Technology and Applications of drill head for metal
Drill heads are essential tools in metalworking, enabling the creation of holes of varying sizes and depths. Their technology and applications are diverse, catering to specific needs in different industries.
Types of Drill Heads:
* Twist drills: Most common type, featuring helical flutes for chip removal and efficient cutting.
* Form drills: Create non-circular holes, such as square or hexagonal.
* Reamer drills: Enlarge existing holes to precise diameters.
* Core drills: Remove cylindrical cores of metal, often used for creating larger holes.
Applications:
* Manufacturing: Essential for drilling holes in metal components for assembly, fastening, and machining operations.
* Construction: Used in drilling holes for anchoring bolts, reinforcing steel, and installing plumbing and electrical systems.
* Automotive: Drilling holes in metal car bodies, engine blocks, and chassis for various components and assembly purposes.
Technological Advancements:
* Coated drills: Special coatings enhance durability, reduce friction, and improve chip evacuation.
* Solid Carbide drills: Offer exceptional hardness and wear resistance, suitable for drilling tough metals and alloys.
* Laser-drilled holes: Precise and efficient for creating small, intricate holes with minimal heat-affected zones.
Drill heads continue to evolve, driven by the need for increased efficiency, accuracy, and versatility in metalworking applications.
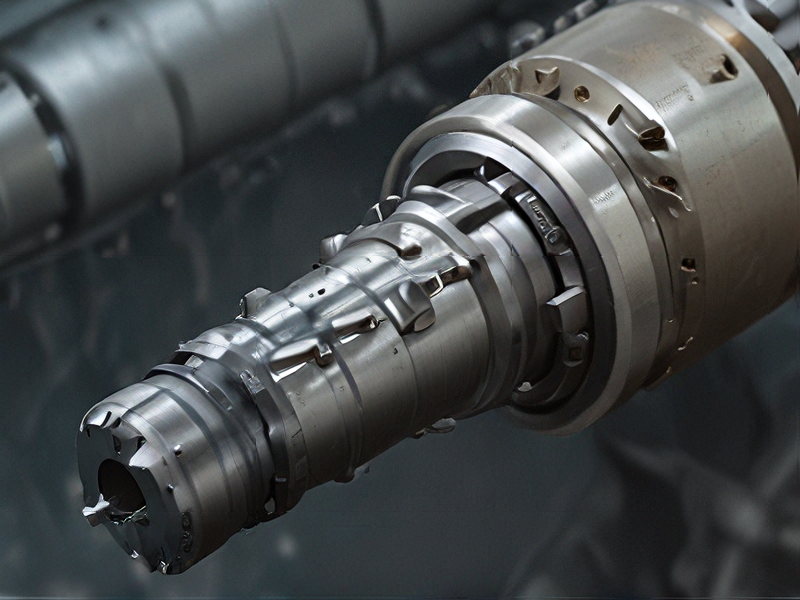
Quality Testing Methods for drill head for metal and how to control quality
Quality testing of drill heads for metal involves several methods to ensure performance, durability, and precision. Key testing methods include:
1. Dimensional Inspection: Using micrometers, calipers, and coordinate measuring machines (CMM) to check the drill head’s dimensions against design specifications.
2. Hardness Testing: Employing Rockwell or Vickers hardness tests to ensure the drill head can withstand the stress of cutting through metal.
3. Material Composition Analysis: Utilizing spectrometry or X-ray fluorescence (XRF) to verify the chemical composition of the drill head material, ensuring it meets required standards.
4. Surface Finish Inspection: Using profilometers or visual inspection to check the surface roughness and ensure it is within acceptable limits to reduce friction and wear.
5. Performance Testing: Conducting practical drilling tests on metal samples to evaluate the drill head’s efficiency, speed, and durability under operational conditions.
6. Coating Adhesion Test: For coated drill heads, performing scratch or bend tests to ensure the coating adheres properly and provides the necessary protection.
7. Fatigue Testing: Simulating repeated drilling operations to assess the drill head’s resistance to fatigue and failure over time.
8. Microscopic Examination: Using optical or electron microscopes to examine the microstructure and detect any defects like cracks or inclusions.
Quality Control Measures:
1. Standardized Procedures: Establishing and adhering to standardized testing procedures for consistency and reliability in results.
2. Statistical Process Control (SPC): Implementing SPC to monitor the manufacturing process and detect variations that could affect quality.
3. Calibration: Regularly calibrating inspection and testing equipment to ensure accurate measurements.
4. Supplier Quality Management: Ensuring raw materials and components from suppliers meet stringent quality standards through regular audits and inspections.
5. Training and Certification: Providing ongoing training for personnel to maintain high skill levels in manufacturing and testing processes.
6. Continuous Improvement: Utilizing feedback from testing results to continuously improve design and manufacturing processes, reducing defects and enhancing performance.
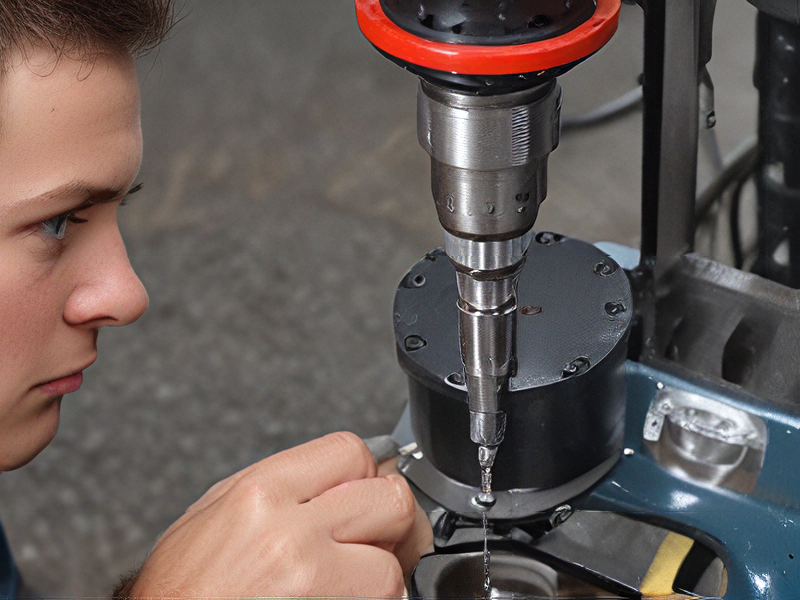
Tips for Procurement and Considerations when Purchasing from drill head for metal
When procuring a drill head for metal, consider the following tips to ensure optimal performance and longevity:
Key Considerations:
1. Material Compatibility: Ensure the drill head is specifically designed for metalworking. Carbide, cobalt, and high-speed steel (HSS) are popular materials known for their durability and efficiency in metal drilling.
2. Drill Head Type: Choose between twist drills, step drills, or hole saws based on the required application. Twist drills are versatile, step drills are ideal for enlarging existing holes, and hole saws are suitable for larger diameter cuts.
3. Coating: Opt for coated drill bits, such as titanium or black oxide, to enhance wear resistance, reduce friction, and extend the tool’s life.
4. Size and Precision: Ensure the drill bit size matches the job requirements for accuracy and efficiency. Consider sets with various sizes for flexibility.
5. Compatibility with Equipment: Verify that the drill head is compatible with the drilling machine, including the chuck size and type.
6. Cutting Speed and Feed Rate: Understand the recommended cutting speed and feed rate for the specific drill head and material to prevent damage and ensure smooth operation.
7. Vendor Reputation: Purchase from reputable suppliers known for quality and reliability. Check reviews and ratings to gauge customer satisfaction.
8. Cost vs. Quality: Balance cost with quality. Higher-priced options often provide better durability and performance, reducing long-term costs.
9. Warranty and Support: Look for products that offer warranties and reliable customer support to handle any issues or defects.
Tips for Procurement:
1. Define Requirements: Clearly outline the specifications needed for the drill head, including material, size, and application.
2. Compare Suppliers: Obtain quotes from multiple suppliers to compare prices, quality, and delivery times.
3. Inspect Samples: If possible, test samples to ensure they meet your requirements before making a bulk purchase.
4. Negotiate Terms: Negotiate for better pricing, extended warranties, or additional support services.
5. Bulk Purchasing: Consider bulk purchasing to benefit from discounts, but ensure storage conditions are suitable to maintain product integrity.
By considering these factors and following these tips, you can make an informed decision when purchasing drill heads for metal, ensuring efficiency and cost-effectiveness in your operations.
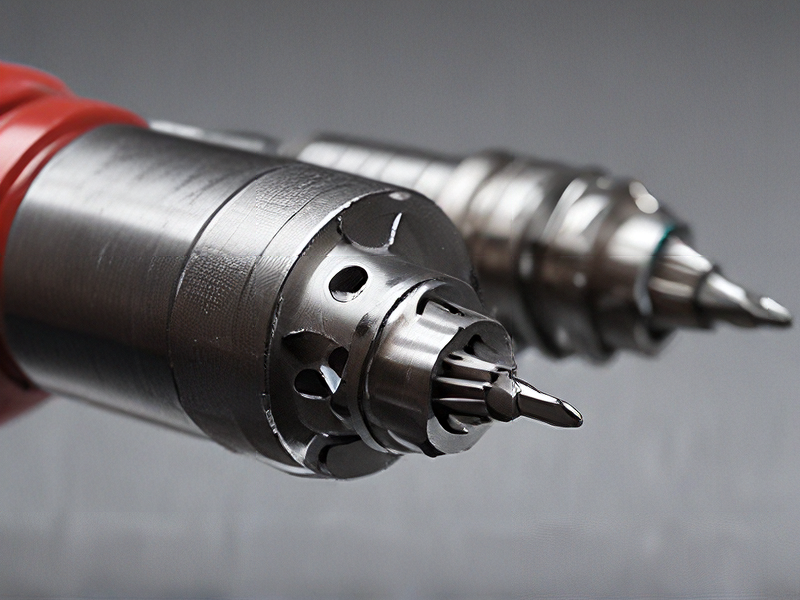
FAQs on Sourcing and Manufacturing from drill head for metal in China
FAQs on Sourcing and Manufacturing Drill Heads for Metal in China
#### 1. Why source drill heads from China?
China offers competitive pricing, a wide range of suppliers, and advanced manufacturing capabilities. These advantages allow for high-quality products at lower costs compared to other markets.
#### 2. How to find reliable suppliers?
Use platforms like Alibaba, Made-in-China, and Global Sources. Verify suppliers through reviews, certifications, and by requesting samples. Trade shows and sourcing agents can also help identify reliable manufacturers.
#### 3. What certifications should I look for?
Look for ISO 9001 for quality management, CE marking for European markets, and other relevant certifications like RoHS for safety and environmental compliance.
#### 4. What are the common materials used in drill heads?
Common materials include high-speed steel (HSS), cobalt steel alloys, and carbide. These materials offer durability and efficiency for metal drilling applications.
#### 5. How to ensure product quality?
Request product samples, conduct factory audits, and use third-party inspection services. Regular quality control checks during production and pre-shipment inspections are also essential.
#### 6. What is the typical lead time for manufacturing?
Lead times vary but generally range from 30 to 60 days, depending on order size and production schedules. Custom orders may take longer.
#### 7. What are the payment terms?
Common payment terms include T/T (Telegraphic Transfer), L/C (Letter of Credit), and Western Union. Initial orders often require a deposit (30%) with the balance paid upon shipment.
#### 8. How to handle shipping and logistics?
Most suppliers offer FOB (Free on Board) terms. Work with a reliable freight forwarder to handle shipping, customs clearance, and delivery to your location.
#### 9. Are there any import regulations to consider?
Check your country’s import regulations for duties, tariffs, and compliance standards. Ensure all necessary documentation, such as commercial invoices and packing lists, is accurate and complete.
#### 10. How to build a long-term relationship with suppliers?
Communicate clearly, make payments on time, and provide feedback on product quality. Visiting suppliers in person and establishing trust can also foster long-term partnerships.
These steps will help ensure a smooth and successful sourcing and manufacturing process for drill heads for metal from China.
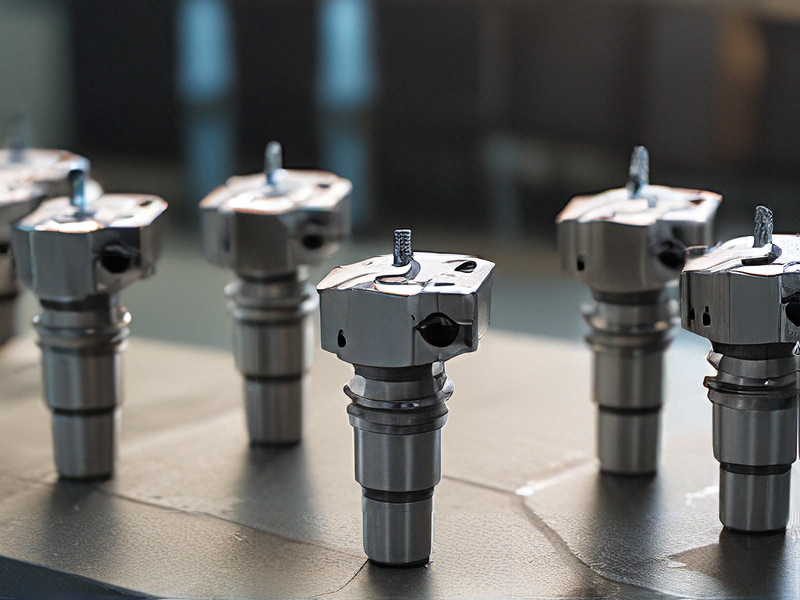