Technology and Applications of cnc machine vacancy
A vacancy for a CNC (Computer Numerical Control) machine technician typically involves specialized knowledge and skills in operating, maintaining, and programming CNC machinery. These machines are pivotal in modern manufacturing for their precision and efficiency in shaping raw materials like metal, wood, or plastic into finished components.
Key responsibilities often include interpreting technical drawings, setting up machines with the right tools and materials, and ensuring the CNC programs are optimized for accuracy and efficiency. Troubleshooting mechanical issues, conducting regular maintenance, and adhering to safety protocols are also crucial aspects of the role.
Proficiency in CAD/CAM software is essential for programming CNC machines, enabling technicians to create and modify design files that dictate the machine’s movements and processes. Additionally, a good understanding of materials and machining processes helps in selecting appropriate cutting tools, speeds, and feeds for different jobs.
In terms of applications, CNC machines are used across various industries such as automotive, aerospace, electronics, and furniture manufacturing. They produce a wide range of products from engine parts and circuit boards to furniture components and medical devices.
Candidates for this position should possess a strong technical aptitude, attention to detail, and the ability to work independently as well as part of a team. Problem-solving skills and adaptability to new technologies are also highly valued in this field, as CNC machining continues to evolve with advancements in automation and digital connectivity.
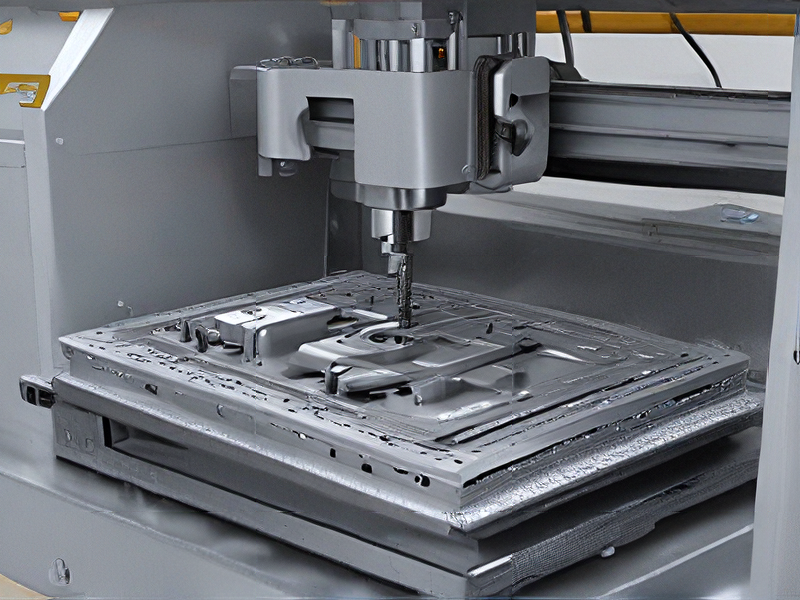
Quality Testing Methods for cnc machine vacancy and how to control quality
For a CNC machine vacancy, quality testing methods and control are crucial to ensure precision and reliability. Here’s a concise overview:
1. Dimensional Inspection: Utilize precision measuring tools like calipers, micrometers, and CMM (Coordinate Measuring Machine) to verify dimensions against engineering drawings.
2. Surface Finish Evaluation: Assess surface roughness using profilometers to ensure it meets specifications for aesthetics and functionality.
3. Material Verification: Employ spectroscopy or chemical analysis methods to confirm material composition and integrity.
4. Functional Testing: Conduct simulated operational tests to verify functionality under typical operating conditions.
5. Statistical Process Control (SPC): Implement SPC techniques to monitor process stability and identify deviations early.
6. Tooling and Fixture Inspection: Regularly inspect and maintain tooling and fixtures to prevent dimensional inaccuracies.
To control quality effectively:
– Document Control: Maintain updated documentation of specifications, procedures, and inspection records.
– Training: Ensure operators are trained in inspection techniques and understand quality requirements.
– Calibration: Regularly calibrate measurement equipment to maintain accuracy.
– Feedback Loop: Establish a feedback loop between production, inspection, and engineering teams to address issues promptly.
– Continuous Improvement: Encourage continuous improvement initiatives based on quality data analysis.
By integrating these methods and controls, CNC machine vacancies can uphold high-quality standards, minimize defects, and enhance overall product reliability and customer satisfaction.
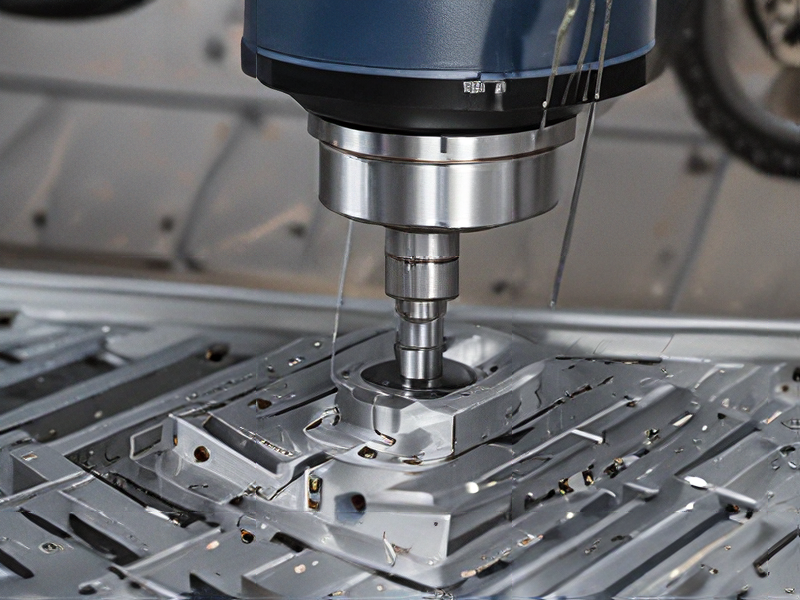
Tips for Procurement and Considerations when Purchasing from cnc machine vacancy
When procuring CNC machines, consider several key factors to ensure you make an informed decision:
1. Machine Specifications: Understand the technical specifications required for your operations, including size, cutting capabilities, spindle speed, and tolerance levels.
2. Supplier Reputation: Choose a reputable supplier with a track record of delivering quality machines and reliable customer support. Check reviews and customer testimonials.
3. Budget: Determine a clear budget that balances initial investment with long-term operational costs, including maintenance and training.
4. Technology and Innovation: Opt for machines that incorporate the latest technological advancements to improve efficiency, accuracy, and productivity.
5. Service and Support: Ensure the supplier provides comprehensive after-sales support, including training programs, maintenance services, and spare parts availability.
6. Compatibility: Verify compatibility with your existing infrastructure, software systems, and workflow to minimize integration issues.
7. Warranty and Insurance: Review warranty terms and consider insurance options to protect against unforeseen damages or malfunctions.
8. Energy Efficiency: Choose machines that are energy-efficient to reduce operating costs and environmental impact.
9. Safety Features: Prioritize machines with robust safety features to protect operators and comply with regulatory standards.
10. Future Expansion: Consider future scalability and expansion plans to ensure the chosen CNC machine can accommodate increased production needs.
By carefully considering these factors and conducting thorough research, you can make a well-informed procurement decision that aligns with your operational requirements and long-term business goals.
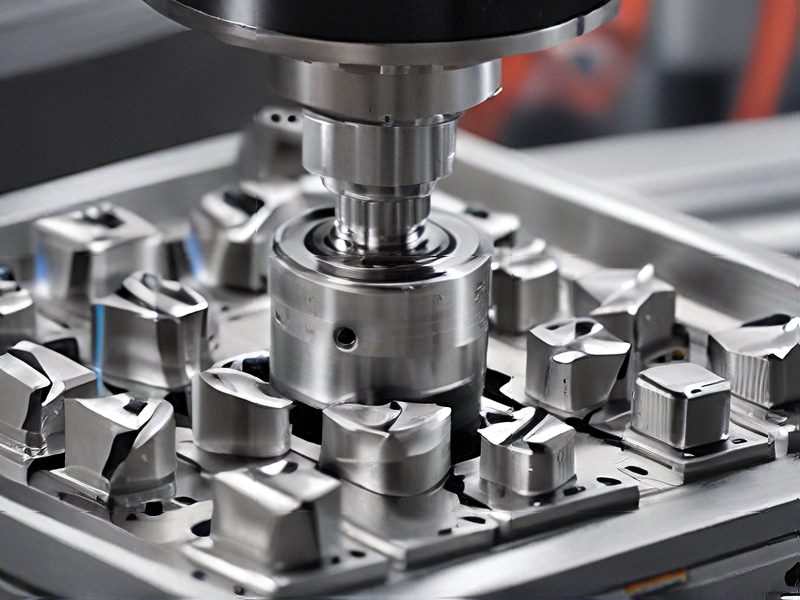
FAQs on Sourcing and Manufacturing from cnc machine vacancy in China
Certainly! Here are some frequently asked questions (FAQs) regarding sourcing and manufacturing from CNC machine vacancies in China:
1. What are the benefits of sourcing from China?
Sourcing from China offers cost advantages due to lower labor and manufacturing costs, a wide range of suppliers and capabilities, and access to a robust manufacturing ecosystem.
2. How do I find reliable CNC machine suppliers in China?
Utilize online platforms like Alibaba, attend trade shows like Canton Fair, or work with sourcing agents who can verify supplier credentials and capabilities.
3. What should I consider when selecting a CNC machine supplier?
Evaluate supplier experience, quality certifications (ISO, CE), production capacity, lead times, and client references to ensure they meet your requirements.
4. How can I ensure product quality when manufacturing in China?
Implement quality control measures such as onsite inspections, product testing, and clear communication of specifications and expectations with the supplier.
5. What are common challenges in manufacturing in China?
Challenges may include language barriers, cultural differences, intellectual property protection, logistics complexities, and maintaining consistent quality standards.
6. What are typical lead times for CNC machining projects in China?
Lead times can vary depending on complexity and supplier capacity but generally range from a few weeks to a couple of months. Clear communication and planning are key to managing lead times effectively.
7. How do I handle logistics and shipping from China?
Work with freight forwarders or shipping agents experienced in international logistics to manage transportation, customs clearance, and delivery to your destination.
8. What are the payment terms typically used with Chinese suppliers?
Payment terms often involve a deposit upfront (30-50%) with the balance due upon completion or shipment. Use secure payment methods and consider trade assurance options for added security.
Navigating sourcing and manufacturing in China requires thorough research, clear communication, and proactive quality management to ensure successful outcomes for CNC machine vacancies.
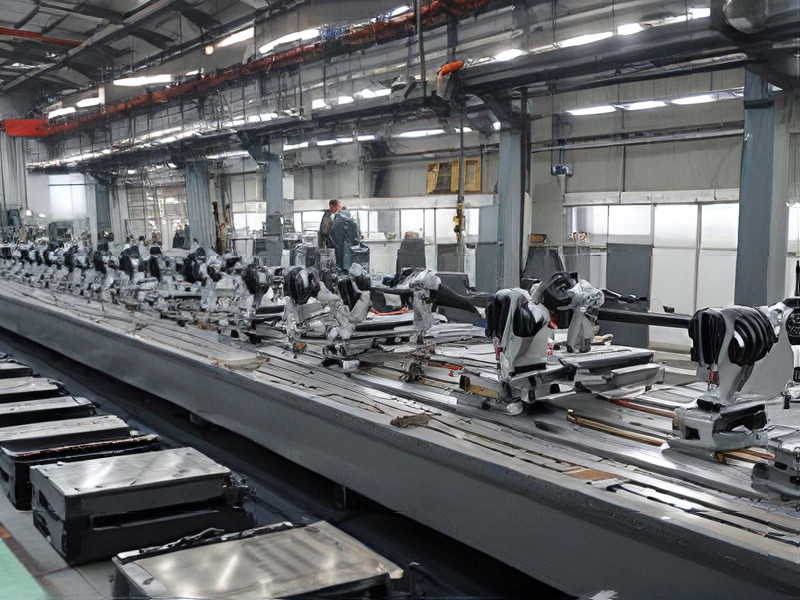