Technology and Applications of cnc routing
CNC (Computer Numerical Control) routing is a precision manufacturing process that employs computer-controlled routers to cut, shape, and engrave materials such as wood, plastic, and metal. This technology has revolutionized industries by enhancing accuracy, efficiency, and repeatability in production.
Technology: CNC routers utilize a combination of hardware and software. The core components include a computer, a motion control system, and a router or spindle. Users design parts using CAD (Computer-Aided Design) software, which the CNC machine translates into G-code—a language that instructs the router on axis movements, feed rates, and tool paths. These machines can range from simple 2D devices to advanced 3D models capable of intricate designs.
Applications: CNC routing has diverse applications across multiple sectors. In woodworking, it’s used for furniture making, cabinetry, and decorative elements. The signage industry leverages CNC routing for custom signs and letters, promoting precision and unique designs. In the manufacturing sector, CNC routers fabricate parts for automotive, aerospace, and electronics industries, ensuring tight tolerances and high production rates. The technology is also prevalent in art and design, allowing artists to create precise sculptures and installations.
CNC routing’s ability to streamline processes and reduce material waste makes it an invaluable tool in modern manufacturing. As the technology continues to evolve, its applications are expanding, incorporating advancements like automation and smart manufacturing, paving the way for future innovations in design and production.
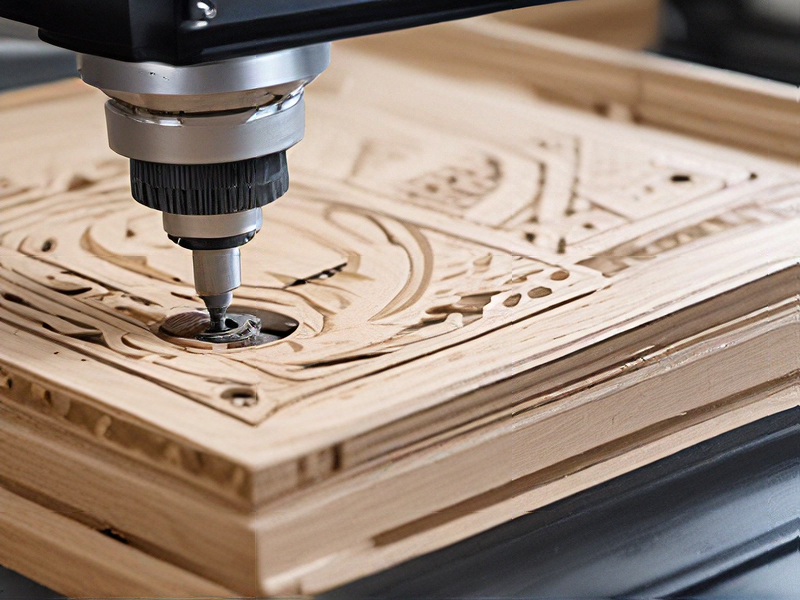
Quality Testing Methods for cnc routing and how to control quality
Quality testing in CNC routing is vital to ensure precision, accuracy, and surface finish. Here are several effective methods and strategies for controlling quality:
1. Dimensional Inspection: Utilize calipers and micrometers to measure critical dimensions of the machined part. Comparing these measurements against CAD models helps identify any deviations.
2. Visual Inspection: Conduct visual checks for surface defects, rough edges, or discoloration. This can be done under standard lighting to ensure clarity.
3. CMM (Coordinate Measuring Machine): For high-precision requirements, CMMs can be used to automate dimensional checks, capturing data points from the part’s surface to compare against the desired specifications.
4. Functional Testing: Depending on the part’s application, perform functional tests to ensure it fits correctly with other components. This is especially important for assembly-critical applications.
5. Tooling Assessment: Regularly inspect and maintain cutting tools. Dull or damaged tools can lead to poor surface finishes and dimensional inaccuracies.
6. Calibration: Keep all measuring instruments and CNC machines properly calibrated. This ensures continual accuracy over time.
7. Process Control: Implement statistical process control (SPC) by collecting data on key parameters (e.g., feed rate, spindle speed) and analyzing trends to prevent defects before they occur.
8. Quality Control Checklists: Develop checklists tailored to your production processes to methodically review each stage of CNC routing.
9. Operator Training: Ensure all operators are well-trained in CNC machine operation and quality standards. A knowledgeable operator can significantly enhance quality control.
By integrating these methods, manufacturers can ensure consistent quality in CNC routing, minimizing defects and maximizing efficiency.
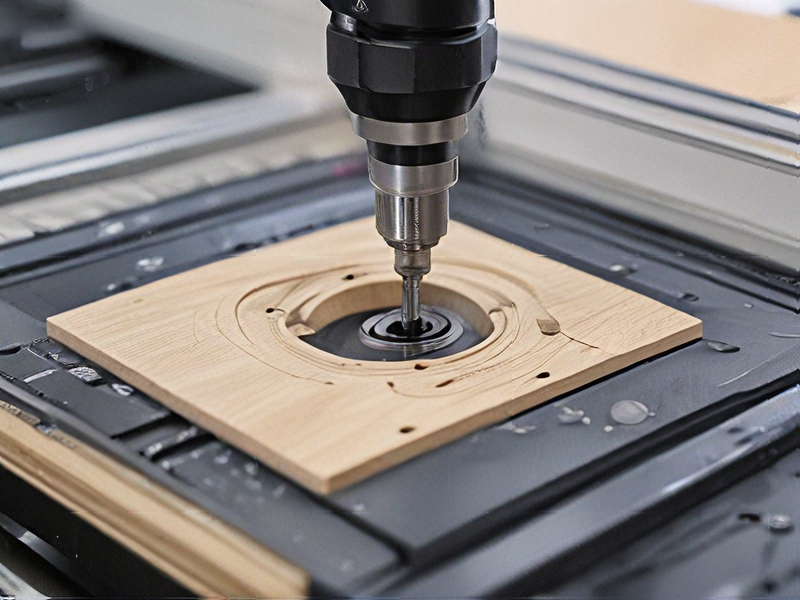
Tips for Procurement and Considerations when Purchasing from cnc routing
When procuring CNC routing services or equipment, several key considerations can help ensure a successful purchase:
1. Define Your Needs: Clearly outline the specifications of your project. Consider material types, dimensions, tolerances, and production volume. A precise understanding of your requirements helps select appropriate machinery or service providers.
2. Research Providers: Look for suppliers with a strong reputation and relevant industry experience. Check reviews, case studies, and customer testimonials. Networking or seeking referrals from industry peers can provide valuable insights.
3. Quality Assurance: Ensure that the provider adheres to quality standards, such as ISO certifications. Inquire about their quality control processes and ask for samples of their previous work to assess quality.
4. Technical Support and Training: Choose a supplier that offers comprehensive technical support and training for their equipment. Being able to access assistance can be crucial for overcoming initial operational challenges.
5. Cost Considerations: While it’s tempting to choose the lowest bid, consider total cost of ownership. This includes not just the purchase price, but ongoing maintenance, material costs, and potential downtime.
6. Lead Times and Flexibility: Discuss lead times upfront to ensure they align with your project timeline. Ask about the provider’s flexibility to accommodate changes in your order or production schedule.
7. Post-Purchase Support: Verify what kind of after-sales service is provided, including spare parts availability and technical assistance.
By carefully considering these factors, you can make informed procurement decisions for CNC routing services or equipment, ultimately leading to enhanced productivity and quality in your projects.
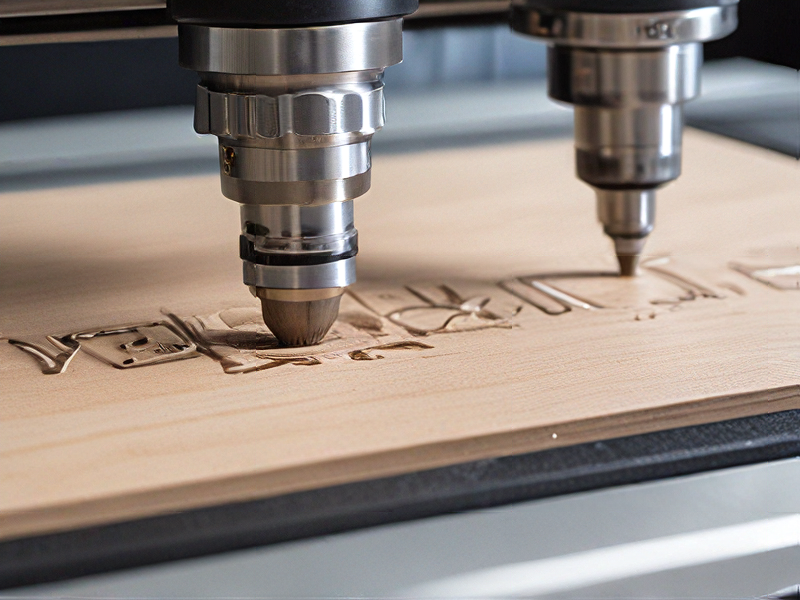
FAQs on Sourcing and Manufacturing from cnc routing in China
FAQs on Sourcing and Manufacturing CNC Routing in China
1. What is CNC routing?
CNC routing is a computer-controlled cutting process that utilizes a router to create detailed shapes and designs from various materials, including wood, plastic, and metal.
2. Why source CNC routing services from China?
China offers competitive pricing, a wide range of materials, skilled labor, and advanced technology, making it an attractive option for manufacturers seeking cost-effective solutions.
3. How do I find a reliable CNC routing manufacturer in China?
Research potential suppliers through platforms such as Alibaba, Made-in-China, or industry trade shows. Check their certifications, customer reviews, and request samples to assess quality.
4. What are the typical lead times for CNC routing projects?
Lead times can vary based on complexity and order size but typically range from 2 to 6 weeks. Always confirm timelines with your supplier before placing an order.
5. What minimum order quantities (MOQs) should I expect?
MOQs can differ by manufacturer; some may accept orders as low as 10 units, while others may require hundreds. Discuss your needs upfront to find a suitable partner.
6. How can I ensure quality control?
Implement quality checks throughout the manufacturing process. Request photos, specifications, and if possible, conduct factory audits. Third-party inspection services can also be useful.
7. What materials can be used in CNC routing?
Common materials include plywood, MDF, acrylic, aluminum, and even exotic woods. Discuss your project needs with the manufacturer to confirm material availability.
8. Are there any tariffs or duties when importing from China?
Yes, customs duties and tariffs may apply depending on your country’s regulations. Consult with a customs broker for specific details.
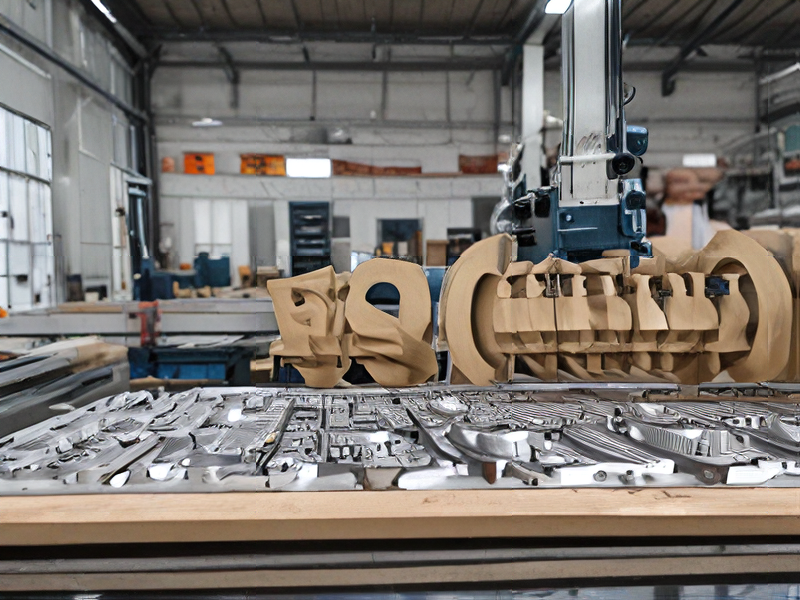