Technology and Applications of coordinate measurement machine
Coordinate Measurement Machines (CMMs) are vital tools in manufacturing and metrology, used to measure the geometrical characteristics of physical objects with high precision. They operate based on Cartesian coordinates and can measure dimensions, angles, and geometric shapes of components.
The technology behind CMMs involves a tactile or optical probe mounted on three axes (X, Y, and Z), allowing it to move along these axes to reach different points on the object’s surface. Tactile probes make physical contact with the surface to record measurements, while optical probes use light or laser technology for non-contact measurements.
Applications of CMMs are diverse across industries such as aerospace, automotive, electronics, and medical devices. In manufacturing, they ensure components meet design specifications, aiding in quality control and process optimization. CMMs are used to inspect complex shapes like turbine blades, automotive engine parts, and circuit boards, ensuring they conform to exact measurements and tolerances.
Advancements in CMM technology include portable CMMs for on-site measurements and multi-sensor systems combining tactile and optical probes for greater flexibility and accuracy. Software integration allows for automated measurement routines and data analysis, improving efficiency and reducing human error.
In summary, CMMs play a critical role in modern manufacturing by ensuring precision, quality, and compliance with design specifications across various industries, making them indispensable tools for dimensional metrology and quality assurance.
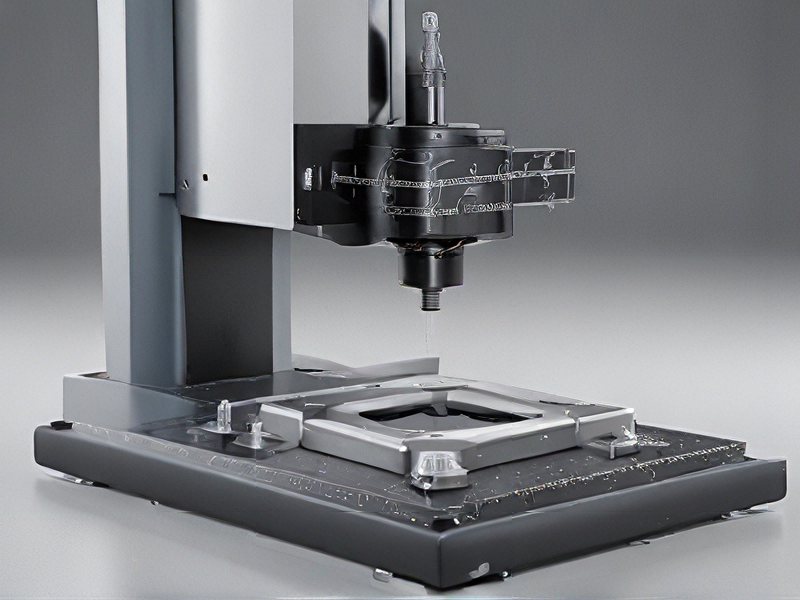
Quality Testing Methods for coordinate measurement machine and how to control quality
Quality testing methods for Coordinate Measurement Machines (CMMs) typically involve several key approaches to ensure accuracy and reliability:
1. Dimensional Accuracy Testing: Utilizes calibrated reference standards (e.g., gauge blocks) to verify the machine’s ability to measure distances accurately across its range.
2. Geometric Accuracy Testing: Checks the machine’s ability to measure geometric features (e.g., circles, angles) accurately using artifacts with known geometric properties.
3. Repeatability and Reproducibility (R&R) Studies: Assesses the consistency of measurements by performing repeated measurements of the same feature under identical conditions (repeatability) and comparing measurements made by different operators or machines (reproducibility).
4. Software Performance Verification: Evaluates the CMM software’s capability to correctly interpret measurement data, apply geometric algorithms, and generate accurate reports.
5. Environmental Influence Testing: Examines how variations in temperature, humidity, and vibrations affect the CMM’s performance to ensure reliable operation in different conditions.
To control quality effectively:
– Calibration: Regular calibration of the CMM and its probes ensures measurement accuracy.
– Maintenance: Scheduled maintenance and cleaning prevent mechanical wear and ensure consistent performance.
– Operator Training: Proper training on CMM operation, measurement techniques, and data interpretation minimizes errors.
– Documentation and Records: Maintain comprehensive records of calibration, maintenance, and measurement results to track performance over time and identify trends.
By employing these methods and controls, manufacturers and quality assurance professionals can ensure that CMMs deliver precise and reliable measurements, essential for maintaining product quality and compliance with standards.
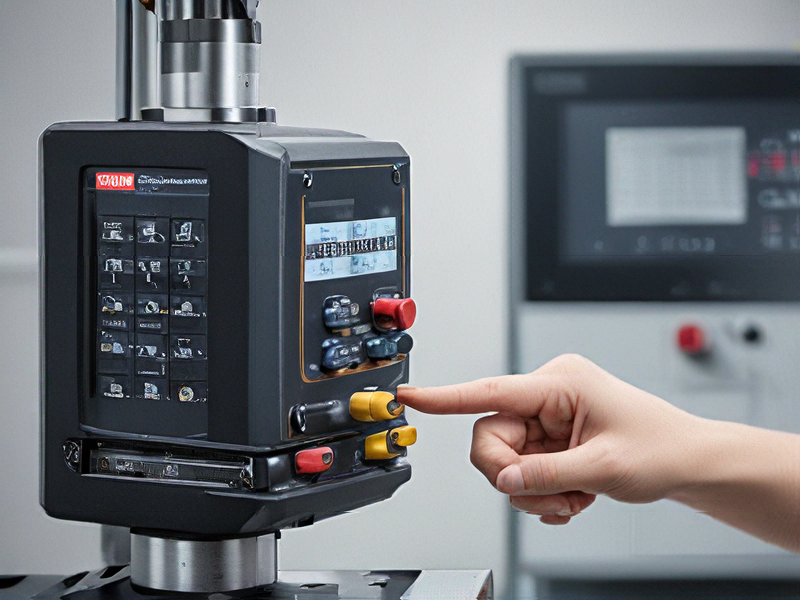
Tips for Procurement and Considerations when Purchasing from coordinate measurement machine
When procuring a Coordinate Measurement Machine (CMM), several key considerations and tips can ensure a successful purchase and long-term value:
1. Define Your Requirements: Clearly identify the specific measurements and tolerances required for your applications. Determine the size, shape, and type of components you will measure.
2. Accuracy and Precision: Choose a CMM with the accuracy and precision needed for your projects. Check the machine’s specifications for repeatability, measurement uncertainty, and resolution.
3. Type of CMM: Decide between different types of CMMs (bridge, cantilever, gantry, or portable). The choice depends on the size of the parts, the measurement volume, and the working environment.
4. Software Capabilities: Ensure the CMM’s software is user-friendly and compatible with your existing systems. It should offer advanced features like CAD integration, automated reporting, and data analysis tools.
5. Ease of Use and Training: Evaluate the learning curve of the machine and the availability of training. Opt for suppliers who offer comprehensive training and ongoing support.
6. Maintenance and Support: Investigate the availability of service contracts, spare parts, and technical support. Regular maintenance and prompt support can minimize downtime and extend the machine’s lifespan.
7. Calibration and Certification: Ensure the CMM comes with a calibration certificate traceable to national standards. Regular recalibration is crucial for maintaining measurement accuracy.
8. Environmental Conditions: Consider the environmental conditions where the CMM will be installed. Factors like temperature, humidity, and vibrations can affect performance.
9. Cost and ROI: Balance the upfront cost with the long-term return on investment. Factor in the potential for increased productivity, improved quality, and reduced scrap rates.
10. Vendor Reputation: Research the vendor’s reputation, customer reviews, and case studies. A reputable vendor with a history of reliable products and excellent customer service is crucial.
11. Future-Proofing: Consider the machine’s flexibility to adapt to future needs, such as upgrades or the ability to handle new measurement tasks.
By carefully considering these factors, you can make an informed decision that meets your measurement needs and provides lasting value.
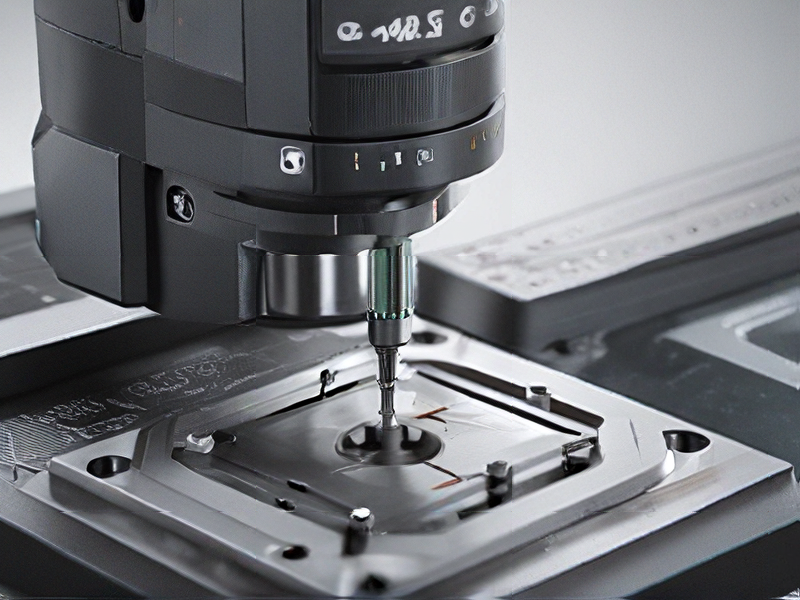
FAQs on Sourcing and Manufacturing from coordinate measurement machine in China
Certainly! Here are some FAQs on sourcing and manufacturing from coordinate measurement machines (CMMs) in China:
1. What are the advantages of sourcing CMMs from China?
China offers cost-effective manufacturing solutions with a wide range of CMM options. Many Chinese manufacturers provide competitive pricing and flexible customization.
2. How do I ensure quality when sourcing CMMs from China?
It’s crucial to conduct thorough due diligence. Look for manufacturers with ISO certifications and a proven track record. Request samples or visit the factory if possible to inspect their production processes and quality control measures.
3. What are the typical lead times for manufacturing CMMs in China?
Lead times can vary depending on the complexity and customization of the CMM. Generally, it ranges from a few weeks to a few months. Clarify lead times with your supplier and factor them into your project timeline.
4. What are the common challenges when sourcing CMMs from China?
Language barriers, cultural differences, and potential logistics issues can be challenging. It’s important to establish clear communication channels and have a contingency plan for any unforeseen delays.
5. Are there any import regulations or tariffs I should be aware of?
Stay updated on import regulations and tariffs imposed by your country and China. Engage with a logistics expert to navigate customs procedures and ensure compliance.
6. How can I find reliable suppliers for CMMs in China?
Utilize online platforms, industry trade shows, and professional networks to identify reputable suppliers. Seek recommendations and verify supplier credentials through references and online reviews.
7. What support can I expect after purchasing a CMM from a Chinese manufacturer?
Ensure your supplier offers adequate technical support, warranty terms, and maintenance services. Clarify these aspects before finalizing the purchase to avoid future complications.
Navigating sourcing and manufacturing from China requires diligence and clear communication to ensure quality and reliability throughout the process.
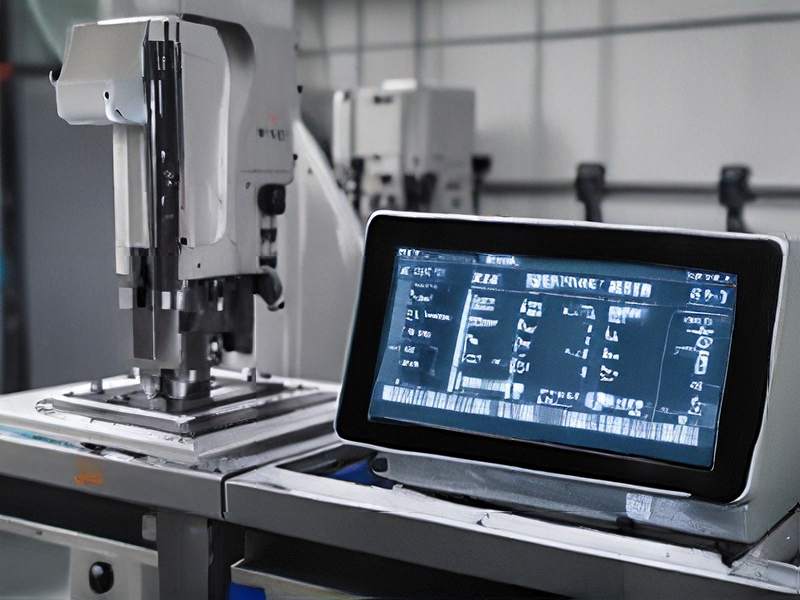