Technology and Applications of cnc milling machines
CNC (Computer Numerical Control) milling machines are advanced manufacturing tools used for precise machining of various materials, including metals, plastics, and wood. These machines use computer-controlled movements to execute complex cutting, drilling, and shaping operations based on pre-programmed designs.
Technology
1. Computer Control: CNC milling machines operate using a computer that interprets a digital design file (CAD) and converts it into a set of instructions (G-code). The machine then follows these instructions to execute precise movements.
2. Multi-Axis Movement: Modern CNC mills can move along multiple axes (typically 3 to 5) to create intricate geometries. This capability allows for the machining of complex shapes and detailed features.
3. Spindle and Cutting Tools: The spindle holds various cutting tools, which rotate at high speeds to remove material from the workpiece. Tool changers enable the automatic swapping of tools during a machining process, increasing efficiency.
4. Precision and Accuracy: CNC milling machines are known for their high precision and repeatability, often achieving tolerances within micrometers. This precision is crucial for industries requiring detailed and consistent parts.
Applications
1. Aerospace: CNC milling is vital for producing high-precision components such as turbine blades, engine parts, and structural components, ensuring reliability and performance.
2. Automotive: The automotive industry uses CNC milling for engine blocks, transmission components, and custom parts, facilitating rapid prototyping and mass production.
3. Medical Devices: CNC milling is used to manufacture complex and precise medical instruments, implants, and prosthetics, ensuring safety and functionality.
4. Electronics: Precision milling is essential for creating components like circuit boards and heat sinks, which require detailed and accurate machining.
5. Tool and Die Making: CNC milling machines produce molds, dies, and fixtures used in various manufacturing processes, enabling the production of consistent and high-quality products.
Conclusion
CNC milling machines are indispensable in modern manufacturing due to their precision, versatility, and efficiency. Their applications span across multiple industries, enhancing production capabilities and enabling the creation of complex and high-quality components.
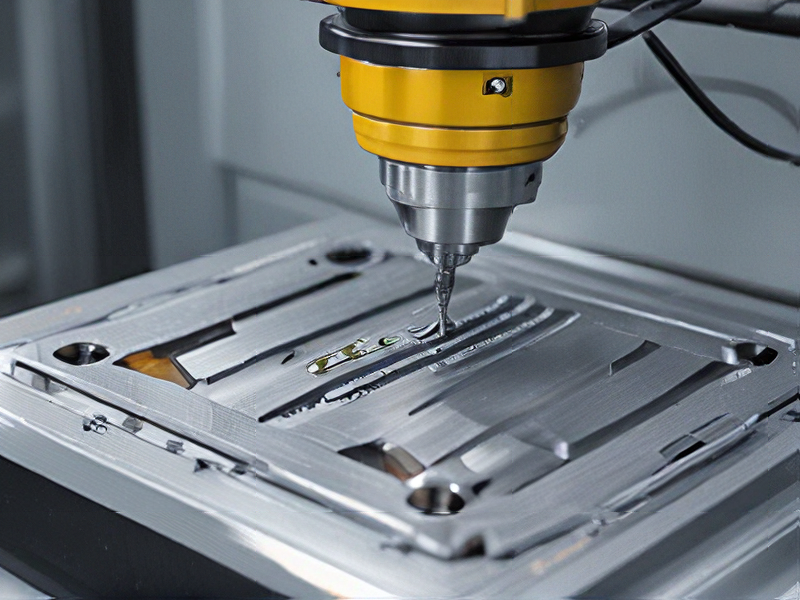
Quality Testing Methods for cnc milling machines and how to control quality
Quality testing for CNC milling machines involves several methods and controls to ensure precision and reliability in manufacturing processes. Key methods include:
1. Dimensional Inspection:
– Coordinate Measuring Machines (CMMs): These machines verify the dimensions of the machined parts against the design specifications.
– Calipers and Micrometers: For manual measurement of key dimensions.
2. Surface Finish Testing:
– Profilometers: These measure the surface roughness to ensure it meets the required standards.
– Visual Inspections: To identify any visible defects or irregularities.
3. Geometric Accuracy Testing:
– Ball Bar Testing: Assesses the machine’s circular interpolation accuracy.
– Laser Interferometry: Measures the machine’s positioning accuracy and repeatability.
4. Material Testing:
– Hardness Tests: To ensure the material properties meet the required standards.
– X-ray Fluorescence (XRF): Analyzes the material composition.
5. Operational Testing:
– Dry Runs: Running the CNC machine without a workpiece to check for proper function and any potential issues.
– Trial Cuts: Machining a test piece to ensure the machine’s performance under actual working conditions.
Quality control involves:
1. Regular Maintenance:
– Routine checks and calibrations to maintain the machine’s accuracy and reliability.
– Lubrication and cleaning schedules to prevent wear and tear.
2. Process Monitoring:
– Real-time Monitoring Systems: Use sensors and software to track the machine’s performance during operation.
– Statistical Process Control (SPC): Monitors the process parameters and identifies any deviations from the norm.
3. Training and Certification:
– Ensuring operators are well-trained and certified to handle CNC machines.
– Regular refresher courses to keep up with the latest techniques and technologies.
4. Documentation and Traceability:
– Keeping detailed records of machine maintenance, inspections, and calibrations.
– Traceability of materials and parts to ensure quality standards are met throughout the production process.
Implementing these methods and controls helps maintain the high quality and precision required in CNC milling operations.
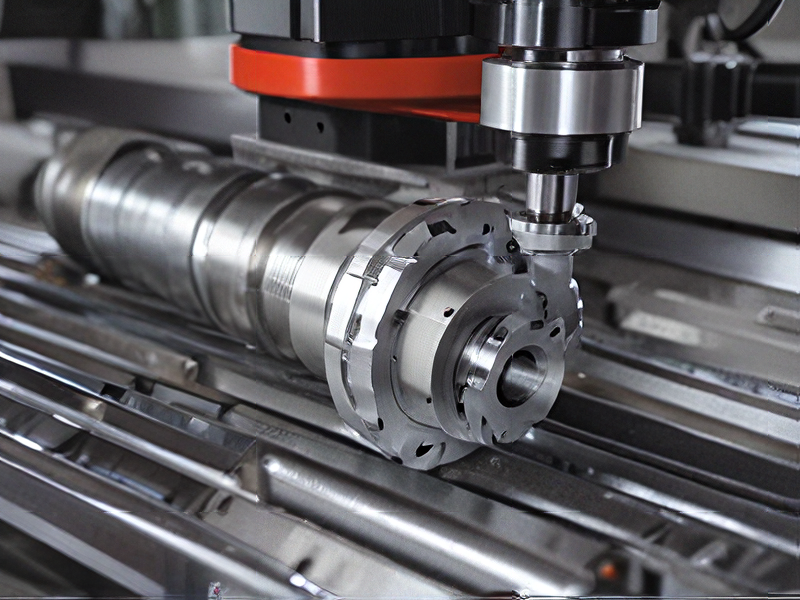
Tips for Procurement and Considerations when Purchasing from cnc milling machines
When purchasing CNC milling machines, consider the following tips and factors:
1. Define Your Needs:
– Material: Identify the types of materials you’ll be machining. Different machines handle different materials (metal, wood, plastic) with varying efficiency.
– Volume: Consider the production volume and the complexity of the tasks. High-volume production may require more robust and versatile machines.
2. Budget:
– Initial Cost vs. Long-term Value: Balance the initial purchase price with the machine’s durability, efficiency, and maintenance costs.
– Financing Options: Explore leasing or financing options to manage cash flow.
3. Technical Specifications:
– Spindle Speed and Power: Ensure the machine has the appropriate spindle speed and power for your tasks.
– Axes and Travel: Check the number of axes (3, 4, 5) and their travel range to match your precision and complexity needs.
– Control System: Choose a machine with a user-friendly and reliable control system. Compatibility with CAD/CAM software is essential.
4. Quality and Brand Reputation:
– Manufacturer Reputation: Opt for well-known brands with a history of quality and reliability.
– Reviews and Testimonials: Read customer reviews and ask for testimonials or references.
5. Support and Service:
– After-Sales Support: Ensure the manufacturer or dealer offers robust after-sales support, including training, maintenance, and repair services.
– Spare Parts Availability: Check the availability and cost of spare parts.
6. Future-Proofing:
– Upgradeability: Look for machines that can be upgraded or expanded to meet future needs.
– Technology Integration: Consider the machine’s ability to integrate with new technologies, like IoT and automation systems.
7. Trial and Demonstration:
– Testing: If possible, test the machine or see a live demonstration to ensure it meets your operational requirements.
– Sample Production: Request sample production to evaluate the machine’s precision and performance.
8. Compliance and Safety:
– Certifications: Ensure the machine complies with industry standards and certifications.
– Safety Features: Check for essential safety features to protect operators.
By thoroughly evaluating these aspects, you can make an informed decision that aligns with your operational needs and budget constraints.

FAQs on Sourcing and Manufacturing from cnc milling machines in China
FAQs on Sourcing and Manufacturing from CNC Milling Machines in China
1. Why source CNC milling machines from China?
China offers competitive pricing, advanced technology, and a vast array of suppliers. Manufacturers in China often provide high-quality machines that can meet various specifications and production needs.
2. How to find reliable suppliers?
Use platforms like Alibaba, Made-in-China, and Global Sources. Check supplier credentials, read reviews, and request samples. Visiting trade shows and fairs, like the Canton Fair, can also help in identifying reputable suppliers.
3. What factors should I consider when choosing a CNC milling machine?
Consider the machine’s specifications, such as spindle speed, feed rate, and axis capabilities. Evaluate the manufacturer’s reputation, after-sales support, and warranty terms. Ensure the machine meets your production requirements and budget.
4. How to ensure the quality of the machines?
Request detailed specifications and certification documents (e.g., ISO, CE). Arrange for pre-shipment inspections by third-party quality control firms. Consider visiting the factory to inspect the machines personally.
5. What are the common payment terms?
Typical payment terms include a 30% deposit before production and 70% balance before shipment. Letters of Credit (LC) are also a secure option. Negotiate payment terms that protect your interests.
6. How to handle shipping and logistics?
Work with experienced freight forwarders who can manage shipping, customs clearance, and delivery. Ensure that the machines are properly packaged to prevent damage during transit.
7. Are there any legal considerations?
Ensure compliance with import regulations and safety standards in your country. Obtain necessary certifications and documentation to avoid legal and customs issues.
8. What about after-sales support?
Check if the supplier offers training, technical support, and spare parts. Reliable suppliers usually provide remote assistance and have local service centers.
9. Can I customize CNC machines from China?
Yes, many manufacturers offer customization options. Clearly communicate your specifications and ensure that modifications do not compromise the machine’s performance or warranty.
10. How to maintain a good relationship with Chinese suppliers?
Maintain clear and consistent communication. Pay on time, respect cultural differences, and visit the supplier occasionally to strengthen the partnership.
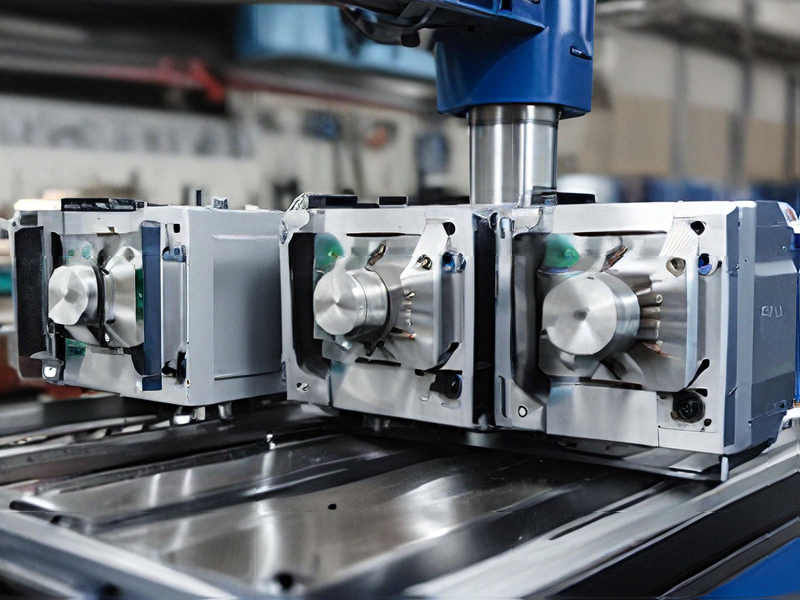