Technology and Applications of metal fabrication custom
Metal fabrication is a critical process in various industries, involving the creation of metal structures and components by cutting, bending, and assembling. The technology employed in metal fabrication has advanced significantly, integrating both traditional methods and modern techniques.
Key technologies include CNC (Computer Numerical Control) machining, which allows for high precision in cutting and shaping metals. Laser cutting has gained popularity for its ability to create intricate designs with minimal material waste. Additionally, plasma cutting and water jet cutting are valuable for their versatility and ability to cut various materials with precision.
Welding technologies have evolved to include MIG (Metal Inert Gas), TIG (Tungsten Inert Gas), and robotic welding systems, enhancing efficiency, consistency, and safety in joining metal parts. Additive manufacturing, or 3D printing of metals, is also emerging as a game-changer, enabling rapid prototyping and the creation of complex geometries that are difficult to achieve with traditional methods.
Custom metal fabrication is essential across numerous applications, including automotive, aerospace, construction, and consumer products. Tailored solutions are crucial for producing components that meet specific design requirements, performance standards, and regulatory compliance.
The trend towards sustainability has led to innovations in recycling scrap metal and utilizing eco-friendly processes, reducing the environmental impact of fabrication practices. Moreover, the integration of automation and IoT (Internet of Things) in metal fabrication enhances productivity and allows for real-time monitoring and quality control.
As industries continue to evolve, the demand for customized metal fabrication solutions will grow, driving advancements in technology and application to meet diverse and complex needs.
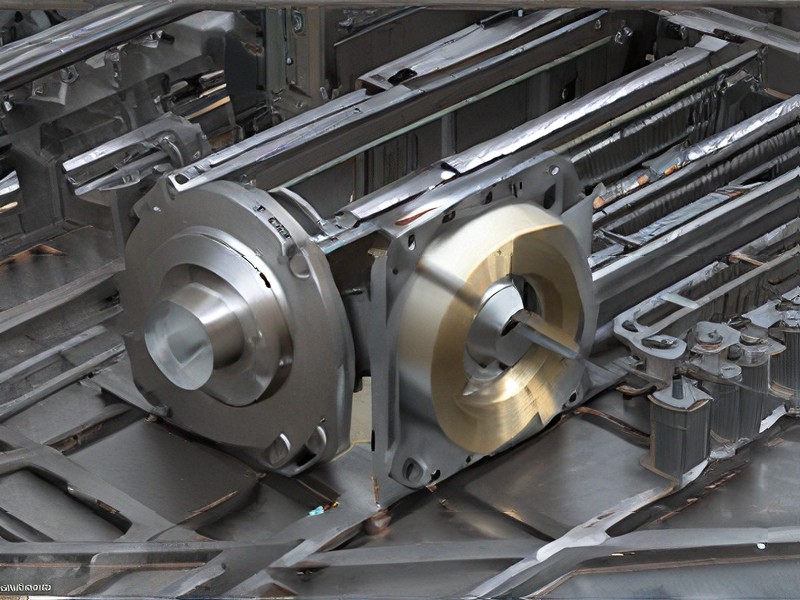
Quality Testing Methods for metal fabrication custom and how to control quality
Quality testing methods for metal fabrication custom processes are essential to ensure that the final products meet the desired specifications and performance standards. Key methods include:
1. Visual Inspection: The simplest and most immediate method. It involves checking for surface defects like scratches, dents, and weld quality. Inspectors use tools such as magnifying glasses and borescopes to examine intricate details.
2. Dimensional Inspection: Ensures the fabricated components meet specified dimensions. Tools such as calipers, micrometers, and coordinate measuring machines (CMM) are used to verify measurements against design specifications.
3. Non-Destructive Testing (NDT):
– Ultrasonic Testing (UT): Uses high-frequency sound waves to detect internal flaws.
– Magnetic Particle Testing (MPT): Detects surface and near-surface discontinuities in ferromagnetic materials.
– Radiographic Testing (RT): X-rays or gamma rays are used to view the internal structure.
– Dye Penetrant Testing (DPT): Liquid penetrant is applied to the surface to reveal cracks.
4. Destructive Testing:
– Tensile Testing: Measures the material’s strength by pulling it until it breaks.
– Hardness Testing: Determines the material’s resistance to deformation.
– Impact Testing: Assesses the material’s toughness under sudden force.
5. Metallurgical Analysis: Examines the microstructure of metals using microscopes to ensure the correct composition and treatment processes.
Quality Control Strategies
1. Standard Operating Procedures (SOPs): Clearly documented processes to ensure consistent quality.
2. Regular Training: Ensuring staff are proficient with the latest techniques and technologies.
3. In-Process Inspections: Regular checks during the fabrication process to catch defects early.
4. Statistical Process Control (SPC): Monitoring production metrics to detect variations that may indicate quality issues.
5. Quality Audits: Routine inspections and audits to ensure compliance with standards and specifications.
Implementing these testing methods and quality control strategies helps ensure that custom metal fabrication projects meet the required standards and customer expectations.
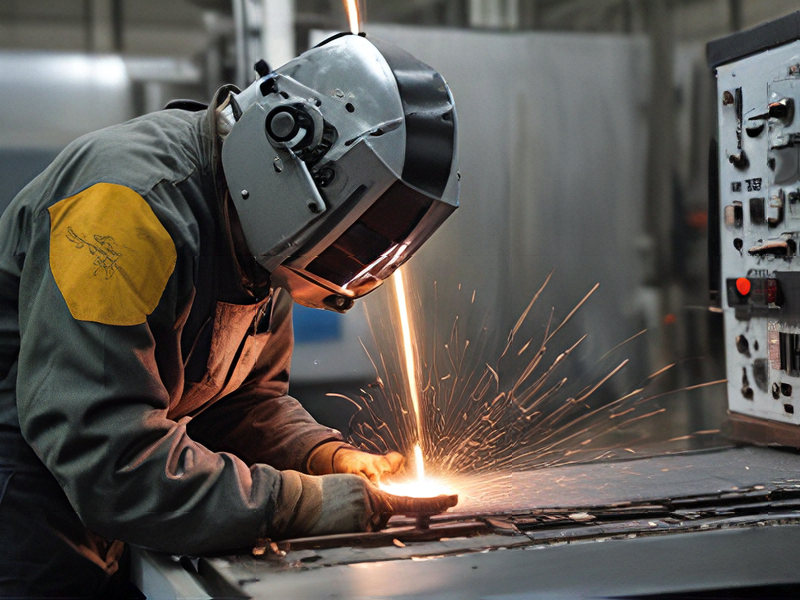
Tips for Procurement and Considerations when Purchasing from metal fabrication custom
When engaging in procurement for custom metal fabrication, several key considerations can ensure a successful partnership and optimal results:
1. Define Requirements Clearly: Begin by specifying your needs in detail, including dimensions, materials, finishes, and tolerances. Clear requirements prevent misunderstandings and ensure the fabricator can meet your expectations.
2. Select the Right Fabricator: Choose a fabricator with relevant experience, capabilities, and certifications. Assess their past projects and client testimonials. A fabricator familiar with your industry’s standards can be more efficient and effective.
3. Material Quality: Ensure the fabricator uses high-quality materials that meet your specifications. Verify the material certifications and traceability to avoid issues with performance and durability.
4. Prototyping and Testing: Request prototypes to validate design and functionality before full-scale production. Prototyping helps identify potential issues early, saving time and costs in the long run.
5. Lead Times and Capacity: Discuss lead times and the fabricator’s capacity to handle your order within your timeline. Confirm their ability to scale production if needed.
6. Cost Considerations: While cost is important, it shouldn’t be the sole factor. Compare quotes, but also consider the fabricator’s quality, reliability, and service. Sometimes, a higher initial cost can lead to long-term savings through superior quality and fewer defects.
7. Communication and Collaboration: Maintain open and frequent communication with the fabricator. A collaborative approach can help address issues promptly and ensure the project stays on track.
8. Compliance and Standards: Ensure the fabricator adheres to relevant industry standards and regulations. This is crucial for safety, quality, and legal compliance.
9. After-Sales Support: Consider the level of after-sales support and services offered by the fabricator. Reliable support can be critical for addressing any post-delivery issues.
10. Sustainability: Evaluate the fabricator’s commitment to sustainable practices, such as recycling and efficient resource use, which can contribute to your own sustainability goals.
By carefully considering these factors, you can select a metal fabrication partner that delivers quality products, meets deadlines, and aligns with your strategic objectives.
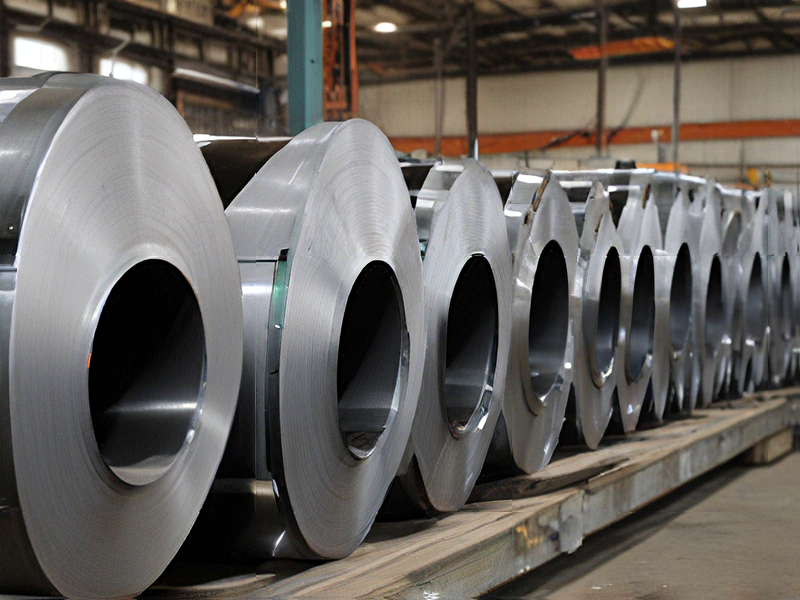
FAQs on Sourcing and Manufacturing from metal fabrication custom in China
FAQs on Sourcing and Manufacturing Custom Metal Fabrication in China
1. Why choose China for metal fabrication?
China is renowned for its cost-effective manufacturing capabilities, skilled labor force, advanced technology, and extensive experience in metal fabrication. This results in competitive pricing and high-quality products.
2. How do I find a reliable metal fabrication supplier in China?
Research online directories, industry trade shows, and recommendations. Verify potential suppliers by checking certifications, visiting their facilities, and requesting samples.
3. What types of metal fabrication services are available?
Chinese suppliers offer a wide range of services, including cutting, bending, welding, stamping, CNC machining, and surface treatments like powder coating and anodizing.
4. What is the typical lead time for custom metal fabrication orders?
Lead times vary based on project complexity, order volume, and supplier workload. Generally, expect 4-8 weeks from order confirmation to delivery.
5. How do I ensure product quality?
Establish clear specifications and quality standards. Request samples before mass production and consider third-party inspections during and after production.
6. What are the payment terms?
Common payment terms include a 30% deposit upfront and 70% balance before shipment. Some suppliers may offer different terms based on relationships and order sizes.
7. How do I handle shipping and logistics?
Suppliers can assist with shipping arrangements. Options include sea freight for cost savings and air freight for faster delivery. Ensure proper documentation to avoid customs issues.
8. What are the key considerations for intellectual property protection?
Use non-disclosure agreements (NDAs) and choose suppliers with a good reputation. Register your designs and trademarks in China to safeguard your IP.
9. Can I communicate effectively with Chinese suppliers?
Most suppliers have English-speaking staff. Use clear, concise communication and consider using a sourcing agent if language barriers are a concern.
10. What should I expect regarding pricing?
Prices depend on material costs, labor, and complexity of the project. Obtain multiple quotes to ensure competitive pricing and understand what is included in the cost.
By addressing these FAQs, businesses can navigate the process of sourcing and manufacturing custom metal fabrication in China more effectively.
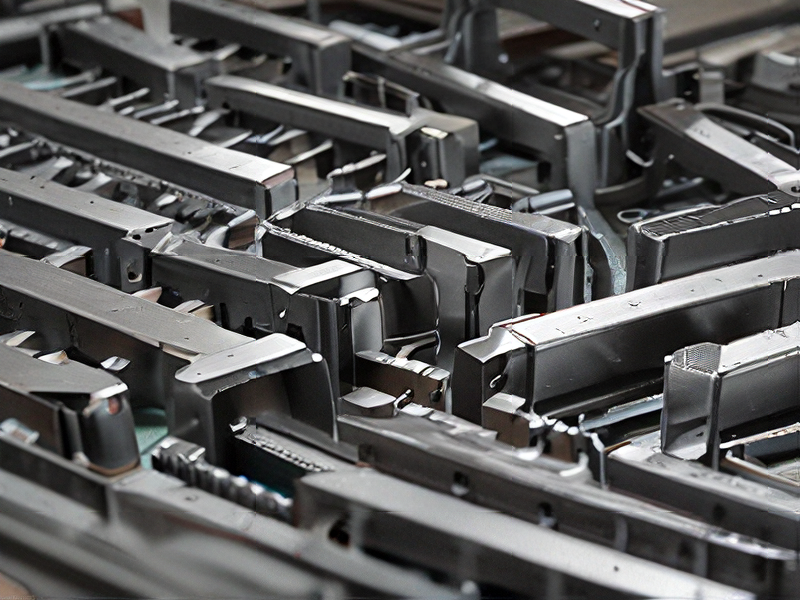