Technology and Applications of cnc wood cutting machines
CNC (Computer Numerical Control) wood cutting machines have revolutionized woodworking by enhancing precision, efficiency, and versatility in manufacturing processes. These machines operate based on digital instructions, translating computer-aided designs (CAD) into precise cutting paths.
Key Technologies and Applications:
1. Computer-Aided Design (CAD): CAD software is integral for designing intricate woodwork patterns and generating instructions for CNC machines. It allows for precise customization and replication of designs.
2. Computer-Aided Manufacturing (CAM): CAM software converts CAD designs into machine-readable instructions (G-codes) that dictate tool movements and cutting paths. CAM software optimizes tool paths for efficiency and quality.
3. Machine Structure and Axis Configurations: CNC wood cutting machines feature robust structures with multiple axes (typically 3 to 5 axes). These axes enable complex cutting operations, including 3D carving and contouring.
4. Tooling and Spindle Options: CNC machines support various cutting tools and spindles, including routers and drills. Automatic tool changers enhance efficiency by enabling uninterrupted operations with different tools.
5. Automation and Precision: CNC machines offer high repeatability and accuracy, ensuring consistent quality across large production runs. Automated features such as tool calibration and material alignment further improve precision.
Applications:
1. Furniture Manufacturing: CNC machines fabricate furniture components with intricate designs and joinery, optimizing material usage and reducing waste.
2. Cabinetry and Millwork: They produce custom cabinetry, doors, and moldings with precise cuts and complex designs, meeting diverse customer requirements.
3. Artistic Woodwork: CNC machines create artistic pieces, sculptures, and decorative items with intricate details and smooth finishes, expanding creative possibilities.
4. Prototyping and Small Batch Production: Ideal for prototyping new designs and producing small batches, CNC machines enable rapid iteration and customization.
5. Architectural Woodwork: Used in construction for producing components like staircases, panels, and exterior trim with precise dimensions and complex profiles.
In summary, CNC wood cutting machines integrate advanced technologies to streamline woodworking processes, enhance design flexibility, and achieve high levels of precision and efficiency in various applications from furniture manufacturing to artistic woodwork.
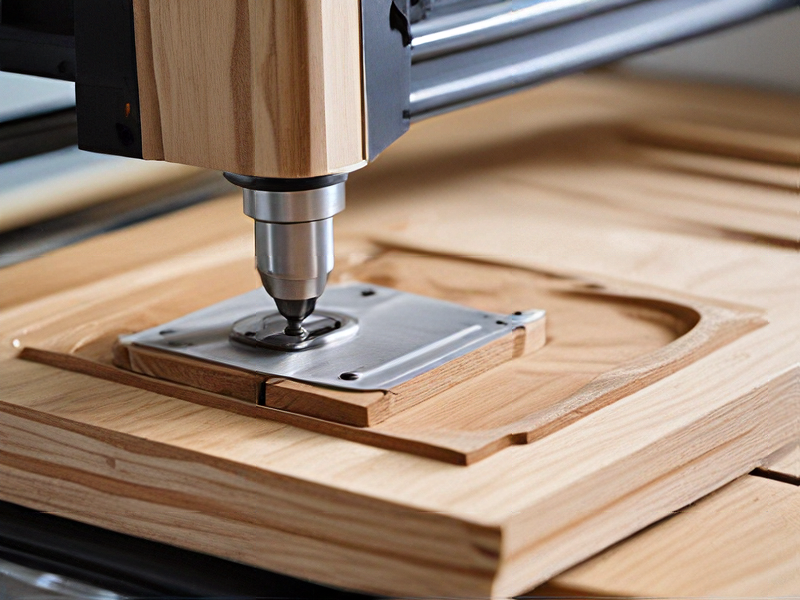
Quality Testing Methods for cnc wood cutting machines and how to control quality
Quality testing methods for CNC wood cutting machines are crucial to ensure precision, reliability, and efficiency. Here are key methods and controls:
Testing Methods:
1. Dimensional Accuracy Tests:
– Caliper and Micrometer Measurements: Measure cut pieces to ensure dimensions match specifications.
– Coordinate Measuring Machine (CMM): Precisely measures the physical geometrical characteristics of the machine components.
2. Repeatability and Reproducibility Tests:
– Test Runs: Perform multiple cuts on the same design to check consistency.
– Statistical Process Control (SPC): Use control charts to monitor and control quality during production.
3. Surface Finish Inspection:
– Visual and Tactile Inspection: Check for smoothness and absence of defects.
– Surface Roughness Tester: Quantitatively measures the texture of the cut surface.
4. Geometric Accuracy Tests:
– Laser Interferometry: Measures linear positioning accuracy.
– Ballbar Testing: Assesses the circularity of movements to identify mechanical inaccuracies.
5. Material Stress Testing:
– Load Testing: Ensures the machine can handle specified loads without compromising quality.
– Vibration Analysis: Detects any vibration issues that might affect cutting precision.
Quality Control Methods:
1. Regular Maintenance and Calibration:
– Scheduled Maintenance: Regularly service the machine to prevent wear and tear.
– Calibration: Frequently calibrate the machine to maintain precision.
2. Operator Training:
– Skill Development: Ensure operators are well-trained in machine handling and maintenance.
– Standard Operating Procedures (SOPs): Implement and enforce SOPs for machine operation.
3. Software Updates and Monitoring:
– Software Calibration: Keep CNC software updated for optimal performance.
– Real-time Monitoring: Use sensors and software to monitor machine performance continuously.
4. Quality Audits and Inspections:
– Internal Audits: Regular internal checks to ensure adherence to quality standards.
– Third-Party Inspections: Periodic inspections by external experts for unbiased quality assessment.
Implementing these methods and controls ensures the high performance and reliability of CNC wood cutting machines, resulting in superior quality products.
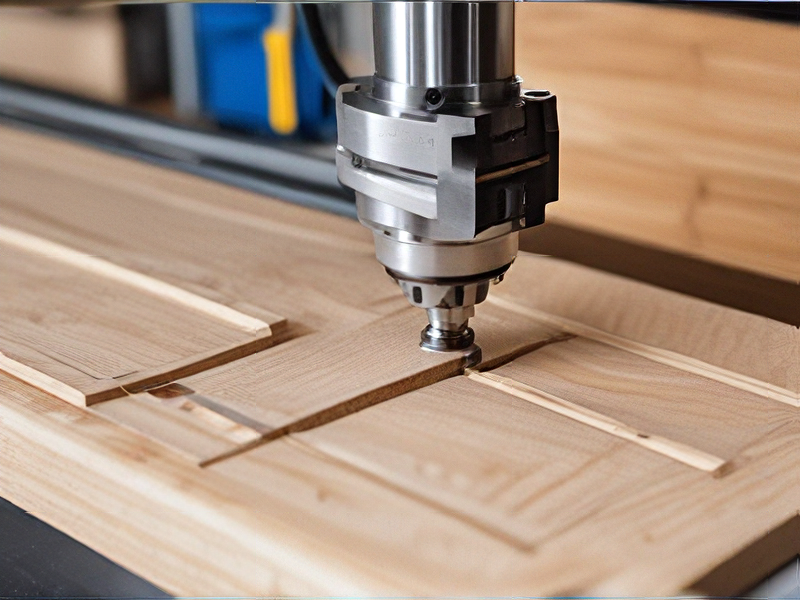
Tips for Procurement and Considerations when Purchasing from cnc wood cutting machines
When procuring CNC wood cutting machines, consider the following tips and factors to ensure a successful purchase:
1. Identify Requirements: Determine your production needs, including material types, cutting precision, speed, and volume. Match these with the machine’s capabilities.
2. Budget and Cost: Establish a clear budget. Consider not just the initial cost, but also the total cost of ownership, including maintenance, operation, and potential upgrades.
3. Machine Specifications: Evaluate key specifications such as spindle power, cutting speed, accuracy, and table size. Ensure these align with your project requirements.
4. Software Compatibility: Confirm that the machine is compatible with your existing design software (e.g., CAD/CAM) to ensure smooth integration into your workflow.
5. Build Quality and Durability: Inspect the machine’s build quality. Durable machines with high-quality components can reduce downtime and maintenance costs.
6. Vendor Reputation: Research the manufacturer’s reputation. Look for reviews, case studies, and user feedback. A reliable vendor with good customer support can be invaluable.
7. Training and Support: Check if the vendor provides training for your team and ongoing technical support. Adequate training can significantly reduce the learning curve and enhance productivity.
8. Warranty and Service Agreements: Review the warranty terms and service agreements. Understand what is covered, the duration of the warranty, and the process for obtaining service and parts.
9. Future Scalability: Consider future expansion. Choose a machine that can be upgraded or expanded to meet growing production demands.
10. Energy Efficiency: Evaluate the machine’s energy consumption. Energy-efficient models can reduce operational costs and are better for the environment.
11. Safety Features: Ensure the machine has adequate safety features to protect operators and comply with industry regulations.
By carefully considering these factors, you can make a well-informed decision that aligns with your operational needs and long-term business goals.
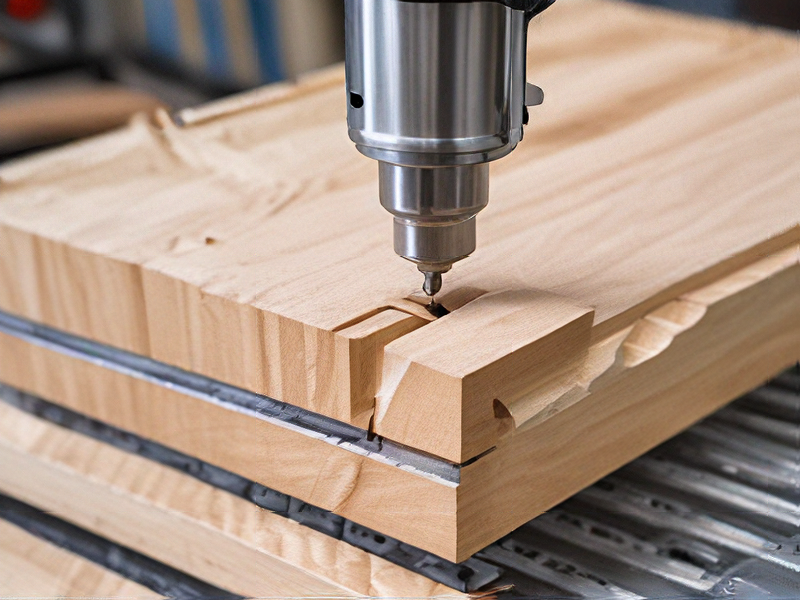
FAQs on Sourcing and Manufacturing from cnc wood cutting machines in China
Certainly! When sourcing and manufacturing CNC wood cutting machines from China, it’s important to consider several key aspects:
1. Supplier Selection: Research and choose suppliers with a proven track record in producing CNC wood cutting machines. Look for manufacturers with positive reviews, certifications (like ISO standards), and experience exporting to your country.
2. Quality Assurance: Request samples or visit the factory if possible to inspect the build quality, materials used, and overall workmanship of the machines. Ensure they meet your quality standards and are capable of long-term performance.
3. Customization Options: Discuss customization possibilities such as machine size, cutting specifications, and additional features. Clarify your specific requirements to avoid misunderstandings later in the manufacturing process.
4. Cost Considerations: While price is important, prioritize value for money over the lowest cost. Factor in shipping, import duties, and potential maintenance costs when comparing quotes from different suppliers.
5. Communication and Contracts: Clearly communicate your expectations regarding specifications, delivery times, payment terms, and after-sales support. Have a detailed contract that outlines these terms to avoid disputes.
6. Logistics and Shipping: Plan logistics in advance, including packaging requirements, shipping methods, and insurance coverage. Understand the shipping timelines and potential delays.
7. After-Sales Support: Inquire about warranty periods, technical support availability, and spare parts availability. A reliable after-sales service is crucial for maintaining and repairing your CNC machines.
8. Legal and Compliance Issues: Ensure compliance with local regulations and import/export laws. Verify that the supplier adheres to environmental and labor standards to avoid legal complications.
By carefully evaluating these factors and maintaining clear communication with your supplier, you can mitigate risks and maximize the benefits of sourcing CNC wood cutting machines from China.
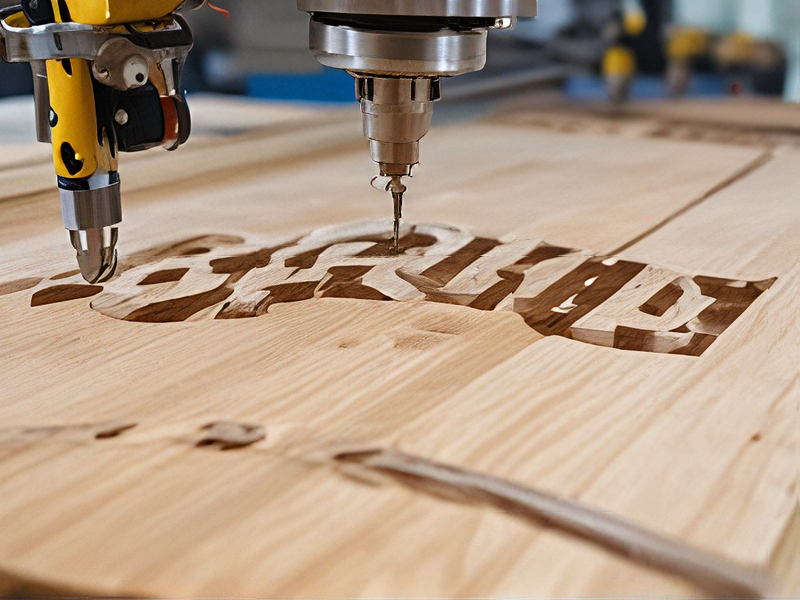