Technology and Applications of cnc machine woodworking
CNC (Computer Numerical Control) machines have revolutionized woodworking by enhancing precision, efficiency, and design capabilities. These automated systems utilize computer-generated designs to guide cutting, shaping, and drilling tools, allowing for intricate and consistent results that would be challenging to achieve manually.
One of the primary technologies in CNC woodworking is the use of tools like routers, milling machines, and laser cutters. These machines can create complex shapes and fine details, making them ideal for furniture production, cabinetry, and decorative items. CNC routers are particularly popular for their versatility, able to work with various materials such as wood, MDF, and plywood.
Applications of CNC machines in woodworking are vast. They are used in custom furniture design, where unique patterns and cuts enhance aesthetic appeal. In cabinetry, CNC allows for precise fitting and uniformity, reducing material waste and increasing production speed. Additionally, CNC technology enables rapid prototyping, allowing designers to visualize and adjust designs before full-scale production.
Moreover, advances in software have made CNC machining accessible to small businesses and hobbyists. User-friendly programs allow individuals to convert 2D designs into 3D models seamlessly, facilitating creativity without extensive technical knowledge.
In summary, CNC technology transforms woodworking by delivering exceptional accuracy, efficiency, and creativity. Its diverse applications not only streamline production processes but also empower artisans to push the boundaries of design, making it an indispensable tool in the modern woodworking industry.

Quality Testing Methods for cnc machine woodworking and how to control quality
Quality testing for CNC machine woodworking involves several methods to ensure precision, accuracy, and consistency in the final product. Here are key methods and controls:
1. Dimensional Accuracy
Method: Use calipers, micrometers, and coordinate measuring machines (CMM) to measure the dimensions of the workpiece against design specifications.
Control: Regularly calibrate measuring instruments and conduct machine maintenance to avoid deviations.
2. Surface Finish
Method: Inspect the surface finish using profilometers or visual inspection under magnification.
Control: Use appropriate cutting tools and speeds, maintain tool sharpness, and monitor coolant flow to ensure a smooth finish.
3. Tolerance Verification
Method: Check parts with go/no-go gauges and other tolerance-specific tools to ensure they fall within acceptable limits.
Control: Implement Statistical Process Control (SPC) to monitor and control the machining process, reducing variations.
4. Material Integrity
Method: Conduct hardness tests, moisture content tests for wood, and visual inspections for defects like knots or cracks.
Control: Source high-quality materials and store them properly to prevent warping or degradation.
5. Repeatability and Consistency
Method: Perform a series of test runs and measure the consistency of output using the same parameters.
Control: Implement regular maintenance schedules and software updates to the CNC machine to maintain consistent performance.
6. Fit and Assembly
Method: Test the fit of assembled parts manually or with fixtures that simulate the final assembly.
Control: Design fixtures and jigs for assembly testing, ensuring parts fit together seamlessly without gaps or excessive force.
7. Visual Inspection
Method: Conduct detailed visual inspections for surface defects, tool marks, and finishing quality.
Control: Train operators and inspectors to identify and rectify common defects early in the production process.
8. Functional Testing
Method: Perform functional tests on moving parts or joints to ensure they operate smoothly and as intended.
Control: Use real-life simulations and stress tests to identify potential failures under operational conditions.
By integrating these methods into the production workflow, CNC woodworking operations can maintain high standards of quality and reliability. Regular monitoring and adjustment of processes are essential for continuous improvement and defect reduction.
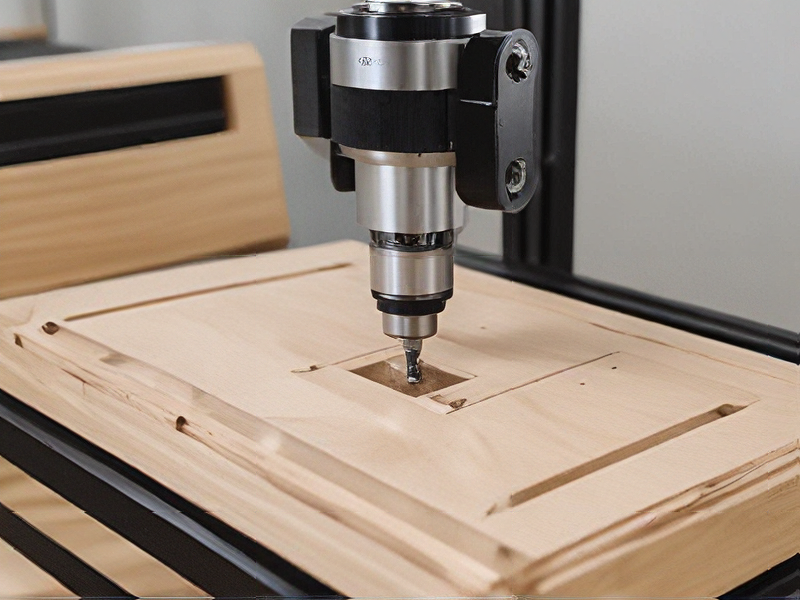
Tips for Procurement and Considerations when Purchasing from cnc machine woodworking
When procuring CNC woodworking machines, several tips and considerations can ensure a successful purchase:
1. Understand Your Needs: Clearly define the specific requirements of your woodworking projects, including material types, complexity, and volume. This helps in choosing a machine with the right specifications and capabilities.
2. Budget Planning: Establish a budget that covers not only the initial cost of the machine but also additional expenses such as installation, training, maintenance, and potential upgrades.
3. Machine Specifications: Pay attention to critical specifications such as working area dimensions, spindle power, speed, precision, and compatibility with your existing software and tools. Ensure the machine can handle your desired workload and project scope.
4. Vendor Reputation: Research and select reputable suppliers known for quality products, reliability, and excellent customer service. Read reviews, seek recommendations, and consider the vendor’s experience in the industry.
5. Training and Support: Confirm that the supplier provides comprehensive training for your team on machine operation and safety. Continuous technical support is crucial for troubleshooting and maintaining optimal performance.
6. Warranty and Service: Check the warranty terms and conditions, including coverage duration and scope. Ensure the availability of local service centers and quick access to spare parts.
7. Software Compatibility: Verify that the CNC machine is compatible with your existing CAD/CAM software or if it requires new software. Ensure the software is user-friendly and includes necessary features for your projects.
8. Future Expansion: Consider the scalability of the machine. It should be flexible enough to accommodate future growth and technological advancements in your woodworking operations.
9. Safety Features: Ensure the machine has essential safety features such as emergency stop buttons, protective guards, and proper ventilation. Safety is paramount to prevent accidents and ensure a safe working environment.
10. Energy Efficiency: Opt for energy-efficient machines that can help reduce operational costs and align with sustainability goals.
By addressing these considerations, you can make a well-informed decision, ensuring the CNC woodworking machine meets your production needs and offers long-term value.
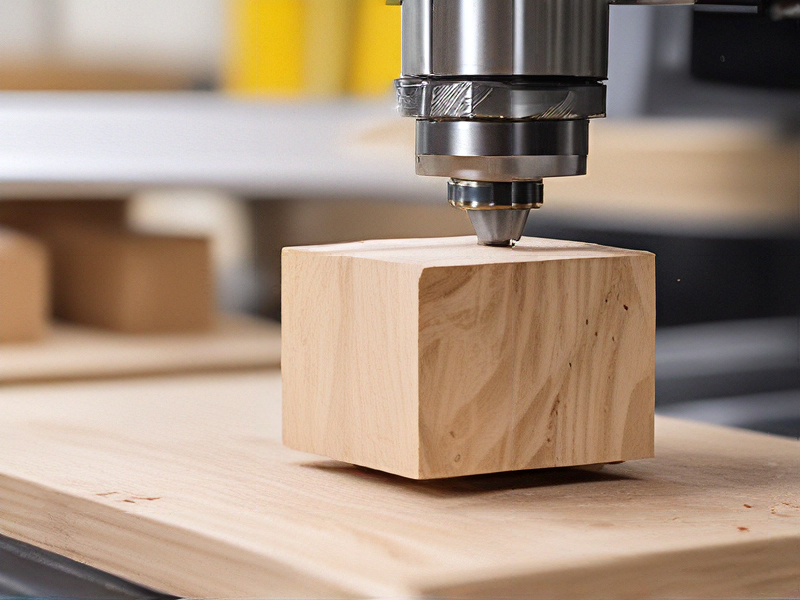
FAQs on Sourcing and Manufacturing from cnc machine woodworking in China
## FAQs on Sourcing and Manufacturing from CNC Machine Woodworking in China
Where can I find reliable CNC woodworking manufacturers in China?
Numerous online platforms specialize in connecting international buyers with Chinese manufacturers. Some popular options include Alibaba, Global Sources, and Made-in-China.
What are the advantages of manufacturing in China?
China offers competitive pricing, a vast pool of skilled labor, advanced manufacturing infrastructure, and efficient production processes.
What types of wood are commonly used in Chinese CNC woodworking?
Chinese manufacturers work with a variety of hardwoods and softwoods, including oak, walnut, cherry, pine, and bamboo.
How can I ensure quality control during the manufacturing process?
Request samples, conduct factory audits, and establish clear quality standards in your contracts. Consider working with a reputable third-party inspection agency.
What are the shipping options and costs?
Sea freight is typically the most cost-effective option for large orders, while air freight is faster but more expensive. Shipping costs vary depending on volume, destination, and chosen carrier.
How can I protect my intellectual property?
Sign strong non-disclosure agreements (NDAs) with manufacturers and consider filing patents for your designs.
Remember to thoroughly research potential manufacturers, communicate your requirements clearly, and establish a strong working relationship based on trust and transparency.
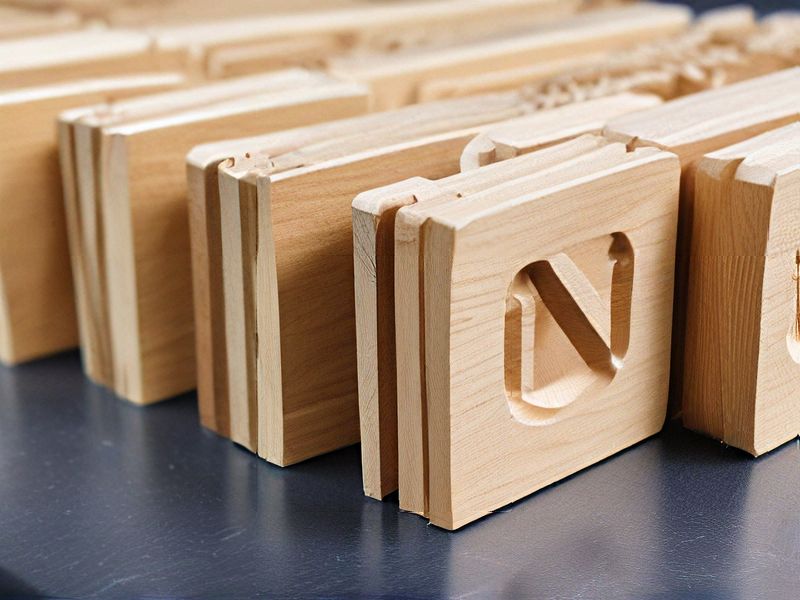