Technology and Applications of cnc machine wood cutting
CNC (Computer Numerical Control) machines revolutionize wood cutting through precise automation. Utilizing CAD (Computer-Aided Design) software, designers create intricate patterns and designs, which CNC translates into precise cutting instructions. This technology enhances productivity and accuracy, reducing human error and material waste.
In furniture manufacturing, CNC wood cutting ensures consistent quality across pieces, whether complex shapes or repetitive cuts. It enables customization at scale, accommodating unique designs and client preferences efficiently. Moreover, CNC machines handle various wood types and densities, from softwoods like pine to hardwoods such as oak, ensuring versatility in production.
Artisans and designers benefit from CNC’s ability to replicate intricate details reliably, empowering creativity without compromising precision. This capability extends to architectural elements, where CNC machines carve ornate moldings and panels accurately, maintaining historical authenticity in restoration projects.
Beyond aesthetics, CNC wood cutting enhances efficiency and cost-effectiveness in construction. Prefabricated components like wall panels and flooring benefit from CNC’s precise cutting, reducing on-site labor and assembly time.
In conclusion, CNC wood cutting technology blends precision with versatility, transforming woodworking across industries. Its applications range from bespoke furniture to large-scale construction, bridging craftsmanship with advanced manufacturing techniques.
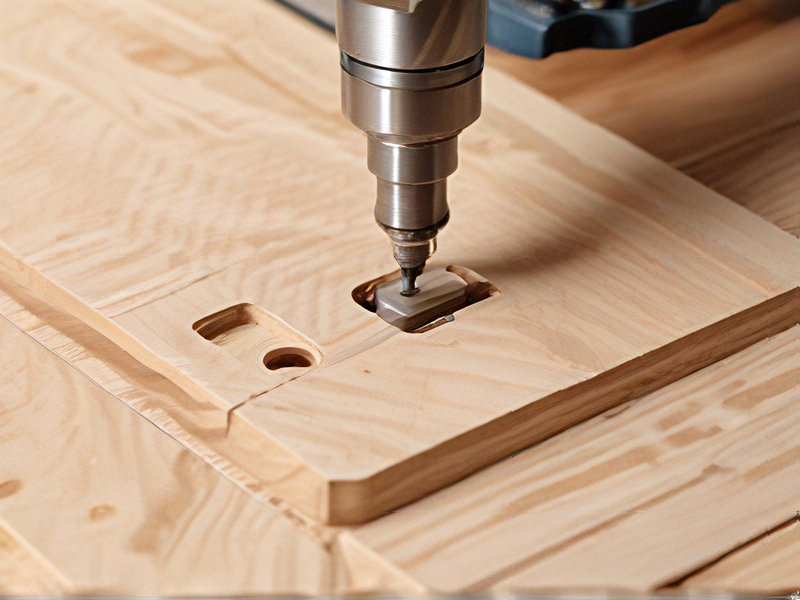
Quality Testing Methods for cnc machine wood cutting and how to control quality
Quality testing methods for CNC machine wood cutting typically include:
1. Dimensional Accuracy: Measure dimensions of cut pieces using calipers or digital measuring tools to ensure they match specifications.
2. Surface Quality: Inspect the surface finish for smoothness and uniformity using visual inspection or touch to detect any roughness or defects.
3. Edge Quality: Check edges for smoothness and straightness using a straightedge or measuring tool to ensure they meet requirements.
4. Precision of Cuts: Verify the precision of cuts by measuring the alignment and angles of cuts against design specifications.
5. Material Integrity: Assess the integrity of the wood material post-cutting to ensure there are no cracks, splits, or other structural defects.
To control quality:
1. Regular Maintenance: Ensure the CNC machine is well-maintained to prevent errors in cutting due to machine wear or misalignment.
2. Calibration: Regularly calibrate the machine to maintain accuracy in cuts and dimensions.
3. Operator Training: Train operators to set up and operate the CNC machine correctly, minimizing errors and maximizing efficiency.
4. Quality Assurance Checks: Implement regular checks throughout the cutting process to catch defects early and prevent further processing of faulty pieces.
5. Documentation: Maintain detailed records of cutting parameters, inspection results, and any issues encountered for traceability and continuous improvement.
By integrating these testing methods and quality control measures, manufacturers can ensure consistent, high-quality wood cutting outputs from CNC machines.
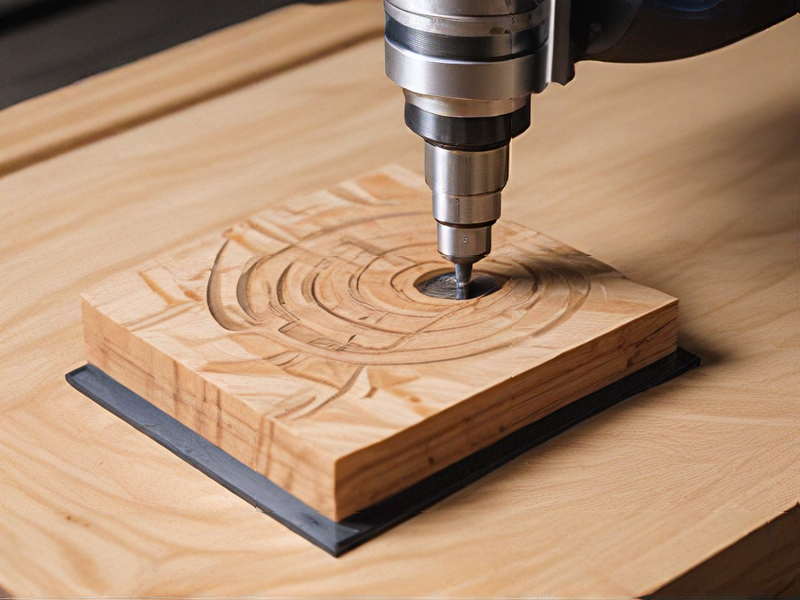
Tips for Procurement and Considerations when Purchasing from cnc machine wood cutting
When purchasing a CNC machine for wood cutting, several key considerations can ensure you make an informed procurement decision:
1. Machine Specifications: Look for machines with appropriate cutting dimensions, spindle power, and speed suitable for your woodworking needs. Consider factors like bed size, Z-axis clearance, and the type of spindle (router or other) for compatibility with your projects.
2. Accuracy and Precision: CNC machines vary in their precision levels. Ensure the machine you choose meets your tolerance requirements for wood cutting. Look for features like ball screws, linear guides, and rigidity in the machine structure to enhance accuracy.
3. Software Compatibility: Check if the CNC machine is compatible with the CAD/CAM software you intend to use. Seamless integration between your design software and the machine’s control system is crucial for efficient operation.
4. Ease of Use and Maintenance: User-friendly interfaces and accessibility for maintenance are essential. Consider the learning curve associated with operating the machine and the availability of technical support or training.
5. Build Quality and Durability: Assess the construction materials and overall build quality of the machine. A robust frame and durable components ensure longevity and consistent performance over time.
6. Safety Features: Prioritize machines with adequate safety features such as emergency stop buttons, protective enclosures, and automatic tool height adjustment to prevent accidents and ensure operator safety.
7. Cost and ROI: Evaluate the initial purchase cost, ongoing maintenance expenses, and potential return on investment (ROI). A higher initial cost may be justified by increased productivity, reduced material waste, and improved product quality.
8. Reviews and Recommendations: Research customer reviews and seek recommendations from industry peers or experts. Real-world experiences can provide insights into the machine’s reliability and performance in woodworking applications.
By carefully evaluating these factors, you can select a CNC machine that aligns with your specific wood cutting requirements, enhances productivity, and delivers consistent results.
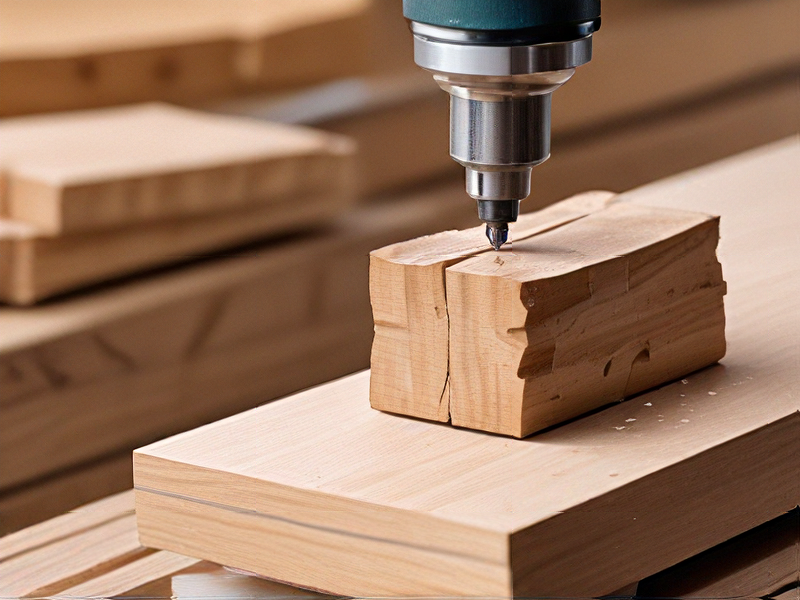
FAQs on Sourcing and Manufacturing from cnc machine wood cutting in China
When sourcing and manufacturing CNC machine wood cutting services in China, it’s essential to consider several key FAQs:
1. Quality Assurance: Ensure that the manufacturer adheres to international quality standards and has a proven track record of delivering high-quality CNC machined wood products.
2. Cost Efficiency: China is known for competitive pricing, but beware of unusually low prices that may compromise quality. Request detailed quotes inclusive of all costs to avoid unexpected charges.
3. Communication: Clear communication is crucial. Confirm that the manufacturer has proficient English skills or utilize a translator to prevent misunderstandings during production.
4. Lead Times and Production Capacity: Understand the manufacturer’s production capacity and lead times to align with your project timeline. Ensure they can meet your volume requirements consistently.
5. Materials and Customization: Verify the types of wood materials available and their sources. Discuss customization options such as finishes, dimensions, and additional processing capabilities.
6. Logistics and Shipping: Determine shipping methods, costs, and logistics arrangements. Factor in packaging requirements to minimize potential damages during transit.
7. Intellectual Property Protection: Implement contracts and non-disclosure agreements (NDAs) to safeguard your designs and intellectual property rights throughout the manufacturing process.
8. Quality Control and Inspections: Plan for regular quality inspections during production and before shipment to maintain product integrity and compliance with specifications.
By addressing these FAQs when sourcing CNC machine wood cutting services from China, you can mitigate risks, ensure quality, and streamline your manufacturing process effectively.
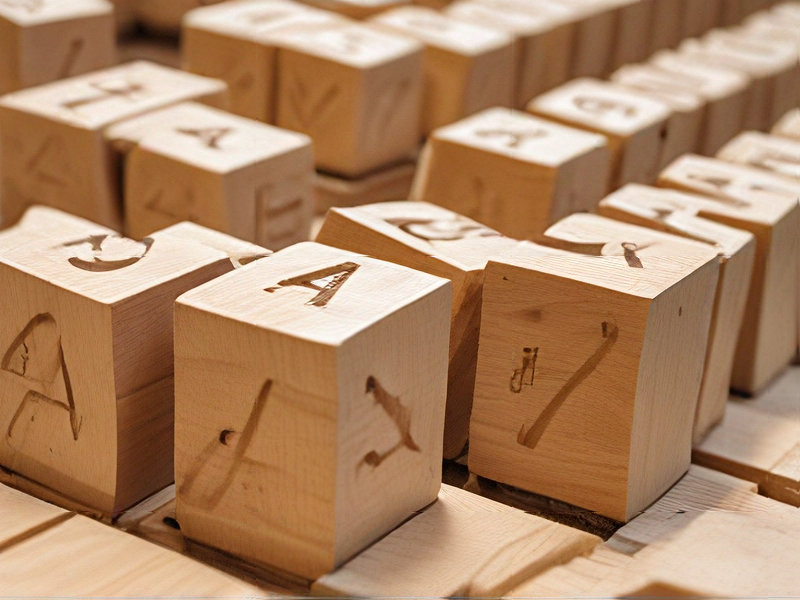