Technology and Applications of cmm measuring machine
Coordinate Measuring Machines (CMMs) are essential tools in modern manufacturing for precise dimensional measurement of objects. They utilize a probe to gather data points on an object’s surface, which are then analyzed to determine its geometric characteristics such as dimensions, angles, and positions relative to a coordinate system.
CMMs find applications across various industries including automotive, aerospace, and electronics. In automotive manufacturing, CMMs ensure parts meet strict tolerances, enhancing quality control and assembly accuracy. In aerospace, where safety and precision are paramount, CMMs verify the dimensions of critical components like turbine blades. Additionally, CMMs aid in reverse engineering by creating digital models of existing physical objects.
The technology behind CMMs has evolved, with traditional tactile probing systems now complemented by non-contact methods such as laser scanning and optical sensors. This versatility allows CMMs to measure complex shapes and fragile materials without physical contact, minimizing the risk of damage.
Integration with CAD software enables CMMs to compare measured data directly with the intended design, facilitating rapid feedback and adjustments in manufacturing processes. Furthermore, advancements in software have improved measurement speed and accuracy, making CMMs indispensable for maintaining high-quality standards in mass production environments.
In conclusion, CMMs play a crucial role in ensuring dimensional accuracy and quality across diverse industries, leveraging both traditional and advanced measurement techniques to support efficient and precise manufacturing processes.
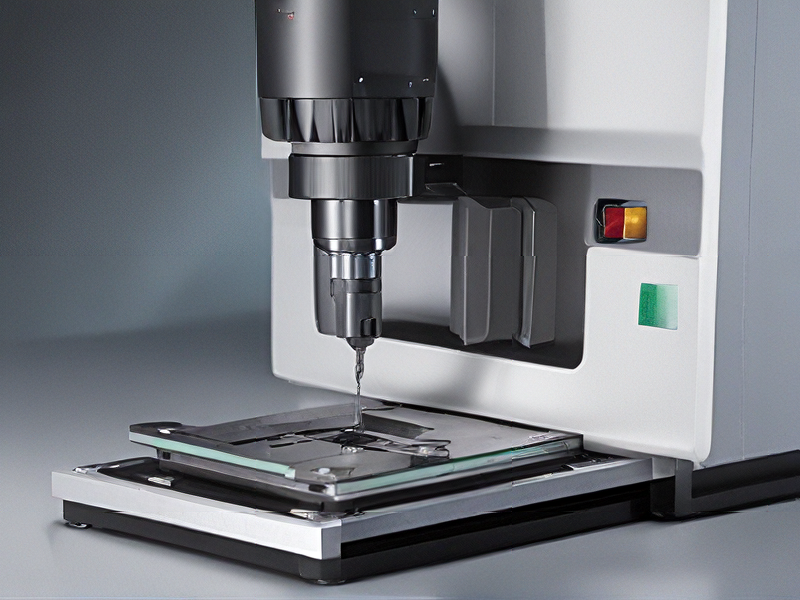
Quality Testing Methods for cmm measuring machine and how to control quality
Quality testing methods for a Coordinate Measuring Machine (CMM) typically include:
1. Accuracy Testing: Using calibrated test artifacts (such as gauge blocks or spheres) to measure dimensional accuracy across the machine’s range.
2. Repeatability and Reproducibility (R&R): Conducting studies to ensure consistent results when measuring the same part repeatedly (repeatability) and when different operators or setups are used (reproducibility).
3. Performance Verification: Regularly testing the CMM’s performance against established standards to verify its ability to measure features accurately.
4. Software Validation: Checking the measurement software against known standards and expected results to ensure it calculates dimensions correctly.
5. Environmental Conditions: Monitoring and controlling factors like temperature, humidity, and vibration that can affect measurement accuracy.
To control quality:
1. Calibration: Regularly calibrate the CMM and ensure traceability to national or international standards.
2. Operator Training: Train operators thoroughly in CMM operation, measurement techniques, and interpreting results.
3. Maintenance: Establish a maintenance schedule to keep the CMM in optimal condition and prevent breakdowns.
4. Documentation: Maintain comprehensive records of calibration, maintenance, and measurement results.
5. Process Control: Implement process controls to monitor CMM performance over time and identify deviations early.
By implementing these methods and controls, organizations can ensure the CMM measuring machine reliably provides accurate measurements, crucial for maintaining product quality and meeting customer requirements.
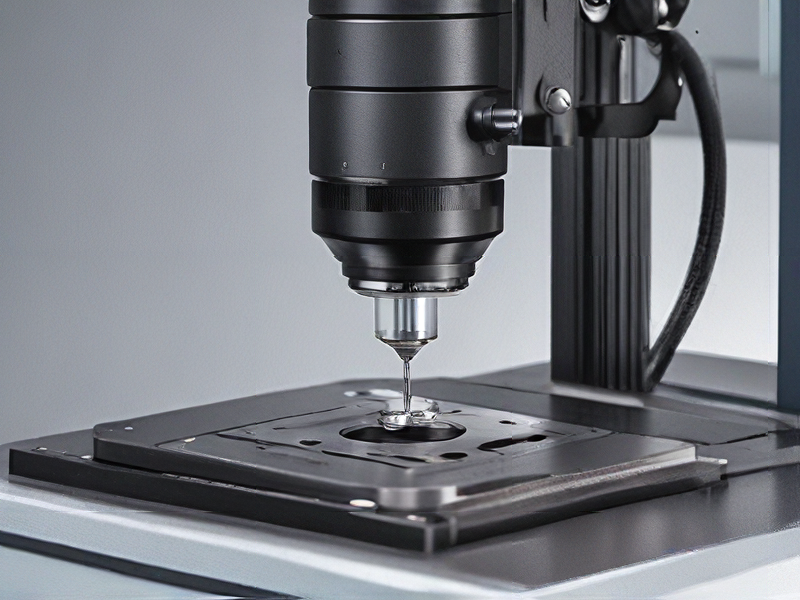
Tips for Procurement and Considerations when Purchasing from cmm measuring machine
When purchasing a Coordinate Measuring Machine (CMM), consider several key factors to ensure you make an informed procurement decision:
1. Accuracy and Precision: Evaluate the CMM’s measurement capabilities, including its accuracy and repeatability. This ensures reliable and consistent measurement results.
2. Measurement Range: Consider the size and dimensions of the parts you will measure. Ensure the CMM’s measurement range accommodates your largest and smallest components.
3. Software and Compatibility: Check if the CMM’s software is user-friendly and compatible with your existing systems. Integration with CAD/CAM software can streamline workflows.
4. Speed and Throughput: Assess the CMM’s measurement speed, as this impacts productivity. High-speed scanning capabilities can reduce inspection cycle times.
5. Flexibility and Versatility: Determine if the CMM can measure complex geometries and various materials effectively. Multi-sensor systems offer versatility for different measurement tasks.
6. Ease of Use and Training: Ensure operators can easily learn to use the CMM. Training and support from the manufacturer are crucial for efficient operation and troubleshooting.
7. Maintenance and Support: Consider the maintenance requirements and availability of technical support. A reliable service network minimizes downtime and ensures longevity.
8. Cost and Return on Investment (ROI): Compare costs against the features and benefits offered. Consider long-term ROI, including productivity gains and reduced scrap.
9. Quality Standards Compliance: Verify if the CMM meets industry standards (e.g., ISO, AS9100). Compliance ensures measurement traceability and reliability.
10. References and Reviews: Seek references from other users and reviews of the CMM model you are considering. Real-world feedback can provide valuable insights.
By carefully evaluating these factors, you can select a CMM that aligns with your measurement needs, enhances quality control processes, and provides a solid return on your investment.
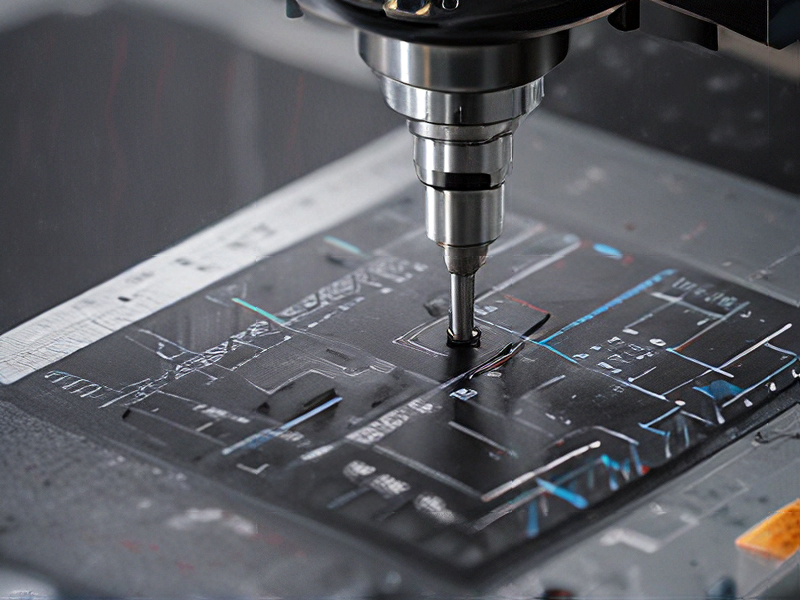
FAQs on Sourcing and Manufacturing from cmm measuring machine in China
Certainly! Here are some FAQs on sourcing and manufacturing using a CMM (Coordinate Measuring Machine) in China:
1. What is a CMM, and why is it important in manufacturing?
A Coordinate Measuring Machine (CMM) is a device used to measure the physical geometrical characteristics of an object. It ensures precision and accuracy in manufacturing processes by verifying dimensions and shapes.
2. Why source a CMM from China?
China offers a competitive advantage in manufacturing due to cost-effectiveness and a robust industrial infrastructure. Sourcing a CMM from China can provide access to advanced technology at a relatively lower cost.
3. How to choose a reliable supplier in China for a CMM?
Prioritize suppliers with a proven track record in manufacturing precision equipment. Conduct thorough background checks, request client references, and ensure compliance with international quality standards.
4. What are the key considerations when setting up a CMM in manufacturing operations?
Ensure adequate training for operators to maximize the machine’s capabilities. Integrate CMM data seamlessly into existing manufacturing processes to enhance quality control and efficiency.
5. How can quality control be maintained when manufacturing with a CMM in China?
Implement regular calibration and maintenance schedules for the CMM. Establish clear quality control protocols and conduct inspections at critical stages of production to detect and rectify deviations promptly.
6. What are the potential challenges when sourcing a CMM from China?
Challenges may include language barriers, cultural differences, logistics, and ensuring intellectual property protection. Mitigate risks by working with experienced partners and legal advisors.
7. What support can be expected from Chinese manufacturers of CMMs?
Chinese manufacturers often provide technical support, training, and after-sales service. Clarify these aspects during supplier negotiations to ensure comprehensive support throughout the CMM’s lifecycle.
Navigating sourcing and manufacturing with a CMM in China requires strategic planning, thorough due diligence, and effective communication to optimize operational efficiency and quality assurance.
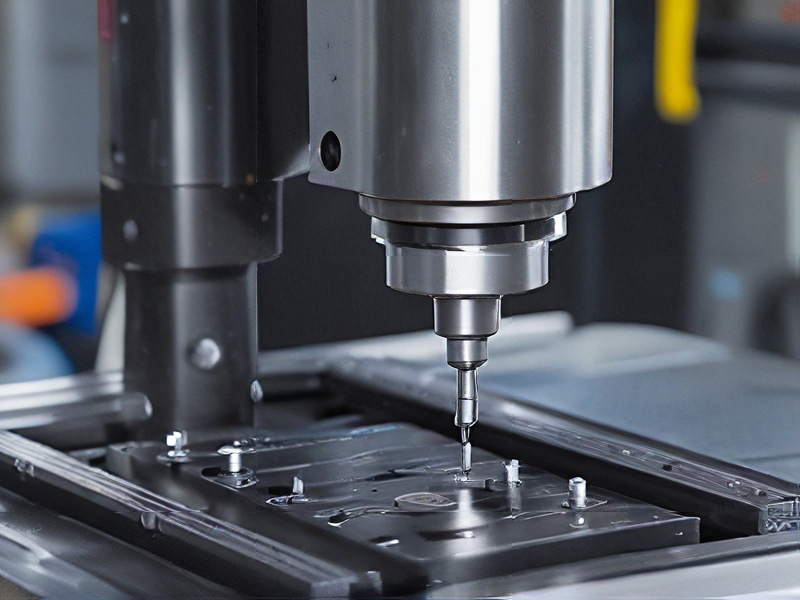