Technology and Applications of cnc programmes
Computer Numerical Control (CNC) programs revolutionize manufacturing by automating machine tool operations. These programs use a sequence of instructions written in a language like G-code to dictate the movements and actions of CNC machines. By converting designs from Computer-Aided Design (CAD) software into executable commands, CNC programs ensure precise and repeatable manufacturing processes across various industries.
Key applications include:
1. Precision Machining: CNC programs control milling, turning, drilling, and grinding operations with high accuracy, making them essential in producing complex components for aerospace, automotive, and medical sectors.
2. Mass Production: They enable consistent production of identical parts, enhancing efficiency and reducing labor costs compared to manual machining.
3. Prototyping: Rapid prototyping allows designers to quickly iterate and refine designs before full-scale production, speeding up product development cycles.
4. Customization: CNC machines can easily switch between different programs, facilitating customized production runs tailored to specific customer requirements.
5. Automation: Integration with robotics and automated material handling systems further enhances productivity and reduces human intervention, improving overall manufacturing efficiency.
6. Complex Geometries: CNC programs handle intricate geometries and surface finishes that are challenging or impossible to achieve manually.
Technological advancements in CNC programming include real-time monitoring, simulation, and optimization software, enhancing machine utilization and reducing downtime. Future trends involve the integration of AI for predictive maintenance, adaptive control, and even more sophisticated part inspection and quality control. CNC programs continue to drive innovation in manufacturing, offering flexibility, precision, and scalability across a wide range of industrial applications.
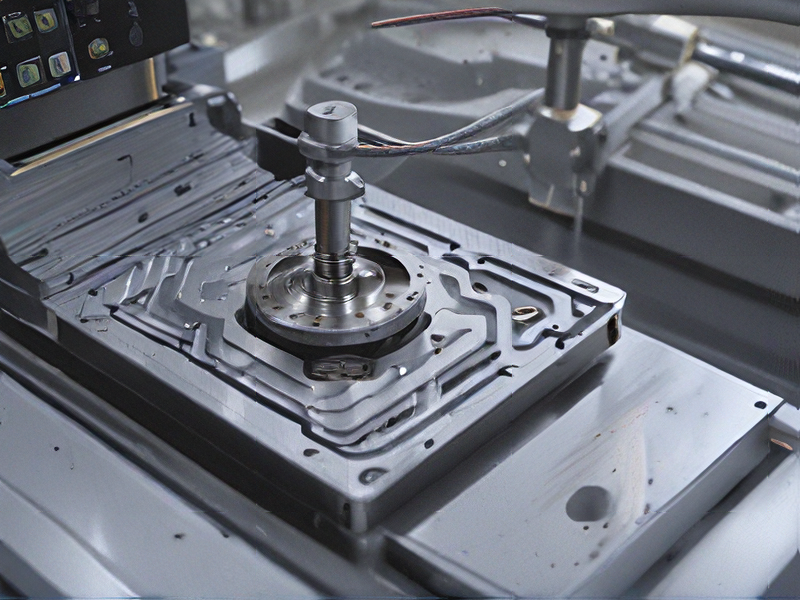
Quality Testing Methods for cnc programmes and how to control quality
Quality testing methods for CNC programs involve several key practices to ensure accuracy and reliability:
1. Simulation and Verification: Utilize CNC simulation software to validate the program’s behavior and detect potential errors in toolpaths, dimensions, and tool collisions before actual machining.
2. First Article Inspection (FAI): Conduct a physical inspection of the first produced part to verify that it meets design specifications. This helps catch discrepancies early in the manufacturing process.
3. Dimensional Inspection: Use precision measuring tools like calipers, micrometers, and coordinate measuring machines (CMMs) to verify critical dimensions against engineering drawings.
4. Tool Wear and Life Monitoring: Implement systems to monitor tool wear and track tool life. This ensures that tools are replaced or re-sharpened at the appropriate intervals to maintain quality.
5. Process Capability Analysis: Perform statistical analysis such as Cp, Cpk to assess the capability of the CNC machining process to consistently produce parts within specified tolerances.
To control quality effectively:
– Document Control: Maintain up-to-date CNC programs and associated documentation, including revision control to ensure only approved versions are used.
– Training and Skills: Provide comprehensive training for CNC operators and programmers to ensure they understand quality requirements and can identify potential issues.
– Regular Maintenance: Implement a preventive maintenance program for CNC machines to minimize variability and ensure consistent performance.
– Feedback Loops: Establish feedback mechanisms from inspection results and production feedback to continuously improve CNC programs and machining processes.
By integrating these methods and controls, manufacturers can uphold high standards of quality in CNC machining processes, minimizing errors and optimizing productivity.
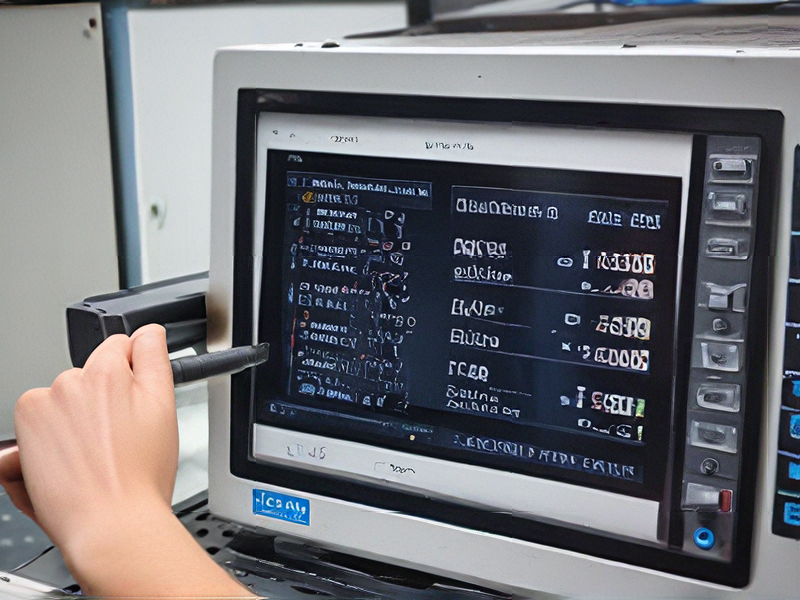
Tips for Procurement and Considerations when Purchasing from cnc programmes
When procuring CNC programs, several considerations are crucial for ensuring efficiency and effectiveness:
1. Quality Assurance: Verify the CNC program’s accuracy and functionality through testing and simulations to ensure it meets production requirements without errors.
2. Supplier Reputation: Choose reputable suppliers or programmers with proven experience and positive reviews to minimize risks and ensure reliable support.
3. Customization Needs: Determine if the CNC program can be customized or tailored to specific manufacturing processes or equipment to optimize performance.
4. Security and Intellectual Property: Ensure that the CNC programs adhere to security protocols to protect intellectual property and prevent unauthorized access or modifications.
5. Cost Efficiency: Evaluate costs not only for initial procurement but also for maintenance, updates, and support to determine the overall cost-effectiveness.
6. Compatibility: Ensure compatibility with existing CNC machines, software, and operational systems to avoid integration issues and maximize operational continuity.
7. Support and Training: Verify the availability of technical support and training resources from the supplier to facilitate smooth implementation and troubleshooting.
8. Scalability: Consider future scalability needs by selecting programs that can accommodate increasing production demands or technological advancements.
9. Documentation: Request comprehensive documentation and manuals to aid in understanding and maintaining the CNC programs effectively.
10. Legal Considerations: Review and negotiate contracts to clarify terms regarding warranties, liabilities, and rights to updates or modifications.
By prioritizing these considerations, businesses can streamline procurement processes and leverage CNC programs effectively to enhance manufacturing capabilities.
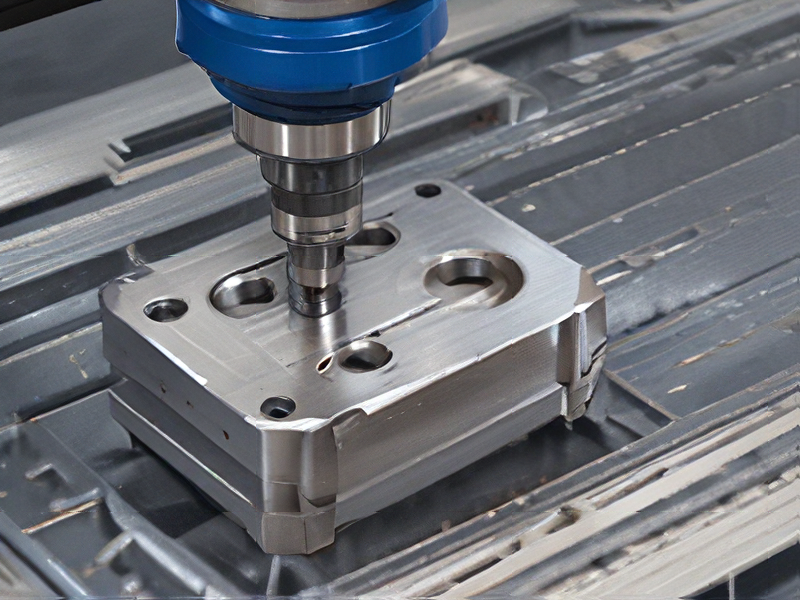
FAQs on Sourcing and Manufacturing from cnc programmes in China
Certainly! Here are some FAQs regarding sourcing and manufacturing from CNC programs in China:
1. What is CNC programming?
CNC (Computer Numerical Control) programming involves creating instructions for automated machinery to produce precise parts and components.
2. Why consider sourcing from China?
China offers competitive pricing due to lower labor costs and established manufacturing infrastructure, making it attractive for CNC production.
3. How to find reliable CNC manufacturers in China?
Utilize online platforms, industry networks, and referrals to identify manufacturers with proven track records, certifications, and quality assurance processes.
4. What are common challenges in sourcing from China?
Challenges include language barriers, cultural differences, quality control issues, and logistics management.
5. How to ensure quality when sourcing CNC programs from China?
Conduct thorough supplier audits, request samples, define clear specifications, and implement quality control checks throughout production.
6. What are typical lead times for CNC manufacturing in China?
Lead times vary based on complexity and volume but generally range from a few weeks to several months.
7. What intellectual property considerations should be addressed?
Implement non-disclosure agreements (NDAs), protect designs with patents or trademarks, and carefully manage sharing of CAD files and technical specifications.
8. How can I manage logistics and shipping from China?
Partner with experienced freight forwarders, clarify incoterms, and stay informed about import regulations and customs duties.
9. What are the payment terms commonly used with Chinese manufacturers?
Negotiate payment terms like Letter of Credit (LC), Telegraphic Transfer (T/T), or use secure platforms to mitigate payment risks.
10. What are emerging trends in CNC manufacturing in China?
Trends include automation with AI and robotics, sustainable manufacturing practices, and advancements in precision machining technologies.
These FAQs provide a foundational understanding for businesses looking to leverage CNC manufacturing capabilities in China while addressing key considerations for successful sourcing and production management.
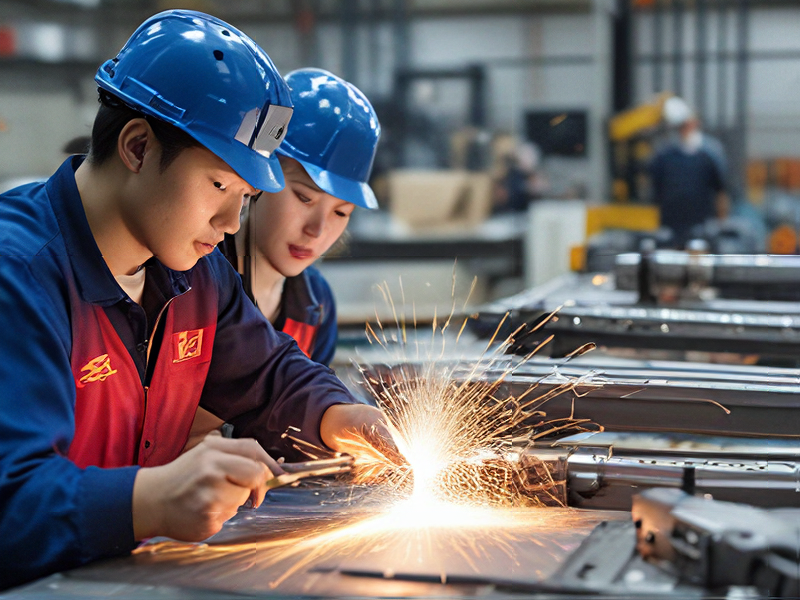