Technology and Applications of define broaching machine
A broaching machine is a specialized tool used to shape and size materials through a process called broaching. This machining operation involves a toothed tool, known as a broach, which is pushed or pulled through the workpiece to remove material. Broaching is particularly effective for producing complex shapes, keyways, and internal or external profiles.
Technology: Broaching machines are powered by hydraulic, electric, or mechanical means, allowing for high-precision cuts with repeatable accuracy. There are two main types: horizontal and vertical broaching machines. Horizontal machines are typically used for linear broaching, while vertical machines excel in internal broaching applications. The broaches differ in design depending on the task; they can be roughing broaches for initial shaping or finishing broaches for fine-tuning.
Applications: Broaching machines are widely used in various industries, including automotive, aerospace, and manufacturing. They are ideal for creating features such as splines, gears, and holes with specific profiles. The ability to produce high-volume parts quickly makes broaching a preferred choice in mass production settings. Furthermore, the use of broaching can lead to improved surface finish and tighter tolerances compared to traditional machining methods.
Overall, broaching machines enhance manufacturing efficiency and precision, making them invaluable in many engineering applications. Advances in technology, including CNC (Computer Numerical Control) broaching, have further refined the process, allowing for more complex tasks and increased automation in production lines. As industries continue to evolve, broaching will remain a critical element in the machining landscape.
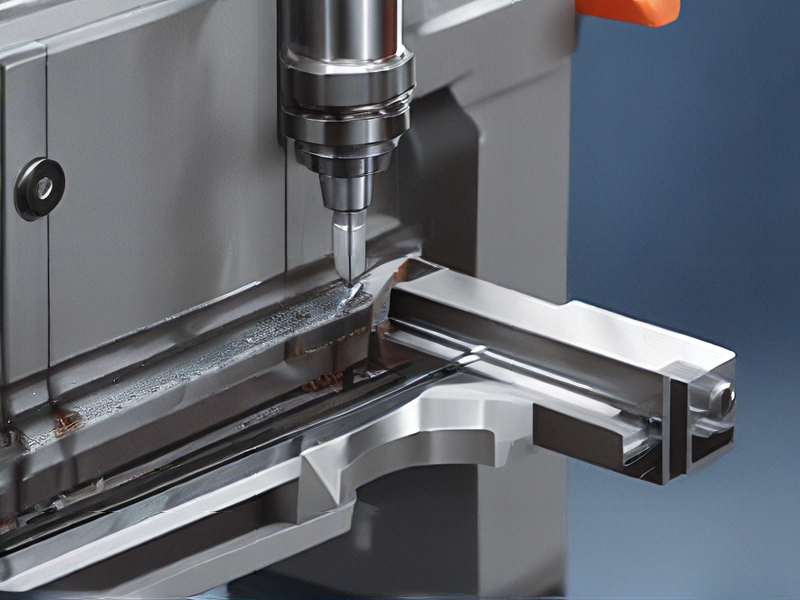
Quality Testing Methods for define broaching machine and how to control quality
Quality testing for a defined broaching machine involves several methods that ensure the machine operates efficiently and outputs high-quality products. Key quality control measures include the following:
1. Dimensional Accuracy Testing: Regularly measure the finished broached components using calipers and micrometers to ensure they meet specified tolerances. This verifies that the broaching process is consistent and that the machine is properly set up.
2. Surface Finish Inspection: Use surface roughness testers to assess the quality of the broached surface. A good surface finish is critical for performance, and deviations can indicate tool wear or improper setup.
3. Tool Condition Monitoring: Implement a regular tool inspection program to check for wear and damage. Dull or damaged broach tools can negatively impact quality. Techniques like visual inspections and hardness testing can be employed.
4. Cycle Time Analysis: Monitor the time taken for broaching cycles. Unusually long or short cycle times can indicate issues with the machine or tooling, affecting the final quality.
5. Vibration Analysis: Use vibration analysis equipment to monitor the machine during operation. Excessive vibration can lead to lower precision and increased tool wear, indicating the need for maintenance.
6. Statistical Process Control (SPC): Utilize SPC techniques to control the production process. By analyzing data from production runs, operators can identify trends or deviations from the norm, enabling proactive adjustments.
7. Training and Certification: Ensure that operators are trained and certified in the proper usability of the machine and quality inspection protocols. Skilled operators contribute significantly to maintaining quality standards.
Implementing these methods collectively helps control the quality of broaching operations and enhances product consistency and reliability.
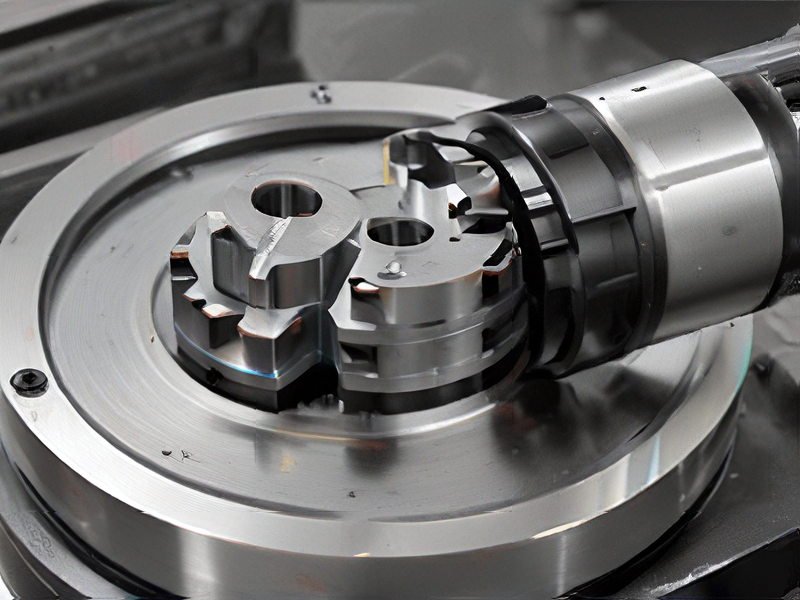
Tips for Procurement and Considerations when Purchasing from define broaching machine
When purchasing a broaching machine, it’s important to consider several factors to ensure you get the best equipment for your needs. Here are some key tips and considerations:
1. Define Your Needs:
– Type of Broaching: Determine whether you need horizontal, vertical, or rotary broaching machines based on the parts you’ll be producing.
– Materials: Consider the types of materials you’ll be working with, such as metals or plastics, to ensure the machine can handle them.
2. Machine Specifications:
– Size and Capacity: Evaluate the size of the workpieces and the production volume to choose a machine with appropriate stroke length, tonnage, and capacity.
– Speed and Precision: Look for machines with the speed and accuracy necessary for your production requirements.
3. Quality and Durability:
– Brand and Manufacturer: Opt for reputable manufacturers known for high-quality, durable machines. Research customer reviews and industry feedback.
– Build Quality: Check the construction and materials of the machine, ensuring it can withstand rigorous use.
4. Technological Features:
– Automation: Consider machines with automated features to increase efficiency and reduce labor costs.
– Control Systems: Look for modern control systems that offer easy operation, programmability, and integration with other equipment.
5. Cost and Budget:
– Initial Cost: Assess your budget and compare the prices of different models, balancing cost with features and quality.
– Operating Costs: Factor in maintenance, tooling, and energy consumption costs over the machine’s lifespan.
6. After-Sales Support:
– Warranty and Service: Ensure the machine comes with a solid warranty and access to reliable customer service and technical support.
– Spare Parts Availability: Check the availability of spare parts and the ease of obtaining them.
7. Training and Safety:
– Operator Training: Verify if the manufacturer provides training for your staff on machine operation and maintenance.
– Safety Features: Ensure the machine includes essential safety features to protect operators and maintain a safe working environment.
By thoroughly evaluating these aspects, you can make an informed decision when purchasing a broaching machine that meets your operational requirements and ensures long-term productivity and reliability.
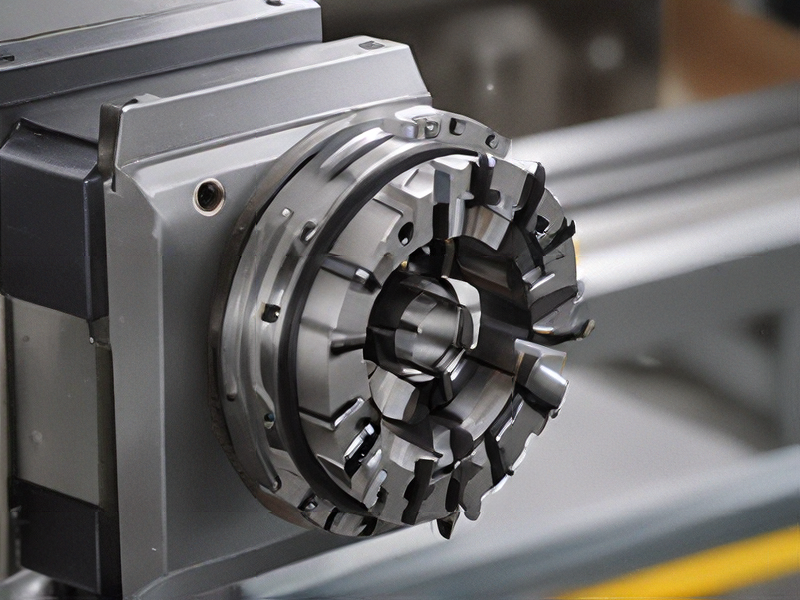
FAQs on Sourcing and Manufacturing from define broaching machine in China
FAQs on Sourcing and Manufacturing Broaching Machines in China
1. What is a broaching machine?
A broaching machine is a manufacturing tool used to remove material from a workpiece by means of a toothed tool called a broach. It is ideal for precision shaping, particularly for making holes, slots, and contours.
2. Why source broaching machines from China?
China is a global leader in manufacturing, offering competitive pricing, advanced technology, and a wide range of suppliers. This makes it an attractive option for sourcing broaching machines.
3. How do I find reliable manufacturers?
To find reliable manufacturers, consider using platforms like Alibaba or Made-in-China, checking supplier credentials, and reading reviews. It’s also advisable to visit factories or request samples before placing large orders.
4. What should I consider when sourcing?
Key factors include product quality, production capacity, lead times, shipping logistics, compliance with international standards, and after-sales service. Conduct thorough due diligence to ensure the manufacturer meets your requirements.
5. What is the typical lead time for manufacturing?
Lead times can vary widely based on the complexity of the machine and the manufacturer’s capacity, typically ranging from 30 to 90 days after order confirmation.
6. Are there quality assurance practices?
Yes, many manufacturers implement quality control checks at various stages of production. You can request reports or engage third-party inspection services to ensure product quality.
7. What are the payment terms?
Payment terms can vary, but common practices include a deposit (often 30% upfront) and the balance before shipment. Always confirm payment terms with your supplier.
8. How can I manage shipping logistics?
You can choose to work with freight forwarders who specialize in international shipping to handle customs clearance and delivery.
For detailed inquiries, it’s advisable to engage directly with manufacturers or sourcing agents.
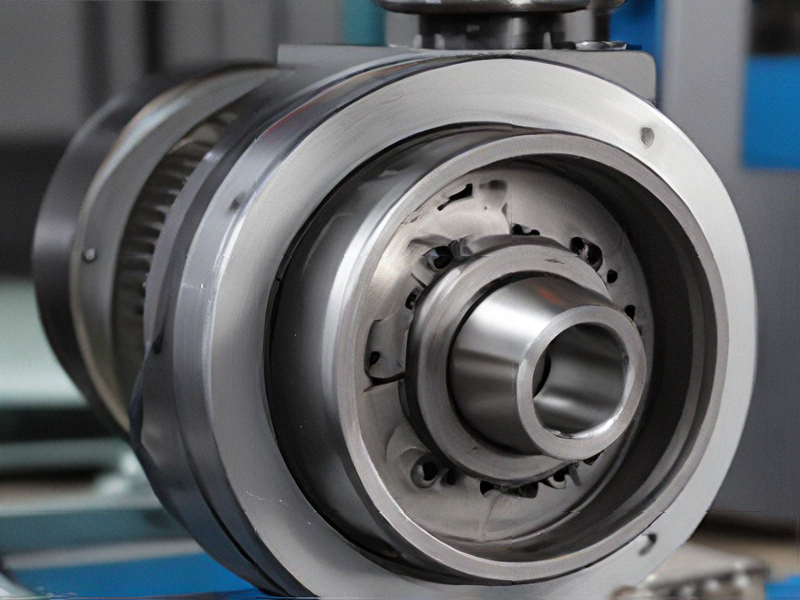