Technology and Applications of engraving on metal
Engraving on metal is a precise and versatile technique used for decorative, functional, and industrial purposes. Traditionally, engraving involves using sharp tools to carve designs into the surface of metals like steel, brass, or silver. This manual process requires skill and craftsmanship to achieve intricate details and varying depths.
Technological advancements have introduced mechanized and computer-controlled engraving methods, such as CNC (Computer Numerical Control) engraving machines. These machines use computer-aided design (CAD) software to translate digital designs into engraved patterns with high accuracy and consistency. This automation enables faster production times and the replication of complex designs across multiple pieces.
Applications of metal engraving span various industries:
1. Jewelry and Art: Engraving enhances jewelry by adding personalized inscriptions or intricate patterns. It’s also used in art for creating detailed metal prints and sculptures.
2. Identification and Branding: Engraved metal plates are crucial for product labeling, serial numbers, and branding on items like tools, equipment, and electronics.
3. Industrial Uses: In manufacturing, engraved metal molds and dies are essential for imprinting patterns on plastics, ceramics, and other materials.
4. Security and Authentication: Engraving is used for creating secure marks on metals to prevent counterfeiting and ensure authenticity, such as on currency, certificates, and valuable items.
5. Medical and Aerospace: In these industries, metal engraving is employed for marking surgical instruments, aerospace components, and critical parts with serial numbers, specifications, and safety information.
Advancements in laser technology have also revolutionized metal engraving, offering precision, speed, and versatility in creating designs on a wide range of metals. Whether for decorative purposes or functional requirements, metal engraving continues to evolve, combining traditional craftsmanship with modern technology to meet diverse industrial and artistic needs.
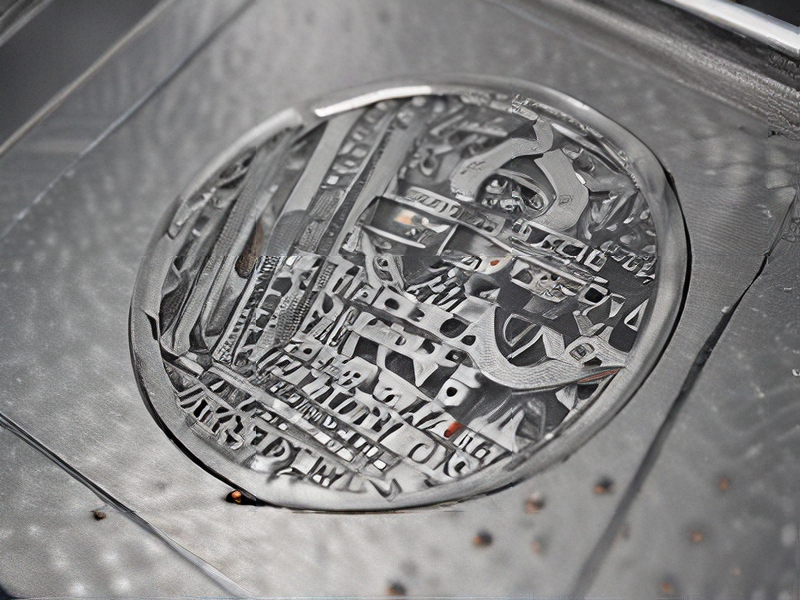
Quality Testing Methods for engraving on metal and how to control quality
Quality testing methods for engraving on metal typically involve both visual inspection and metrological techniques:
1. Visual Inspection: A trained operator visually inspects the engraved surface for clarity, depth consistency, and any defects like burrs or irregularities. This method is subjective but essential for initial assessment.
2. Metrological Techniques:
– Depth Measurement: Instruments like depth micrometers or digital height gauges measure the depth of engraving at multiple points to ensure consistency.
– Profile Measurement: Laser profilometers or coordinate measuring machines (CMMs) verify the engraved profile against design specifications.
– Surface Roughness: Roughness testers assess the texture of the engraved surface to ensure it meets required standards.
3. Control Strategies:
– Statistical Process Control (SPC): Regularly sampling and measuring engraved parts to detect variations early and maintain consistency.
– Quality Gates: Implementing checkpoints in the production process where engraving quality is verified before proceeding to the next stage.
– Training and Documentation: Ensuring operators are trained to recognize quality criteria and maintaining clear documentation of standards and procedures.
By combining visual inspection with precise metrological measurements and robust control strategies, manufacturers can effectively ensure high-quality engraving on metal parts.
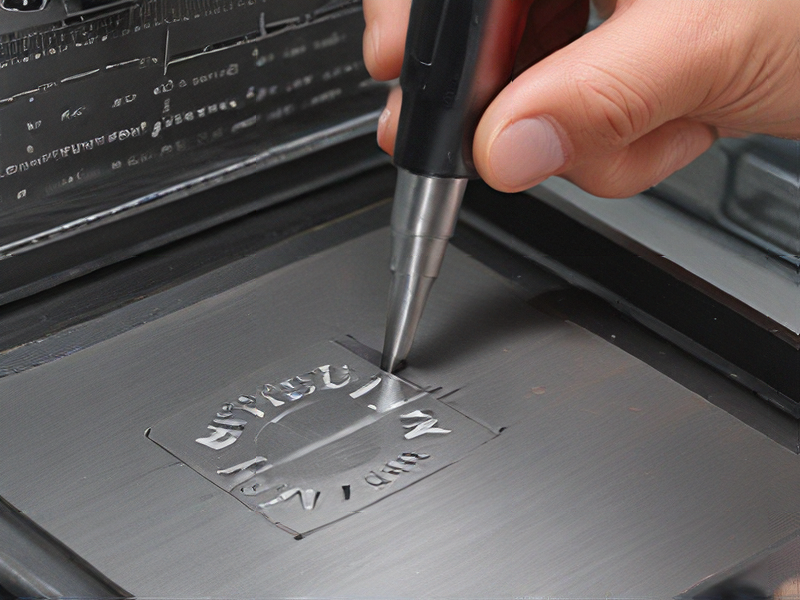
Tips for Procurement and Considerations when Purchasing from engraving on metal
Tips for Procurement and Considerations when Purchasing Metal Engraving Services
1. Material Selection:
– Choose the appropriate metal (e.g., aluminum, brass, stainless steel) based on durability, aesthetics, and application.
– Verify the metal’s thickness and grade to ensure it meets the project’s specifications.
2. Engraving Method:
– Laser engraving is precise and suitable for intricate designs, while mechanical engraving is ideal for deeper marks.
– Consider the final appearance; laser engraving offers cleaner lines, whereas mechanical engraving can provide a more tactile finish.
3. Design Specifications:
– Provide detailed and clear design files (preferably in vector formats like .AI or .SVG) to avoid misinterpretation.
– Ensure the design takes into account the limitations of the engraving process, such as minimum line thickness and spacing.
4. Supplier Expertise:
– Select a supplier with experience in the specific type of engraving required.
– Request samples of previous work to assess the quality and precision of their engraving.
5. Cost Considerations:
– Obtain multiple quotes to compare pricing but be wary of significantly lower prices which may compromise quality.
– Factor in additional costs such as setup fees, especially for custom designs or small production runs.
6. Quality Assurance:
– Specify quality control measures, such as inspection of engraved samples before full production.
– Ensure the supplier follows industry standards and can provide certifications if needed.
7. Turnaround Time:
– Discuss and confirm the lead time, especially for large orders or projects with tight deadlines.
– Account for possible delays in the procurement timeline.
8. Environmental Impact:
– Consider suppliers who use eco-friendly practices and materials.
– Evaluate the recycling options for the engraved metal products.
9. After-Sales Support:
– Check the warranty and after-sales service policy.
– Ensure the supplier offers support for any issues that may arise post-purchase.
10. Logistics and Delivery:
– Confirm the delivery options and associated costs.
– Ensure the packaging is robust to prevent damage during transit.
Following these tips will help ensure a successful procurement process and a high-quality outcome for metal engraving projects.
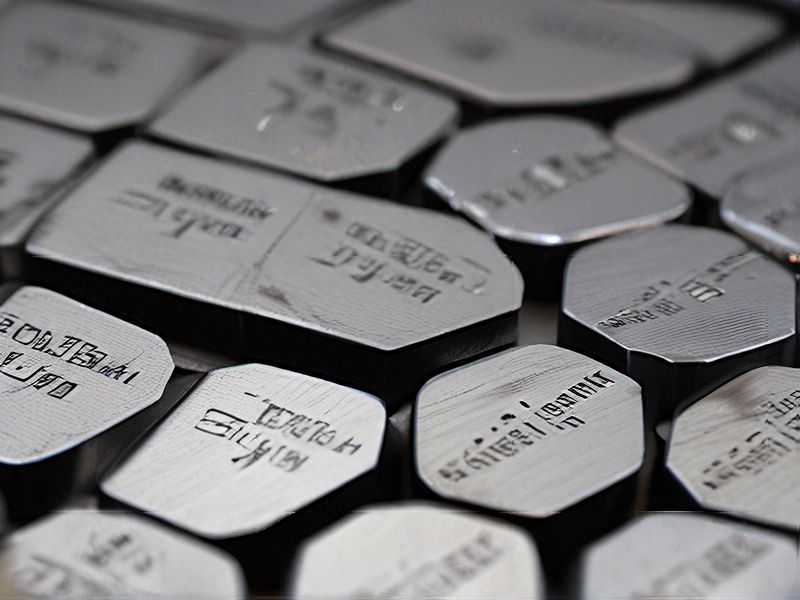
FAQs on Sourcing and Manufacturing from engraving on metal in China
When sourcing and manufacturing engraving on metal in China, several common questions arise:
1. How do I find reliable suppliers for metal engraving in China?
Start by researching online directories like Alibaba or Made-in-China. Look for suppliers with a proven track record, positive reviews, and verified certifications. It’s crucial to visit potential suppliers, conduct background checks, and inspect their facilities to ensure they meet your standards.
2. What are the typical costs associated with metal engraving in China?
Costs can vary based on factors such as the complexity of the engraving, type of metal, and order quantity. Generally, Chinese suppliers offer competitive pricing due to lower labor costs. Obtain detailed quotes including setup fees, per-piece costs, and any additional charges for custom designs.
3. How can I ensure quality when manufacturing metal engraving in China?
Quality control is essential. Specify your quality requirements in detail, including material specifications, engraving precision, and finishing standards. Implement inspections during production and before shipment. Consider hiring a third-party inspection service to verify quality and adherence to your standards.
4. What are the typical lead times for metal engraving production?
Lead times vary depending on the complexity of the engraving and supplier capacity. Discuss timelines with your supplier upfront and factor in buffer time for unforeseen delays. Communicate clearly and regularly to ensure production stays on schedule.
5. What are the shipping and import considerations when importing metal engraving from China?
Understand shipping options (air, sea, express) and associated costs. Familiarize yourself with import regulations, tariffs, and taxes in your country. Work closely with a freight forwarder to manage logistics and customs clearance efficiently.
By addressing these FAQs, you can navigate sourcing and manufacturing metal engraving in China effectively, ensuring quality, cost-efficiency, and timely delivery of your products.
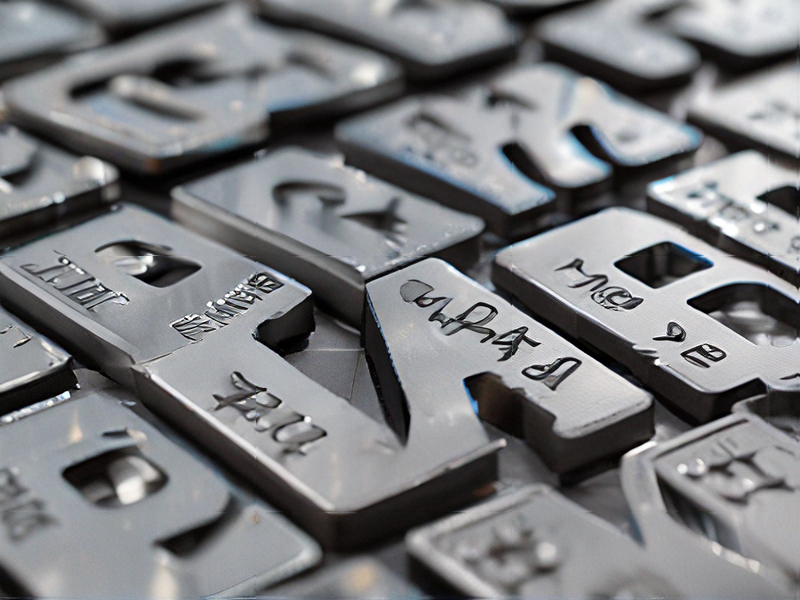