Technology and Applications of cnc cnc
Computer Numerical Control (CNC) technology revolutionizes manufacturing by automating machine tools through computer programming. It allows for precise control over machinery such as lathes, mills, and routers, enabling the production of intricate parts with high accuracy and repeatability.
CNC operates through a process that involves designing a 2D or 3D model using Computer-Aided Design (CAD) software. This digital blueprint is then translated into a set of instructions, known as G-code, that the CNC machine interprets. These instructions dictate the movement of the cutting tools, the speed of operation, and other parameters necessary to create the desired physical product.
The applications of CNC technology span numerous industries. In aerospace, it is used for manufacturing components requiring tight tolerances, such as turbine blades. The automotive industry employs CNC machining for producing parts like engine components, chassis, and brackets. In metalworking, CNC routers and plasma cutters create complex shapes from various materials, including metals, plastics, and wood.
Furthermore, CNC technology facilitates the production of bespoke items in small batches, making it invaluable for custom manufacturing. Its ability to quickly switch between designs and maintain consistent quality enhances efficiency.
Emerging technologies, such as CNC in conjunction with additive manufacturing and robotics, are pushing the boundaries of what is possible in design and production. As CNC systems evolve, they are becoming more accessible and affordable, making them a pivotal tool for engineers, machinists, and hobbyists alike. Overall, CNC technology has transformed traditional manufacturing processes, leading to enhanced productivity, precision, and innovation.
Quality Testing Methods for cnc cnc and how to control quality
Quality testing methods for CNC (Computer Numerical Control) machining are essential to ensure precision, accuracy, and conformity to specifications. Here are the key methods and controls for managing quality:
1. Visual Inspection: The first step in quality control involves a thorough visual inspection. Operators check for obvious defects like surface finish, dimensional irregularities, and tool marks.
2. Dimensional Measurement: Calipers, micrometers, and coordinate measuring machines (CMM) are used to measure critical dimensions. Comparing these measurements against CAD specifications ensures that products meet their design criteria.
3. Functional Testing: For components with moving parts or assemblies, functional testing ensures that they operate as intended under specified conditions.
4. Material Verification: Testing often extends to verifying that the raw materials used meet predetermined standards. This may involve chemical composition analysis or hardness testing.
5. Process Monitoring: Implementing in-process monitoring systems enables real-time tracking of operational parameters such as tool wear, spindle speed, and feed rates. This helps identify deviations from standard procedures immediately.
6. Statistical Process Control (SPC): Using statistical tools to analyze process data allows for identifying trends or variations in the manufacturing process. This helps maintain consistent quality and reduces defects.
7. Documentation and Traceability: Keeping detailed records of inspections and tests helps trace any defects back to their source, which is crucial for continuous improvement.
By employing these methods, CNC manufacturers can effectively control quality, ensuring that products meet both internal and external standards, thus enhancing customer satisfaction and reducing costly rework.
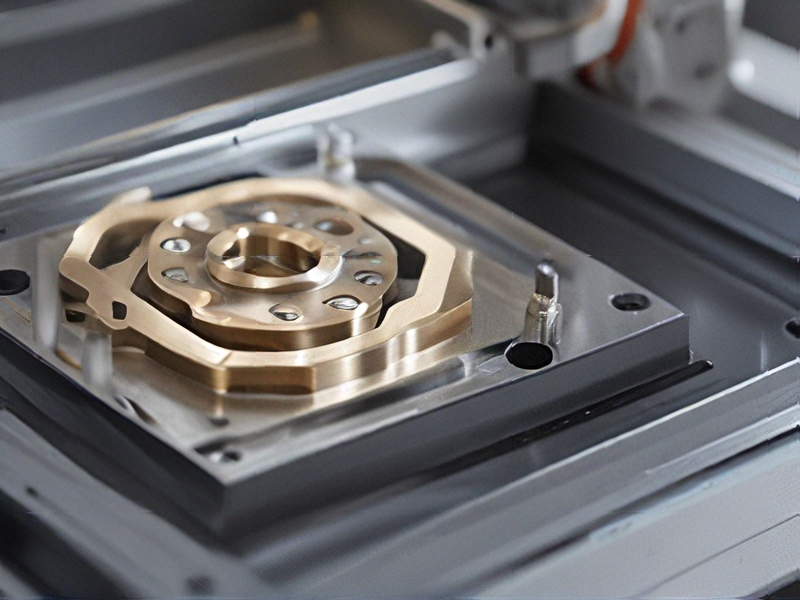
Tips for Procurement and Considerations when Purchasing from cnc cnc
When considering procurement from CNC (Computer Numerical Control) manufacturers or suppliers, it’s essential to keep several key factors in mind to ensure a successful purchase.
1. Quality Assurance: Verify the quality standards and certifications of the CNC products. Look for ISO certifications or other relevant compliance indicators that reflect the manufacturer’s commitment to quality.
2. Technical Specifications: Understand your specific machining needs, including the materials to be processed, tolerances required, and production volume. Ensure that the CNC machine you are considering meets all these technical requirements.
3. Supplier Reputation: Research the supplier’s reputation in the industry. Look for customer reviews, testimonials, and case studies. A reliable supplier will have proven experience and a solid track record.
4. Support and Training: Assess the level of after-sales support and training offered. Comprehensive training programs and accessible customer support can significantly affect the productivity of your operations.
5. Parts Availability: Inquire about the availability of replacement parts and their delivery times. A supplier that ensures readily available parts will minimize downtime in case of machine issues.
6. Cost of Ownership: Consider not just the initial purchase price but also the total cost of ownership, which includes maintenance, energy consumption, and potential upgrades.
7. Customization Options: Check if the supplier can offer customized solutions tailored to your specific process requirements, which can enhance efficiency and productivity.
8. Warranty and Service Agreements: A robust warranty and service agreement are essential for safeguarding your investment and ensuring long-term reliability.
In summary, thorough research and careful consideration of these tips will lead to informed purchasing decisions, enhancing operational efficiency and productivity.
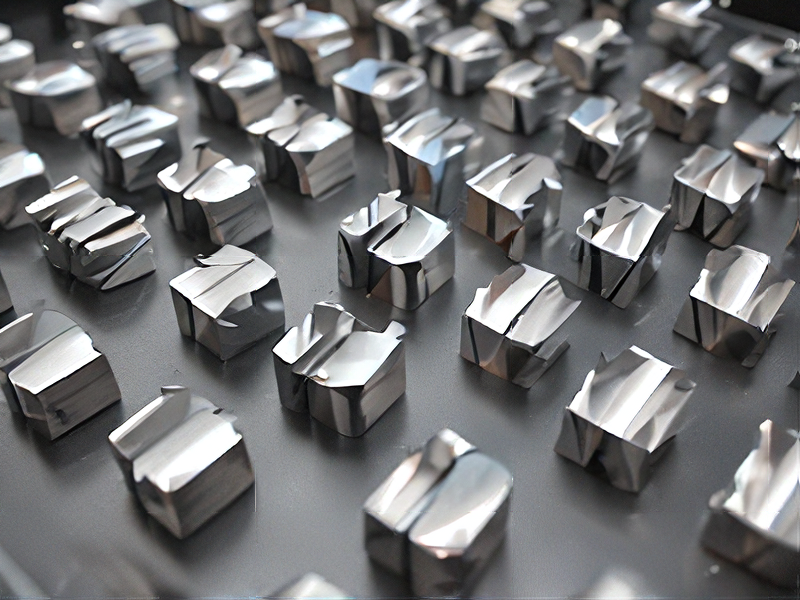
FAQs on Sourcing and Manufacturing from cnc cnc in China
FAQs on Sourcing and Manufacturing CNC Parts in China
1. What is CNC machining?
CNC (Computer Numerical Control) machining is a manufacturing process that uses pre-programmed software to control machine tools, allowing for high precision and efficiency in producing parts.
2. Why source CNC machined parts from China?
China offers competitive pricing, a vast manufacturing network, skilled labor, and advanced technology, making it a popular choice for sourcing CNC parts.
3. How do I find a reliable CNC manufacturer in China?
Research online directories, attend trade shows, and seek recommendations from industry contacts. Verify manufacturers by checking their certifications, client reviews, and production capabilities.
4. What are the typical lead times for CNC machining in China?
Lead times vary based on complexity and order size, but a typical timeframe ranges from 2 to 6 weeks. Always confirm with the manufacturer.
5. What quality standards should I expect?
Most reputable manufacturers adhere to international quality standards, such as ISO 9001. Always request quality assurance documentation and consider on-site inspections if necessary.
6. Can I request prototypes?
Yes, most manufacturers offer prototype services to test designs before mass production, ensuring that your specifications are met.
7. What is the minimum order quantity (MOQ)?
MOQs vary by manufacturer. Some may have a low MOQ for prototypes, while others may require higher quantities for initial production runs.
8. How do I handle shipping and customs?
Discuss shipping terms with your manufacturer. They may assist you in logistics and provide advice on customs documentation to ensure smooth delivery.
9. What payment methods are common?
Common payment options include wire transfers, PayPal, and letters of credit. Verify payment terms before finalizing agreements.
By addressing these FAQs, you can streamline your sourcing and manufacturing processes with CNC technologies in China.
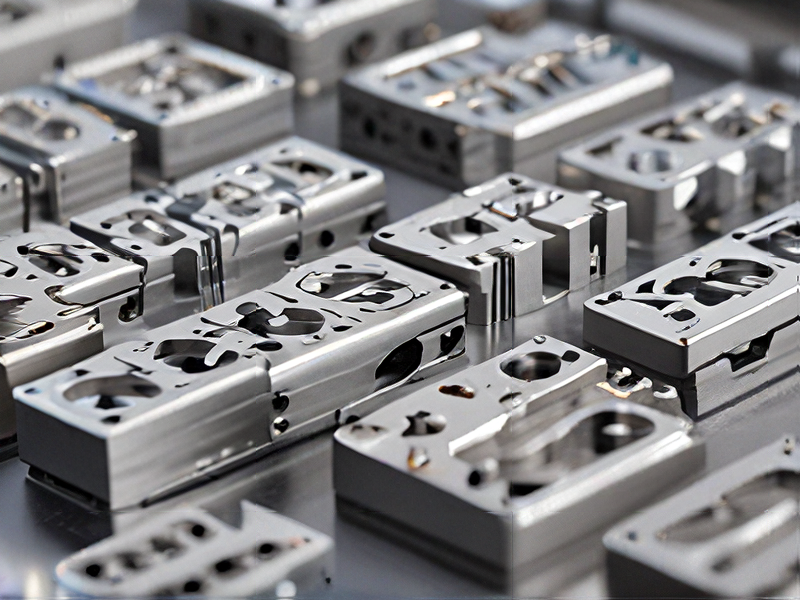