Technology and Applications of custom metal manufacturing
Custom metal manufacturing encompasses a range of technologies and applications aimed at producing specialized metal parts and components tailored to specific needs. The primary technologies include:
1. CNC Machining: This involves computer-controlled machines that precisely cut, mill, and shape metal components from raw material blocks. CNC machining is widely used in industries like aerospace, automotive, and medical devices for its accuracy and repeatability.
2. Additive Manufacturing: Also known as 3D printing, this technology builds metal parts layer by layer from powder or wire feedstock. It is particularly useful for creating complex geometries that are difficult to achieve with traditional methods. Applications include custom prosthetics, aerospace components, and intricate tooling.
3. Laser Cutting and Welding: Laser technology is used to cut metal sheets with high precision and to weld components together. It is essential in industries requiring intricate designs and strong joints, such as automotive, electronics, and heavy machinery.
4. Metal Casting: This process involves pouring molten metal into a mold to produce parts with complex shapes. Custom casting is used in applications like engine components, machinery parts, and architectural elements.
5. Sheet Metal Fabrication: Techniques like bending, stamping, and forming are used to create metal enclosures, panels, and chassis. This is crucial for the construction, electronics, and appliance industries.
Applications of custom metal manufacturing are vast and diverse. In the aerospace industry, it enables the creation of lightweight, durable components essential for aircraft and spacecraft. Automotive manufacturers use custom metal parts for engines, transmissions, and body components to enhance performance and efficiency. The medical sector benefits from precision-engineered surgical instruments and implants, while electronics and telecommunications rely on metal enclosures and heat sinks for device protection and cooling.
In summary, custom metal manufacturing integrates advanced technologies to produce tailored metal parts for critical applications across multiple industries, driving innovation and enhancing product performance.
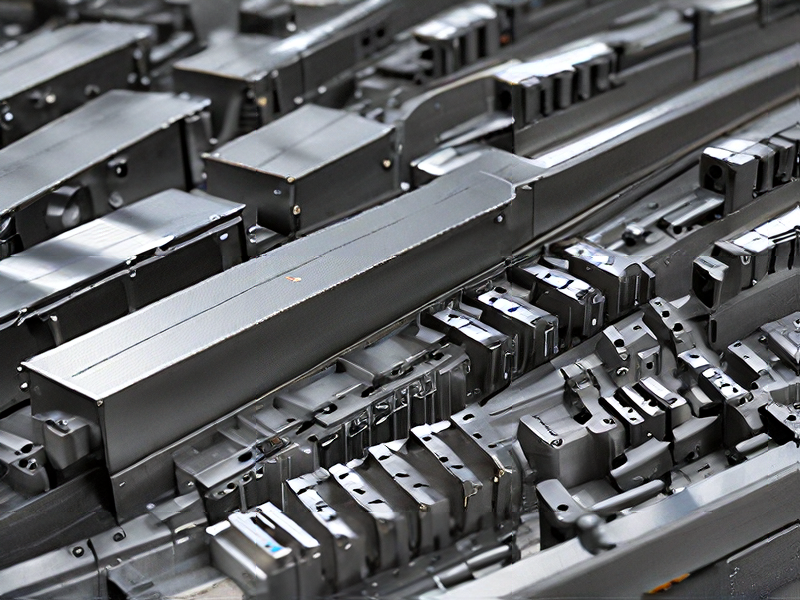
Quality Testing Methods for custom metal manufacturing and how to control quality
Quality testing in custom metal manufacturing is crucial for ensuring product reliability, safety, and compliance with specifications. Here are some key methods and control measures:
Quality Testing Methods:
1. Visual Inspection:
– Purpose: Detect surface defects, such as cracks, pits, and discolorations.
– Tools: Magnifying glasses, microscopes, and surface comparators.
2. Dimensional Inspection:
– Purpose: Ensure parts meet precise dimensional specifications.
– Tools: Calipers, micrometers, and coordinate measuring machines (CMMs).
3. Non-Destructive Testing (NDT):
– Ultrasonic Testing: Uses high-frequency sound waves to detect internal flaws.
– Radiographic Testing: Uses X-rays or gamma rays to view the internal structure.
– Magnetic Particle Testing: Detects surface and near-surface discontinuities in ferromagnetic materials.
– Dye Penetrant Testing: Reveals surface cracks by using a dye that seeps into defects.
4. Mechanical Testing:
– Tensile Testing: Measures the force required to pull something to the point of failure.
– Hardness Testing: Determines the hardness of a material by measuring its resistance to deformation.
5. Chemical Analysis:
– Purpose: Verify the material composition.
– Tools: Spectrometers and chemical analysis kits.
Quality Control Measures:
1. Process Control:
– Implement Statistical Process Control (SPC) to monitor and control production processes.
– Use control charts to track process variations and maintain process stability.
2. Standard Operating Procedures (SOPs):
– Develop and adhere to SOPs to ensure consistent manufacturing practices.
3. Supplier Quality Management:
– Qualify and regularly audit suppliers to ensure they meet quality standards.
4. Training and Certification:
– Train and certify employees in quality control and testing procedures.
5. Documentation and Traceability:
– Maintain detailed records of all inspections, tests, and process controls to ensure traceability and accountability.
6. Corrective and Preventive Actions (CAPA):
– Implement CAPA systems to address and prevent recurring quality issues.
By integrating these testing methods and quality control measures, custom metal manufacturers can ensure their products meet the required standards and specifications.

Tips for Procurement and Considerations when Purchasing from custom metal manufacturing
When purchasing from custom metal manufacturing, consider these essential tips:
1. Define Your Requirements: Clearly outline your specifications, including material type, dimensions, tolerances, and any specific certifications or standards required.
2. Supplier Selection: Research potential suppliers thoroughly. Look for experience in similar projects, quality certifications (ISO, AS9100, etc.), and check customer reviews or testimonials.
3. Quality Assurance: Ensure the supplier has robust quality control measures in place. Request documentation such as inspection reports, material certificates, and process validations.
4. Communication: Maintain open and clear communication throughout the project. Discuss milestones, timelines, and any potential challenges upfront.
5. Cost and Value: Evaluate quotes not just based on price but also on the overall value, including quality, lead times, and supplier reliability.
6. Flexibility and Capacity: Assess the supplier’s flexibility to accommodate changes or custom requirements. Verify their production capacity to meet your volume and timeline needs.
7. Prototyping and Samples: If feasible, request prototypes or samples to validate quality and suitability before full-scale production.
8. Contract and Terms: Have a detailed contract that outlines deliverables, timelines, payment terms, and contingencies for delays or quality issues.
9. Sustainability and Ethics: Consider the supplier’s commitment to sustainability and ethical practices, especially if these factors are important to your organization.
10. Post-Production Support: Clarify what post-production support the supplier offers, such as warranty, maintenance, or ongoing part availability.
By focusing on these considerations, you can streamline the procurement process and ensure successful outcomes when purchasing from custom metal manufacturing suppliers.
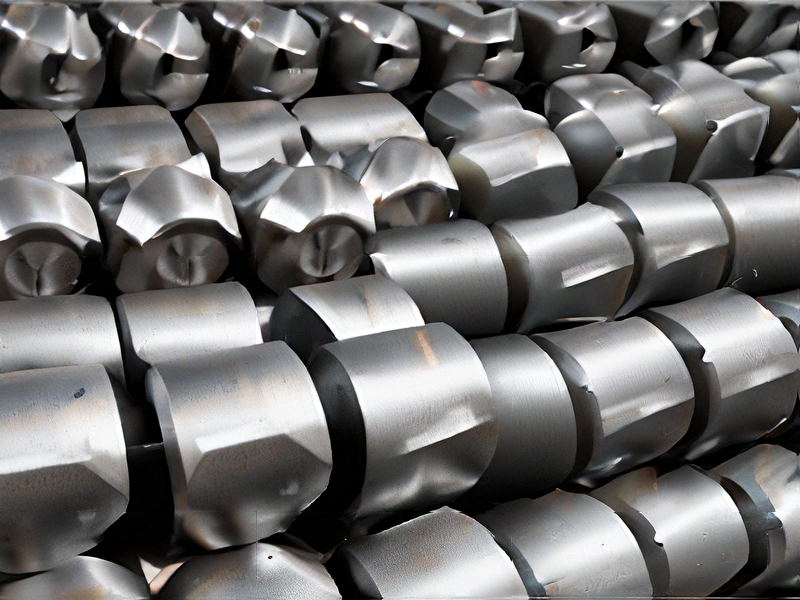
FAQs on Sourcing and Manufacturing from custom metal manufacturing in China
FAQs on Sourcing and Manufacturing from Custom Metal Manufacturing in China
1. Why should I consider sourcing metal products from China?
China offers competitive pricing, a wide range of manufacturing capabilities, and an extensive network of suppliers. The country’s well-established infrastructure and expertise in metal manufacturing ensure high-quality products and efficient production processes.
2. What types of metal products can be manufactured in China?
China specializes in a variety of metal products including castings, forgings, machining parts, sheet metal, stamped parts, and fabricated assemblies. Both ferrous and non-ferrous metals are available.
3. How do I find a reliable metal manufacturer in China?
Research thoroughly, leveraging online platforms, trade shows, and sourcing agents. Look for manufacturers with relevant certifications, positive customer reviews, and a track record of producing similar products to your specifications.
4. What quality control measures should I take?
Implement strict quality control measures such as pre-production samples, in-process inspections, and final product inspections. Consider hiring third-party inspection agencies to ensure compliance with your standards.
5. How can I ensure my intellectual property is protected?
Sign non-disclosure agreements (NDAs) and ensure that all legal agreements clearly state intellectual property (IP) protections. Work with legal professionals familiar with Chinese IP laws to safeguard your designs and patents.
6. What is the typical lead time for manufacturing metal products in China?
Lead times vary depending on the complexity and volume of the order. Generally, lead times range from 4 to 12 weeks, including production and shipping.
7. What are the payment terms for Chinese manufacturers?
Common payment terms include a 30% deposit upfront with the balance paid before shipment or upon receipt of goods. Letter of Credit (LC) and Telegraphic Transfer (T/T) are widely used payment methods.
8. How can I manage logistics and shipping?
Work with experienced freight forwarders to handle logistics and shipping. They can assist with customs clearance, documentation, and choosing the best shipping method to balance cost and delivery time.
9. What are the risks involved in sourcing from China?
Potential risks include communication barriers, quality inconsistencies, and longer lead times. Mitigate these risks through thorough research, clear communication, and rigorous quality control processes.
10. How do I handle potential cultural differences in business practices?
Respect cultural differences by understanding common business etiquette in China. Build strong relationships through clear communication, regular visits, and developing trust with your manufacturing partners.
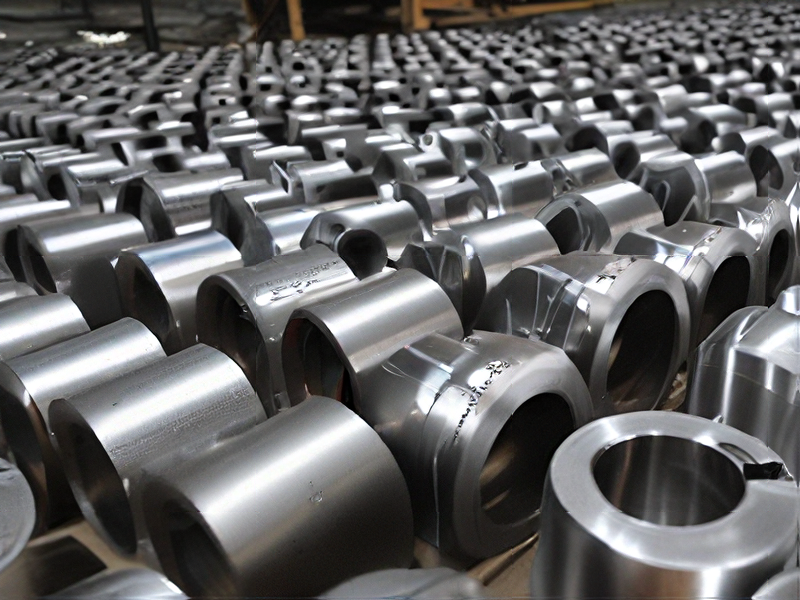