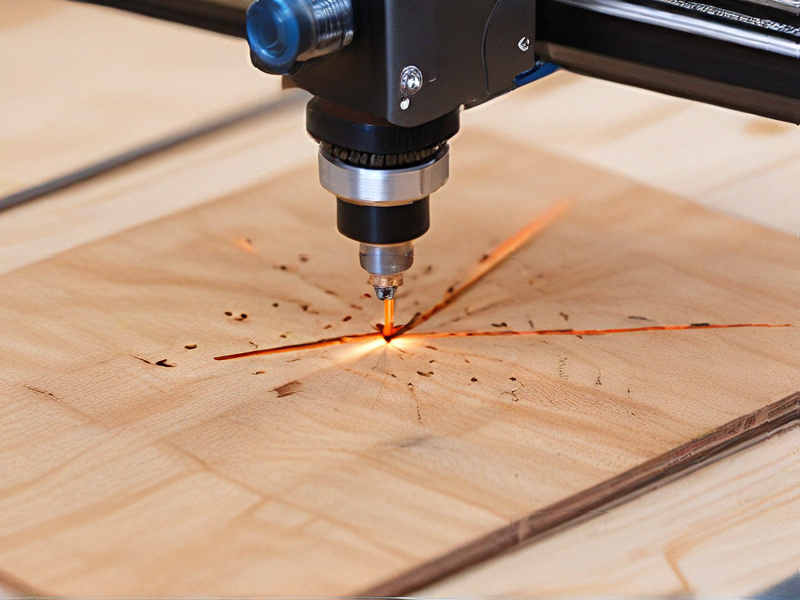
Tips for Procurement and Considerations when Purchasing from laser cutting machine for wood
When purchasing a laser cutting machine for wood, consider several key factors to ensure you make an informed decision:
1. Machine Specifications: Look for a machine with appropriate power levels (typically measured in watts) suitable for the thickness and type of wood you plan to cut. Higher wattage generally allows for faster cutting speeds and the ability to cut thicker materials.
2. Cutting Bed Size: Ensure the cutting bed size accommodates the largest dimensions of wood you intend to work with. This prevents limitations and allows for flexibility in your projects.
3. Accuracy and Precision: Check the machine’s specifications for accuracy in cutting, particularly if you require intricate designs or precise dimensions in your woodwork.
4. Ease of Use and Software Compatibility: User-friendly interfaces and compatibility with commonly used design software (like AutoCAD or Adobe Illustrator) can streamline workflow and reduce learning curves.
5. Maintenance Requirements: Understand the maintenance schedule and requirements for the machine, including cleaning procedures and the availability of technical support.
6. Safety Features: Laser cutting machines involve high-power lasers and moving parts. Ensure the machine has adequate safety features such as emergency stop buttons, enclosed cutting areas, and laser beam shielding.
7. Manufacturer Reputation and Support: Choose a reputable manufacturer known for quality machines and reliable customer support. Read reviews and seek recommendations from others in the industry.
8. Cost and Return on Investment (ROI): Compare prices while considering long-term costs such as maintenance, operating expenses (like electricity and consumables), and the potential increase in productivity and capabilities.
9. Training and Support: Ensure the supplier offers training on machine operation and maintenance. This is crucial for maximizing efficiency and safety.
10. Future Expansion: Consider whether the machine can be upgraded or expanded in the future to accommodate changing business needs.
By carefully evaluating these factors, you can select a laser cutting machine that meets your specific woodworking requirements effectively and efficiently.
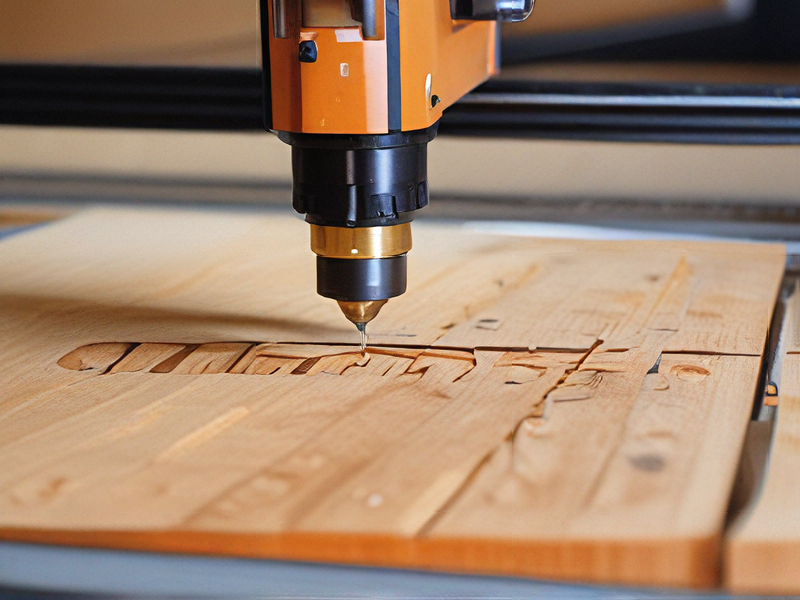
FAQs on Sourcing and Manufacturing from laser cutting machine for wood in China
Certainly! Here are some FAQs regarding sourcing and manufacturing from laser cutting machines for wood in China:
1. What are the advantages of sourcing laser cutting machines from China?
Sourcing from China often offers cost advantages due to lower labor and manufacturing costs. Chinese manufacturers also have extensive experience in producing a wide range of machinery, including laser cutting machines.
2. How do I ensure quality when sourcing from China?
It’s crucial to conduct thorough research and due diligence on potential suppliers. This includes requesting samples, visiting factories if possible, and checking for certifications like ISO standards. Using a reputable sourcing agent or conducting regular quality inspections can also help maintain standards.
3. What types of wood can laser cutting machines in China handle?
Laser cutting machines from China are capable of handling various types of wood, including plywood, MDF (Medium Density Fiberboard), hardwoods like oak and maple, and even some types of softwoods. The machine’s specifications and laser power will determine the exact capabilities.
4. Are there any regulatory or import/export considerations?
Yes, importing machinery from China may involve compliance with local regulations and import duties in your country. It’s essential to be aware of these requirements and work with a customs broker if needed to ensure smooth importation.
5. How can I manage logistics and shipping?
Chinese manufacturers often have experience with international shipping and can assist with logistics. It’s beneficial to clarify shipping terms (FOB, CIF, etc.) and work with freight forwarders to manage transportation efficiently.
6. What after-sales support can I expect?
Reputable manufacturers typically offer warranties and after-sales support. Clarify warranty terms, availability of spare parts, and technical support options before finalizing a purchase.
Navigating sourcing and manufacturing from China requires careful planning and communication, but it can offer significant benefits in terms of cost-effectiveness and product variety.
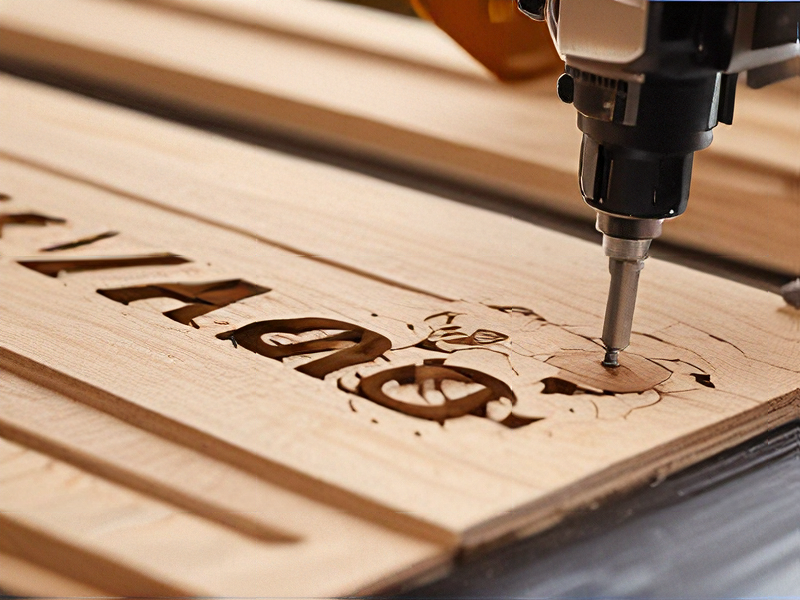