Technology and Applications of cnc routing machine
CNC (Computer Numerical Control) routing machines are pivotal in modern manufacturing and fabrication due to their precision and versatility. These machines use computer-controlled movements to carve out designs from various materials such as wood, plastics, metals, and composites.
Technology:
CNC routers operate based on CAD (Computer-Aided Design) files that specify the desired dimensions and shapes. The machine interprets these instructions to precisely position the cutting tool along multiple axes (typically three or more). High-precision stepper motors or servo motors drive these axes, ensuring accuracy down to fractions of a millimeter. Spindle motors with variable speeds accommodate different materials and cutting requirements. Advanced models may incorporate automatic tool changers, enhancing efficiency by reducing manual intervention.
Applications:
1. Woodworking: CNC routers excel in crafting furniture, cabinetry, and decorative woodwork. They automate intricate designs, from ornate patterns to custom joinery.
2. Plastics and Composites: Used in manufacturing components for aerospace, automotive, and marine industries. CNC routers precisely cut panels, molds, and prototypes from materials like acrylics, fiberglass, and carbon fiber.
3. Metal Fabrication: Though less common than in woodworking, CNC routers equipped with appropriate tools can cut and shape aluminum, brass, and other softer metals for signage, molds, and structural components.
4. Prototyping and Rapid Manufacturing: Rapid prototyping benefits from CNC routers’ ability to quickly translate digital designs into physical prototypes with minimal setup time.
5. Art and Signage: From sculptures to detailed signs, CNC routers enable artists and fabricators to produce intricate, repeatable designs efficiently.
6. Education and DIY Projects: Entry-level CNC routers serve educational purposes and empower hobbyists to create custom items ranging from model kits to personalized gifts.
In essence, CNC routing machines leverage precision and automation to streamline manufacturing across various industries, from large-scale production to bespoke craftsmanship. Their adaptability continues to expand as technology advances, offering new possibilities for design and production efficiency.
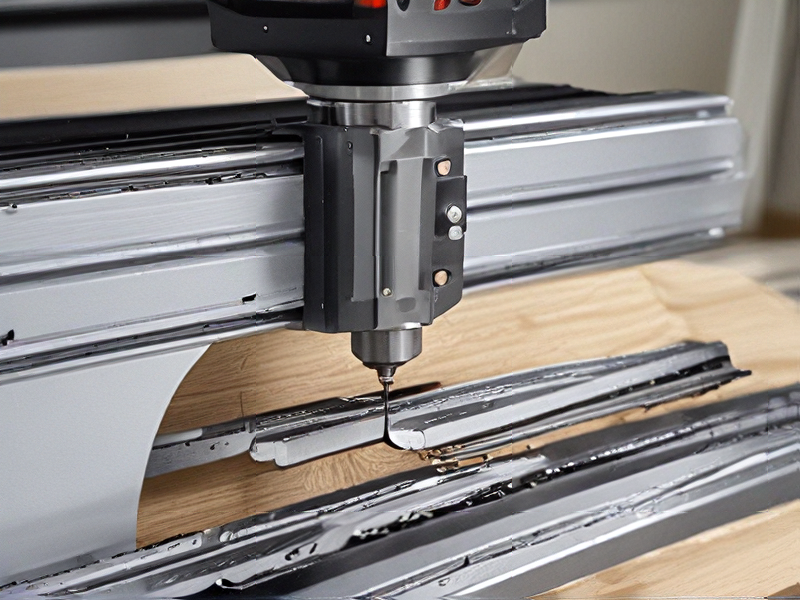
Quality Testing Methods for cnc routing machine and how to control quality
Quality testing methods for CNC routing machines typically include several key approaches to ensure precision and reliability of output:
1. Dimensional Accuracy Checks: Utilizing precision measuring tools such as calipers, micrometers, or coordinate measuring machines (CMMs) to verify dimensions against design specifications.
2. Surface Finish Evaluation: Assessing the quality of surface finishes using visual inspection, profilometers, or surface roughness testers to ensure smoothness and adherence to required standards.
3. Tool Performance Monitoring: Regularly monitoring tool wear and performance through tool life management systems or periodic inspection to maintain cutting accuracy.
4. Material Testing: Conducting material tests to verify material properties such as hardness, tensile strength, and thermal conductivity, ensuring compatibility with machine capabilities.
5. Runout and Alignment Checks: Checking spindle runout and machine alignment using dial indicators or laser alignment tools to ensure concentricity and perpendicularity.
To control quality effectively:
– Establish Standard Operating Procedures (SOPs): Documenting step-by-step procedures for machine setup, operation, maintenance, and inspection ensures consistency.
– Implement Regular Calibration: Calibrating machines and measuring instruments at scheduled intervals to maintain accuracy and reliability.
– Training and Skill Development: Providing training for operators on machine operation, maintenance, and quality control procedures enhances competency and reduces errors.
– Continuous Monitoring and Improvement: Implementing a system for continuous monitoring of quality metrics and feedback mechanisms for identifying areas of improvement.
By integrating these methods and controls, CNC routing machine operators can uphold stringent quality standards, minimize production errors, and enhance overall product quality and reliability.
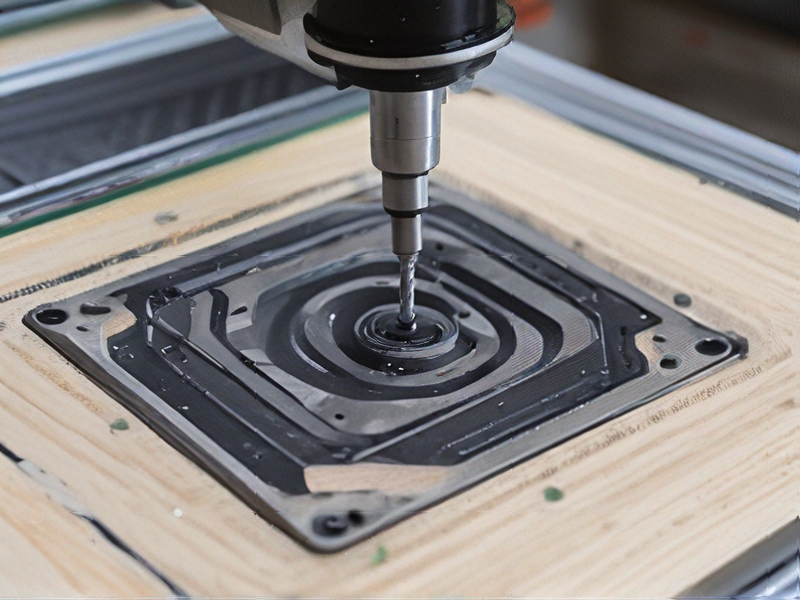
Tips for Procurement and Considerations when Purchasing from cnc routing machine
When procuring a CNC routing machine, consider these tips and key considerations:
1. Machine Specifications: Understand your production needs—such as cutting area size, spindle power, and material compatibility—to choose a machine that meets these requirements effectively.
2. Accuracy and Precision: Look for machines with high-resolution stepper or servo motors and rigid construction for precise cutting and consistent performance.
3. Software Compatibility: Ensure the CNC machine is compatible with your existing CAD/CAM software to streamline workflow and reduce setup time.
4. Maintenance and Support: Research the manufacturer’s reputation for customer support, availability of spare parts, and ease of maintenance to minimize downtime.
5. Safety Features: Prioritize machines equipped with safety interlocks, emergency stops, and proper guarding to protect operators and comply with safety standards.
6. Cost and ROI: Evaluate the total cost of ownership, including initial purchase price, operating costs, and potential return on investment based on increased productivity and capabilities.
7. User Interface and Ease of Use: Choose a machine with an intuitive interface and user-friendly controls to reduce training time and optimize production efficiency.
8. Reviews and Recommendations: Seek feedback from industry peers and reviews online to gauge reliability, performance, and overall satisfaction with specific machine models.
9. Future Expansion: Consider scalability and flexibility—choose a machine that allows for future upgrades or expansion of capabilities as your business grows.
10. Supplier Reputation: Select a reputable supplier or manufacturer with a proven track record in delivering quality CNC machines and reliable customer service.
By carefully considering these factors, you can make an informed decision when purchasing a CNC routing machine that best fits your operational needs and long-term business goals.
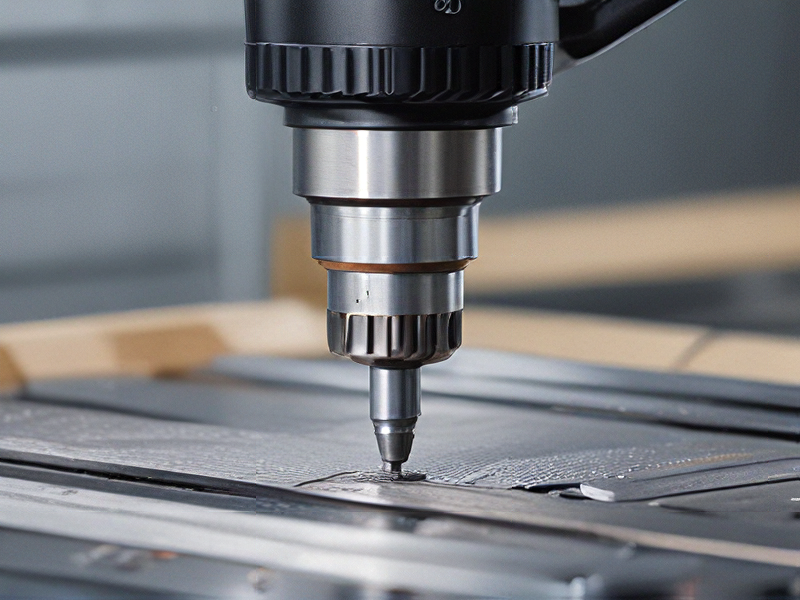
FAQs on Sourcing and Manufacturing from cnc routing machine in China
When sourcing from a CNC routing machine manufacturer in China, several key FAQs typically arise:
1. Quality Assurance: Ensure the manufacturer adheres to international quality standards like ISO. Request samples or visit their facilities if possible.
2. Cost and Pricing: Understand the pricing structure, including unit costs, shipping fees, and any potential tariffs or taxes. Negotiate terms that suit your budget.
3. Lead Times: Clarify production lead times and shipping durations to manage expectations and plan inventory effectively.
4. Communication: Establish clear lines of communication, preferably in writing, to address any issues promptly.
5. Customization: Inquire about the ability to customize machine specifications, software integration, and after-sales support.
6. Certifications and Compliance: Verify the CNC machine complies with relevant industry regulations and certifications.
7. Warranty and Support: Seek information on warranties, technical support availability, and spare parts accessibility.
8. Payment Terms: Discuss payment methods, schedules, and terms to ensure transparency and security.
9. Logistics and Shipping: Confirm shipping methods, packaging standards, and insurance coverage during transit.
10. References and Reviews: Request references from previous clients or check online reviews to gauge customer satisfaction and reliability.
By addressing these FAQs with potential CNC routing machine suppliers in China, you can make informed decisions and mitigate risks associated with sourcing and manufacturing processes.
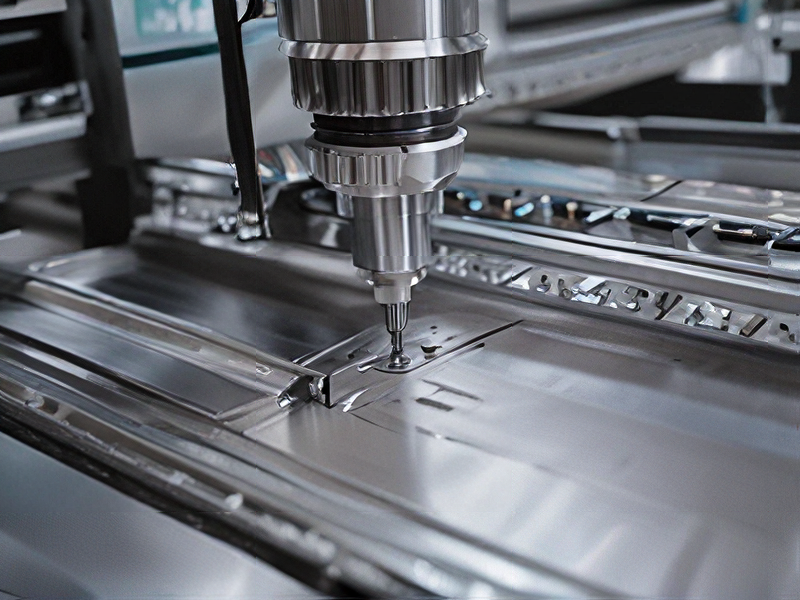