Technology and Applications of cnc 5 axis machining
CNC (Computer Numerical Control) 5-axis machining represents a pinnacle in manufacturing technology, offering significant advantages over traditional 3-axis machining. By enabling movement along five axes (three linear and two rotational), this technology enhances precision and flexibility in complex part production.
Applications span various industries, including aerospace, automotive, medical, and mold making. Aerospace benefits from 5-axis machining due to its capability to produce aerodynamic components with intricate geometries from solid blocks of metal. In the automotive sector, it facilitates the production of molds, dies, and engine components requiring precise detailing and surface finishes. Medical industries utilize it for manufacturing prosthetics, implants, and surgical instruments, ensuring accuracy critical for patient safety.
Key technological advancements include simultaneous machining of multiple surfaces, reducing setup times, and enhancing productivity. Complex geometries that previously required multiple setups can now be machined in a single operation, improving accuracy and reducing human error. Moreover, the ability to tilt and rotate the cutting tool enhances access to difficult-to-reach areas, minimizing material waste and improving efficiency.
Challenges include programming complexity and initial investment costs. Skilled operators are essential due to the intricacies of multi-axis programming and machine operation. However, ongoing advancements in software and control systems are simplifying programming and enhancing machine capabilities, making 5-axis CNC machining increasingly accessible.
Overall, CNC 5-axis machining represents a technological leap, offering manufacturers unprecedented capabilities in producing intricate components with superior precision and efficiency across diverse industries.
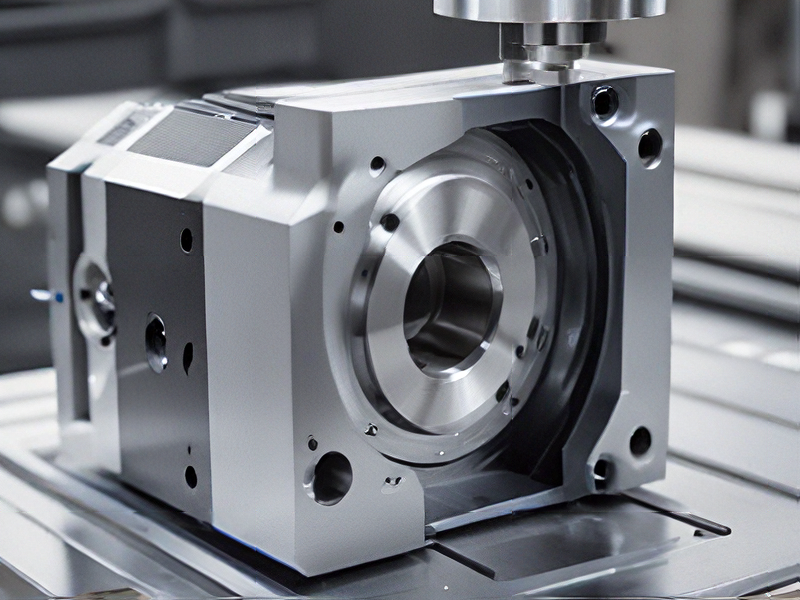
Quality Testing Methods for cnc 5 axis machining and how to control quality
Quality testing methods for CNC 5-axis machining typically involve a combination of techniques to ensure precision and consistency in manufacturing processes. Here are key methods and strategies to control quality:
1. Dimensional Inspection: Utilize coordinate measuring machines (CMMs) to measure critical dimensions and geometries of machined parts against CAD models. This ensures accuracy within specified tolerances.
2. Surface Finish Analysis: Employ surface roughness testers to evaluate the texture and smoothness of machined surfaces, ensuring they meet required specifications.
3. Tool Wear Monitoring: Implement sensor-equipped tools or periodic inspections to monitor tool wear. This helps maintain machining accuracy and surface finish quality over time.
4. In-process Monitoring: Use sensors and real-time monitoring systems to track parameters like cutting forces, vibrations, and temperatures during machining. Deviations from set parameters can indicate potential quality issues.
5. First Article Inspection (FAI): Perform comprehensive inspections of the first few parts produced to validate the manufacturing process and ensure all requirements are met before full-scale production.
6. Statistical Process Control (SPC): Implement SPC techniques to monitor process variability and ensure consistency. Control charts and other statistical tools help detect trends or deviations from standard processes.
7. Fixture and Workholding Inspection: Verify the accuracy and stability of fixtures and workholding devices to prevent part movement or distortion during machining.
8. Post-Machining Checks: Conduct final inspections after machining to verify all features, dimensions, and surface finishes meet specified requirements.
By integrating these methods, manufacturers can effectively control the quality of CNC 5-axis machining processes, ensuring products meet design specifications and customer expectations. Regular calibration of measuring equipment and continuous process improvement are also essential for maintaining high standards of quality.

Tips for Procurement and Considerations when Purchasing from cnc 5 axis machining
When purchasing from CNC 5-axis machining services, consider these tips and key considerations:
1. Capabilities and Expertise: Evaluate the supplier’s experience with 5-axis CNC machining. Look for expertise in handling complex geometries and materials relevant to your project.
2. Quality and Precision: Check for certifications (ISO, AS9100, etc.) and inquire about their quality control processes. Precision is crucial in 5-axis machining, so ensure they have a track record of delivering high-quality parts.
3. Technology and Equipment: Assess the CNC machines they use. State-of-the-art equipment enhances accuracy and efficiency. Ensure they can accommodate your specific part size and material requirements.
4. Material Selection: Verify their capability to work with the materials you need (metals, plastics, composites, etc.). Consider their experience in machining the specific material properties crucial for your application.
5. Lead Times and Capacity: Understand their production capacity and lead times. Timely delivery is essential, so align their capabilities with your project timelines.
6. Cost and Value: Compare quotes based on quality, services offered, and overall value. Avoid choosing solely based on cost; prioritize the supplier’s reputation and ability to meet your needs consistently.
7. Communication and Support: Clear communication channels are vital. Ensure they provide responsive customer support and can accommodate any design changes or issues that may arise during production.
8. References and Reviews: Request references from past clients and review their testimonials or online reviews. This provides insights into their reliability and customer satisfaction.
9. Prototyping and Testing: If applicable, inquire about their prototyping capabilities and testing procedures. Prototyping helps validate designs before full-scale production.
10. Long-Term Partnership: Consider the potential for a long-term partnership. A reliable supplier who understands your needs can streamline future projects and offer continuous improvement suggestions.
By considering these factors, you can effectively navigate the procurement process for CNC 5-axis machining services and select a supplier that best fits your project requirements.

FAQs on Sourcing and Manufacturing from cnc 5 axis machining in China
When sourcing and manufacturing via CNC 5-axis machining in China, several FAQs commonly arise:
1. What are the advantages of using CNC 5-axis machining?
CNC 5-axis machining allows for complex and precise manufacturing of parts from various angles, reducing the need for multiple setups and improving accuracy.
2. How do I ensure quality when outsourcing to China?
Choose suppliers with certifications (ISO, AS9100, etc.), conduct thorough background checks, and request samples or visit facilities if feasible. Regular communication and clear specifications are crucial.
3. What are typical lead times for CNC 5-axis machining in China?
Lead times vary based on complexity, quantity, and supplier capacity. Generally, they range from weeks to months. Clarify timelines upfront and monitor progress closely.
4. How can I manage intellectual property concerns?
Use Non-Disclosure Agreements (NDAs), specify ownership in contracts, and consider patent protection. Work with reputable suppliers who respect intellectual property rights.
5. What are the cost considerations?
Costs depend on part complexity, material, volume, and supplier capabilities. China offers competitive pricing, but factors like shipping, tariffs, and quality control inspections should be factored in.
6. How can I overcome language and cultural barriers?
Choose suppliers with proficient English speakers or employ translators. Clarify expectations and details in writing, and ensure both parties understand each other’s requirements clearly.
7. What are the steps involved in the manufacturing process?
It typically involves design review, prototyping (if needed), CNC programming, machining, inspection, and shipping. Regular updates and milestone checks help maintain alignment.
Navigating these aspects ensures a smoother experience when utilizing CNC 5-axis machining services in China, balancing cost-efficiency with quality and reliability.
