Technology and Applications of broaching machine definition
A broaching machine is a precision machining tool used to remove material from a workpiece through a cutting process known as broaching. This process involves a toothed tool, called a broach, which progressively removes material in a single pass to create precise shapes, such as splines, keyways, or holes. Broaching is highly effective for high-volume production of complex geometries with tight tolerances.
Technology
Broaching machines come in two primary types: horizontal and vertical.
1. Horizontal Broaching Machines: These are used for longer strokes and are ideal for larger workpieces. The broach moves horizontally through the workpiece.
2. Vertical Broaching Machines: These are more compact and used for shorter strokes. The broach moves vertically, which is suitable for smaller or more complex workpieces.
The broaching process involves the following key components:
– Broach: A multi-toothed cutting tool that progressively removes material.
– Fixture: Holds the workpiece securely in place.
– Drive Mechanism: Moves the broach through the workpiece, either hydraulically, mechanically, or electrically.
Applications
Broaching is widely used in various industries due to its efficiency and precision:
1. Automotive Industry: For manufacturing transmission gears, connecting rods, and other components that require precise internal shapes.
2. Aerospace Industry: For producing complex parts like turbine disks and structural components.
3. Manufacturing of Tools: Creating detailed shapes in cutting tools and dies.
4. Hardware Production: Making parts such as lock mechanisms and fasteners.
Advantages
– High Precision: Capable of achieving tight tolerances.
– Efficient Production: Ideal for mass production with consistent quality.
– Versatility: Can produce complex internal and external geometries.
Disadvantages
– Initial Cost: High initial investment for broaching machines and tooling.
– Specific Applications: Limited to parts that fit within the machine’s capabilities.
Broaching machines are integral to industries that demand high precision and efficiency in producing complex shapes, making them invaluable in modern manufacturing.
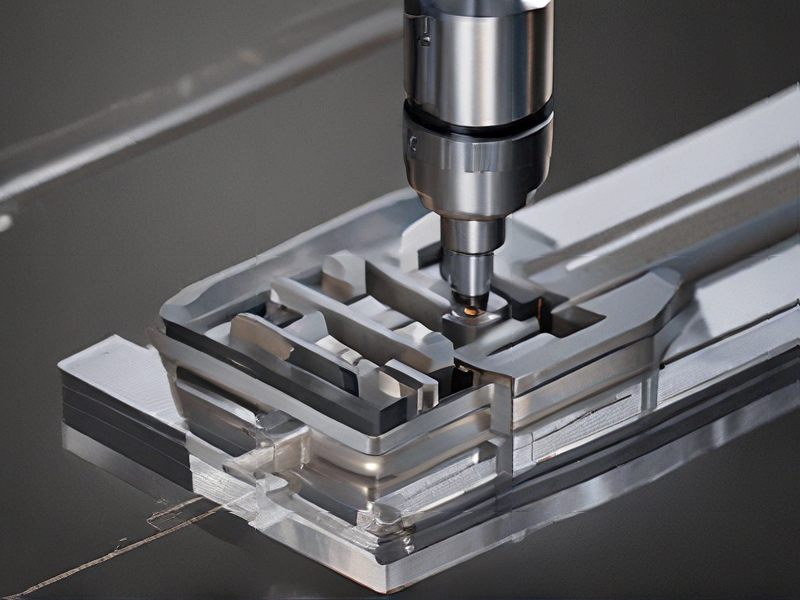
Quality Testing Methods for broaching machine definition and how to control quality
Broaching is a machining process that involves using a broach, a tool with multiple cutting teeth, to remove material and create complex shapes or features in a workpiece. Quality testing methods for broaching machines are crucial to ensure precision, repeatability, and durability of both the tool and the finished product.
Key Quality Testing Methods:
1. Dimensional Inspection: This involves measuring the critical dimensions of the machined part using tools like calipers, micrometers, and coordinate measuring machines (CMM). Ensuring that the dimensions fall within specified tolerances is essential for function.
2. Surface Finish Evaluation: Surface roughness can significantly impact the performance of the machined part. Techniques such as surface profilometry can be used to assess the finish quality, ensuring it meets the required standards.
3. Tool Wear Analysis: Regular inspection of the broach after use helps identify wear patterns. Techniques like visual inspections and microscopy can provide insights into the tool’s condition and predict its lifespan.
4. Vibration Analysis: Monitoring vibrations during the broaching process can indicate potential issues, such as misalignment or imbalanced components, which can compromise quality.
5. Material Testing: Ensuring that the material properties of the workpiece meet specifications is vital. Non-destructive testing methods, like ultrasonic testing, can assess the integrity of the material before machining.
Quality Control Practices:
– Standard Operating Procedures (SOPs): Establishing clear protocols for setup, operation, and maintenance of broaching machines helps minimize errors.
– Regular Calibration: Routine calibration of measuring instruments ensures accuracy and consistency over time.
– Continuous Training: Educating operators and technicians on best practices enhances their ability to maintain quality throughout the broaching process.
Implementing these methods can effectively control and enhance the quality of broaching operations.
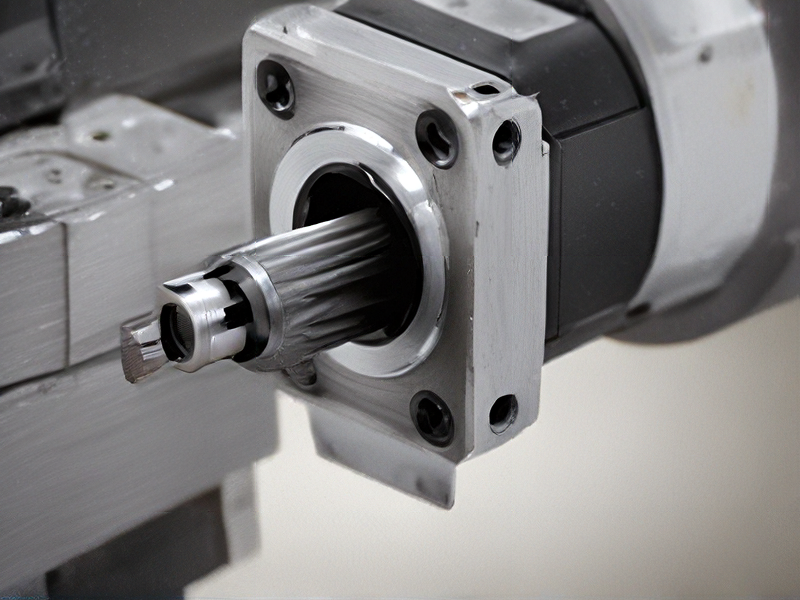
Tips for Procurement and Considerations when Purchasing from broaching machine definition
Tips for Procurement and Considerations when Purchasing a Broaching Machine
1. Understand the Requirements:
– Define the materials and components you will be broaching.
– Determine the necessary production volume and precision level.
2. Research Machine Types:
– Internal Broaching: Suitable for creating keyways, splines, or internal gears.
– External Broaching: Used for shaping the exterior of a part, such as slots and grooves.
3. Evaluate Machine Capabilities:
– Cutting Speed: Ensure the machine can handle the required speed for your production rate.
– Accuracy and Precision: Confirm the machine meets your tolerances and quality standards.
4. Consider Machine Size and Capacity:
– Check the machine’s stroke length and tonnage capacity to ensure it can handle your largest and hardest parts.
5. Look at Automation and Control Features:
– CNC Controls: For high precision and repeatability, consider machines with advanced CNC systems.
– Automation Options: Evaluate if automated loading and unloading can improve efficiency.
6. Assess Maintenance and Support:
– Reliability: Look for machines with a reputation for durability.
– Manufacturer Support: Ensure the supplier offers robust after-sales support, including maintenance and spare parts availability.
7. Total Cost of Ownership:
– Initial Purchase Price: Compare prices across different suppliers.
– Operating Costs: Factor in power consumption, tooling costs, and maintenance expenses.
– Depreciation and Resale Value: Consider the machine’s lifespan and potential resale value.
8. Compliance and Standards:
– Ensure the machine complies with industry standards and safety regulations.
9. Vendor Reputation:
– Research the manufacturer’s reputation for quality and customer service.
– Request references or case studies from similar industries.
10. Trial and Testing:
– Whenever possible, request a demo or trial to see the machine in action with your specific parts.
Conclusion:
Purchasing a broaching machine is a significant investment. Thoroughly evaluating your needs, the machine’s capabilities, and the supplier’s support will help ensure you make a well-informed decision that enhances your production capabilities.
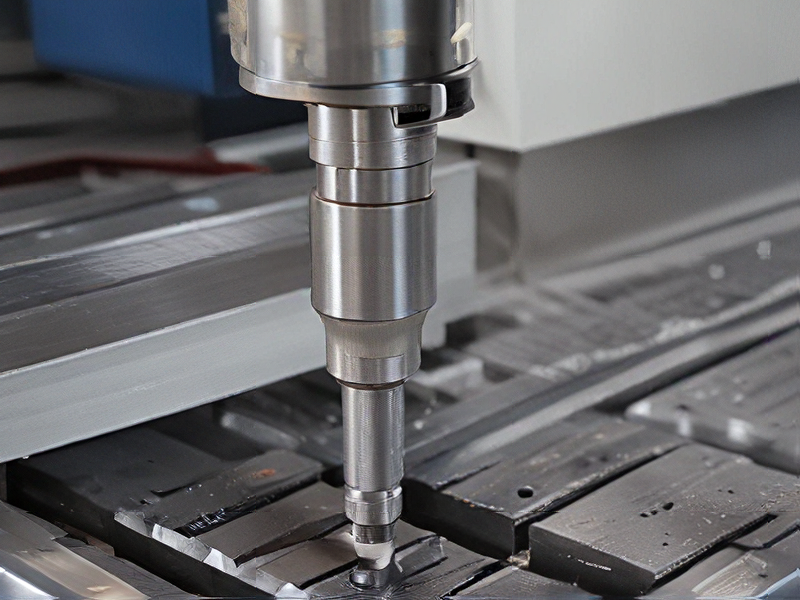
FAQs on Sourcing and Manufacturing from broaching machine definition in China
FAQs on Sourcing and Manufacturing Broaching Machines in China
1. What is a broaching machine?
A broaching machine is a specialized tool used for precision machining to remove material from a workpiece through a toothed tool called a broach. This machine is ideal for creating complex shapes and fine finishes.
2. Why source broaching machines from China?
China is a leading manufacturer of industrial machinery, including broaching machines. Benefits include competitive pricing, a wide range of products, and significant advancements in manufacturing technology.
3. How to identify reliable manufacturers?
Research and due diligence are essential. Look for manufacturers with ISO certifications, positive reviews, and a history of exporting to international markets. Visiting trade shows and factories can also help assess credibility.
4. What are the quality standards for Chinese broaching machines?
Many Chinese manufacturers adhere to international standards such as ISO, CE, and ANSI. Ensure the supplier provides detailed quality control documentation and product certifications.
5. What is the typical lead time for manufacturing?
Lead times vary depending on the machine’s complexity and customization requirements but generally range from 30 to 90 days. Always confirm with the manufacturer.
6. How is shipping and logistics handled?
Most manufacturers offer shipping solutions. Costs and times depend on the destination and shipping method (sea, air, or land). Ensure proper packaging and insurance to safeguard the machinery during transit.
7. What about after-sales service and support?
Reliable manufacturers provide comprehensive after-sales services, including installation assistance, training, and ongoing technical support. Ensure the terms are clear in the contract.
8. Are there any import regulations to be aware of?
Yes, importing machinery involves adhering to specific regulations and obtaining necessary permits and certifications in your country. Work with a customs broker to navigate these requirements.
9. How to handle payments and transactions?
Use secure payment methods such as letters of credit (LC) or bank transfers. Establish clear payment terms in the contract, including advance payments and balance settlements.
10. Can customization be requested?
Yes, many manufacturers offer customization to meet specific requirements. Discuss detailed specifications, additional features, and any unique needs with the supplier beforehand.
By following these guidelines, businesses can effectively source high-quality broaching machines from China, ensuring efficiency and precision in their manufacturing processes.
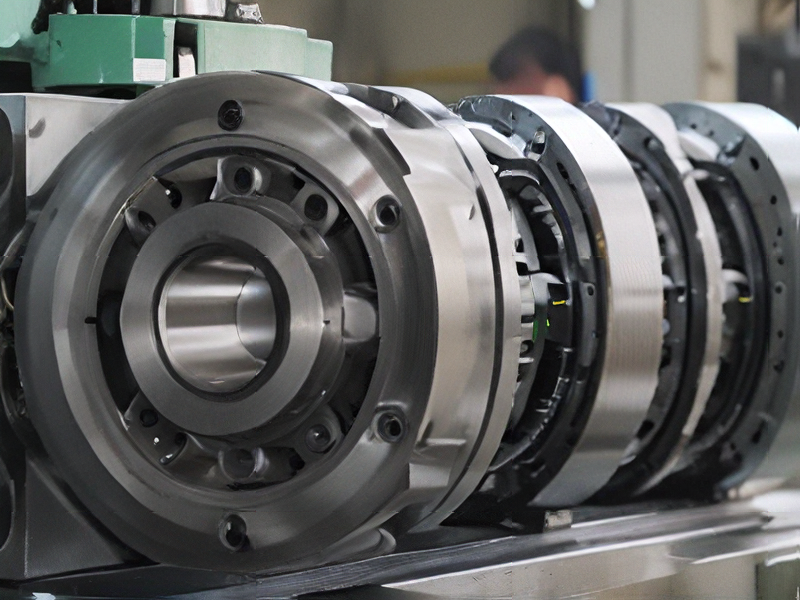