Technology and Applications of laser wood cut machine
Laser wood cutting machines leverage high-powered lasers to slice through wood with precision. These machines utilize focused laser beams, typically generated by CO2 or fiber lasers, to burn, melt, or vaporize the material along the designated paths. The technology ensures minimal wastage and high accuracy, making it a preferred method for detailed and intricate designs.
Technology
1. Laser Source: CO2 lasers are the most common for wood cutting, offering high efficiency and the ability to cut various wood types, including hardwood, softwood, and plywood.
2. Laser Control: Advanced software controls the laser’s movement and power, ensuring precision. CAD (Computer-Aided Design) software is often used to create detailed patterns and designs.
3. Motion System: High-precision motors and linear guides move the laser head accurately over the wood surface.
4. Cooling System: To prevent overheating, laser wood cutters are equipped with cooling systems, typically using water or air.
5. Exhaust System: An exhaust system is essential to remove smoke and debris generated during cutting, maintaining a clean work environment and prolonging machine life.
Applications
1. Furniture Making: Laser cutters can create complex joints and decorative elements, enhancing the aesthetic appeal and functionality of furniture.
2. Art and Craft: Artists and hobbyists use laser cutters to produce intricate designs, custom shapes, and detailed engravings on wood.
3. Signage: Laser cutting is ideal for creating precise and attractive wooden signs, logos, and lettering.
4. Prototyping: Designers and engineers use laser cutting for rapid prototyping, allowing them to quickly create and test designs.
5. Educational Tools: Schools and universities use laser cutters in STEM education for projects involving design, engineering, and technology.
Laser wood cutting machines combine precision, efficiency, and versatility, making them indispensable tools in various industries, from manufacturing and design to education and the arts.
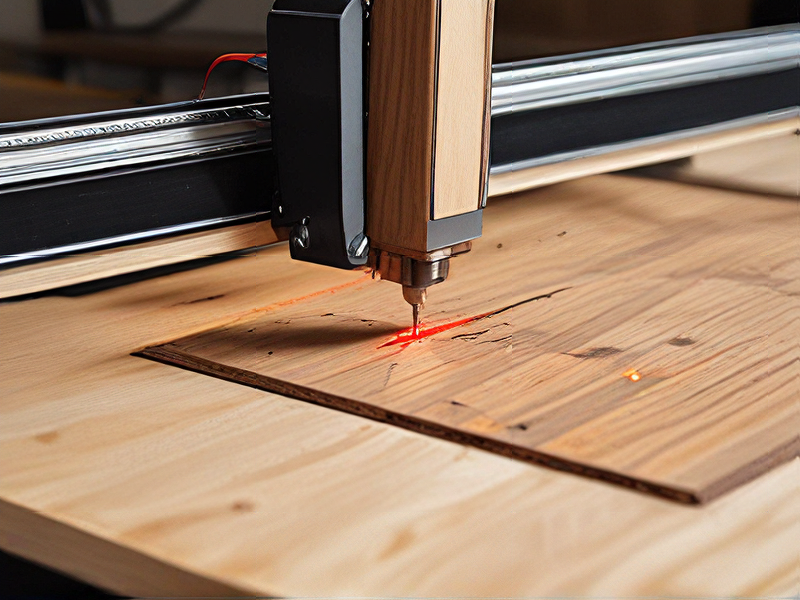
Quality Testing Methods for laser wood cut machine and how to control quality
Quality testing for laser wood cut machines involves several methods to ensure precision, consistency, and safety. Here are key methods and controls:
Quality Testing Methods:
1. Calibration: Regularly calibrate the laser machine to ensure accuracy. Use standard calibration tools and test cuts to verify precision.
2. Material Testing: Test various wood types to understand how the laser interacts with different grains and densities. This helps in adjusting settings for consistent results.
3. Dimensional Accuracy: Measure the cut pieces using calipers or micrometers to ensure they meet specified dimensions. This can be automated with vision systems for high volume production.
4. Edge Quality Inspection: Examine the edges for burns, charring, or roughness. High-quality cuts should have smooth, clean edges without discoloration.
5. Cut Depth Consistency: Verify that the laser maintains a consistent cut depth across the entire piece. Use depth gauges to check uniformity.
6. Test Cuts: Perform regular test cuts with predetermined patterns to check for any deviations or defects in the cutting process.
Quality Control Measures:
1. Routine Maintenance: Keep the machine in top condition through scheduled maintenance. Clean lenses, mirrors, and other optical components regularly to prevent degradation in performance.
2. Environment Control: Maintain an appropriate environment, controlling dust and temperature, to ensure consistent machine performance and cut quality.
3. Software Updates: Ensure the machine’s software is up-to-date to benefit from the latest optimizations and bug fixes.
4. Operator Training: Train operators thoroughly on machine handling, maintenance, and troubleshooting to prevent errors and enhance production quality.
5. Documentation and Record Keeping: Maintain detailed logs of machine settings, maintenance activities, and test results to track performance over time and identify patterns in defects or failures.
By implementing these methods and controls, manufacturers can ensure high-quality outputs from laser wood cutting machines, leading to superior products and satisfied customers.
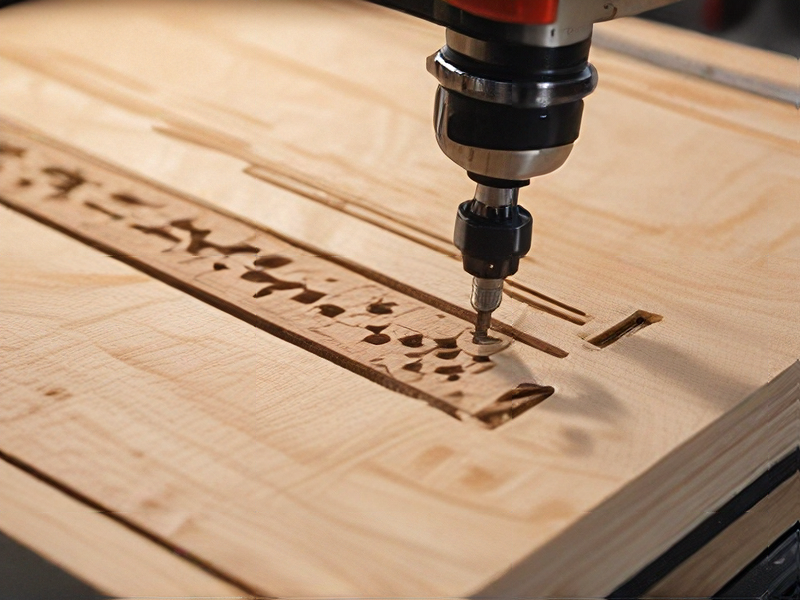
Tips for Procurement and Considerations when Purchasing from laser wood cut machine
When purchasing a laser wood cutting machine, consider the following key tips and factors:
1. Machine Specifications: Evaluate the laser power (wattage), cutting bed size, and types of materials it can process (thickness and compatibility with various woods).
2. Quality and Precision: Look for machines known for high precision and quality output, as this affects the finished product’s details and edge smoothness.
3. Ease of Use: User-friendly interfaces and software are crucial. Ensure the machine’s controls and software are intuitive and compatible with your workflow.
4. Maintenance and Support: Check availability of technical support, warranty coverage, and ease of maintenance. Reliable after-sales service is essential for minimizing downtime.
5. Safety Features: Laser machines require safety measures. Look for features like enclosed cutting areas, emergency stop buttons, and safety interlocks to protect operators.
6. Budget Considerations: Balance your budget with the machine’s capabilities and long-term reliability. Cheaper options may lack durability or precise cutting abilities.
7. Reviews and Recommendations: Research user reviews and seek recommendations from other businesses or professionals in your industry.
8. Training and Education: Ensure adequate training is provided or available. Proper training enhances efficiency and reduces the risk of accidents.
9. Scalability and Future Needs: Consider your business growth and future projects. Choose a machine that can accommodate expanding production requirements.
10. Environmental Impact: Assess the environmental footprint, such as energy efficiency and material waste, to align with sustainability goals.
By focusing on these factors, you can make an informed decision when purchasing a laser wood cutting machine that meets your specific needs and enhances your procurement process.
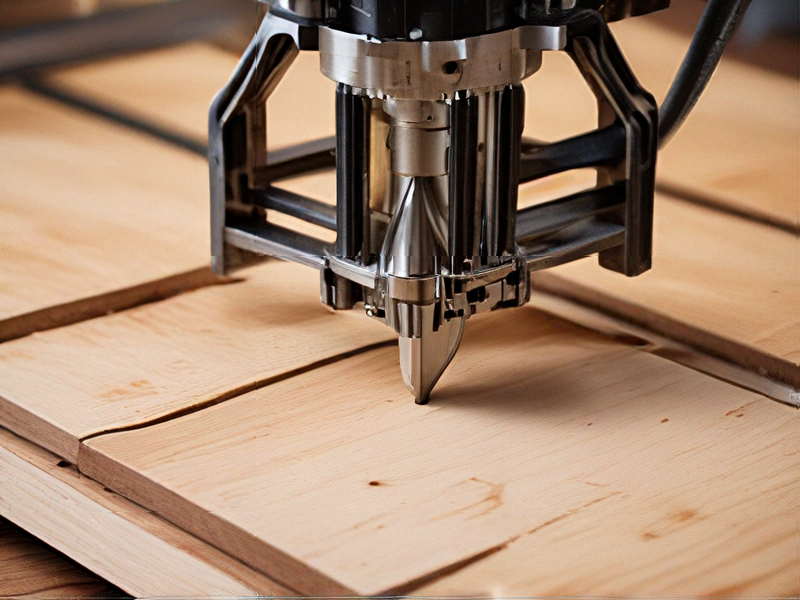
FAQs on Sourcing and Manufacturing from laser wood cut machine in China
Certainly! Here are some frequently asked questions (FAQs) regarding sourcing and manufacturing from laser wood cutting machines in China:
1. What types of wood can be effectively cut using Chinese laser machines?
Chinese laser machines are versatile and can cut a wide range of woods including plywood, MDF (Medium Density Fiberboard), hardwoods like oak and maple, and even some softer woods like pine and cedar.
2. What are the typical lead times for ordering laser cut wood products from China?
Lead times can vary based on factors like order size and customization requirements, but generally range from 2 to 6 weeks. Larger orders or complex designs may take longer.
3. What quality standards should I expect from Chinese laser cutting manufacturers?
Reputable manufacturers adhere to international quality standards like ISO 9001. It’s advisable to request samples and visit factories if possible to ensure quality meets your expectations.
4. How can I ensure intellectual property protection when sourcing from China?
Utilize contracts that clearly outline IP ownership and confidentiality agreements. Working with established manufacturers with a good reputation for IP protection is crucial.
5. What are the typical payment terms when working with Chinese manufacturers?
Payment terms often involve a deposit (typically 30%) upfront, with the balance due upon completion of production and before shipment. Negotiate terms that suit both parties to ensure a smooth transaction.
6. Can Chinese manufacturers handle custom design requirements?
Yes, many Chinese manufacturers offer customization services. Provide detailed specifications and designs, and communicate clearly to ensure your requirements are met accurately.
7. What logistics options are available for shipping laser cut wood products from China?
Manufacturers often work with international freight forwarders to arrange shipping by sea or air. Choose the option that best suits your timeline and budget.
Navigating sourcing and manufacturing from Chinese laser wood cutting machines involves clear communication, attention to quality standards, and careful management of logistics and intellectual property.
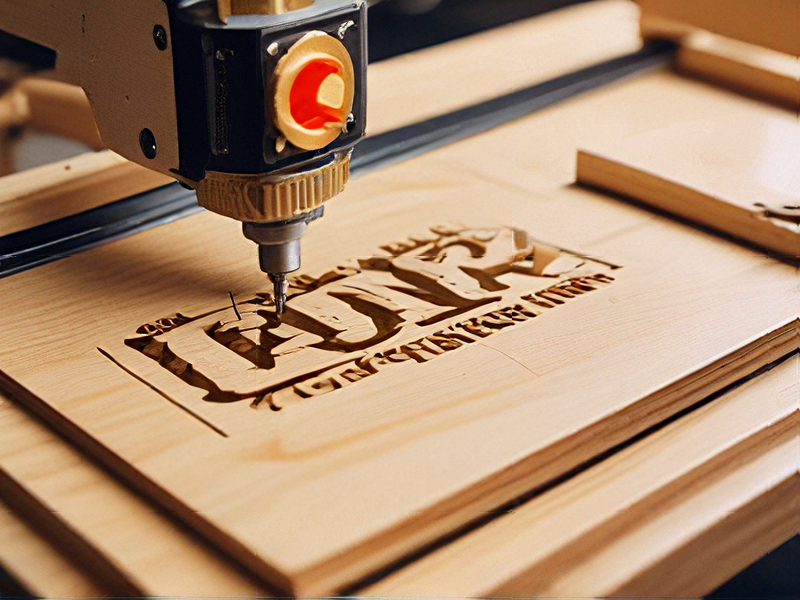