Technology and Applications of broaching machining
Broaching is a precision machining process used to remove material from a workpiece with a specialized tool called a broach. This tool features a series of cutting teeth arranged in a linear progression, enabling it to create complex shapes and features, such as keyways, gears, and profiles. Broaching is especially effective for hard materials where traditional cutting methods may be less efficient.
Technology:
Broaching machines can be vertical or horizontal, depending on the design and application. They employ either a pull broaching (pulling the broach through the workpiece) or push broaching (driving the broach into the material). The process is relatively quick and can achieve tight tolerances, making it suitable for high-volume production. Advances in CNC technology have further improved broaching, allowing for automated controls and enhanced precision.
Applications:
Broaching is commonly used in various industries, including automotive, aerospace, and manufacturing. Key applications involve shaping internal and external grooves, slots, and complex profiles on components such as engine blocks, transmission parts, and fittings. The ability to produce intricate designs and maintain high dimensional accuracy makes broaching ideal for producing parts like splines and keyways that require tight fitting with adjacent components.
In summary, broaching machining combines specialized tooling and efficient processing technology, resulting in high-quality components used in critical industrial applications. Its ability to handle complex geometries and deliver consistent results makes it a valuable technique in modern manufacturing.

Quality Testing Methods for broaching machining and how to control quality
Quality testing in broaching machining is essential for ensuring precision and performance. Here are several methods and controls to ensure quality:
1. Dimensional Inspection: Use calipers, micrometers, and coordinate measuring machines (CMM) to measure critical dimensions of the broached parts. This ensures that the machined features meet the specified tolerances.
2. Visual Inspection: Regular visual checks for surface finish, tool marks, and any visible defects are crucial. This can often be done with the naked eye or using magnifying tools.
3. Functional Testing: For parts with specific functional roles, testing their fit and performance in actual applications is vital. This might involve assembly tests or performance simulations.
4. Sampling: Implement statistical process control (SPC) by taking random samples from production batches to evaluate dimensional and surface quality against established standards.
5. Tool Condition Monitoring: Utilize methods to evaluate the condition of broaching tools, such as monitoring wear or using vibration analysis to detect tool deterioration. This helps prevent defects before they occur.
6. Material Verification: Conduct hardness tests and material composition checks to confirm that the raw materials meet specified standards before machining begins.
To control quality systematically:
– Standard Operating Procedures (SOPs): Establish clear SOPs for broaching operations to minimize variability.
– Training: Ensure operators are well-trained in broaching techniques, quality standards, and inspection protocols.
– Feedback Loop: Create a system for reporting and resolving quality issues, allowing for continuous improvement.
Implementing these methods and controls can significantly enhance the quality of broached components, reducing defects and ensuring they meet performance requirements.
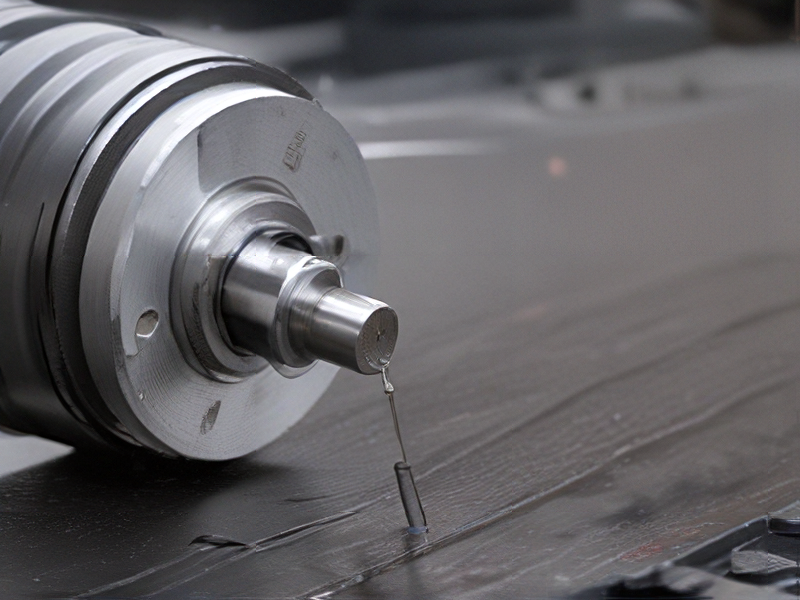
Tips for Procurement and Considerations when Purchasing from broaching machining
When procuring broaching machining services or equipment, several key tips and considerations can help ensure a successful purchase:
1. Define Requirements: Clearly outline the specifications for your broaching needs, including part dimensions, material types, tolerances, and production volumes. This will help in identifying the right machine or service provider.
2. Supplier Evaluation: Research potential suppliers thoroughly. Look for companies with proven experience in broaching machining, good reviews, and reliable customer support. Request references and case studies to gauge their capabilities.
3. Quality Assurance: Ensure that the supplier adheres to quality management standards such as ISO 9001. Inquire about their quality control processes, such as inspection techniques and certifications.
4. Cost Considerations: Get detailed quotes from multiple suppliers and compare not just the prices but also the value offered. Consider hidden costs, such as shipping, tooling, and setup fees, which can impact the total expenditure.
5. Lead Time: Understand the production lead times and ensure they align with your project timelines. Delays in procurement can significantly affect overall production schedules.
6. Technology and Innovation: Stay informed about advancements in broaching technology, as modern machines may offer improved efficiency, precision, and versatility. This could lead to cost savings in the long run.
7. Support and Maintenance: Consider the level of technical support and maintenance services provided. A reputable supplier should offer training and post-purchase support to enhance machine operation and longevity.
8. Buyer Flexibility: Be open to discussing various terms of service, such as warranties and return policies, which can protect your investment.
By following these guidelines, you can make informed decisions that optimize your procurement process in broaching machining.
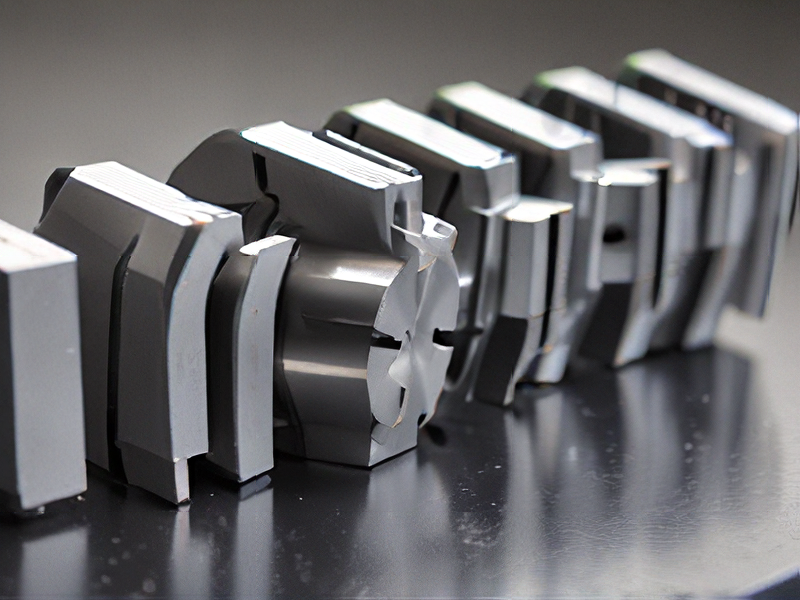
FAQs on Sourcing and Manufacturing from broaching machining in China
FAQs on Sourcing and Manufacturing of Broaching Machining in China
1. What is broaching machining?
Broaching is a machining process that uses a toothed tool (broach) to remove material. It’s efficient for producing complex shapes and is often used for keyways, holes, and internal features.
2. Why choose China for broaching machining?
China is a global leader in manufacturing, offering competitive pricing, advanced technology, and a skilled workforce. Their extensive infrastructure supports high-volume production and quick turnaround times.
3. How do I find reliable suppliers?
Start by researching online directories and trade platforms like Alibaba or Made-in-China. Verify suppliers through reviews, testimonials, and factory audits. Consider attending trade shows for direct interactions.
4. What quality control measures should I take?
Implement inspections at various production stages, including in-process checks, and pre-shipment inspections. Request certificates for materials and compliance with industry standards.
5. What are the typical lead times?
Lead times can vary, typically ranging from several weeks to a few months, depending on the complexity of the part and the supplier’s capabilities. Always confirm with your supplier.
6. How can I manage language barriers?
Consider hiring a local sourcing agent or using professional translation services to facilitate clear communication. Ensure technical documents are unambiguous.
7. What are the common payment terms?
Payment terms vary but may include a deposit (30-50%) upon order confirmation, with the balance before shipment. Use secure payment methods to mitigate risk.
8. Are there any import duties or taxes?
Yes, import duties and taxes may apply depending on your country’s regulations. Consult a customs broker for specific details related to your imports.
For tailored assistance, always consult professionals experienced in sourcing and manufacturing in China.
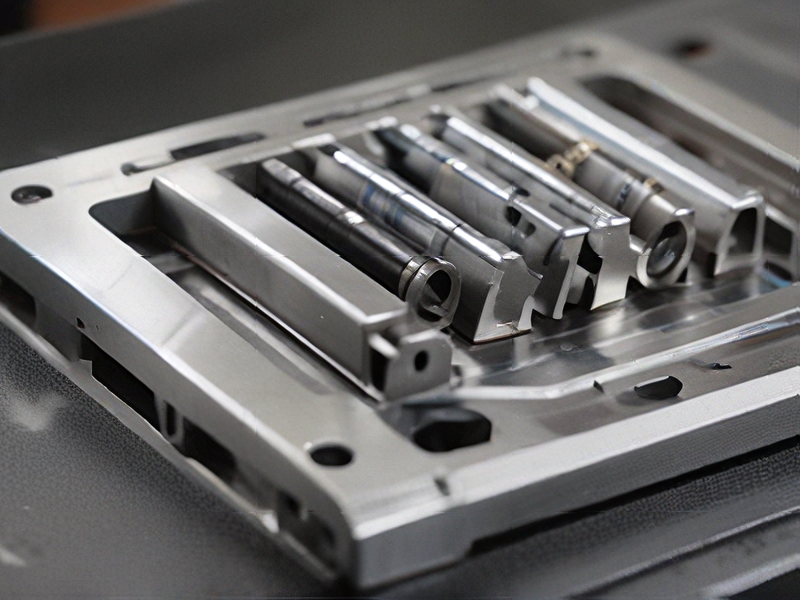