Technology and Applications of cnc how to program
Computer Numerical Control (CNC) technology automates machine tools through programmed commands. To program CNC machines, engineers use specialized software like CAD (Computer-Aided Design) and CAM (Computer-Aided Manufacturing). Here’s a simplified overview of the process:
1. Design and CAD: Engineers create a 3D model of the part using CAD software. This model defines dimensions, tolerances, and features.
2. CAM Programming: CAM software translates the CAD model into instructions (G-code) that CNC machines understand. It determines toolpaths, cutting strategies, and machine settings based on material type and desired finish.
3. G-code Generation: CAM generates G-code, a language that tells the CNC machine how to move its tools to create the part. G-code includes commands for tool movements (coordinates, speed, and feed rate), spindle speeds, tool changes, and coolant use.
4. Simulation and Verification: Before machining, engineers simulate the toolpath using CAM software to verify accuracy and avoid collisions. This step ensures the program will produce the desired part correctly.
5. Machining Process: Once verified, the G-code is transferred to the CNC machine. The machine executes the program, cutting, drilling, or shaping the material according to the specified instructions.
6. Post-Processing: After machining, additional processes like deburring or surface finishing may be required depending on the part’s specifications.
CNC technology finds applications in various industries including manufacturing, aerospace, automotive, and electronics, enabling precise and efficient production of complex parts with minimal human intervention. Mastering CNC programming involves understanding both the software tools and the principles of machining to optimize performance and quality.
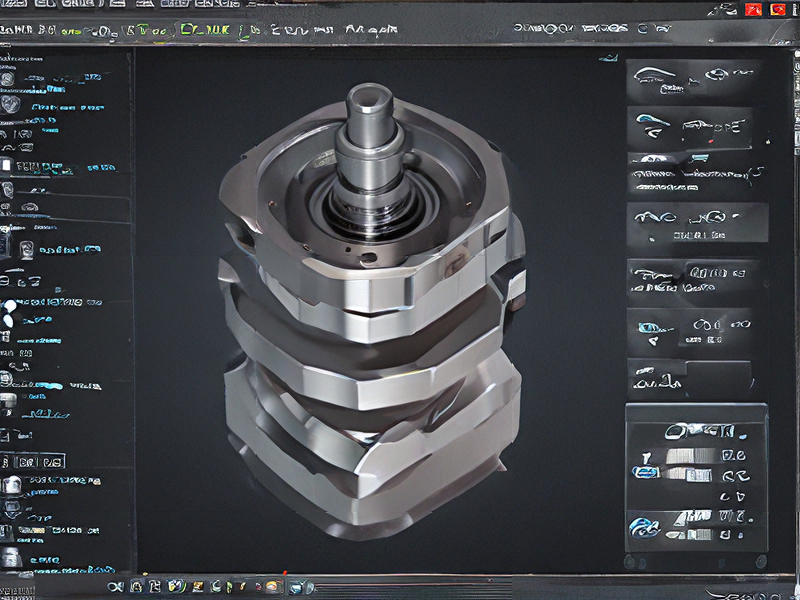
Quality Testing Methods for cnc how to program and how to control quality
Quality testing methods for CNC (Computer Numerical Control) programming and control involve several key approaches to ensure precision and reliability:
1. Simulation and Verification: Utilize CAD/CAM software to simulate tool paths and operations before actual machining. This helps identify potential issues and ensures the program matches design specifications.
2. Dimensional Inspection: Implement coordinate measuring machines (CMMs) or laser scanners to verify part dimensions against CAD models. This ensures accuracy and detects deviations early in the process.
3. Tooling Inspection: Regularly check and calibrate cutting tools using tool presetters to maintain dimensional accuracy and prevent tool wear, which can affect part quality.
4. In-Process Monitoring: Employ sensors and probes on CNC machines to monitor cutting forces, vibrations, and temperature. Deviations from predefined thresholds trigger alerts, preventing defects before they occur.
5. Statistical Process Control (SPC): Analyze process data using statistical methods to monitor variability and maintain consistency in part dimensions and surface finish. Control charts and histograms help identify trends and take corrective actions.
6. Documentation and Traceability: Maintain comprehensive records of machine settings, tooling specifications, and inspection results. Traceability ensures accountability and facilitates root cause analysis in case of quality issues.
By integrating these methods into CNC programming and quality control processes, manufacturers can optimize efficiency, minimize scrap, and deliver high-quality parts consistently.
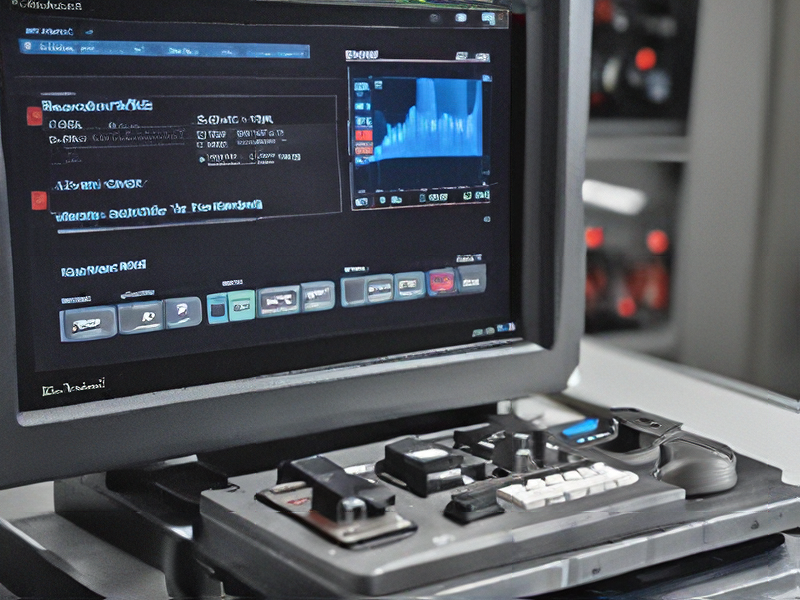
Tips for Procurement and Considerations when Purchasing from cnc how to program
When procuring CNC (Computer Numerical Control) machines, several considerations are crucial:
1. Machine Specifications: Define your operational needs clearly—consider factors like spindle speed, axis travel, and tolerance levels. Ensure the machine meets your production requirements.
2. Programming Compatibility: Assess the ease of programming. Look for machines compatible with standard programming languages like G-code or conversational programming options for simpler tasks.
3. Supplier Reputation: Choose reputable suppliers with a track record of delivering quality CNC machines and providing reliable customer support. Check reviews and testimonials.
4. Training and Support: Ensure the supplier offers training for operators and ongoing technical support. Familiarity with the machine’s programming interface is essential for efficient operation.
5. Maintenance Requirements: Evaluate the maintenance schedule and costs associated with the machine. A preventive maintenance plan can minimize downtime and extend the machine’s lifespan.
6. Integration with Existing Systems: If you have existing CNC machines or software systems, ensure compatibility and consider whether the new machine can integrate seamlessly.
7. Cost Considerations: Factor in initial purchase costs, operating expenses (like power consumption), and potential costs for tooling and spare parts.
8. Safety Features: Prioritize machines equipped with modern safety features to protect operators and prevent accidents.
9. Future Expansion: Consider scalability—whether the machine can accommodate future growth in production demands or technological advancements.
10. Reviews and References: Seek references from other users or industry experts to gauge the machine’s performance and reliability in real-world applications.
By prioritizing these considerations, you can make informed decisions when purchasing CNC machines, ensuring they meet your programming needs while aligning with your operational goals and budgetary constraints.
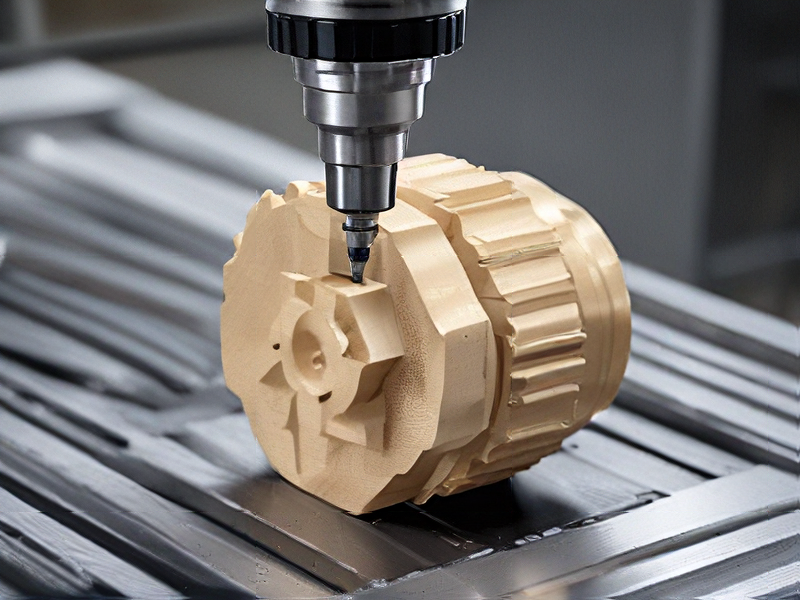
FAQs on Sourcing and Manufacturing from cnc how to program in China
Certainly! Here are some FAQs on sourcing and manufacturing from CNC programming in China:
1. Why should I consider CNC programming in China?
China offers competitive pricing, advanced manufacturing capabilities, and a wide range of CNC programming expertise.
2. How can I find a reliable CNC programming partner in China?
Utilize online platforms like Alibaba, attend trade shows such as Canton Fair, and seek recommendations from industry contacts or sourcing agencies.
3. What are the key considerations when sourcing CNC programming services in China?
Look for experience in your industry, quality certifications (ISO, CE), communication skills, production capacity, and sample availability.
4. How do I ensure quality when manufacturing CNC parts in China?
Conduct thorough due diligence, request samples, visit facilities if possible, implement quality control measures, and use contracts with clear specifications.
5. What are common challenges when outsourcing CNC programming to China?
Language barriers, cultural differences, intellectual property protection, and logistics management can pose challenges.
6. How can I protect my intellectual property (IP) when working with Chinese suppliers?
Use non-disclosure agreements (NDAs), clearly define ownership rights in contracts, consider patents or trademarks where applicable, and limit access to sensitive information.
7. What are the typical lead times for CNC programming and manufacturing in China?
Lead times vary based on complexity and volume but typically range from a few weeks to a couple of months.
8. How can I manage logistics and shipping when sourcing from China?
Work with freight forwarders or shipping agents, clarify incoterms (FOB, CIF), and anticipate customs procedures to avoid delays.
9. What are some emerging trends in CNC programming and manufacturing in China?
Adoption of automation, integration of AI and IoT technologies, and increasing focus on sustainability and environmental standards.
10. How do I handle communication effectively with Chinese suppliers?
Establish clear communication channels, use translators or bilingual staff if necessary, and prioritize building strong relationships based on trust and respect.
These FAQs provide a foundational understanding for sourcing and manufacturing through CNC programming in China, helping to navigate complexities and optimize outcomes.
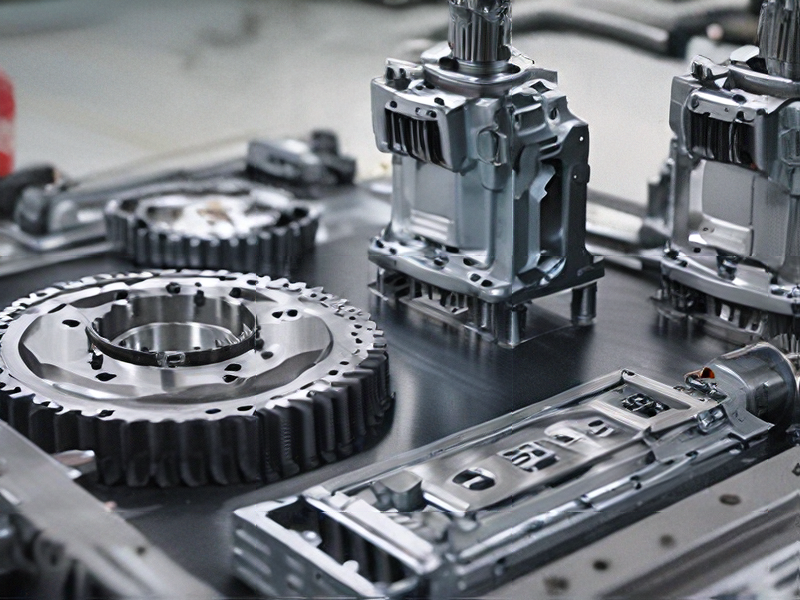