Technology and Applications of aluminum metal density
Aluminum is a versatile metal known for its low density, approximately 2.7 grams per cubic centimeter, which is about one-third that of steel. This property, along with its high strength-to-weight ratio, makes it valuable in various applications.
Applications of Aluminum
1. Aerospace Industry: Aluminum’s lightweight nature is critical in aircraft and spacecraft manufacturing. It reduces the overall weight, thereby improving fuel efficiency and performance.
2. Automotive Sector: The automotive industry uses aluminum for vehicle frames, engines, and other components to enhance fuel economy and reduce emissions. Its corrosion resistance also extends vehicle lifespan.
3. Construction: In construction, aluminum is used for window frames, roofing, and cladding due to its durability, resistance to corrosion, and aesthetic appeal.
4. Packaging: Aluminum’s non-toxicity and recyclability make it ideal for food and beverage packaging, including cans and foil.
5. Electrical Applications: Aluminum is used in electrical transmission lines due to its excellent conductivity and lower cost compared to copper.
6. Consumer Electronics: Aluminum is used in the production of smartphones, laptops, and other electronics for its lightweight and heat-conductive properties.
Technological Aspects
– Alloying: Aluminum is often alloyed with other metals like copper, magnesium, and silicon to enhance its mechanical properties for specific applications.
– Surface Treatments: Anodizing and other surface treatments improve corrosion resistance and aesthetic qualities.
– Recycling: Aluminum is highly recyclable, retaining its properties through multiple cycles, which is crucial for sustainable manufacturing practices.
Aluminum’s unique combination of low density, strength, and versatility continues to drive its widespread use across industries, supported by ongoing advancements in alloying, surface treatments, and recycling technologies.
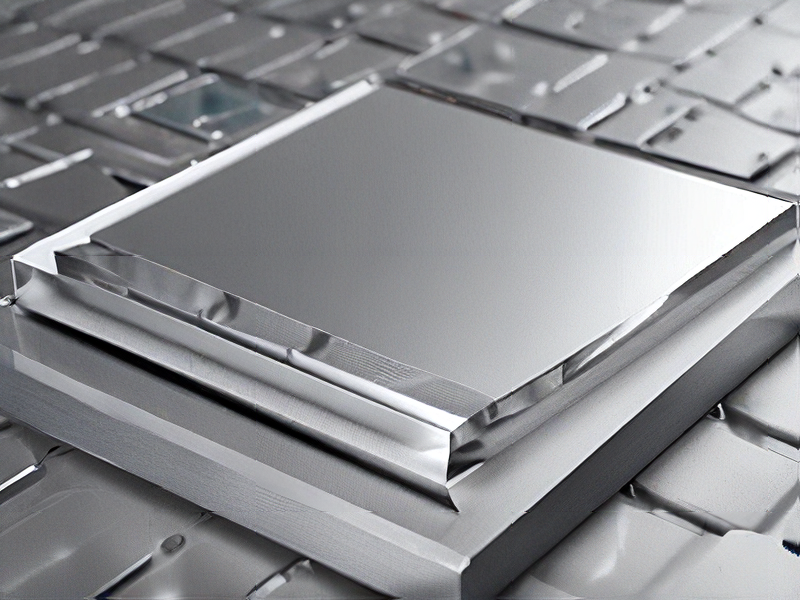
Quality Testing Methods for aluminum metal density and how to control quality
Quality testing of aluminum density is crucial to ensure material performance in various applications. Here are several methods and quality control measures:
Testing Methods:
1. Archimedes’ Principle (Water Displacement):
– Weigh a dry aluminum sample to determine its mass.
– Submerge it in water to measure the volume of water displaced.
– Calculate density using the formula: Density = Mass/Volume.
2. Hydrostatic Weighing:
– Similar to Archimedes’ method but uses a hydrostatic balance for more precision.
– This method eliminates external factors such as buoyancy.
3. X-ray Fluorescence (XRF):
– While primarily used for compositional analysis, it can help infer density based on alloy composition.
4. Ultrasonic Testing:
– Utilizes high-frequency sound waves to assess the material’s density. Variations in sound speed correlate with density variations.
5. Computed Tomography (CT):
– 3D imaging can be employed to detect internal defects that might affect density, and density can be calculated from the volume displayed.
Quality Control Measures:
1. Supplier Certification:
– Ensure all aluminum sourced comes with certifications detailing its density and composition.
2. Routine Testing:
– Implement regular testing of incoming materials and finished products to monitor density.
3. Calibration of Equipment:
– Regularly calibrate testing instruments to ensure accuracy in density measurements.
4. Standardized Procedures:
– Adhere to standardized testing protocols (ASTM or ISO standards) to maintain consistency across tests.
5. Documentation and Traceability:
– Maintain thorough records of testing results and procedures to trace any issues back to their source.
By employing these methods and control measures, manufacturers can ensure the quality and reliability of aluminum materials in their applications.
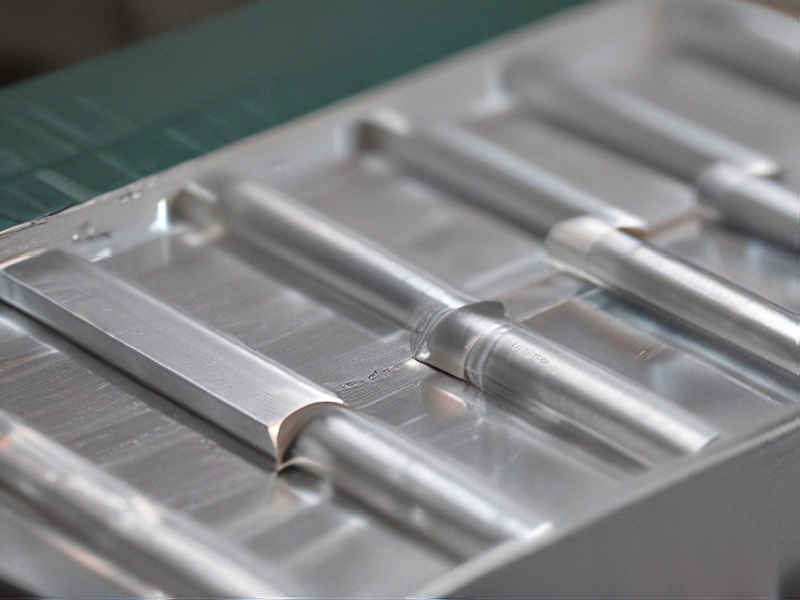
Tips for Procurement and Considerations when Purchasing from aluminum metal density
When procuring aluminum, there are several key considerations to keep in mind to ensure optimal purchase decisions:
1. Material Specifications: Understand the specific grade of aluminum needed for your application. Common grades include 6061 (structural), 7075 (aerospace), and 1050 (electric applications). Each has different properties, including strength, corrosion resistance, and machinability.
2. Density and Weight: Aluminum has a density of about 2.7 g/cm³, making it lightweight yet strong. It’s essential to consider weight in your designs, especially in industries like aerospace and automotive where reducing mass enhances efficiency.
3. Supplier Reliability: Choose reputable suppliers with a track record of providing high-quality materials. Verify their certifications and adherence to industry standards (e.g., ISO, ASTM) to ensure compliance with specifications.
4. Cost Analysis: Evaluate total cost, including material price, transport, and any additional processing needed. Sometimes a cheaper material can lead to higher long-term costs due to lower performance or durability.
5. Lead Times and Availability: Ensure your suppliers can meet your timeline and have sufficient stock. Long lead times can hinder project timelines, so reliable sources are crucial.
6. Recycling and Sustainability: Aluminum is highly recyclable, making it an eco-friendly choice. Consider sourcing from suppliers that offer recycled options which also may reduce costs.
7. Technical Support: A good supplier should provide technical support, including material recommendations and processing advice. This can be invaluable in selecting the right material for your specific application.
By considering these factors, you’ll be better equipped to make informed procurement decisions when purchasing aluminum.
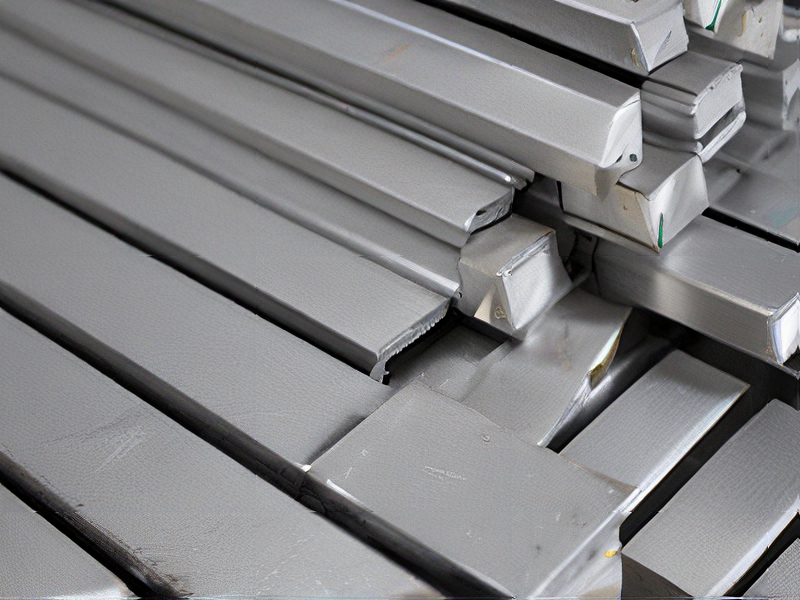
FAQs on Sourcing and Manufacturing from aluminum metal density in China
FAQs on Sourcing and Manufacturing Aluminum in China
1. What is the density of aluminum?
The density of aluminum is approximately 2.7 g/cm³, making it lightweight yet strong, ideal for various manufacturing applications.
2. Why source aluminum from China?
China is a leading producer of aluminum, offering competitive prices, vast manufacturing capabilities, and a well-established supply chain.
3. What are the common types of aluminum alloys used in manufacturing?
Common alloys include 6061 (general-purpose), 7075 (high strength), and 3003 (good corrosion resistance). The choice depends on specific application requirements.
4. How can I ensure quality when sourcing aluminum?
Collaborate with suppliers who adhere to international standards, conduct quality control inspections, and request certifications (e.g., ISO 9001).
5. What are the lead times for aluminum manufacturing in China?
Lead times vary by order size and complexity. Generally, expect 3-6 weeks for production, plus additional time for shipping.
6. What are the shipping options for aluminum products?
Common shipping methods include air freight (faster but more expensive) and sea freight (cheaper but slower). Choose based on urgency and budget.
7. Are there any trade regulations to consider?
Be mindful of tariffs and trade regulations depending on your country’s relationship with China. Consult with a customs broker for specific guidance.
8. How can I find reliable aluminum suppliers in China?
Utilize platforms like Alibaba, Trade Assurance, and local trade shows. Verify suppliers through reviews, references, and factory visits if possible.
9. What sustainability practices should I look for?
Look for suppliers using energy-efficient processes and recycling practices, as the aluminum industry is increasingly focused on sustainability.
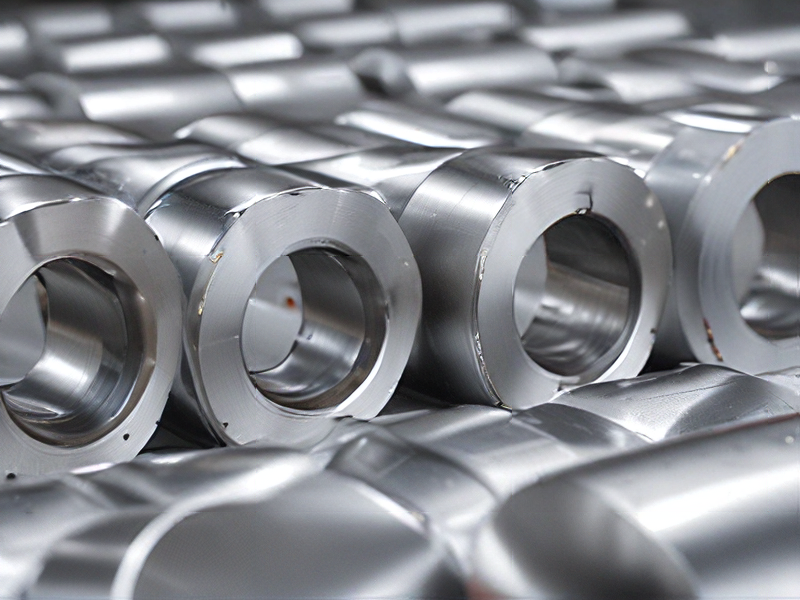