Technology and Applications of cnc programs
Computer Numerical Control (CNC) programs revolutionize manufacturing by automating machine tools through coded instructions. These programs utilize G-code, a standardized language that directs the movement and operation of CNC machines such as mills, lathes, and routers. By converting designs from CAD software into G-code, CNC programs ensure precise and repeatable production of complex parts with minimal human intervention.
Key applications of CNC programs span various industries:
1. Manufacturing: CNC machines fabricate components with high accuracy, improving quality control and production efficiency in industries like automotive, aerospace, and electronics.
2. Prototyping: Rapid prototyping benefits from CNC’s ability to swiftly translate digital designs into physical models, facilitating iterative testing and refinement.
3. Customization: CNC enables customization of products such as furniture, signage, and medical implants, catering to specific client requirements efficiently.
4. Mass Production: For mass-produced items like smartphone components or packaging materials, CNC ensures uniformity and consistency in large-scale manufacturing.
Technological advancements in CNC programming include:
– Multi-axis Machining: CNC machines with multiple axes allow complex geometries and contours to be machined in a single setup, reducing production time and enhancing accuracy.
– High-speed Machining: Improved tooling and machine capabilities enable faster material removal rates without compromising precision, crucial for time-sensitive production environments.
– Integration with CAD/CAM: Seamless integration between Computer-Aided Design (CAD) and Computer-Aided Manufacturing (CAM) software streamlines the CNC programming workflow, from design conception to final production.
In summary, CNC programs leverage advanced technology to enhance manufacturing capabilities across diverse sectors, enabling cost-effective production, rapid prototyping, and intricate customization of products.
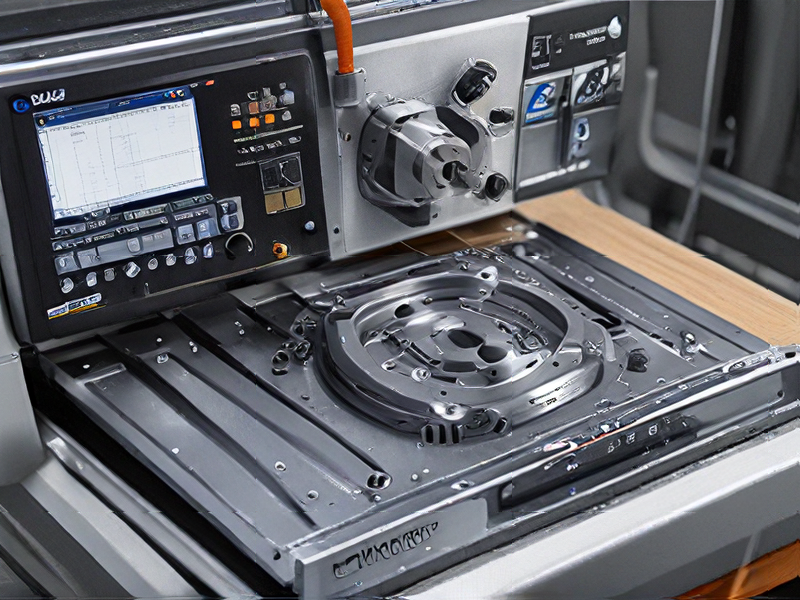
Quality Testing Methods for cnc programs and how to control quality
Quality testing methods for CNC programs involve several key approaches:
1. Simulation and Verification: Utilize CNC simulation software to run the program virtually. This ensures the toolpaths, speeds, and feeds are correct without risking machine or material damage.
2. Dry Run on Machine: Before actual machining, perform a dry run with the CNC machine to check for any unexpected movements or errors in toolpaths. This helps identify potential issues early.
3. Tooling and Material Checks: Ensure the correct tools and materials are loaded into the machine as specified in the program. Verify tool dimensions, sharpness, and material characteristics to prevent errors during machining.
4. Dimensional Inspection: After machining, use precision measurement tools like calipers, micrometers, or coordinate measuring machines (CMMs) to verify part dimensions against design specifications.
5. Statistical Process Control (SPC): Implement SPC techniques to monitor process variability and ensure consistency in production. This involves collecting data from machining processes to detect trends and prevent defects.
6. Documentation and Version Control: Maintain accurate documentation of CNC programs and revisions. Implement version control to ensure that only approved and validated programs are used in production.
By combining these methods, manufacturers can effectively control the quality of CNC programs and ensure that machined parts meet required specifications reliably.
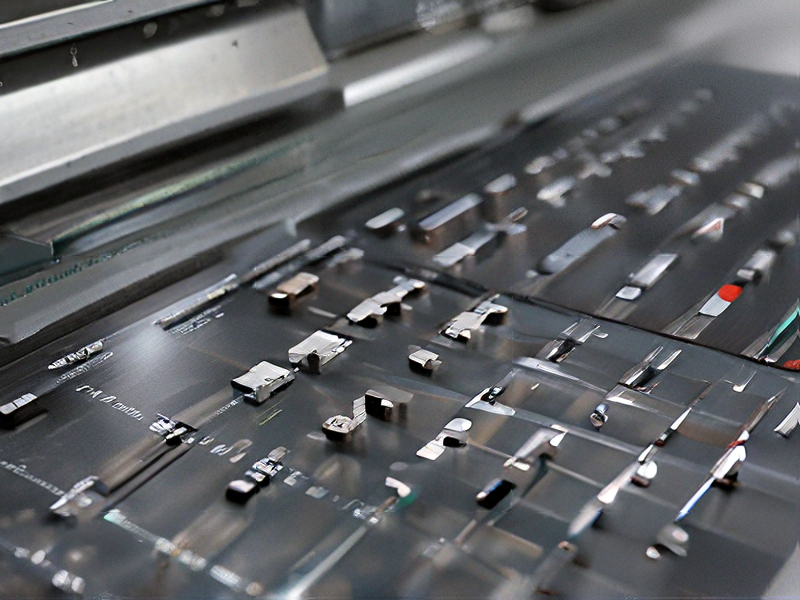
Tips for Procurement and Considerations when Purchasing from cnc programs
When procuring CNC programs, consider the following tips and considerations:
1. Quality Assurance: Ensure the CNC programs are from reputable sources or developed by skilled programmers to avoid errors that could lead to costly mistakes during machining.
2. Compatibility: Verify compatibility with your specific CNC machine model and control system to ensure seamless integration and optimal performance.
3. Customization Needs: Assess whether the programs can be easily customized or adapted to meet specific machining requirements or to accommodate unique materials and geometries.
4. Version Control: Maintain proper version control to track revisions and updates, ensuring you are using the latest and most reliable CNC programs available.
5. Security and Confidentiality: Protect intellectual property rights and ensure confidentiality by acquiring programs from trusted suppliers and implementing secure data handling practices.
6. Training and Support: Consider the availability of training and technical support from the program provider to assist your operators in effectively using and troubleshooting the CNC programs.
7. Cost and ROI: Evaluate the overall cost of acquiring the CNC programs against the potential return on investment, factoring in reduced setup times, improved accuracy, and enhanced productivity.
By focusing on these aspects, you can streamline the procurement process and maximize the benefits of using CNC programs in your manufacturing operations.
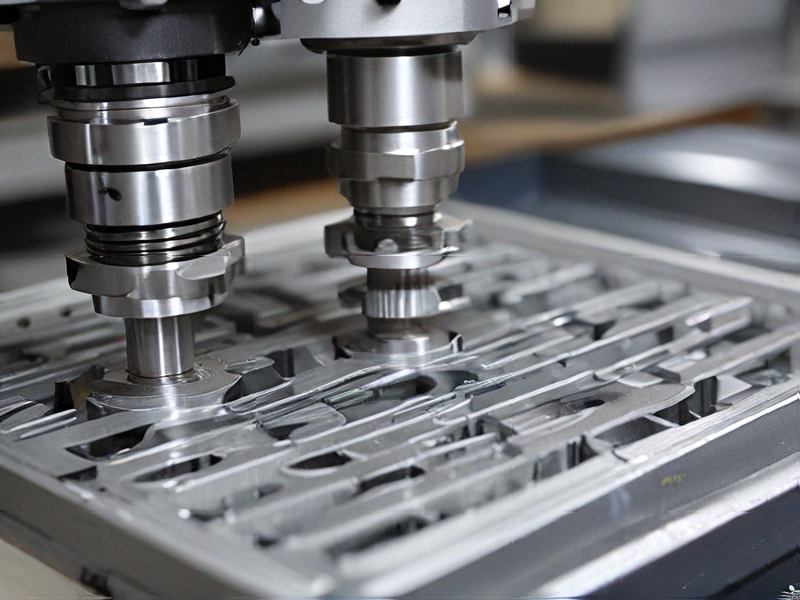
FAQs on Sourcing and Manufacturing from cnc programs in China
Certainly! Here are some FAQs on sourcing and manufacturing from CNC programs in China:
1. What types of CNC machining services are available in China?
China offers a wide range of CNC machining services, including milling, turning, drilling, and grinding. Specialized processes like EDM (Electrical Discharge Machining) are also commonly available.
2. How can I find a reliable CNC machining supplier in China?
Look for suppliers with certifications like ISO 9001, which ensure quality management systems. Reading reviews and obtaining referrals can also help gauge reliability.
3. What are the typical lead times for CNC machined parts from China?
Lead times vary depending on complexity and quantity, but they typically range from a few days to a few weeks. Factors like material availability and finishing requirements can affect lead times.
4. Are there language barriers when communicating CNC specifications?
While language barriers can exist, many Chinese suppliers have English-speaking staff or use translators. Clear documentation and drawings can also mitigate communication issues.
5. How do I ensure quality control when manufacturing CNC parts in China?
Specify quality requirements in detail, conduct inspections during production, and consider third-party quality assurance services if needed. Requesting samples before mass production is also advisable.
6. What are the payment terms usually accepted by Chinese CNC machining suppliers?
Common payment terms include T/T (Telegraphic Transfer), PayPal, and Alibaba Trade Assurance. Negotiate terms that balance payment security with supplier expectations.
7. What should I consider when choosing between domestic and Chinese CNC suppliers?
Cost-effectiveness, production capacity, and expertise in specific machining processes are key factors. Chinese suppliers often offer competitive pricing but require careful due diligence.
By addressing these FAQs, you can navigate sourcing and manufacturing from CNC programs in China more effectively.
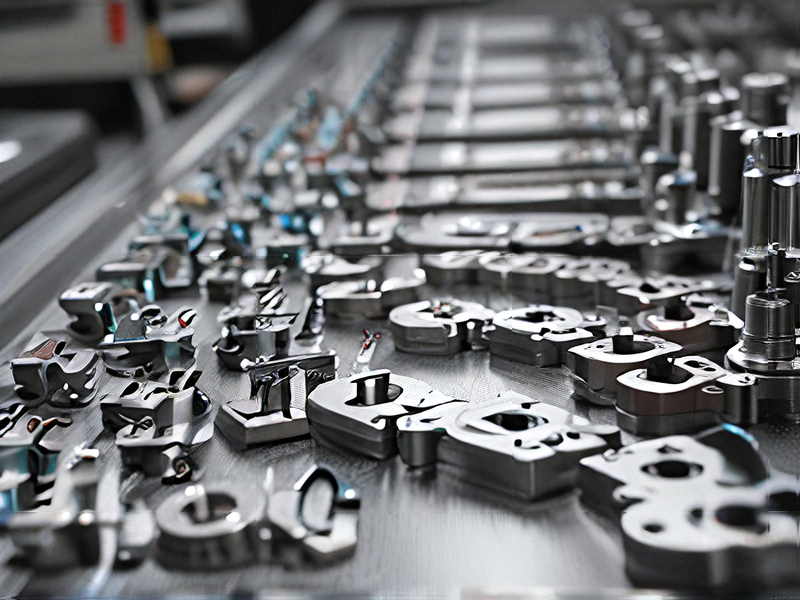