Technology and Applications of boring in machining
Boring is a machining process that enlarges and improves the accuracy of an existing hole. It is commonly employed in various industries to create precise and smooth holes in materials like metals and plastics. Here are the key technologies and applications:
Technologies
1. Boring Machines: These include vertical and horizontal boring mills, which are used based on the orientation and size of the workpiece. Horizontal boring mills are suitable for larger and heavier workpieces, while vertical mills are used for smaller, more intricate tasks.
2. Boring Bars and Tools: These tools are inserted into the existing hole to perform the boring operation. They come in various designs, such as single-point, multi-point, and adjustable boring heads, to cater to different requirements.
3. Computer Numerical Control (CNC): CNC technology enhances boring by providing precise control over the cutting tools’ movement, ensuring high accuracy and repeatability. CNC boring machines are essential for complex and high-precision tasks.
4. Tooling Materials: Advanced materials like carbide, high-speed steel (HSS), and cubic boron nitride (CBN) are used to manufacture boring tools, providing durability and resistance to wear.
Applications
1. Automotive Industry: Boring is crucial in manufacturing engine blocks, cylinders, and other components requiring precise hole dimensions and smooth finishes.
2. Aerospace Industry: Used for creating holes in critical components such as turbine blades and structural parts, where precision and reliability are paramount.
3. Manufacturing of Machinery: Boring is applied in producing parts for industrial machinery, ensuring components fit together correctly and function smoothly.
4. Oil and Gas Industry: In drilling equipment manufacturing, boring creates precise and durable holes in drill bits and other components.
5. Medical Device Manufacturing: Precision boring is essential for creating parts for medical instruments and implants, where accuracy is critical.
Overall, boring is a fundamental machining process that enhances the functionality and longevity of various industrial components by ensuring precise hole dimensions and finishes.
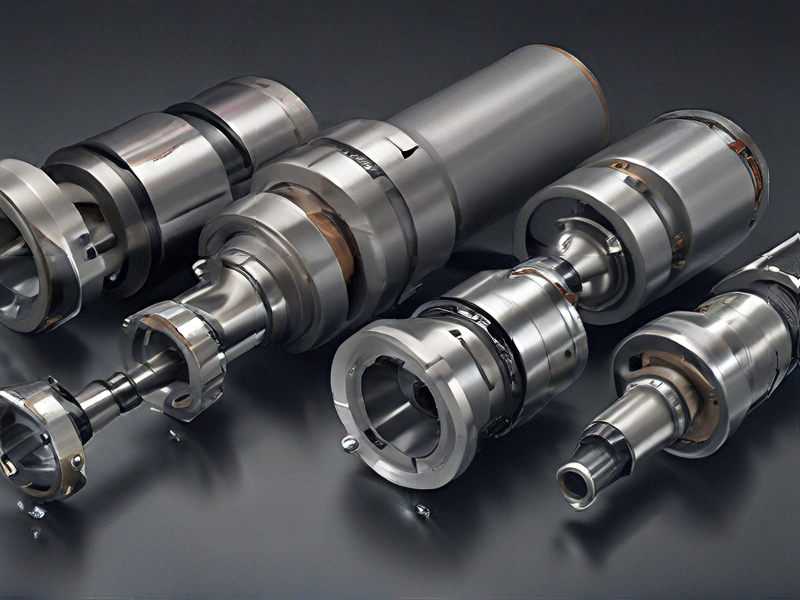
Quality Testing Methods for boring in machining and how to control quality
Quality testing methods for boring in machining involve several key techniques to ensure precision and consistency:
1. Surface Roughness Testing: Use instruments like profilometers to measure the surface finish of the bored holes, ensuring they meet specified roughness parameters.
2. Diameter Measurement: Employ precision gauges such as micrometers, calipers, and bore gauges to measure the diameter of the bored holes. Automated coordinate measuring machines (CMMs) can also be used for higher accuracy.
3. Roundness Testing: Use roundness testers to check for deviations from a perfect circular cross-section, ensuring the bore is uniformly round.
4. Concentricity Testing: Measure the alignment of the bore relative to the outer surface or other features using dial indicators or CMMs to ensure proper concentricity.
5. Depth Measurement: Ensure the bore depth meets specifications using depth micrometers or other precision depth measuring tools.
6. Defect Inspection: Perform visual inspections and use techniques like ultrasonic testing or dye penetrant inspection to detect internal and surface defects.
To control quality in boring:
1. Tool Selection and Maintenance: Choose the right boring tools and maintain them regularly to prevent tool wear, which can affect bore quality.
2. Machining Parameters: Optimize cutting speed, feed rate, and depth of cut to achieve the desired surface finish and dimensional accuracy.
3. Coolant Use: Apply appropriate coolants to reduce heat and wear, improving tool life and surface finish.
4. Regular Calibration: Calibrate measuring instruments and machinery regularly to maintain measurement accuracy.
5. Process Monitoring: Implement real-time monitoring systems to track machining conditions and make immediate adjustments as needed.
6. Training: Ensure operators are well-trained in both the operation of boring equipment and the use of quality testing instruments.
By employing these methods and controls, high precision and quality in boring processes can be consistently achieved.
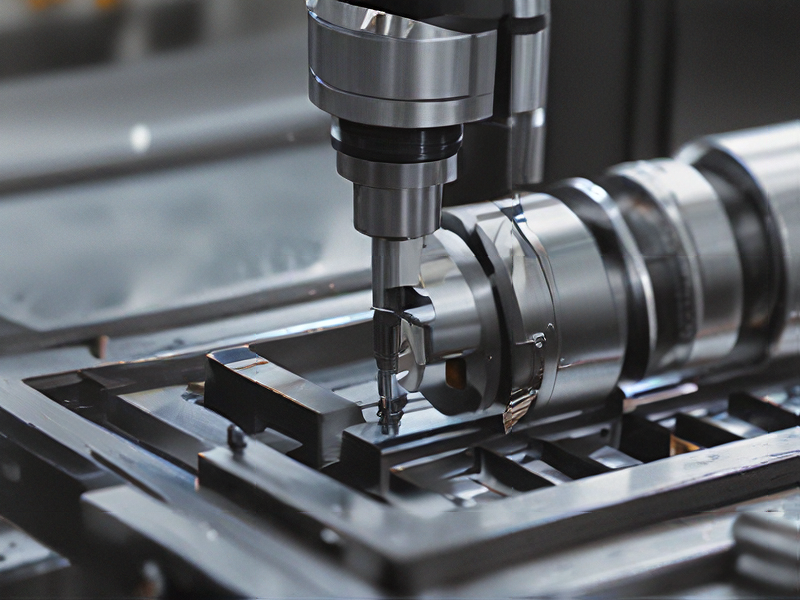
Tips for Procurement and Considerations when Purchasing from boring in machining
When procuring boring tools for machining, it’s essential to consider the following tips and factors:
1. Material Compatibility: Ensure the boring tool material is compatible with the workpiece material. Common materials include high-speed steel (HSS), carbide, and ceramics.
2. Tool Size and Type: Select the correct size and type of boring bar and inserts for your specific application. Consider adjustable and micro-adjustable boring heads for precision work.
3. Precision and Tolerance: Evaluate the required precision and tolerance of the boring operation. Higher precision tools may be necessary for tight tolerances.
4. Surface Finish: Consider the desired surface finish. Some boring tools are better suited for achieving smoother finishes.
5. Tool Life and Durability: Assess the tool’s expected life and durability. Opt for high-quality tools that offer longer service life to reduce downtime and replacement costs.
6. Machine Compatibility: Verify that the boring tool is compatible with your machining center or lathe. Check the shank type and size for proper fitting.
7. Cooling and Lubrication: Ensure the boring tool can accommodate appropriate cooling and lubrication methods to prevent overheating and extend tool life.
8. Supplier Reputation: Purchase from reputable suppliers known for high-quality tools and good customer service. Research reviews and testimonials.
9. Cost vs. Performance: Balance the cost of the tool with its performance benefits. Sometimes, investing in a more expensive tool can yield better results and cost savings in the long run.
10. Technical Support: Choose suppliers that offer robust technical support and after-sales service to assist with any issues that may arise during use.
11. Customization: For specialized applications, consider suppliers that offer custom tool design and manufacturing services.
By focusing on these considerations, you can optimize your procurement process and ensure you select the best boring tools for your machining needs.
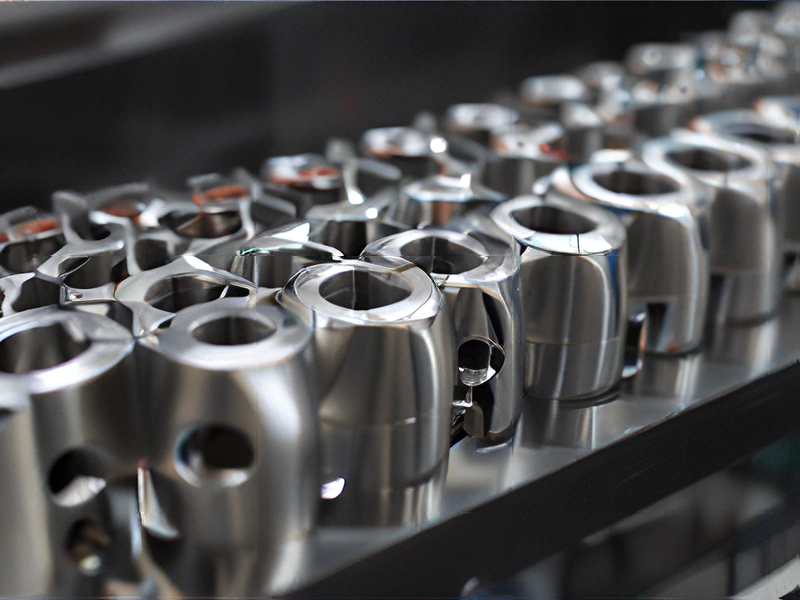
FAQs on Sourcing and Manufacturing from boring in machining in China
FAQs on Sourcing and Manufacturing from Boring in Machining in China
1. What is boring in machining?
Boring is a machining process that enlarges a pre-drilled or cast hole with precision. It enhances the accuracy and finish of the hole, often used for final sizing and finishing.
2. Why source boring machining from China?
China offers competitive pricing, advanced technology, and a large pool of skilled labor. Chinese manufacturers can provide high-quality boring services at a fraction of the cost compared to Western countries.
3. How to select a reliable Chinese manufacturer?
Research potential suppliers, check their certifications (e.g., ISO 9001), request samples, and visit their facilities if possible. Use platforms like Alibaba or Made-in-China, and consider using sourcing agents for additional security.
4. What are the common materials used in boring machining?
Common materials include metals like aluminum, steel, and cast iron, as well as plastics and composites. Ensure the manufacturer specializes in the material you require.
5. What quality control measures are in place?
Chinese manufacturers often follow strict quality control processes, including in-process inspections, final product testing, and compliance with international standards. Request documentation and third-party inspections to verify quality.
6. How do I handle shipping and logistics?
Work with experienced freight forwarders and logistics companies. Choose between air and sea freight based on urgency and cost. Ensure all customs documentation is in order to avoid delays.
7. What about intellectual property protection?
Sign non-disclosure agreements (NDAs) and work with manufacturers who respect IP laws. Register your IP in China to provide legal protection against infringements.
8. What are the lead times for boring machining projects?
Lead times vary based on the complexity and volume of the order. Generally, it ranges from a few weeks to a couple of months. Clear communication and planning can help manage timelines effectively.
9. How can I ensure effective communication?
Employ bilingual staff or interpreters, use clear and detailed drawings/specifications, and maintain regular communication through emails, video calls, and visits.
10. What are the payment terms?
Common payment terms include 30% deposit upfront and 70% upon completion or shipment. Using letters of credit (LC) or escrow services can provide additional security for transactions.
By addressing these FAQs, businesses can navigate the complexities of sourcing and manufacturing boring in machining from China more effectively.
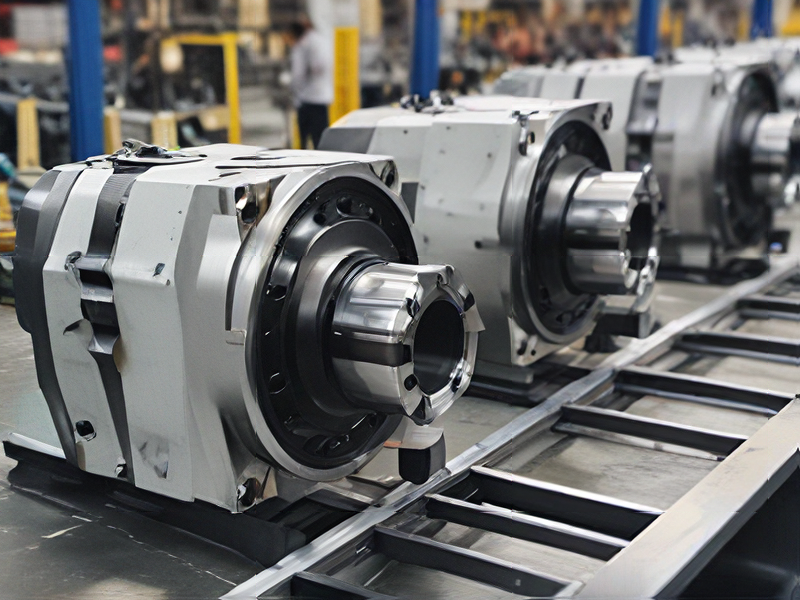