Technology and Applications of cnc machine for cutting wood
CNC (Computer Numerical Control) machines revolutionize wood cutting with precision and efficiency. These machines operate based on digital instructions, translating designs from CAD (Computer-Aided Design) software into precise movements of cutting tools. Key applications include:
1. Precision Cutting: CNC machines excel at intricate designs and complex shapes, surpassing human capabilities for accuracy. This is crucial for furniture, cabinetry, and decorative woodworking where exact dimensions are essential.
2. High Efficiency: Automating wood cutting reduces production time and waste. CNC machines optimize material usage by minimizing errors and utilizing the full surface of wood panels.
3. Versatility: They accommodate various wood types and thicknesses, offering flexibility for different projects. This includes cutting, carving, and engraving tasks, enhancing creative possibilities.
4. Consistency: Repetitive tasks like mass production benefit greatly from CNC technology. Consistent output in shape and size ensures uniformity across batches.
5. Complex Designs: Intricate patterns and 3D contours are achievable with CNC machines, enabling detailed artistic and architectural elements in woodworking.
6. Cost-effectiveness: While initial investment can be significant, long-term benefits include reduced labor costs and increased productivity, making CNC machines economically viable for medium to large-scale operations.
Technological advancements continue to refine CNC capabilities, integrating features like automatic tool changers and real-time monitoring for enhanced productivity and reliability. As CNC machines evolve, they remain indispensable in modern woodworking, combining precision craftsmanship with industrial efficiency.
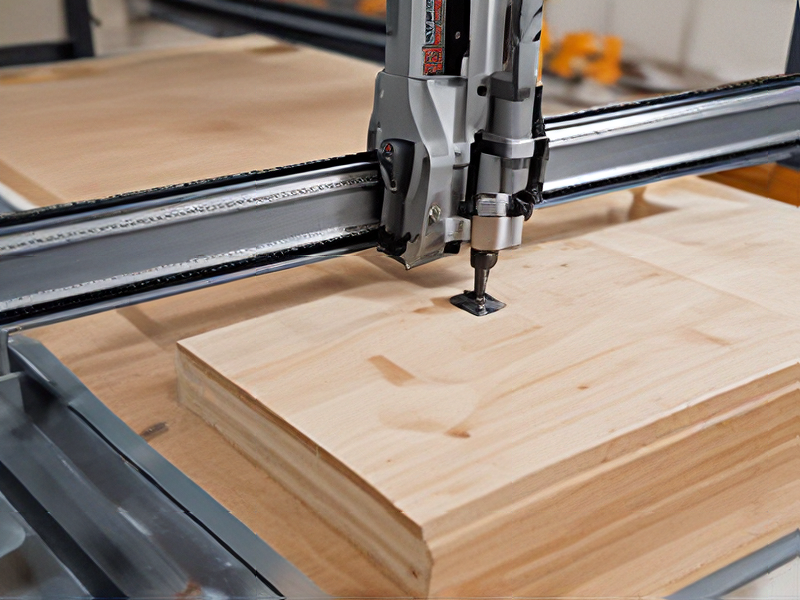
Quality Testing Methods for cnc machine for cutting wood and how to control quality
Quality testing methods for CNC machines used for cutting wood typically involve both process controls and final product inspections. Here’s a concise overview of methods and control measures:
1. Process Controls:
– Tool Calibration: Regular checks and calibrations ensure tools are sharp and correctly aligned, minimizing errors in cutting dimensions.
– Machine Calibration: Periodic calibration of the CNC machine itself ensures movements are accurate and within specified tolerances.
– Speed and Feed Optimization: Adjusting cutting speeds and feed rates based on wood type and thickness can prevent burning or uneven cuts.
2. Quality Control Measures:
– Dimensional Inspection: Using precision measuring tools to verify cut dimensions against CAD/CAM specifications.
– Surface Quality Inspection: Visual inspection or tactile methods to ensure smoothness and absence of splinters or rough edges.
– Edge Quality Assessment: Checking for burrs, tear-outs, or other imperfections along cut edges.
– Material Integrity Checks: Verifying that the wood material is not compromised during cutting, such as excessive splintering or cracking.
3. Automation and Monitoring:
– Sensor Integration: Implementing sensors to monitor cutting parameters in real-time, such as temperature and vibration, to detect anomalies.
– Data Logging: Recording and analyzing data from CNC operations to identify trends or issues affecting cut quality.
4. Operator Training and Maintenance:
– Training Programs: Ensuring operators are trained in machine operation, maintenance, and quality control procedures.
– Preventive Maintenance: Scheduled maintenance to keep the CNC machine in optimal condition, reducing the likelihood of quality issues.
By integrating these methods and controls, manufacturers can effectively manage and maintain the quality of wood cutting processes using CNC machines, ensuring consistency and precision in the final products.
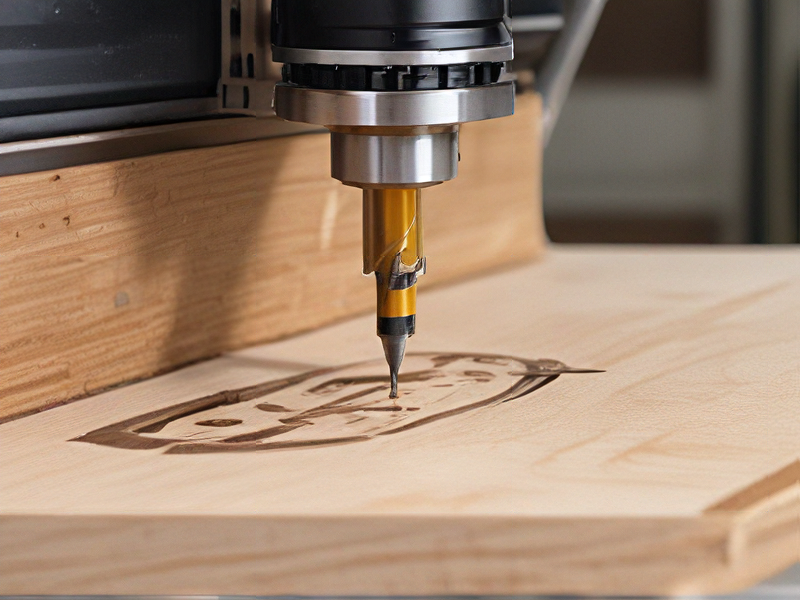
Tips for Procurement and Considerations when Purchasing from cnc machine for cutting wood
When purchasing a CNC machine for cutting wood, consider the following tips and considerations:
1. Machine Specifications: Ensure the CNC machine meets your specific requirements for wood cutting, including bed size, spindle power (typically higher for hardwoods), and cutting speed.
2. Accuracy and Precision: Look for machines with high accuracy ratings and robust construction to ensure precise cuts, especially if your projects involve intricate designs or fine detailing.
3. Ease of Use: User-friendly interfaces and software compatibility are crucial. Consider the learning curve for operating the machine and the availability of training and support.
4. Maintenance and Support: Check the availability of spare parts, maintenance requirements, and technical support from the manufacturer or supplier to minimize downtime.
5. Software Compatibility: Verify that the CNC machine is compatible with the design software you use (e.g., CAD/CAM programs) to streamline the workflow from design to production.
6. Budget and ROI: Balance your budget with the long-term return on investment. Cheaper machines may have higher operating costs or lower durability.
7. Safety Features: Ensure the machine complies with safety standards and has features like emergency stops, safety guards, and proper ventilation systems for dust extraction.
8. Reviews and Recommendations: Research customer reviews and seek recommendations from others in the woodworking industry to gauge reliability and performance.
9. Customization Options: Evaluate whether the machine can be customized or upgraded in the future to accommodate changing business needs or technological advancements.
10. Warranty and Service Contracts: Understand the warranty coverage and available service contracts to protect your investment and ensure ongoing support.
By considering these factors, you can make a well-informed decision when purchasing a CNC machine for cutting wood, tailored to your specific operational needs and business goals.
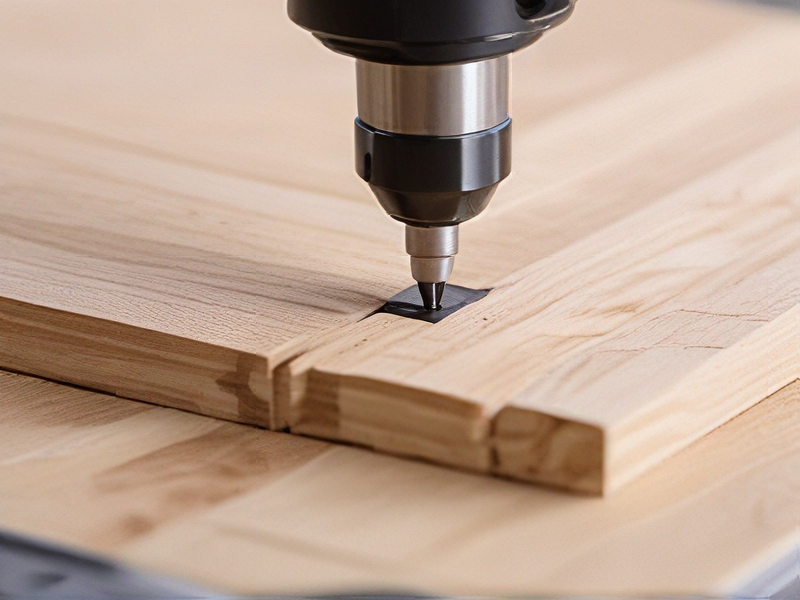
FAQs on Sourcing and Manufacturing from cnc machine for cutting wood in China
When sourcing CNC machines for cutting wood from China, here are some frequently asked questions (FAQs) to consider:
1. What types of CNC machines are available for wood cutting in China?
– CNC routers and CNC laser cutting machines are popular options. Routers are versatile for detailed cuts, while lasers offer precision for intricate designs.
2. How do I choose a reliable manufacturer in China?
– Look for manufacturers with a proven track record and positive customer reviews. Verify certifications like ISO standards for quality assurance.
3. What are typical lead times for CNC machines from Chinese manufacturers?
– Lead times vary but typically range from 4 to 12 weeks, depending on machine complexity and customization.
4. What about customization options?
– Many Chinese manufacturers offer customization to fit specific wood cutting needs, including size adjustments and additional features.
5. What certifications or standards should I consider for CNC machines from China?
– CE certification is crucial for compliance with European standards, indicating safety and quality. ISO 9001 certification ensures consistent manufacturing processes.
6. How do I handle shipping and import logistics?
– Work with manufacturers experienced in international shipping or use freight forwarders for smooth transit and customs clearance.
7. What after-sales support can I expect?
– Ensure the manufacturer provides technical support, warranty details, and access to replacement parts to minimize downtime.
8. Are there potential challenges with language and communication?
– Overcome language barriers by using translators or choosing manufacturers with English-speaking support teams.
9. What are the payment terms typically offered?
– Payment terms vary but often include initial deposit, progress payments, and final payment upon completion or delivery.
10. How can I ensure product quality and avoid issues like defects?
– Request samples, visit the manufacturer if possible, or hire a third-party inspector to ensure the CNC machine meets specifications before shipment.
Navigating these FAQs will help streamline your sourcing process and ensure a successful partnership with a CNC machine manufacturer in China for wood cutting applications.
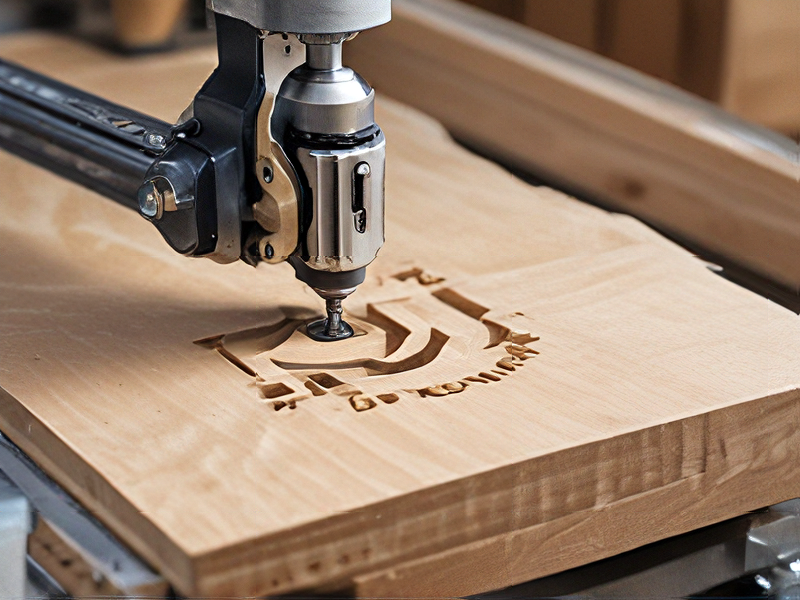