Technology and Applications of computer numerical control machining
Computer Numerical Control (CNC) machining is a technology that automates the control of machine tools through computer programming. It enhances precision, efficiency, and repeatability in manufacturing processes, making it crucial in industries like aerospace, automotive, and medical devices.
CNC machining operates using a computer program that dictates the movement of machines, including mills, lathes, and routers. The process begins with a digital design created in CAD (Computer-Aided Design) software, which is converted into a numerical control (NC) program via CAM (Computer-Aided Manufacturing) software. This program controls axis movements, tool paths, and operational sequences, allowing for intricate and complex shapes to be machined with high accuracy.
Key applications of CNC machining include prototyping, production work, and custom parts manufacturing. It enables the production of components with tight tolerances and intricate designs that would be difficult or impossible to achieve manually. Industries utilize CNC machining for tasks such as drilling, milling, turning, and grinding.
The technology also supports the use of advanced materials, including metals, plastics, and composites, offering various surface finishes and capabilities. Furthermore, CNC machining enhances productivity through features like automation and multi-tasking, which reduce human error and lead times.
As CNC technology evolves, integration with Industry 4.0 concepts like IoT and AI is becoming more prevalent. These advancements promise greater automation, predictive maintenance, and smart manufacturing solutions, positioning CNC machining as a cornerstone of modern manufacturing. Overall, CNC machining provides critical benefits in terms of quality, flexibility, and efficiency, meeting the demands of contemporary production environments.
Quality Testing Methods for computer numerical control machining and how to control quality
Quality testing methods for Computer Numerical Control (CNC) machining are essential to ensure precision and accuracy in manufacturing processes. Here are some key testing methods and quality control strategies:
1. Dimensional Inspection: This involves measuring the physical dimensions of a machined component using tools like calipers, micrometers, and CMMs (Coordinate Measuring Machines). Ensuring that the produced dimensions meet the specified tolerances is crucial.
2. Visual Inspection: A thorough visual check can identify surface defects such as scratches, misalignments, or discolored areas. Inspections are often conducted under controlled lighting and magnification.
3. Functional Testing: This checks the performance of the machined part in its intended application. Testing can include load tests, fit tests, and operational evaluations.
4. Surface Finish Measurement: Techniques such as profilometry can assess the surface finish of machined parts to ensure they meet required standards.
5. Material Testing: Conducting tests like hardness, tensile strength, and toughness via methods such as Rockwell or Brinell hardness tests ensures the material properties meet specified requirements.
Quality Control Strategies:
– In-Process Monitoring: Implementing real-time monitoring systems can help detect anomalies during machining, allowing for immediate corrective actions.
– Statistical Process Control (SPC): Utilizing statistical methods to analyze workflow processes helps identify variations and maintains process consistency.
– Quality Management Systems (QMS): Adopting frameworks like ISO 9001 to streamline processes and document quality control measures ensures compliance and continuous improvement.
– Employee Training: Ensuring that operators are well-trained in CNC operation and quality standards minimizes errors and enhances product quality.
By integrating these testing methods and strategies, manufacturers can maintain high-quality standards in CNC machining.
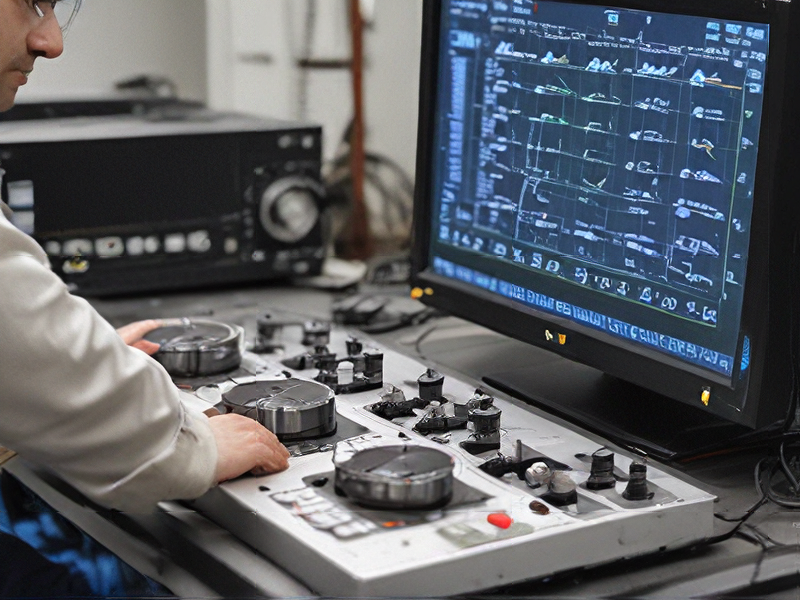
Tips for Procurement and Considerations when Purchasing from computer numerical control machining
When procuring services from Computer Numerical Control (CNC) machining, keep the following tips and considerations in mind:
1. Define Requirements: Clearly outline the specifications, including material type, dimensions, tolerances, and surface finishes. This helps in receiving accurate quotes and ensures the final product meets standards.
2. Research Suppliers: Investigate potential suppliers’ capabilities, technological resources, and experience. Look for reviews or case studies that demonstrate their proficiency in projects similar to yours.
3. Quality Assurance: Ensure the supplier adheres to quality control standards. Check for certifications like ISO 9001, which indicates a commitment to quality management.
4. Cost Analysis: While price is important, evaluate the overall value. A lower price may lead to compromised quality or longer lead times. Consider long-term relationships that might yield better pricing and service.
5. Lead Time and Flexibility: Inquire about lead times and a supplier’s ability to handle changes or rush orders. A flexible supplier can be invaluable in fast-paced industries.
6. Communication: Establish clear communication protocols. Ensure that the supplier understands your needs and that you can easily reach them for updates or concerns.
7. Prototype and Testing: Request prototypes to evaluate the machining process and final product quality before full-scale production. Testing early can save costs and time in the long run.
8. Support Services: Consider suppliers that offer design support, machining advice, and after-sales service. This can enhance collaboration and problem resolution.
By focusing on these aspects, you can make informed decisions and foster successful partnerships in CNC machining procurement.
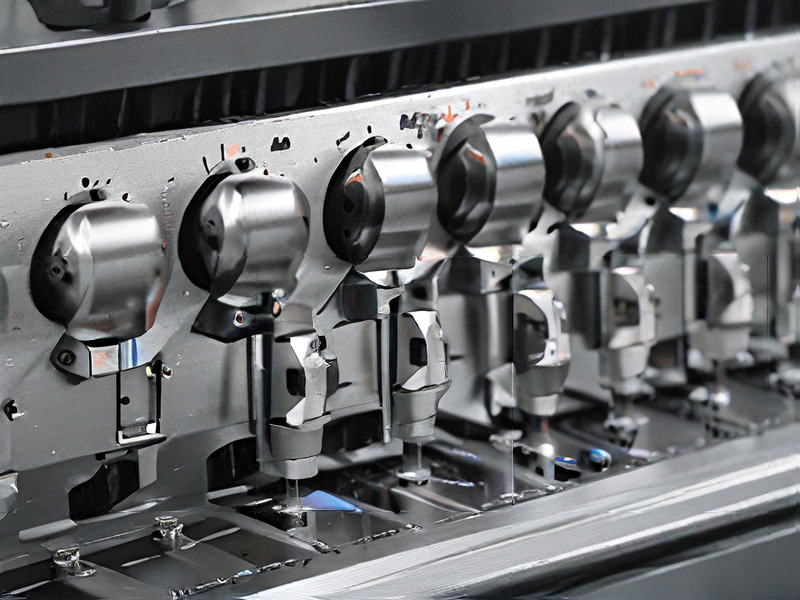
FAQs on Sourcing and Manufacturing from computer numerical control machining in China
FAQs on Sourcing and Manufacturing CNC Machining in China
1. What is CNC machining?
CNC (Computer Numerical Control) machining is a manufacturing process that uses computer-controlled tools to create precise components. It allows for high accuracy and consistency across large production runs.
2. Why consider sourcing CNC machining from China?
China is known for its advanced manufacturing capabilities, competitive pricing, and scalability. Many companies choose China to reduce costs while maintaining quality.
3. How do I find a reliable CNC machining supplier in China?
Start by researching online platforms like Alibaba, Made-in-China, or Globalsources. Look for suppliers with good ratings, verified credentials, and positive reviews. Request samples and assess their communication skills.
4. What quality control measures are used in CNC machining?
Reputable suppliers implement quality control throughout the manufacturing process, including initial inspections, in-process checks, and final product evaluations. Certificates like ISO 9001 can indicate a supplier’s commitment to quality.
5. What are the typical lead times for CNC machining orders?
Lead times can vary based on complexity and order volume but generally range from 2 to 6 weeks after finalizing designs. Always confirm with your supplier.
6. How should I approach shipping and logistics?
Discuss shipping options with your supplier, including FOB (Free on Board) or DDP (Delivery Duty Paid). Understand customs duties and import regulations for your country.
7. What are the potential risks?
Risks include communication barriers, quality inconsistencies, and delays. Conduct thorough due diligence and maintain open lines of communication to mitigate these risks.
8. Can I customize my design?
Yes, CNC machining allows for significant design flexibility. Provide detailed specifications and drawings to your supplier for accurate production.
For a successful project, clear communication and good planning are key.
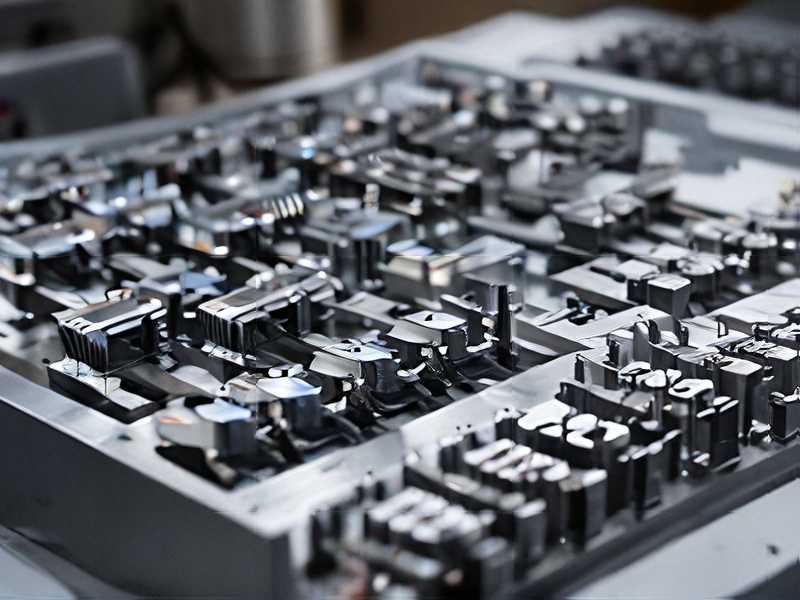