Technology and Applications of cnc program
Computer Numerical Control (CNC) programming revolutionizes manufacturing by automating machine tools through coded instructions. This technology translates designs into precise movements of cutting tools, enabling high accuracy and repeatability in production processes. CNC programs, typically written in languages like G-code, dictate tool paths, speeds, and operations, crucial for machining tasks such as milling, turning, and drilling.
Applications of CNC programming span various industries, including aerospace, automotive, electronics, and healthcare. In aerospace, CNC machines craft intricate components like turbine blades with exacting precision, ensuring safety and performance. Automotive manufacturing relies on CNC for fabricating engine parts, chassis components, and molds with consistent quality. In electronics, PCB fabrication employs CNC for drilling, routing, and milling circuit boards to microscopic tolerances.
The benefits of CNC programming are manifold. It reduces human error, enhances production speed, and enables complex geometries impossible with manual methods. CNC’s flexibility accommodates rapid prototyping and mass customization, crucial in today’s market demands. Moreover, advancements like multi-axis machining and additive manufacturing extend CNC’s capabilities, pushing boundaries in design complexity and material diversity.
In conclusion, CNC programming stands as a cornerstone of modern manufacturing, driving efficiency, precision, and innovation across diverse industries. As technology evolves, CNC continues to expand its applications, solidifying its role in shaping the future of production.
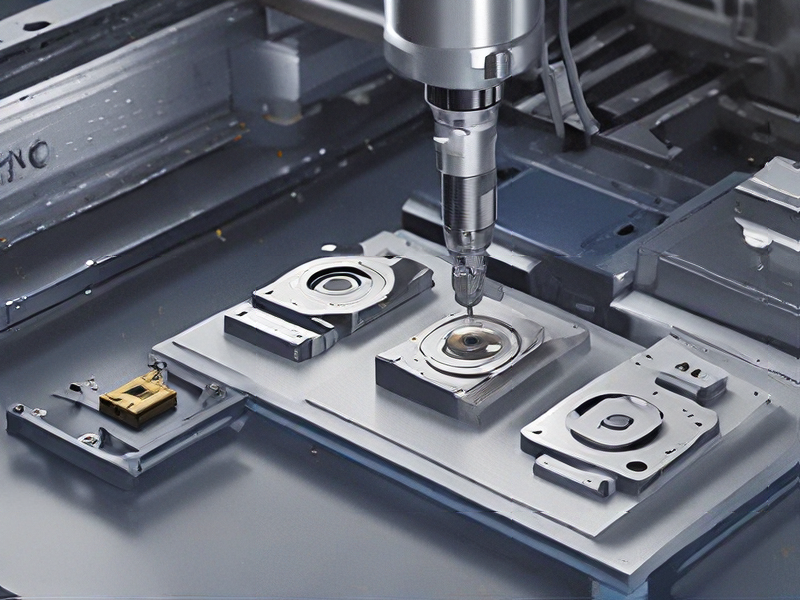
Quality Testing Methods for cnc program and how to control quality
Quality testing methods for CNC (Computer Numerical Control) programs involve several key practices to ensure accuracy and reliability:
1. Simulation and Verification: Utilize CNC simulation software to preview toolpaths and simulate machining operations. This helps detect errors in toolpath generation and ensures that the program behaves as intended.
2. Dimensional Inspection: After machining, perform dimensional inspections using coordinate measuring machines (CMMs) or other measuring tools to verify part dimensions against CAD specifications.
3. Tool Path Analysis: Analyze tool paths to ensure they are efficient and minimize machining time while adhering to safety and quality standards. This involves checking for smooth transitions between tool moves and avoiding collisions.
4. Post-Processor Verification: Validate the output of the post-processor to ensure it correctly translates the CAM (Computer-Aided Manufacturing) system’s output into machine-readable G-code.
5. Documentation and Version Control: Maintain thorough documentation of CNC programs and revisions. Implement version control practices to track changes and ensure that only approved programs are used in production.
6. Operator Training and Qualification: Ensure CNC operators are trained in program verification techniques and understand the importance of quality control in CNC machining processes.
By implementing these methods, manufacturers can effectively control the quality of CNC programs, minimize errors, and optimize production processes to deliver accurate and reliable machined parts.
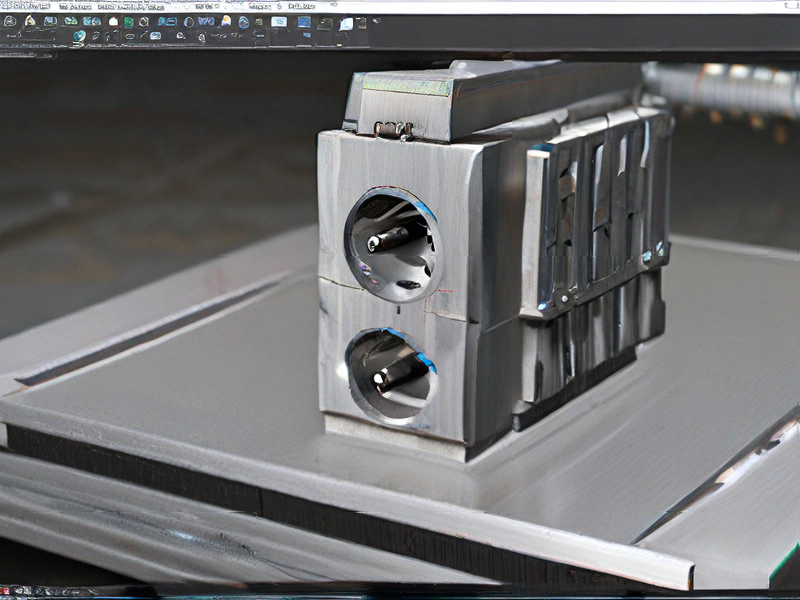
Tips for Procurement and Considerations when Purchasing from cnc program
When purchasing CNC (Computer Numerical Control) programs, consider the following tips and key considerations:
1. Quality and Compatibility: Ensure the program is compatible with your CNC machine and meets your quality standards. Check if it supports the file formats and specifications required by your equipment.
2. Supplier Reputation: Choose reputable suppliers with a track record of delivering reliable CNC programs. Look for reviews, testimonials, or recommendations from other users to gauge their reliability.
3. Functionality and Features: Evaluate the program’s features and functionalities. Does it offer the capabilities needed for your specific machining operations? Consider aspects like toolpath optimization, simulation capabilities, and ease of customization.
4. Support and Updates: Check if the supplier provides technical support, training, and regular updates for the CNC program. This ensures you can resolve issues quickly and stay updated with advancements in machining technology.
5. Cost and Value: Compare prices from different suppliers while considering the value offered. Avoid opting solely for the cheapest option; instead, prioritize programs that provide the best balance of functionality, support, and long-term cost-effectiveness.
6. Security and License: Ensure the CNC program comes with proper licensing and security measures to protect your data and comply with legal requirements.
7. Trial and Testing: Whenever possible, request a trial or demo version of the CNC program. This allows you to test its functionality and compatibility with your equipment before making a purchase decision.
8. User Interface and Ease of Use: Consider the user interface of the CNC program. A user-friendly interface can reduce training time for operators and improve overall productivity.
9. Integration with CAD/CAM Software: If you use CAD/CAM software, check compatibility and integration capabilities with the CNC program to streamline workflow and data transfer.
10. Future Expansion: Consider your future needs and whether the CNC program can scale with your business as it grows. Look for flexibility and scalability in terms of features and licensing.
By carefully evaluating these factors, you can make an informed decision when purchasing CNC programs, ensuring they meet your operational requirements and deliver value over the long term.
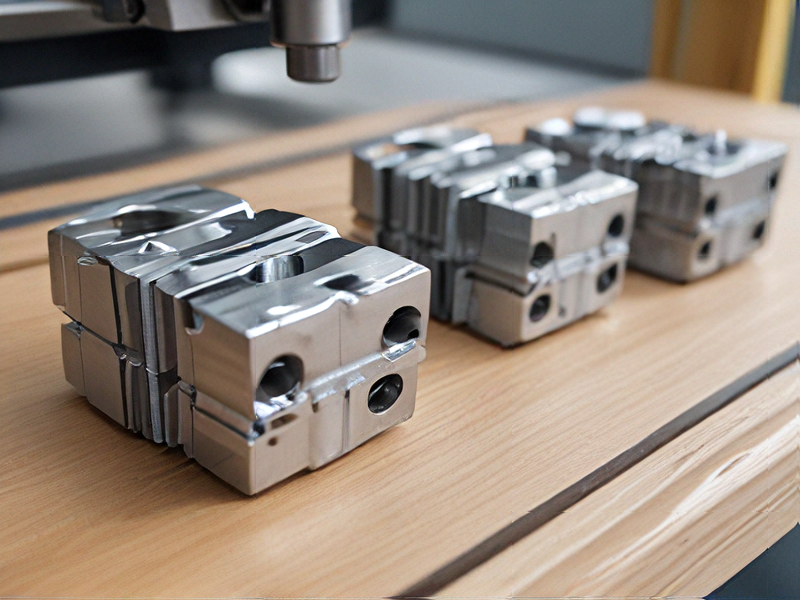
FAQs on Sourcing and Manufacturing from cnc program in China
Certainly! Here are some FAQs regarding sourcing and manufacturing from CNC programs in China:
1. What types of CNC machining services are commonly available in China?
– Chinese manufacturers offer a wide range of CNC machining services including milling, turning, drilling, and precision grinding, among others.
2. How can I find reliable CNC manufacturers in China?
– Research online directories, attend trade shows, and seek recommendations from industry contacts. Verify certifications and visit facilities if possible.
3. What are the typical lead times for CNC machining projects in China?
– Lead times vary based on complexity and quantity, but generally range from a few days to several weeks. Communication with suppliers about timelines is crucial.
4. What quality standards should I expect from Chinese CNC manufacturers?
– Reputable manufacturers adhere to international standards such as ISO 9001. Request samples and conduct quality inspections before finalizing orders.
5. How do I manage language and communication barriers with Chinese suppliers?
– Use translators or hire bilingual staff. Clearly document specifications and expectations in writing to minimize misunderstandings.
6. What are the considerations for intellectual property protection when sourcing from China?
– Sign non-disclosure agreements (NDAs) and protect designs through patents or trademarks where applicable. Work with reputable manufacturers with good IP protection policies.
7. What are the payment terms typically used with Chinese CNC manufacturers?
– Payment terms often include a deposit upfront with the balance due upon completion or shipment. Negotiate terms that align with project milestones and risks.
8. How can I ensure consistent quality and reliability in CNC manufacturing from China?
– Establish long-term relationships with trusted suppliers. Conduct regular quality audits and maintain open communication to address any issues promptly.
By addressing these FAQs, you can better navigate sourcing and manufacturing through CNC programs in China, ensuring smoother processes and outcomes for your projects.
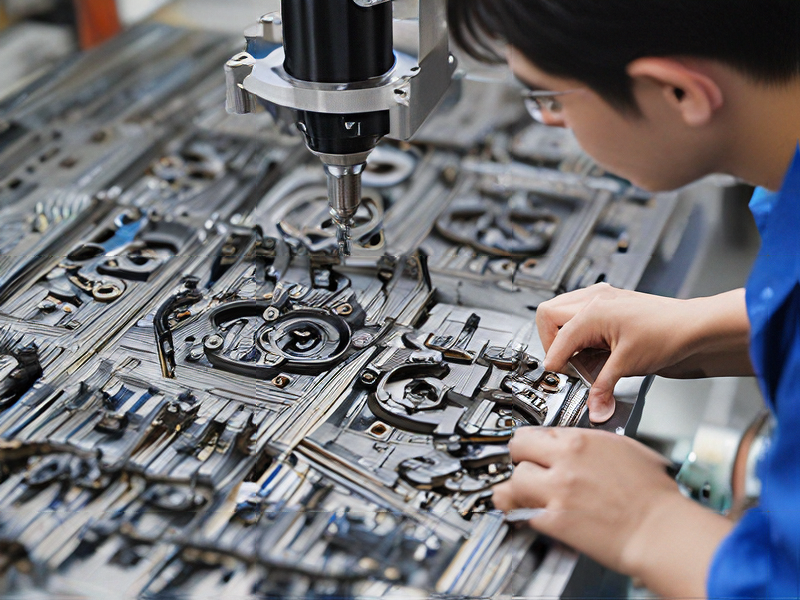